バフ研磨ホイールの種類と交換目安
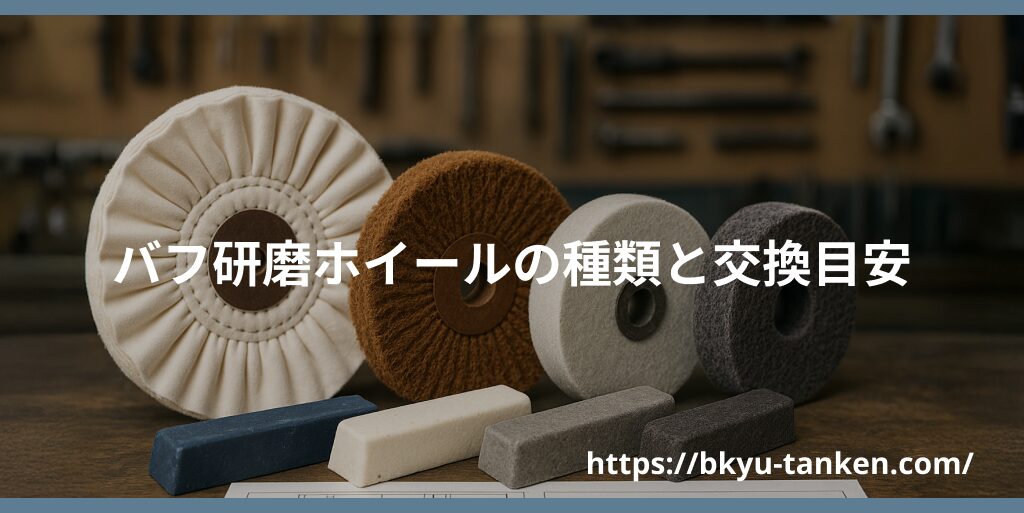
「ステンレスの鏡面仕上げには、どのバフを使えばいいんだ?」
「このバフ、まだ使えるかな?交換時期がいまいち分からない…」
「バフの消費が激しくて、コストがかさんで困る…」
中小企業の金属加工現場で、バフ研磨を担当されている皆さん、こんにちは!金属研磨ドットコムの研磨職人タカです。20 年以上この道にいますが、バフ選びと交換タイミングは、研磨の品質とコストを左右する非常に重要なポイントだと常々感じています。
適切なバフを選び、最適なタイミングで交換することは、製品の品質を安定させ、無駄なコストを削減し、さらには作業効率を向上させる鍵となります。しかし、バフの種類は多岐にわたり、交換基準も曖昧になりがちで、悩んでいる方も多いのではないでしょうか?
この記事では、研磨職人タカが、バフ研磨ホイールの基本的な種類とその選び方、そして「いつ交換すべきか?」という交換目安について、現場目線で分かりやすく解説します。さらに、バフを長持ちさせるコツや、おすすめの製品もご紹介します。
この記事を読めば、もうバフ選びや交換時期で迷うことはありません。最適なバフ研磨で、品質向上とコスト削減を実現しましょう!
バフ研磨ホイールとは?基本を知ろう
まず、バフ研磨の基本と、その中で「バフ研磨ホイール(以下、バフ)」がどのような役割を果たしているのかを確認しましょう。ここを理解することが、適切なバフ選びの第一歩です。
バフ研磨の仕組みとホイールの役割
バフ研磨は、回転するバフ(布やフェルトなどでできた円盤状の工具)の外周に研磨剤(コンパウンド)を塗布し、それを加工対象物(ワーク)に押し当てて表面を磨き上げる加工方法です。
バフ自体に研磨力があるわけではなく、バフは研磨剤を保持し、ワーク表面に均一に作用させるための「媒体」としての役割を担っています。モーターなどで高速回転させることで、研磨剤による微細な切削作用と、摩擦による塑性流動(表面を滑らかにする作用)を引き起こし、光沢のある滑らかな表面を作り出します。
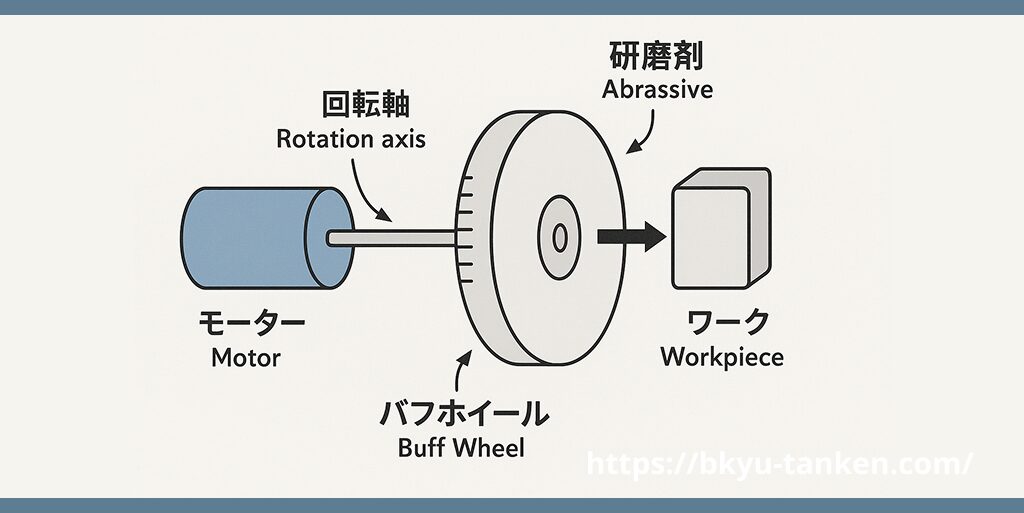
ホイール選びが重要な理由
バフの材質や形状、硬さによって、研磨剤の保持能力やワークへの追従性、研磨熱の発生具合などが大きく異なります。
ワークの材質(鉄、ステンレス、アルミ、真鍮など)や、求める仕上げレベル(粗磨き、中仕上げ、鏡面仕上げなど)に合わせて最適なバフを選ばないと、以下のような問題が発生しやすくなります。
- 研磨ムラや傷が残る
- 狙い通りの光沢が出ない
- 研磨に時間がかかりすぎる
- バフや研磨剤の消費が激しい
- ワークが焼け付いてしまう
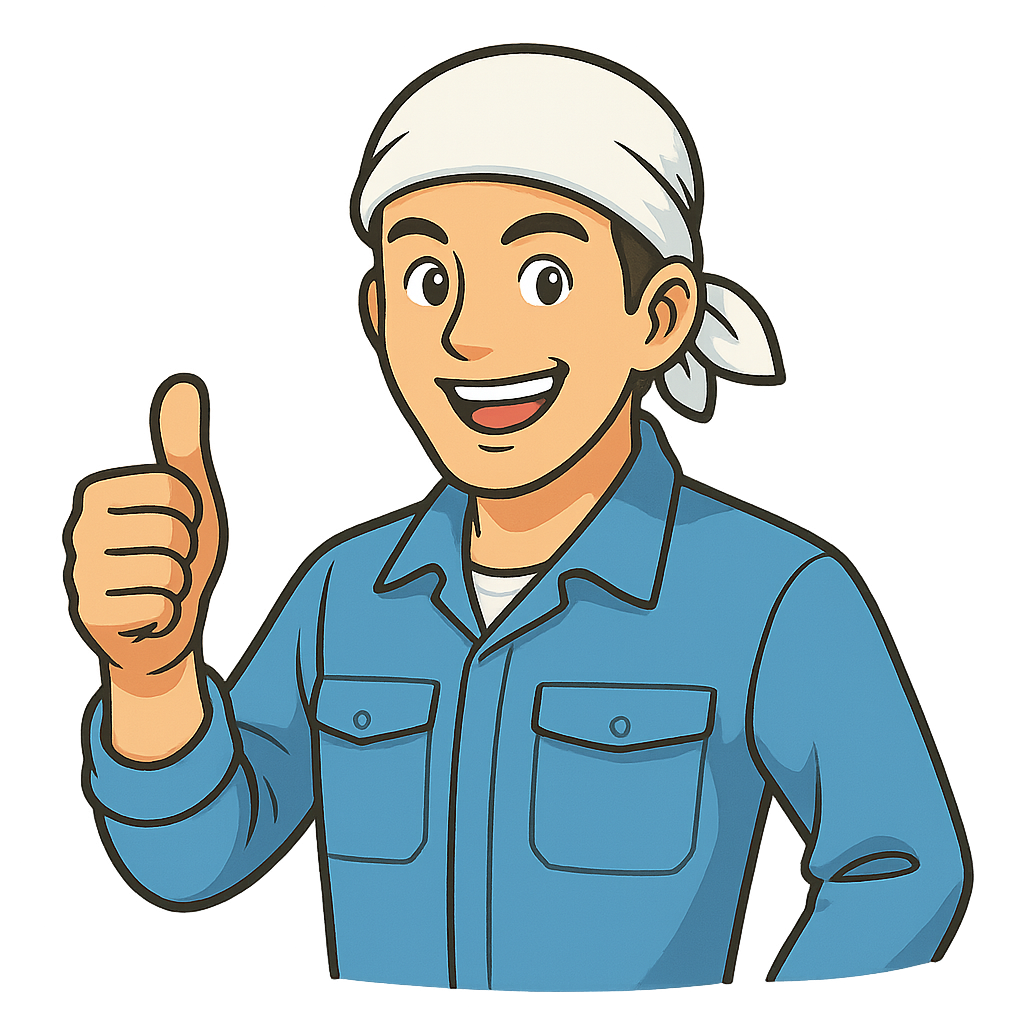
特に量産品の場合、この「わずかな差」がクレームや不良率の増加につながることも少なくありません。ロボットはプログラムされた通りに正確な動作を繰り返すため、人為的なミスやばらつきを限りなくゼロに近づけ、常に安定した高品質な研磨を実現できます。これは、企業の信頼性を高める上でも非常に重要です。
【材質別】主なバフ研磨ホイールの種類と特徴
バフの材質は、研磨性能を決定づける最も重要な要素です。ここでは、現場でよく使われる代表的な材質のバフについて、その特徴と主な用途を解説します。
① 綿バフ(コットンバフ):万能選手、仕上げに最適
最も一般的で、幅広い用途に使われるのが綿(コットン)製のバフです。布の織り方や密度、処理方法によって様々な種類がありますが、一般的に柔らかく、ワークへの当たりがソフトなのが特徴です。
- 主な用途:中仕上げ~最終仕上げ(鏡面仕上げ含む)、各種金属(鉄、ステンレス、アルミ、真鍮、亜鉛ダイカストなど)、樹脂
- 特徴:柔軟性があり、複雑な形状にも馴染みやすい。研磨剤の保持能力が高い。比較的安価。
- 注意点:研削力はサイザルなどに劣る。耐久性は材質や使い方による。
仕上げ用の「ネルバフ」なども綿バフの一種です。青棒や白棒といった仕上げ用研磨剤との組み合わせで、美しい光沢を得るために広く使われています。
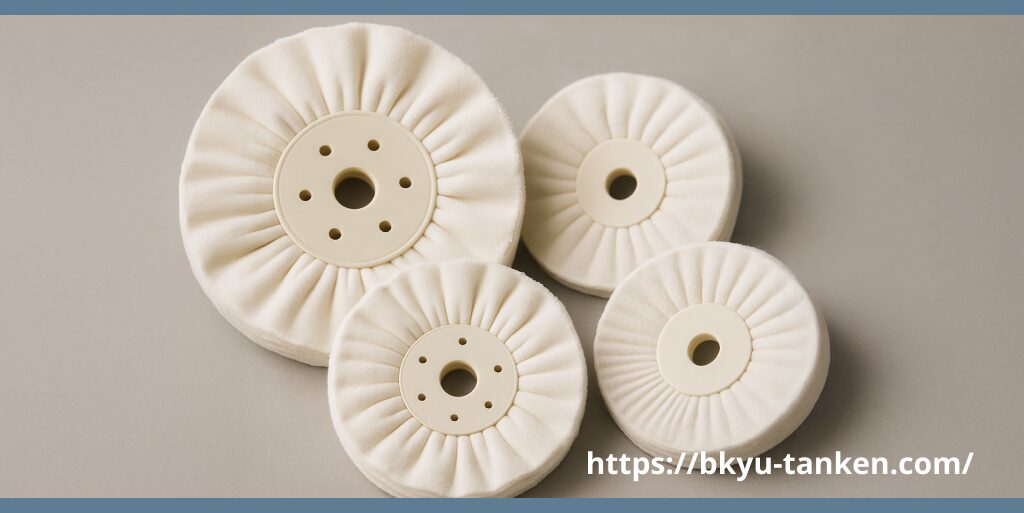
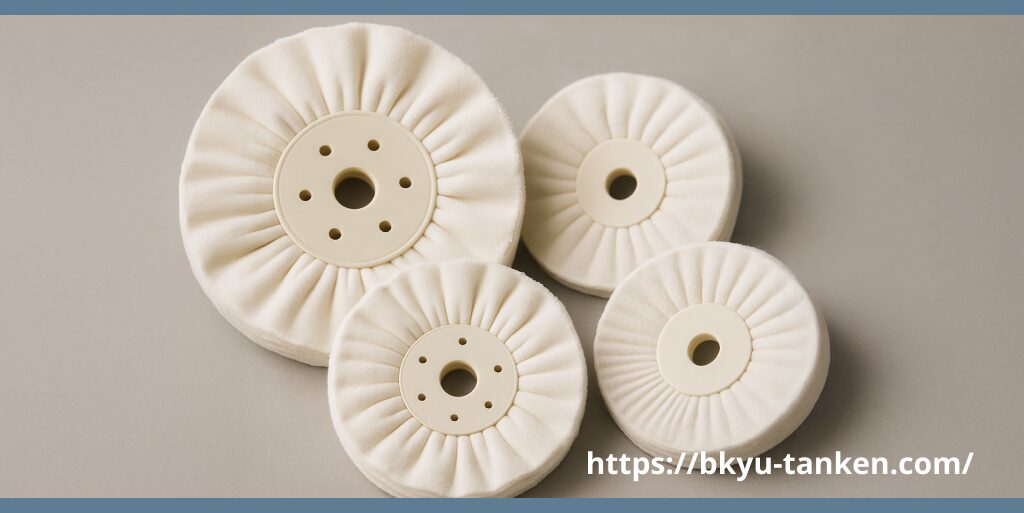
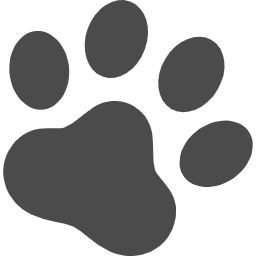
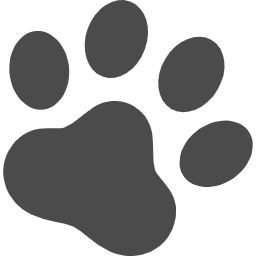
② サイザルバフ:粗研磨・中研磨のパワーヒッター
麻の一種であるサイザル麻の繊維を使ったバフです。綿バフに比べて硬く、強い研削力を持つのが特徴です。
- 主な用途:粗研磨~中研磨、素地調整、バリ取り、キズ取り。鉄、ステンレスなどの硬い金属。
- 特徴:高い研削力と耐久性。研磨熱が発生しやすい。
- 注意点:ワークへの当たりが強い。仕上げ研磨には不向き。
綿布とサイザルを組み合わせた「サイザル綿バフ」もあり、研削力と柔軟性のバランスを取っています。トリポリやエメリーといった粗~中仕上げ用研磨剤と組み合わせて使用されることが多いです。
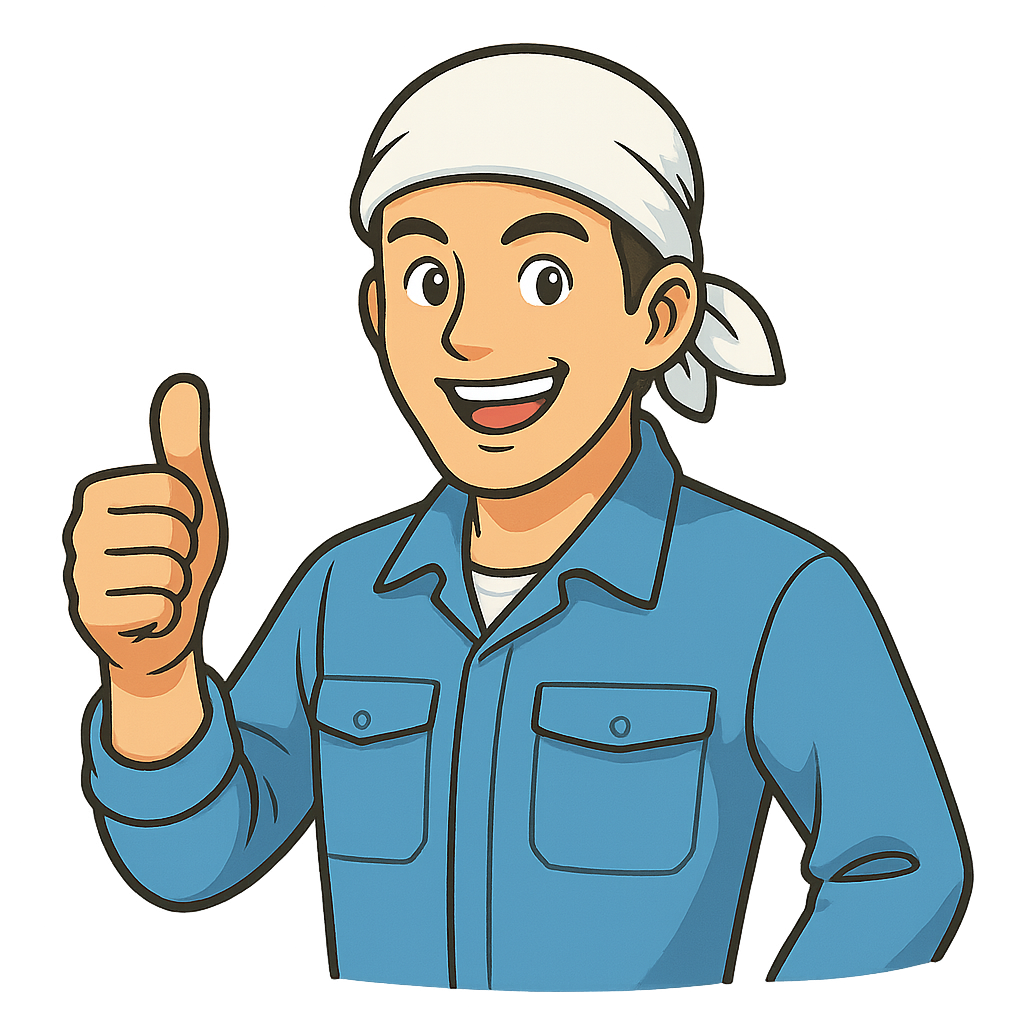
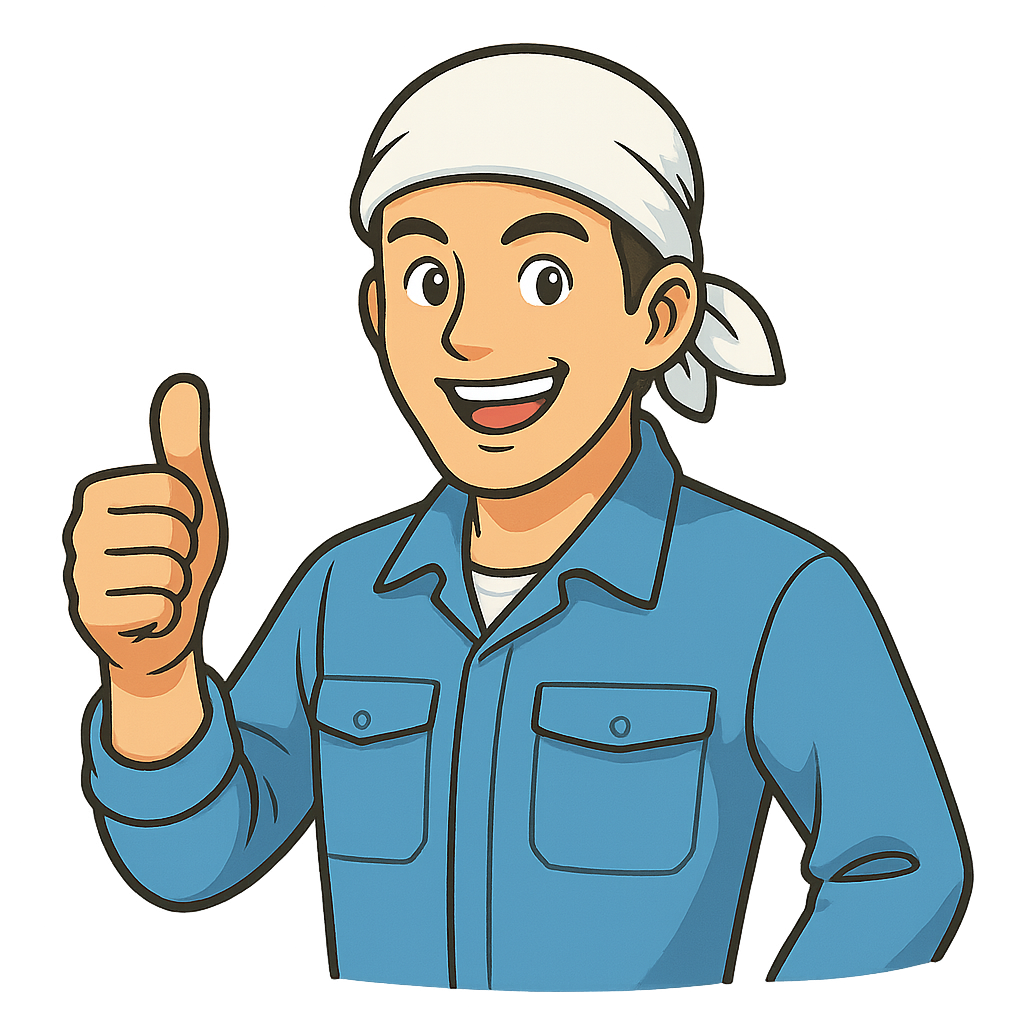
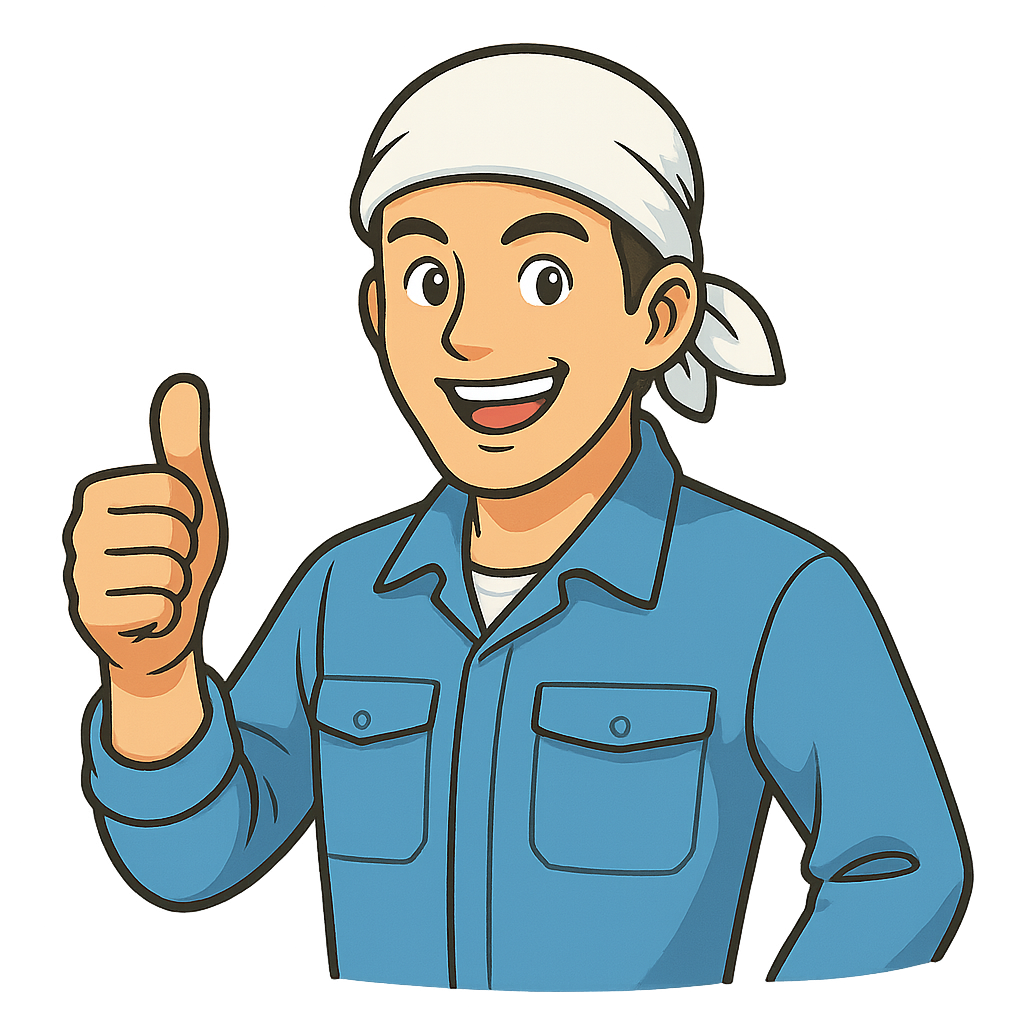
最初に深い傷やバリを効率よく取るなら、サイザルバフの出番です。ただし、削りすぎや焼け付きには注意が必要。回転数や押し当てる力を調整しながら使うのがコツですね。
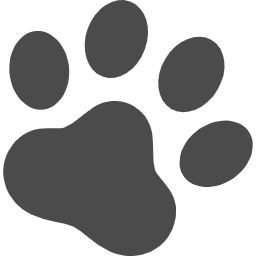
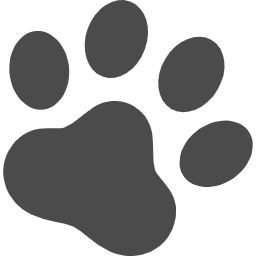
③ フェルトバフ:鏡面仕上げの最終兵器
羊毛などの繊維を圧縮して固めたフェルト製のバフです。非常に密度が高く、硬さがあり、型崩れしにくいのが特徴です。
- 主な用途:最終鏡面仕上げ、精密研磨。金型、ステンレス、貴金属など。
- 特徴:形状保持性が高く、平滑な面を出しやすい。研磨剤の保持性が非常に高い。
- 注意点:柔軟性に欠けるため、複雑な形状には不向き。価格は比較的高め。
ダイヤモンドペーストや酸化セリウムなどの超微粒子研磨剤と組み合わせて、最高レベルの鏡面仕上げを実現するために使用されます。
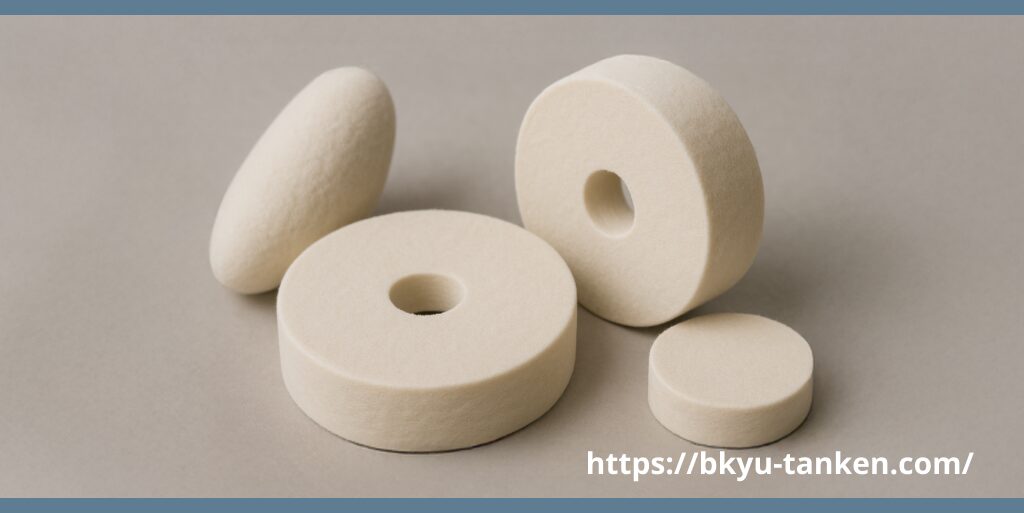
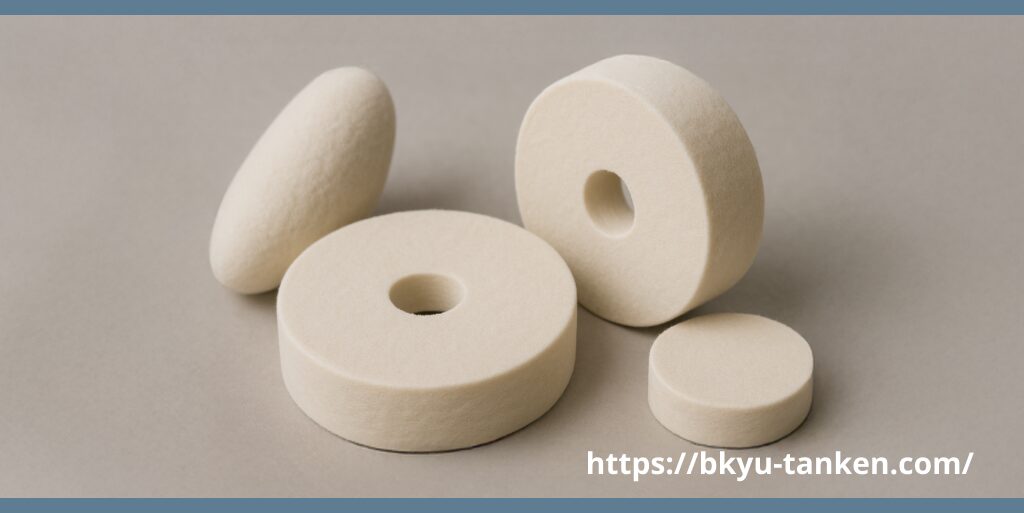
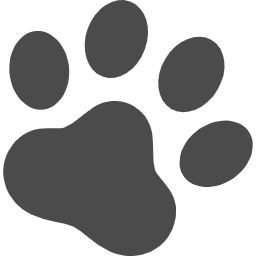
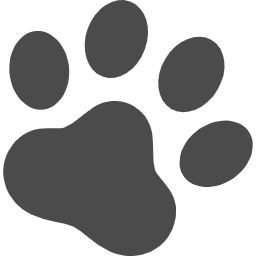
④ 不織布バフ(ナイロンバフ):万能性と安定性
ナイロンなどの合成繊維に研磨砥粒を固着させた不織布(ふしょくふ)を使ったバフです。砥粒の種類や密度によって、粗研磨から仕上げまで幅広い用途に対応できます。
- 主な用途:サテン仕上げ(ヘアライン)、クリーニング、微細バリ取り、酸化被膜除去、木工研磨など。
- 特徴:目詰まりしにくく、安定した研磨力が持続する。水や油を使っても性能が落ちにくい(湿式研磨にも対応)。弾力性がある(クッション性)。
- 注意点:種類が多く、選定が難しい場合がある。
研磨剤を別途塗布する必要がないタイプ(砥粒入り)も多く、手軽に均一な仕上げ面を得られるのがメリットです。金属だけでなく、木材や樹脂の研磨にも使われます。
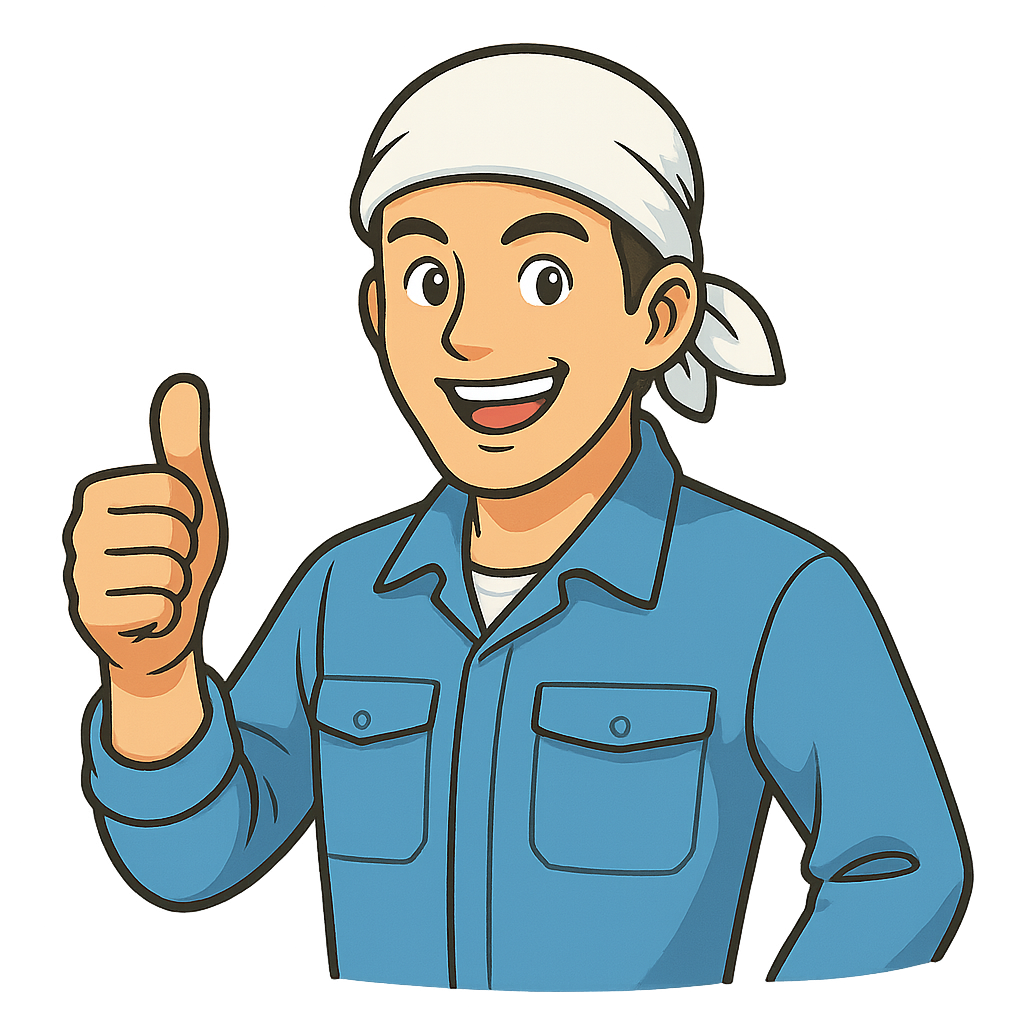
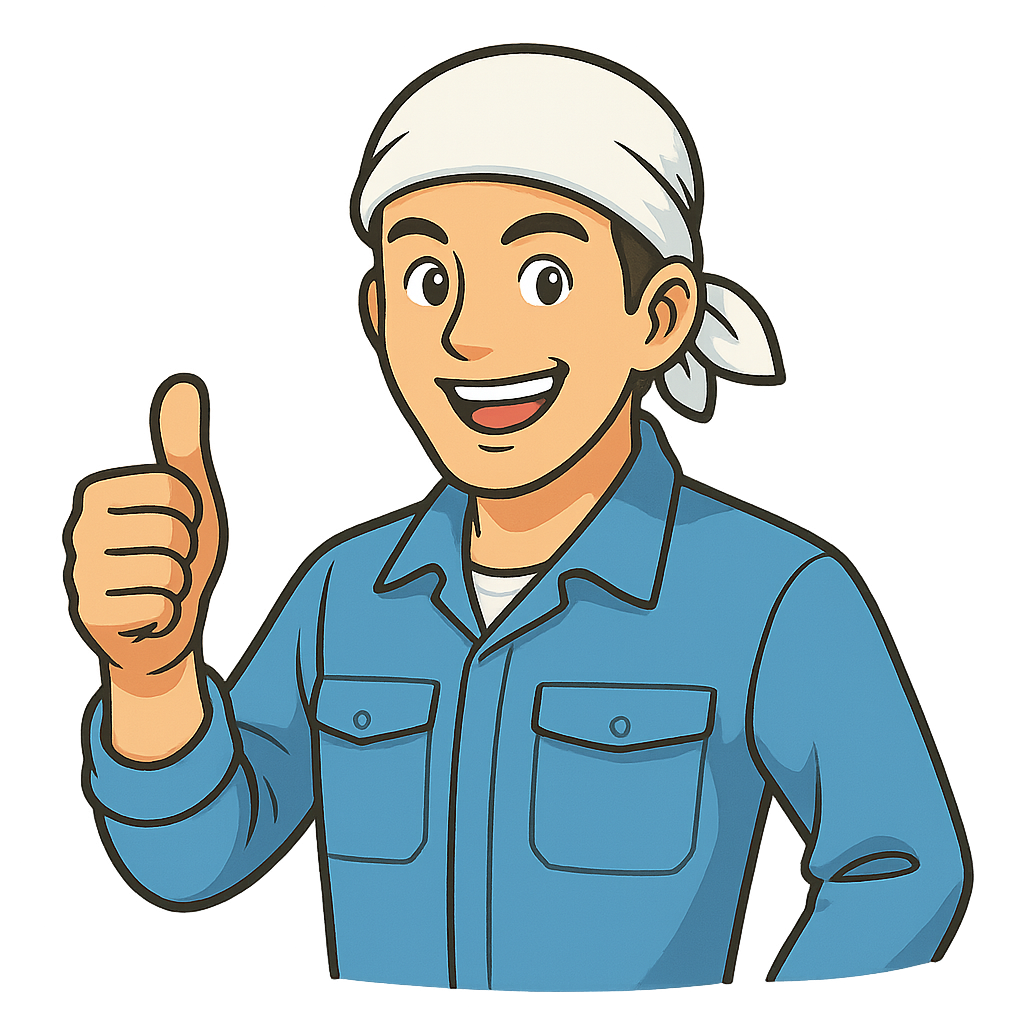
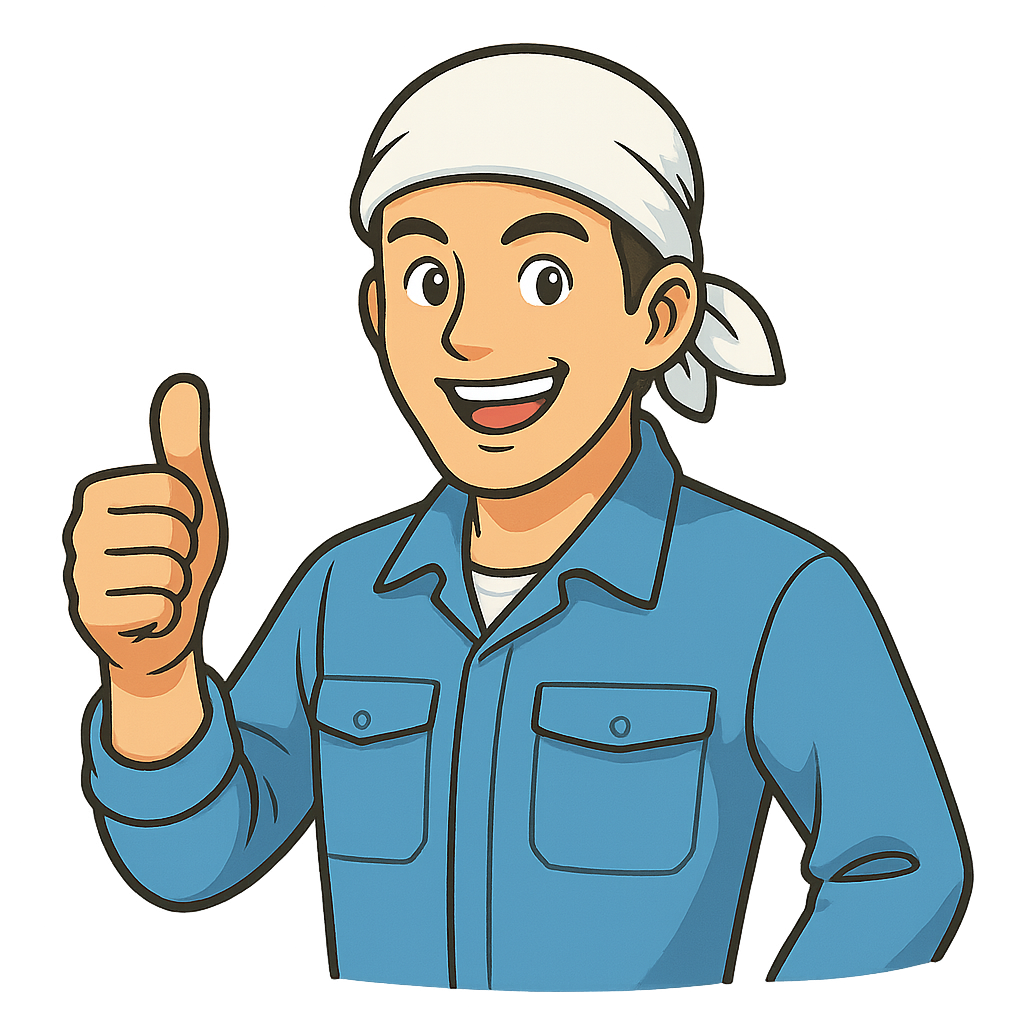
不織布バフは、「磨きすぎず、均一な仕上がり」にしたい時に重宝しますね。特にステンレスのヘアライン仕上げなんかには欠かせません。砥粒の粗さ(番手)選びがポイントになります。
⑤ その他(ウール、合成繊維など)
上記以外にも、ウール(羊毛)バフ(フェルトより柔らかく、塗料の磨きなどに使われる)、特殊な合成繊維を使ったバフなど、様々な種類のバフが存在します。特定の用途に特化したものが多いですが、目的に合わせてこれらを検討することも有効です。
【形状・構造別】バフ研磨ホイールの選び方
バフの性能は、材質だけでなく、その形状や構造によっても変わってきます。ここでは代表的な3つのタイプを見ていきましょう。
① プリーツ(ひだ)タイプ:冷却性と追従性
布を放射状に折り畳んで(ひだ状にして)作られたバフです。回転すると遠心力でひだが開き、風を取り込むため、冷却効果が高いのが特徴です。
- メリット:研磨熱が発生しにくいため、熱に弱い材質(アルミ、樹脂など)や、長時間の研磨に適している。柔軟性があり、ワークの凹凸によく馴染む(追従性が高い)。
- デメリット:構造上、ルーズタイプよりは硬め。
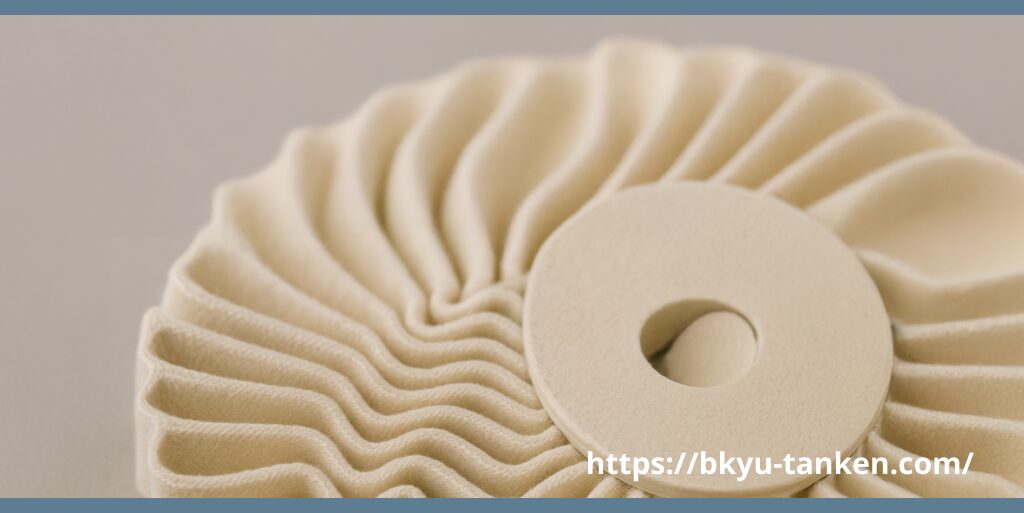
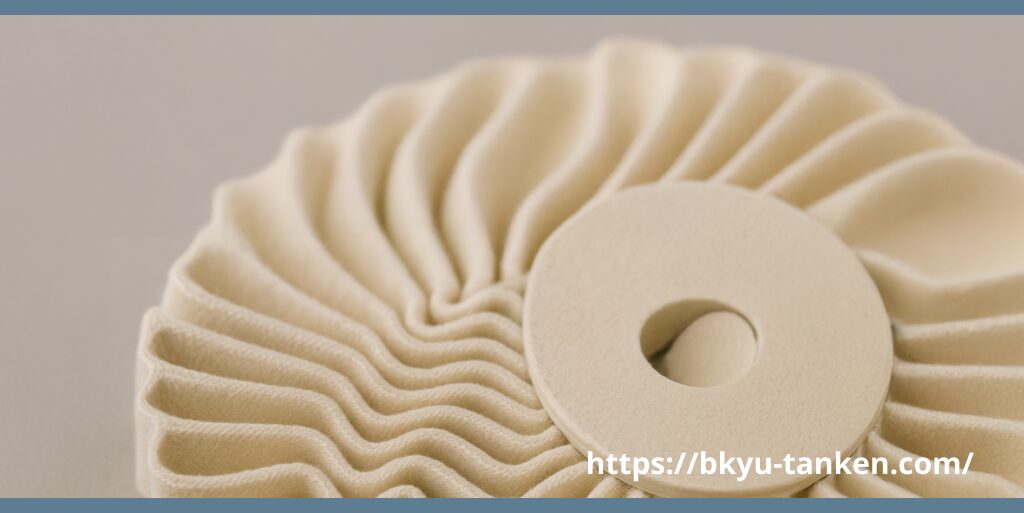
② 縫い合わせ(ステッチ)タイプ:硬さと研磨力
複数枚の布を同心円状に縫い合わせて強度を高めたバフです。縫い目の間隔やパターンによって硬さを調整できます。
- メリット:型崩れしにくく、硬さがあるため研削力が高い。平滑な面の研磨や、ある程度の圧力をかけて研磨したい場合に適している。
- デメリット:柔軟性はプリーツやルーズに劣る。研磨熱が発生しやすい。
縫い目の数が多いほど硬くなり、研削力が増します。粗磨き~中仕上げに使われることが多いタイプです。
③ ルーズ(オープン)タイプ:柔軟性と最終仕上げ
布を単純に重ねて中心部だけを固定した、縫い目のないバフです。最も柔軟性に富んでおり、ワークへの当たりが柔らかいのが特徴です。
- メリット:複雑な形状や曲面にもよく馴染む。最終仕上げや、傷をつけたくないデリケートな素材の研磨に適している。
- デメリット:研削力は低い。型崩れしやすい。
主に綿やネルなどの柔らかい素材で作られ、最終の艶出し(鏡面仕上げ)工程で活躍します。
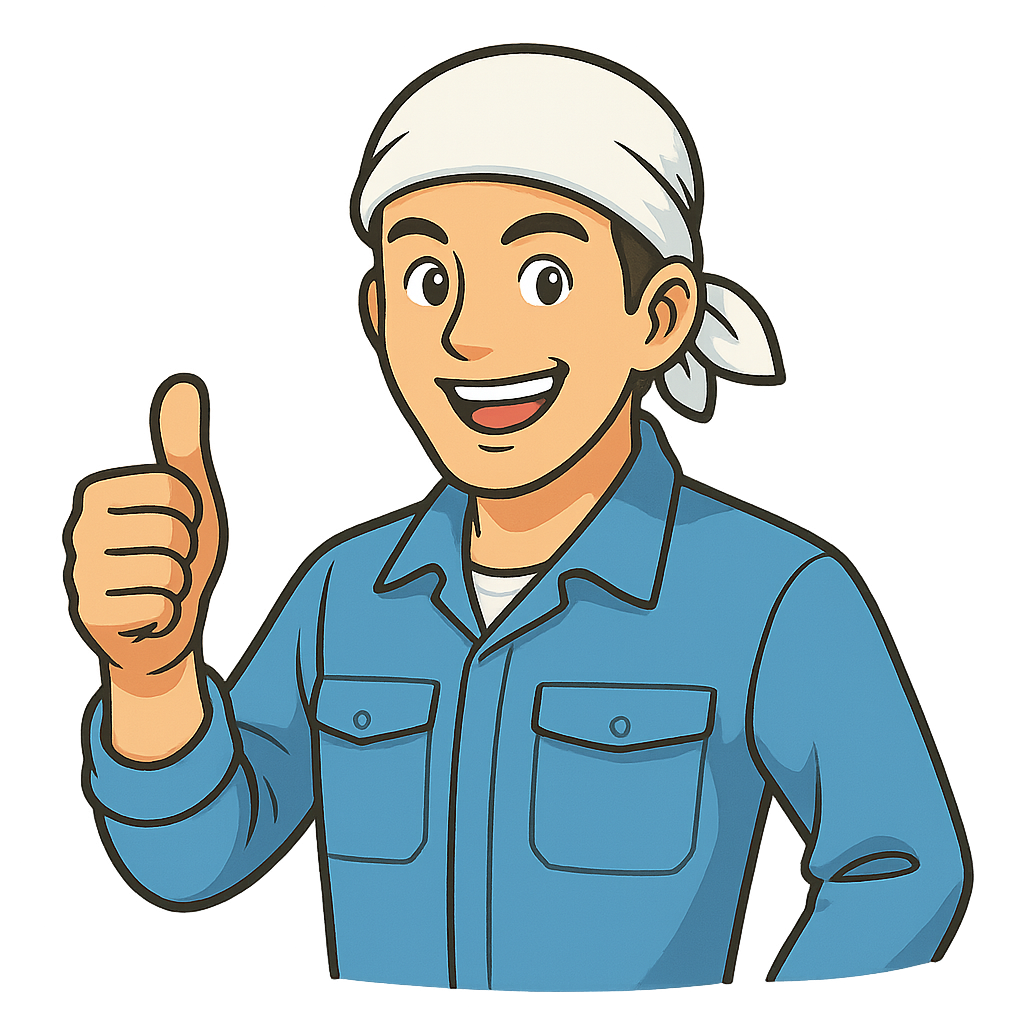
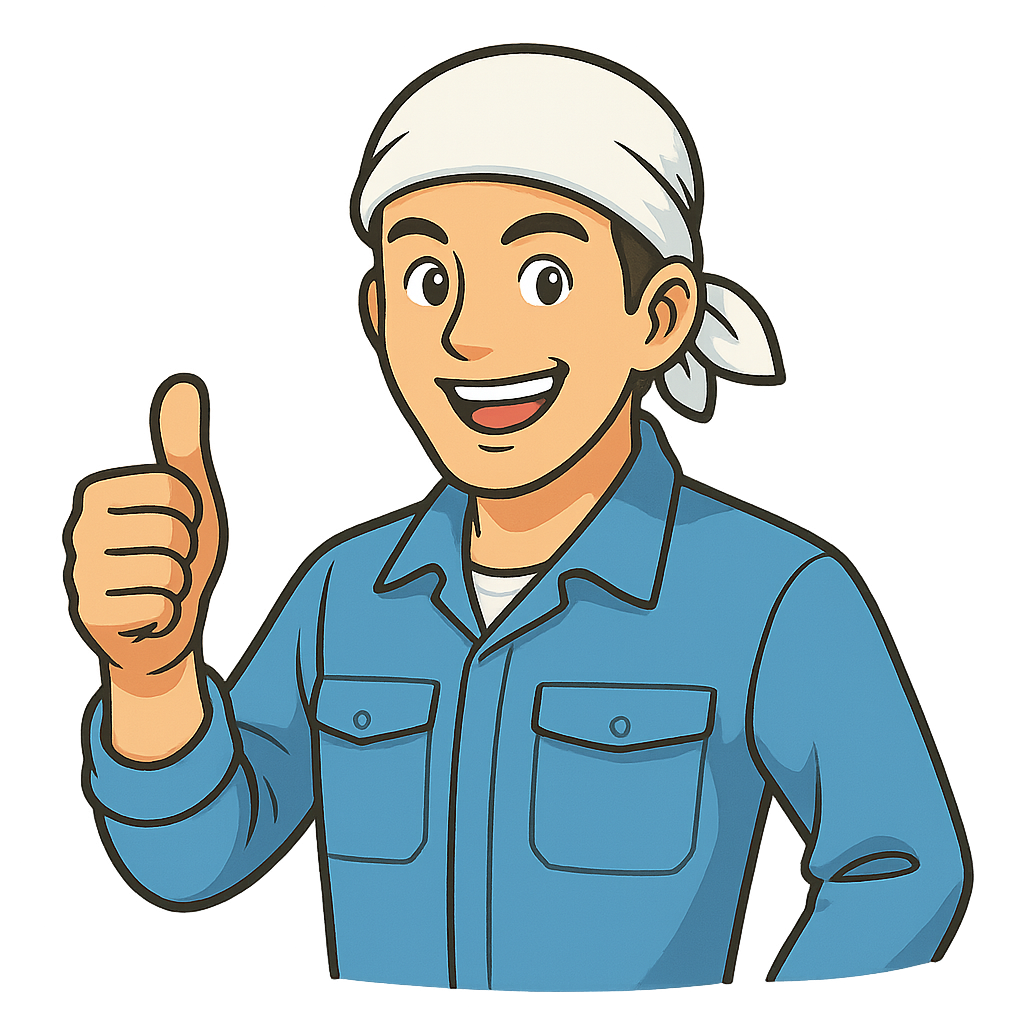
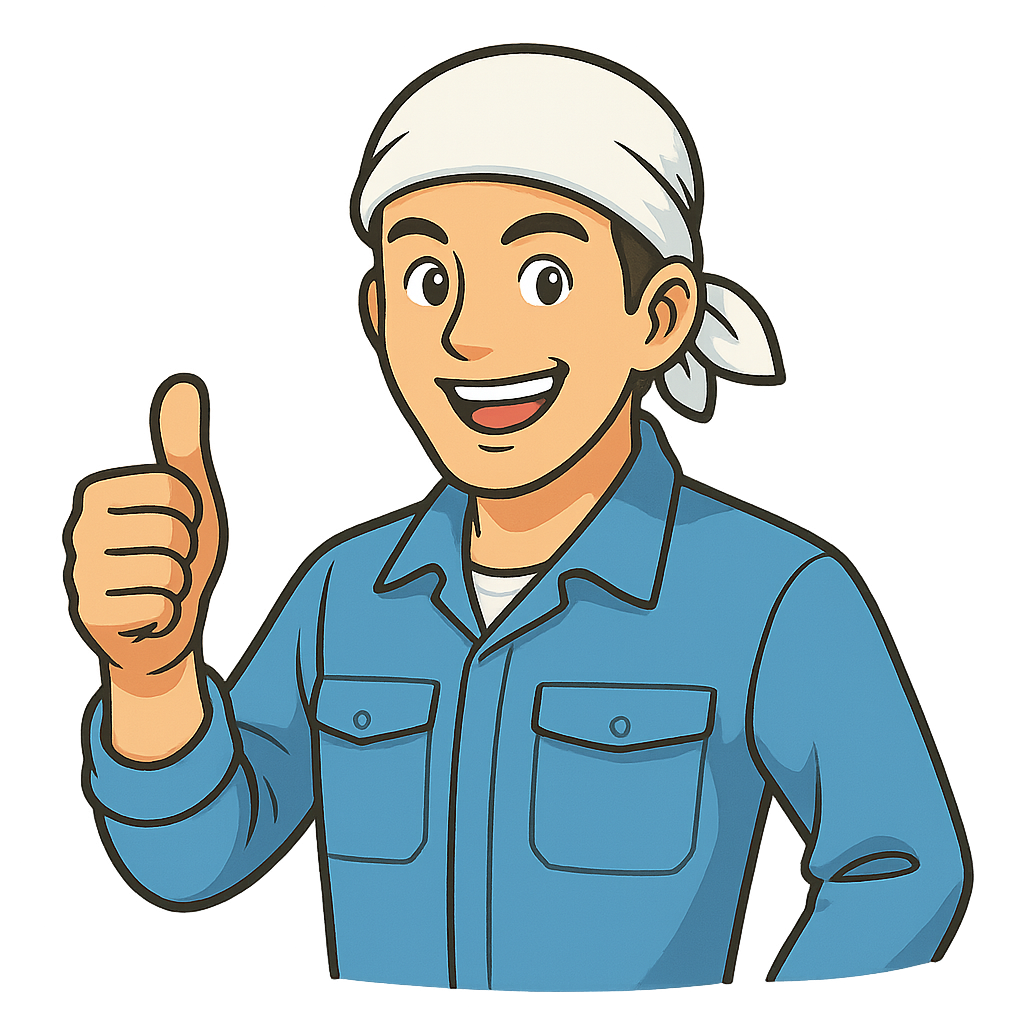
同じ材質のバフでも、この構造の違いで使い勝手が全く変わります。例えば、同じ綿バフでも、粗磨きならステッチ、中仕上げならプリーツ、最終仕上げならルーズ、といった使い分けが考えられますね。
見逃し厳禁!バフ研磨ホイールの交換目安
「まだ使えるかも…」と思って古いバフを使い続けると、品質低下や思わぬトラブルの原因になります。ここでは、バフの交換時期を見極めるための具体的な判断基準を解説します。
① 見た目での判断基準(摩耗、型崩れ、焼け)
最も分かりやすいのが、見た目の変化です。
- 摩耗:新品時に比べて〔==外径が著しく小さくなった==〕。特に、フランジ(取付金具)径に近づいてきたら限界です。
- 型崩れ:バフの形状が崩れて、いびつになっている。回転させた時にブレが大きい。
- 繊維のほつれ・脱落:布バフの場合、糸が過度にほつれたり、繊維の塊が飛散したりする。
- 焼け・硬化:研磨熱でバフ表面が黒っぽく焼けたり、硬化したりしている。研磨剤が溶けて固まっている(グレーズ)。
- 目詰まり:バフ表面に研磨カスや研磨剤が詰まって、カチカチになっている。
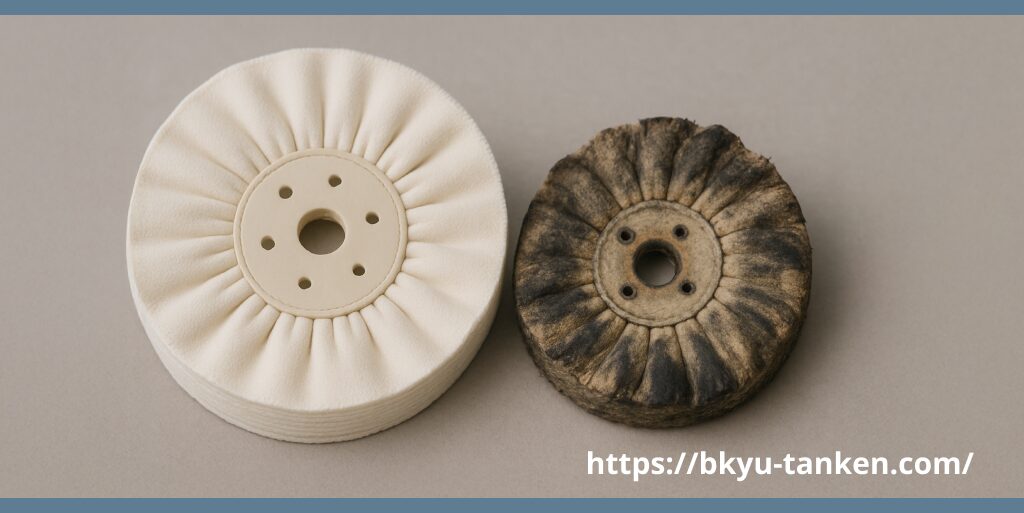
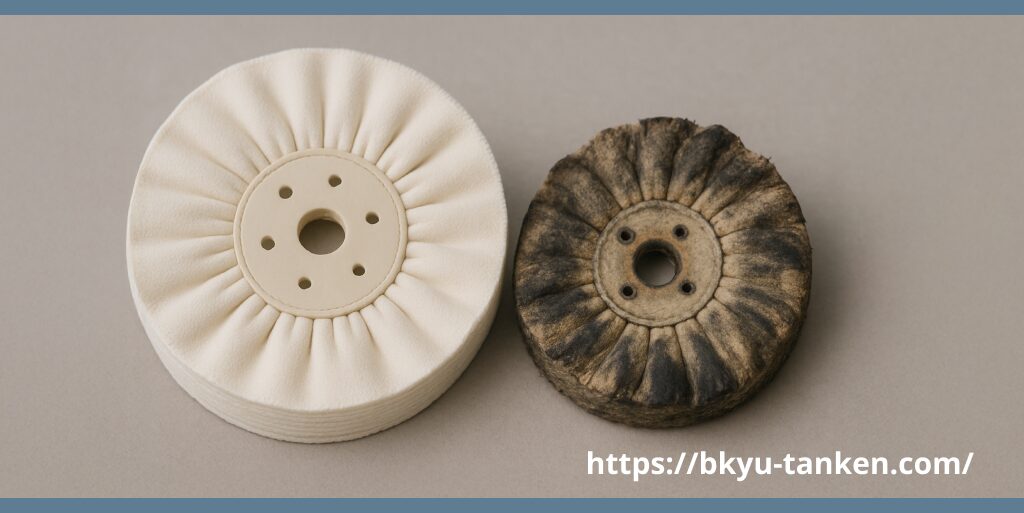
これらの兆候が見られたら、交換を検討すべきサインです。
② 研磨能力の低下(時間、仕上がり品質)
見た目では分かりにくくても、性能が低下している場合があります。
- 研磨に時間がかかる:以前と同じように磨いても、なかなか傷が取れない、光沢が出ない。
- 仕上がり品質の悪化:研磨ムラが出る、変なスジが入る、狙った光沢度にならない。
- 研磨剤のノリが悪い:バフに研磨剤がうまく付着しなくなった。
これらの変化を感じたら、バフの研磨能力が落ちている証拠です。無理に使い続けると、作業効率が悪化するだけでなく、不良品を出す原因にもなります。
③ 振動や異音の発生
バフが摩耗したり、型崩れしたり、あるいは研磨カスが不均一に付着したりすると、回転バランスが崩れて振動や異音が発生することがあります。
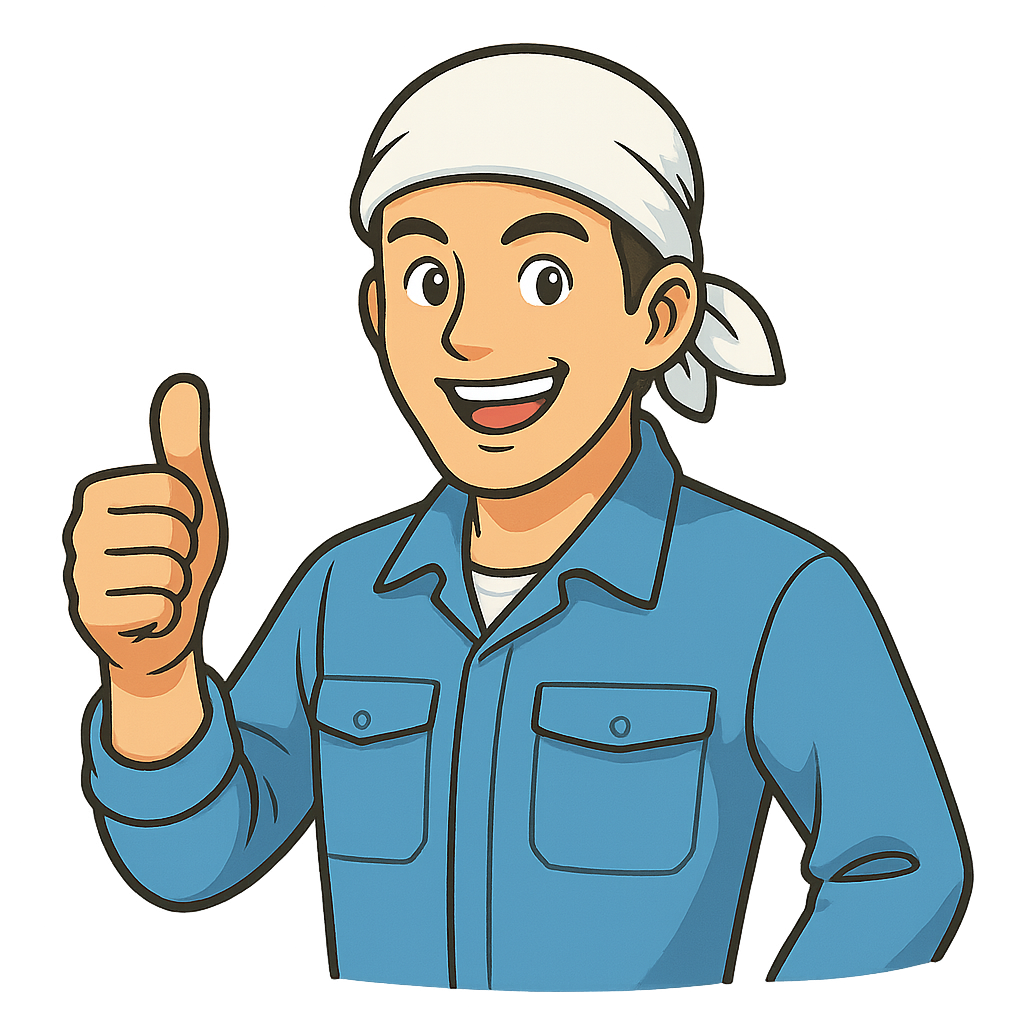
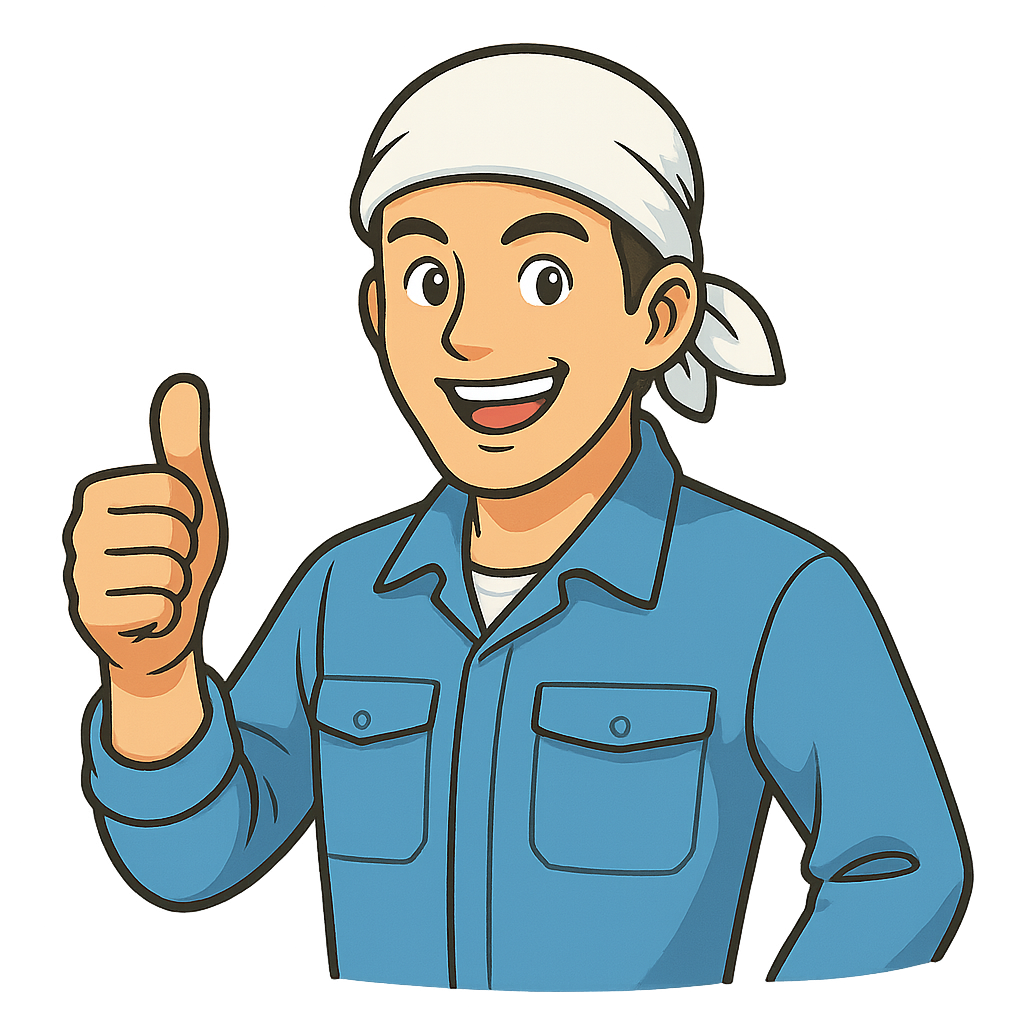
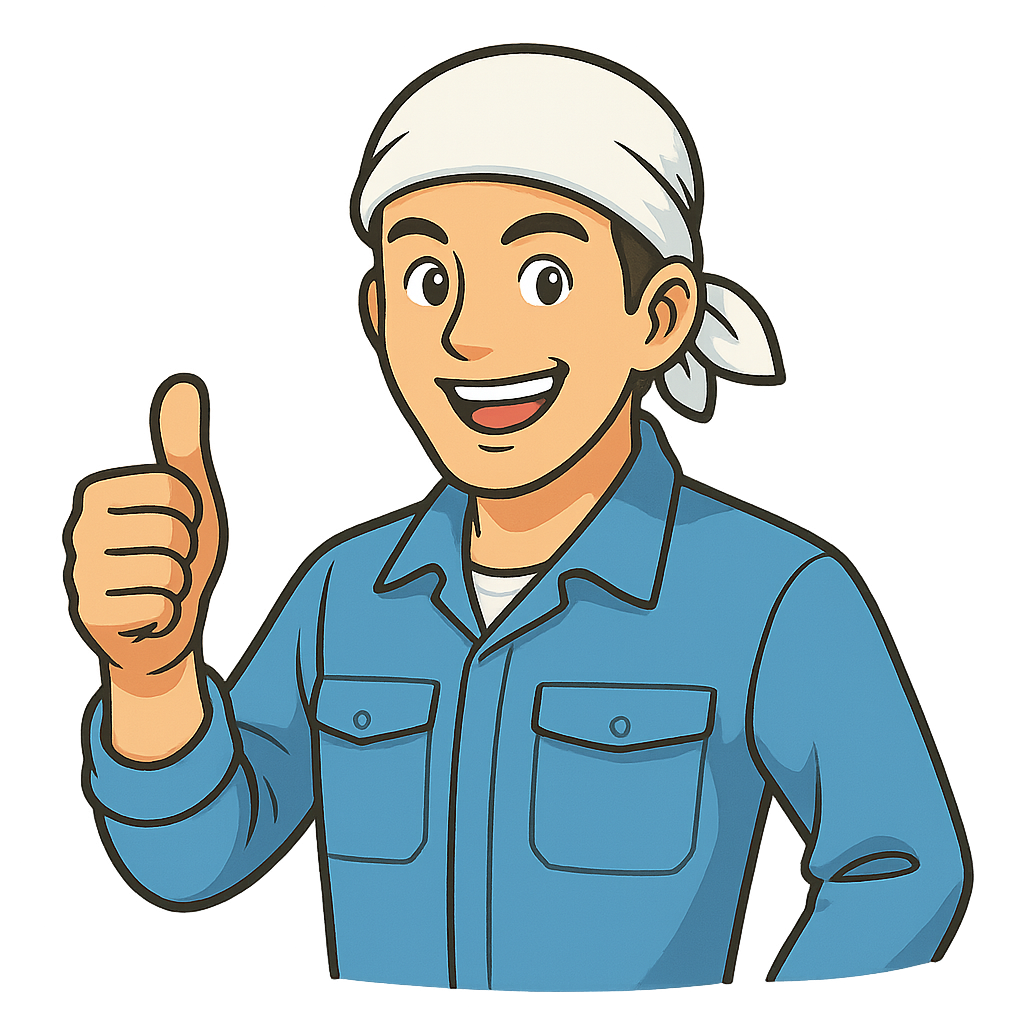
「いつもと違う振動や音がするな」と感じたら、要注意! これはバフの異常だけでなく、研磨機本体のトラブルの可能性もありますが、まずはバフの状態を確認してください。異常な振動は、作業者に負担をかけるだけでなく、大きな事故につながる危険性もあります。
交換を怠るリスク:品質低下と事故の危険性
交換時期を過ぎたバフを使い続けることは、「百害あって一利なし」です。
- 品質の低下:研磨ムラ、キズ、光沢不足など、製品の価値を損なう。
- 作業効率の悪化:研磨に時間がかかり、生産性が低下する。
- コストの増加:不良品の発生、手直しの工数増、研磨剤の無駄遣いにつながる。
- 事故のリスク:バフが破損して飛散したり、振動でワークを弾いたりする危険性がある。
「もったいない」という気持ちは分かりますが、トータルで見れば、適切なタイミングで交換することが、結果的にコスト削減と安全確保につながるのです。
バフ研磨ホイールの寿命を延ばすコツ
適切な交換はもちろん重要ですが、できるだけバフを長持ちさせ、コストを抑えたいと考えるのも当然です。ここでは、バフの寿命を延ばすための基本的なコツを 3 つご紹介します。
① 最適な研磨剤(コンパウンド)の選定と塗布量
バフの材質と研磨剤の相性は非常に重要です。相性が悪いと、バフの摩耗が早まったり、目詰まりしやすくなったりします。また、研磨剤の塗布量が多すぎても少なすぎても、バフに負担がかかります。
- 選定:バフメーカーや研磨剤メーカーが推奨する組み合わせを参考に、ワーク材質と目指す仕上げに合った研磨剤を選びましょう。
- 塗布量:一度に大量に塗布せず、少量をこまめに塗布するのが基本です。塗布しすぎは目詰まりの原因になります。
② 適正な回転数と圧力の維持
研磨機(バフモーター、グラインダーなど)の回転数が高すぎたり、ワークをバフに押し付ける圧力(研磨圧)が強すぎたりすると、過剰な摩擦熱が発生し、バフの焼けや早期摩耗の原因となります。
- 回転数:バフの直径や材質、ワーク材質によって推奨される周速(回転速度)があります。取扱説明書などを確認し、適切な設定で使用しましょう。
- 研磨圧:必要以上に強く押し付けないことが大切です。軽い力で、バフと研磨剤の力で磨くイメージを持ちましょう。
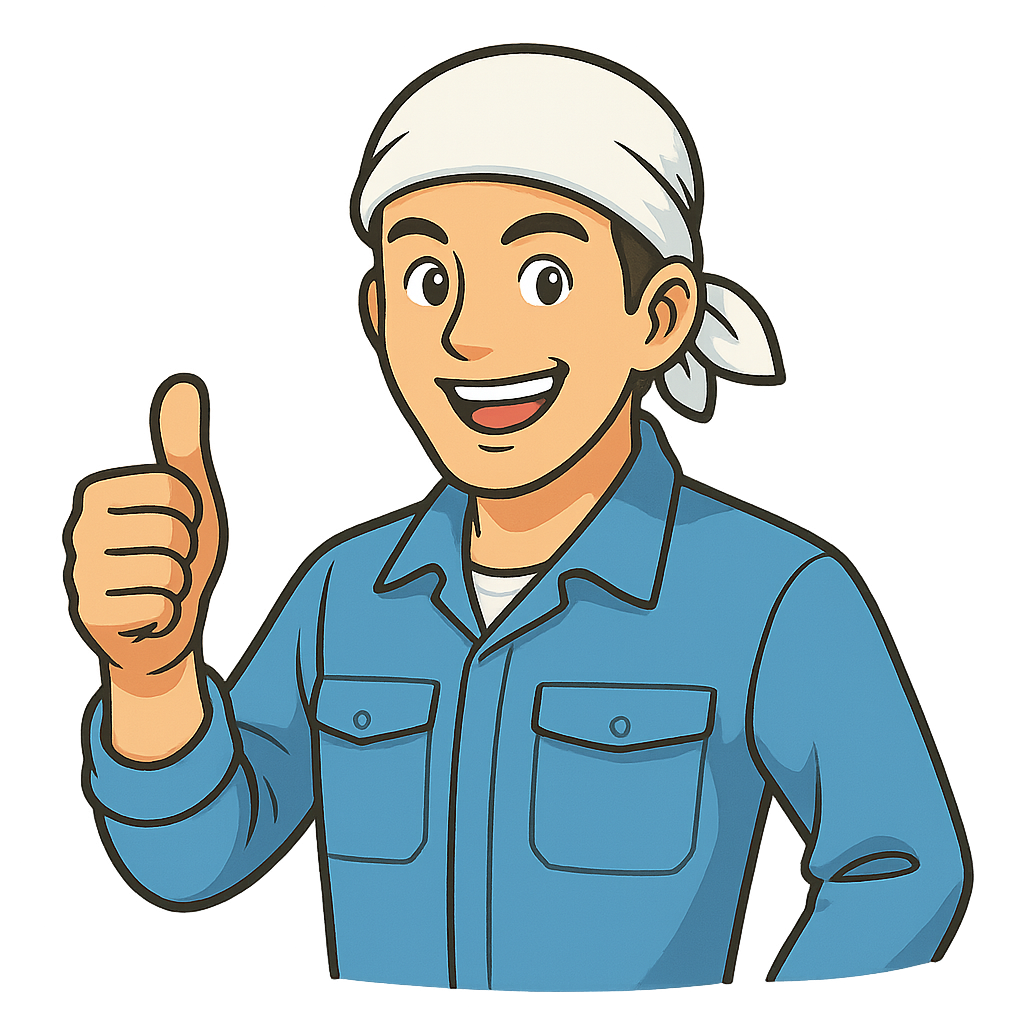
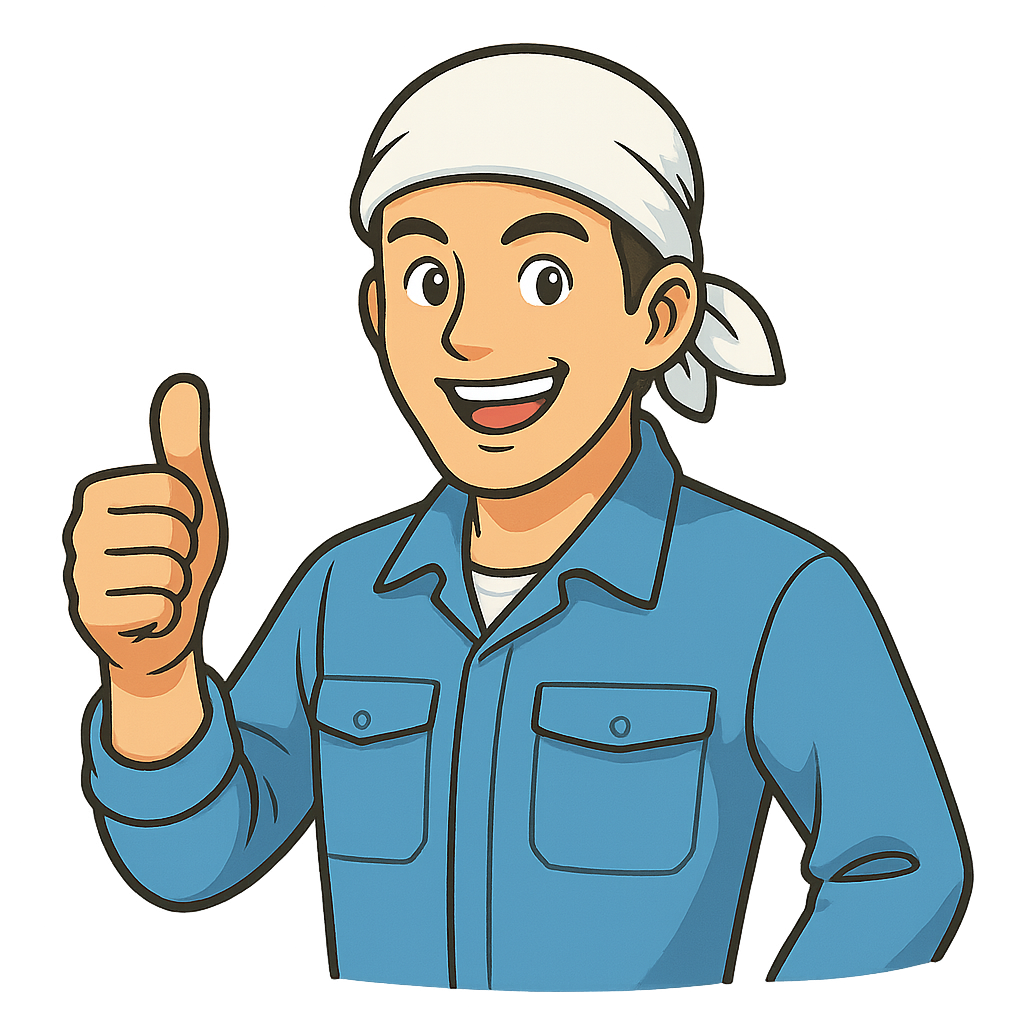
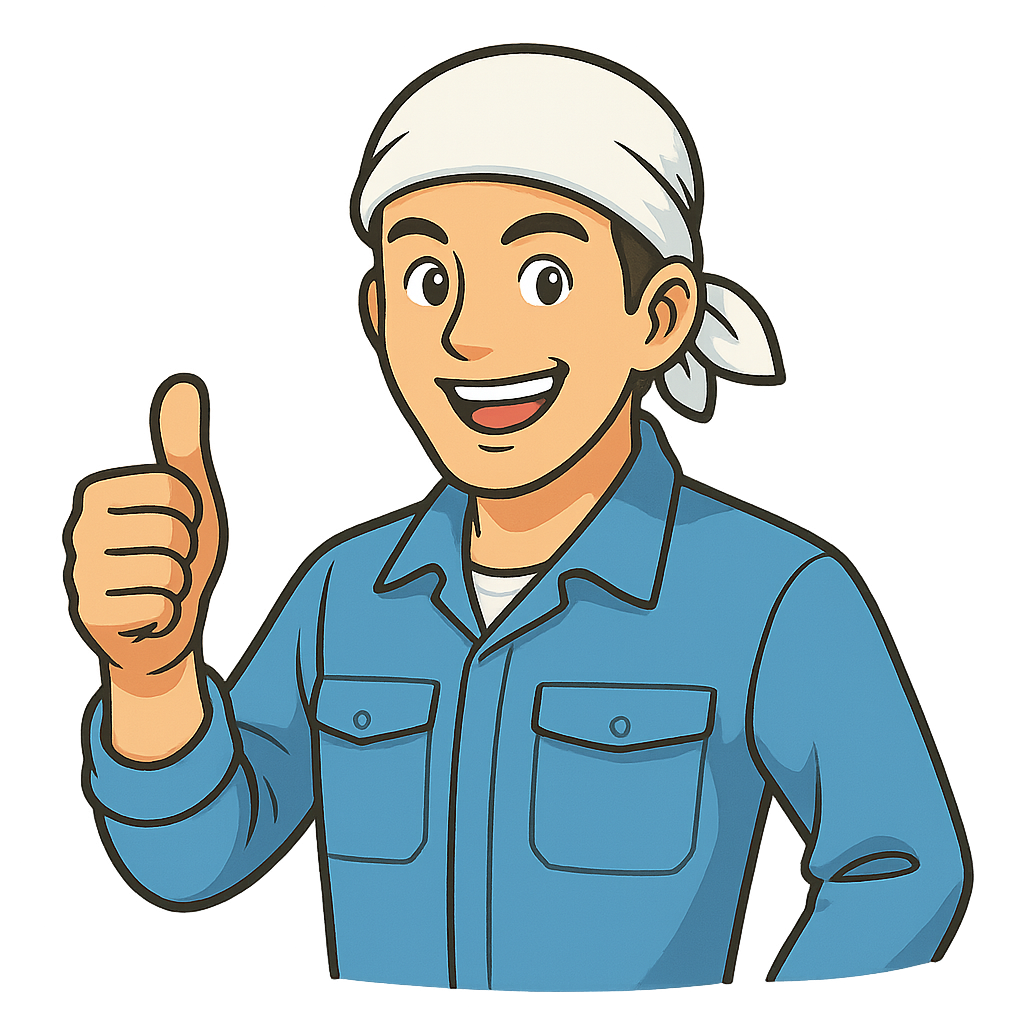
特に「早く終わらせたい」と焦って、つい力を入れすぎてしまうことがありますが、逆効果になることが多いです。適正な回転数と圧力で、丁寧に作業することが、結果的にバフを長持ちさせ、綺麗な仕上がりにもつながります。
③ バフの「目立て(ドレッシング)」
使用しているうちに、バフ表面には研磨カスや固まった研磨剤が付着し、目詰まりを起こします。これを放置すると研磨力が低下し、発熱の原因にもなります。
そこで重要になるのが「目立て(ドレッシング)」です。ワイヤーブラシや専用のドレッサー(目立て工具)を使って、バフ表面の目詰まりを取り除き、バフの切れ味を回復させる作業です。
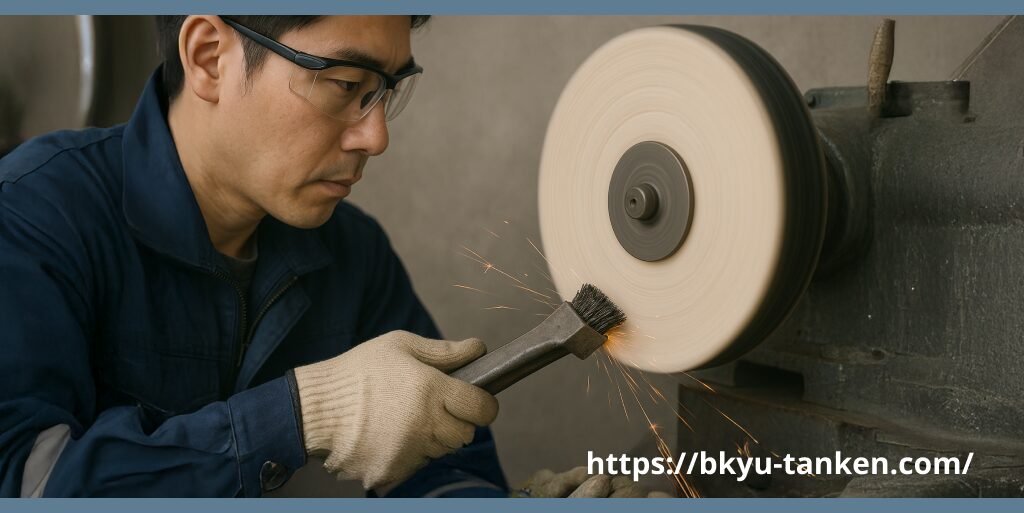
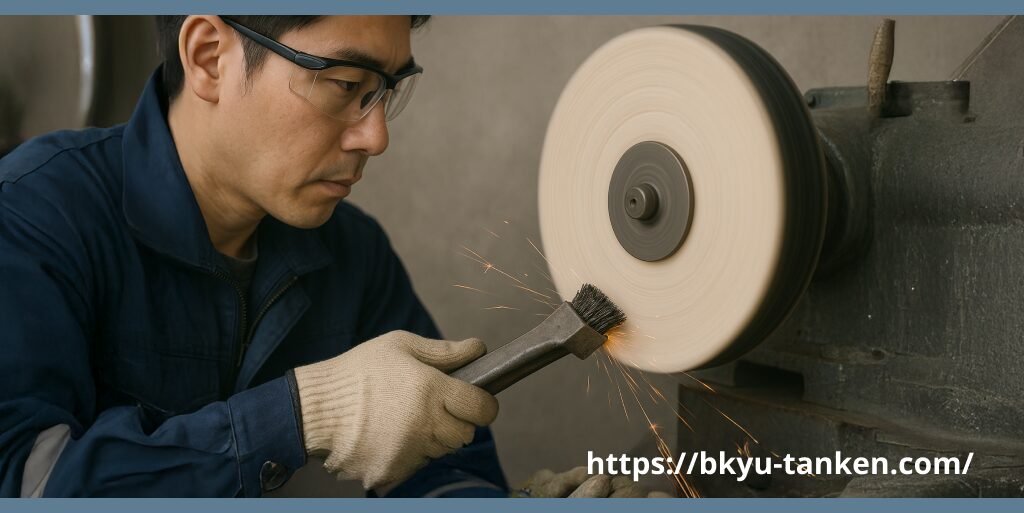
定期的に目立てを行うことで、バフの寿命を延ばし、常に良好な研磨状態を保つことができます。ただし、やりすぎるとバフを過剰に消耗させてしまうので注意が必要です。
まとめ
今回は、バフ研磨ホイールの種類と特徴、形状による選び方、そして最も重要な交換目安と長持ちさせるコツについて解説しました。
バフ選びのポイント
- 材質:仕上げレベルとワーク材質に合わせて選ぶ(綿、サイザル、フェルト、不織布など)。
- 形状/構造:冷却性、研磨力、柔軟性のバランスで選ぶ(プリーツ、縫い合わせ、ルーズ)。
交換のサイン
- 見た目:摩耗、型崩れ、焼け、ほつれ、目詰まり。
- 性能:研磨時間増、品質低下、研磨剤のノリ悪化。
- 異常:振動、異音。
長持ちのコツ
- 最適な「研磨剤」の選定と適量塗布。
- 適正な「回転数」と「圧力」の維持。 定期的な「目立て(ドレッシング)」。
適切なバフを選び、交換時期を見逃さず、日々のメンテナンスを怠らないことが、高品質な研磨加工を安定して行い、トータルコストを削減するための基本です。ぜひ、今回の記事を参考に、皆さんの現場でのバフの使い方を見直してみてください。
「うちの製品にはどのバフが最適?」「もっと効率的な研磨方法は?」など、具体的なお悩みがあれば、いつでも金属研磨ドットコムにご相談くださいね!
コメント