製造現場で使われる金属研磨とは?基本の「き」から分かる技術解説
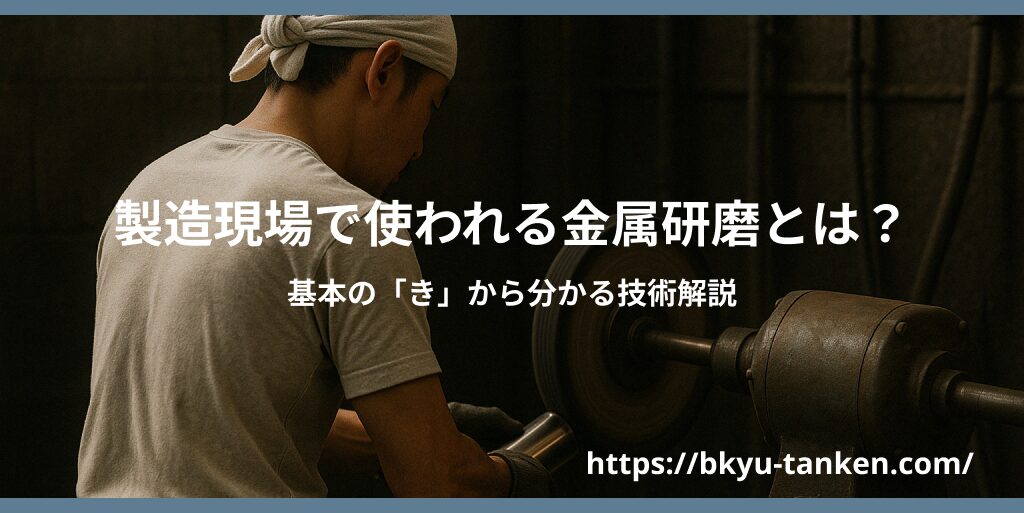
金属製品の製造現場で、表面処理は製品の機能性と美観を左右する重要な工程です。特に金属研磨は、多くの中小製造業で日常的に行われている作業でありながら、「なんとなくやっている」という状態の現場も少なくありません。
本記事では、金属加工における研磨作業の基本を解説します。新しく研磨作業に携わることになった技術者の方、外注先の選定に悩む購買担当者の方、また設備導入を検討している生産技術部門の方々に向けて、研磨の目的から具体的な手法・設備選定のポイントまでを分かりやすく説明します。
研磨作業の技術的な側面だけでなく、品質トラブルの防止策や作業環境の改善まで踏み込んで解説することで、明日からの現場改善に役立てていただける内容となっています。金属研磨の”基本の基礎”を身につけて、より高品質な製品づくりに活かしましょう。
1. 金属研磨とは何か?基本概念と目的
金属研磨とは、金属表面の凹凸を平滑化し、目的に応じた表面性状を作り出す加工技術です。単に「ピカピカにする」だけでなく、製品の機能性向上や後工程の品質確保という重要な役割を担っています。
研磨の主な目的は以下の3つに分類できます。
- 外観品質の向上:光沢・美観の確保
- 機能性の付与:摩擦係数の制御、潤滑性向上
- 後工程の前処理:めっき・塗装下地の均一化
特に製造業では、「見た目の美しさ」だけでなく、部品の寸法精度や機能性を確保するための研磨が重要です。例えば、軸受け部品では摩擦抵抗を減らすための研磨が、医療機器では衛生面を考慮した鏡面研磨が求められます。
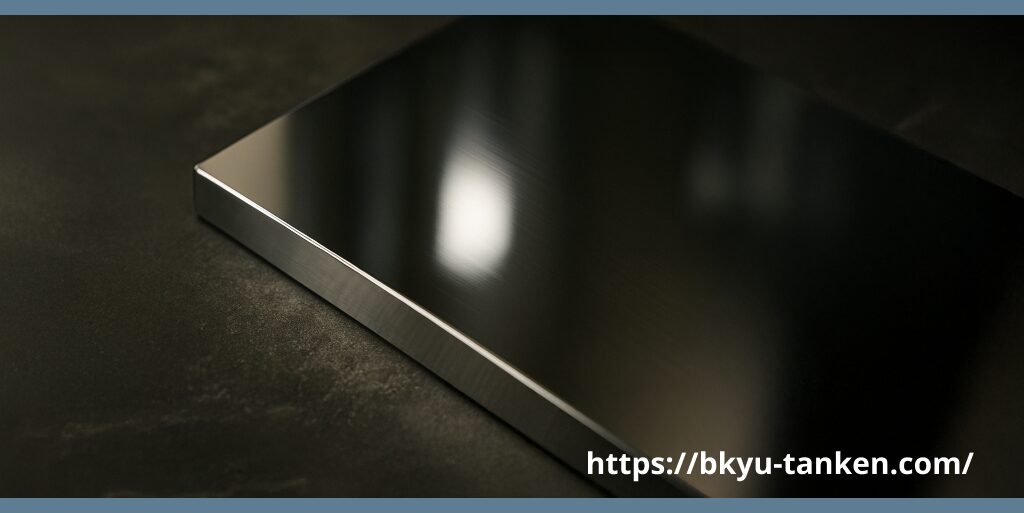
研磨が必要とされる業界と用途
研磨技術は様々な業界で活用されています。
- 自動車部品:エンジン内部品、外装パーツ
- 医療機器:手術器具、インプラント
- 食品機械:タンク内面、配管接続部
- 光学部品:レンズ金型、反射板
- 電子部品:コネクタ、筐体
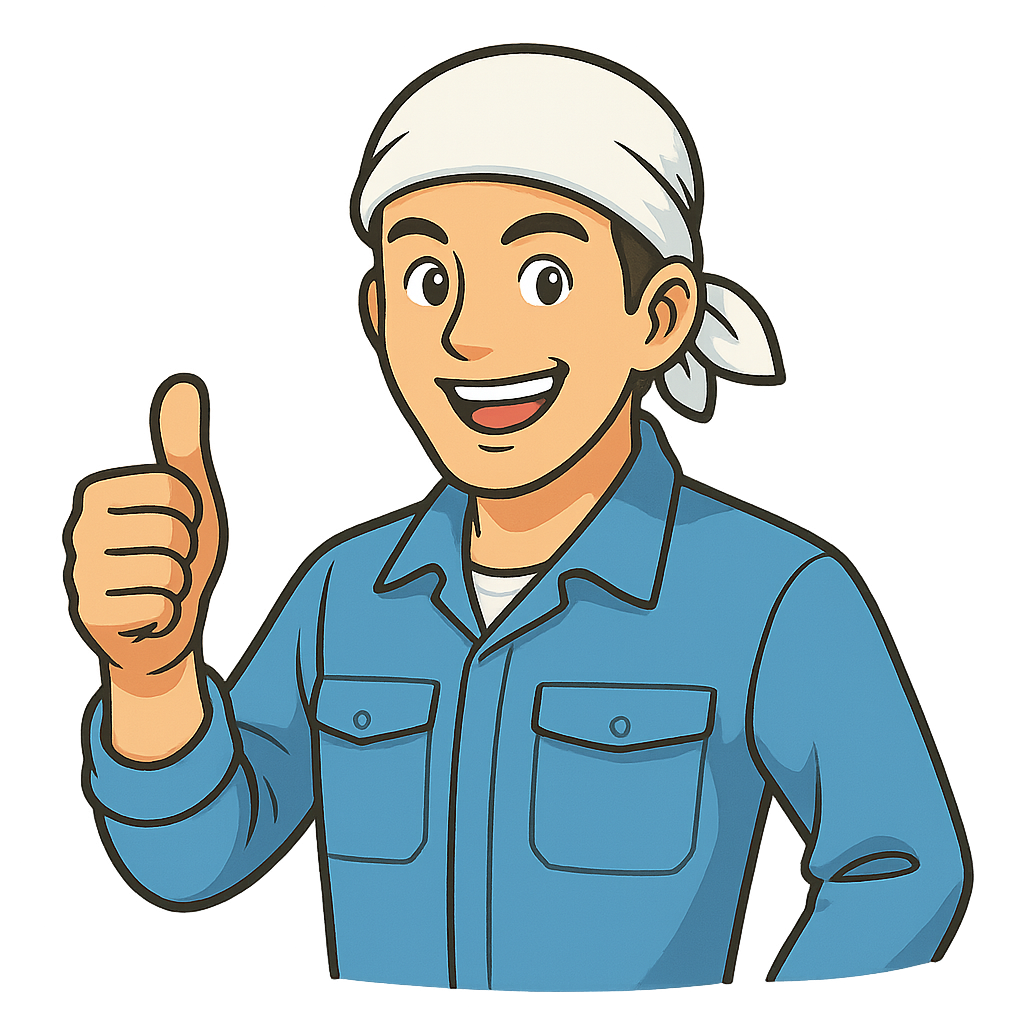
研磨の目的を明確にすることが重要です。「どの程度の表面粗さが必要か」「どのような機能が求められるか」を事前に整理しておくと、適切な研磨方法の選定につながります!
2. 主要な研磨方式と特徴【機械/手作業】
金属研磨には様々な方式があり、目的や対象物によって最適な手法が異なります。大きく分けると、機械研磨と手作業研磨の2つに分類できます。
機械研磨の種類と特徴
機械研磨は、動力を使って研磨材を金属表面に当てる方式です。生産性が高く、安定した品質が得られる利点があります。
① ベルト研磨
砥粒を塗布したベルトを回転させて研磨する方法です。平面や大きな曲面の研磨に適しています。
- 特徴:高い研削力、広い面積の処理が可能
- 適用例:板材、パイプ外周面
② バフ研磨
円盤状の布製バフに研磨剤(コンパウンド)を付けて回転させる方法です。鏡面仕上げに適しています。
- 特徴:美しい光沢が得られる、仕上げ工程に適する
- 適用例:装飾品、鏡面仕上げが必要な部品
③ 研削盤研磨
砥石を使用した精密研磨で、高い精度が要求される場合に使用します。
- 特徴:高い寸法精度、平面度の確保
- 適用例:金型部品、軸受け部品
④ バレル研磨(タンブリング)
研磨材と工作物を容器に入れて回転させる方法で、多数の小型部品を同時に処理できます。
- 特徴:大量処理が可能、人手がかからない
- 適用例:小型部品、バリ取り作業
手作業研磨の種類と特長
手作業研磨は、職人の技術と経験に基づいて行われます。複雑な形状や局所的な研磨に適しています。
① サンドペーパー研磨
研磨紙を使用して手作業で研磨する最も基本的な方法です。
- 特徴:道具が簡単、細部の研磨が可能
- 適用例:複雑形状、仕上げ工程
② ヤスリ研磨
金属製のヤスリを使用した研磨方法で、硬質材料の粗加工に適しています。
- 特徴:高い研削力、細部の成形が可能
- 適用例:溶接部の処理、バリ取り
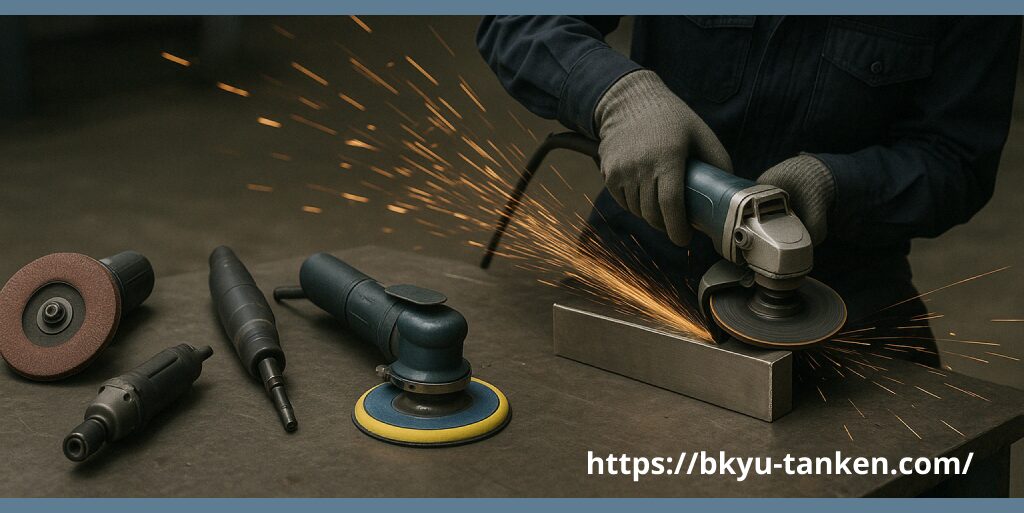
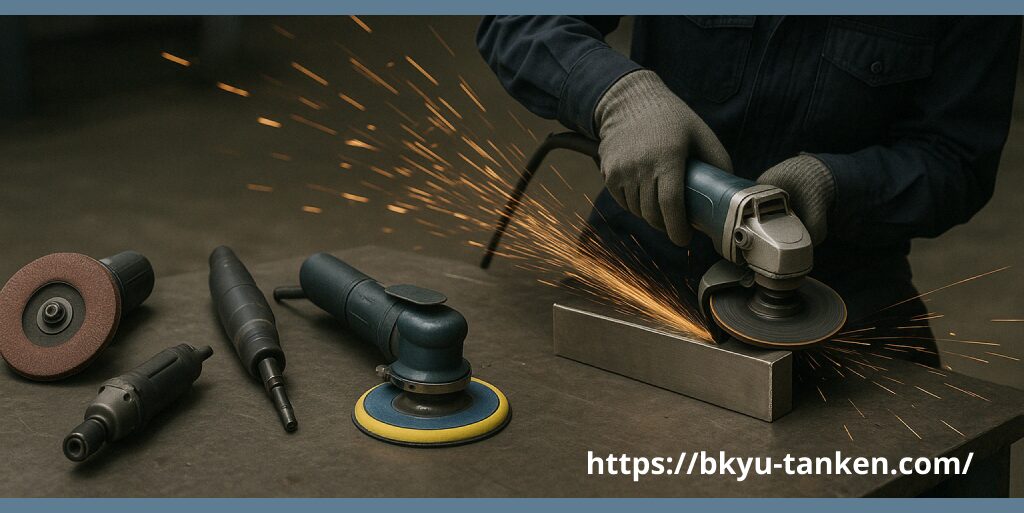
研磨方式の選定基準
研磨方式を選定する際の主なポイントは以下の通りです。
- 加工対象の材質(鉄系、アルミ、ステンレスなど)
- 求められる表面性状(粗さ、光沢など)
- 加工対象の形状・サイズ(平面、曲面、細部など)
- 生産量(少量多品種か大量生産か)
- コスト制約(設備投資、加工コスト)
これらの要素を総合的に判断し、最適な研磨方式を選定することが重要です。
3. 番手と表面粗さ Ra の関係を理解する
研磨作業では、砥粒の粒度(番手)と表面粗さ(Ra)の関係を理解することが重要です。番手は研磨材の粒子の大きさを表し、数字が大きいほど粒子が細かくなります。
番手(JIS規格)について
研磨紙やバフ材などには、粒度を表す「番手」が設定されています。JIS規格では、#(シャープ)の後に数字で表記されます。
番手区分 | 番手例 | 主な用途 |
---|---|---|
粗目 | #80~#180 | バリ取り、荒研磨 |
中目 | #240~#400 | 一般的な表面仕上げ |
細目 | #600~#1000 | 精密仕上げ |
超細目 | #1200~#4000 | 鏡面仕上げ前処理 |
表面粗さ Ra との関係
表面粗さは一般的に「Ra」(算術平均粗さ)で表されます。単位はμm(マイクロメートル)で、値が小さいほど表面が滑らかであることを示します。
番手 | 得られる表面粗さ Ra(μm) | 仕上がり状態 |
---|---|---|
#80 | 約3.2~1.6 | 肉眼で明らかな凹凸が見える |
#180 | 約1.6~0.8 | 指で触ると引っかかりを感じる |
#400 | 約0.8~0.4 | 鈍い光沢が出始める |
#800 | 約0.4~0.2 | 明確な光沢が現れる |
#1500 | 約0.2~0.1 | 高い光沢が得られる |
#3000以上 | 約0.1以下 | 鏡面状態に近づく |
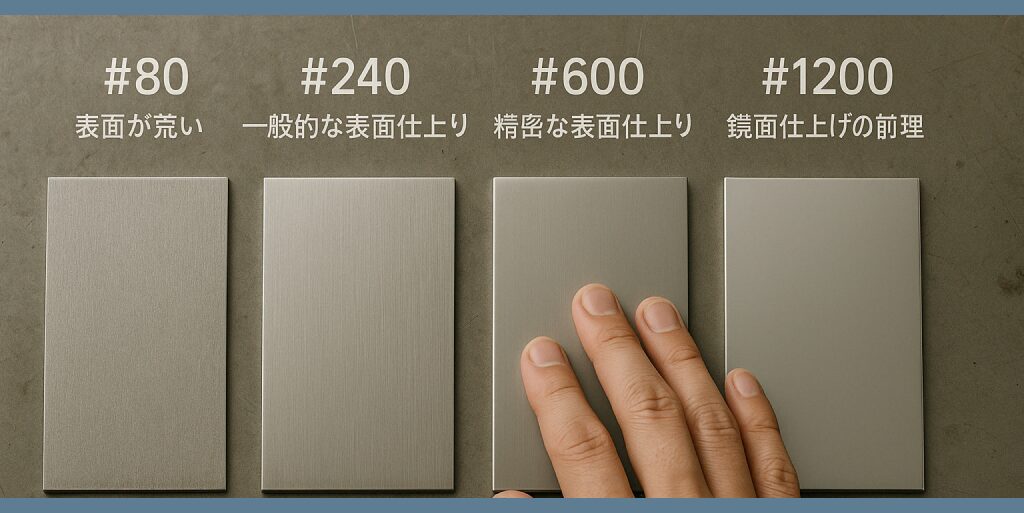
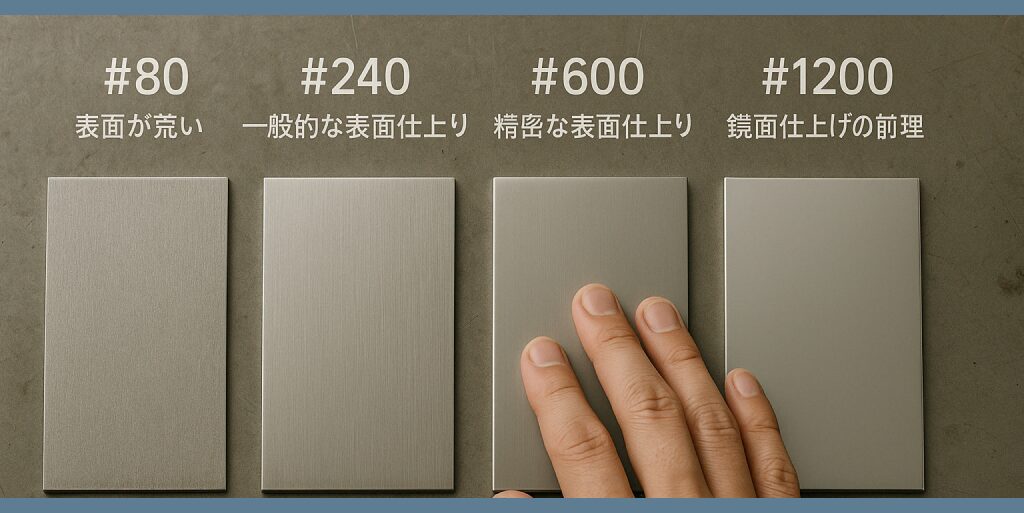
段階的な研磨の重要性
高品質な研磨仕上げを実現するためには、段階的に番手を上げていくことが重要です。いきなり細かい番手で研磨すると、前工程の傷が残ったり、作業効率が悪化したりする恐れがあります。
一般的な段階的研磨のステップは次のとおりです。
- 粗研磨:大きな凹凸や傷を除去(#80~#180)
- 中研磨:表面を均一に整える(#240~#400)
- 仕上げ研磨:光沢を出す(#600~#1000)
- 鏡面研磨:高い光沢を実現(#1200以上とバフ)
この段階的な工程を適切に行うことで、効率的に高品質な仕上がりを得ることができます。
4. 品質トラブル事例と対策ポイント
研磨作業では様々な品質トラブルが発生する可能性があります。ここでは、よくある問題とその対策を紹介します。
主な品質トラブルと発生原因
① 研磨ムラ・スジ
均一でない仕上がりや、特定方向に残る線状の痕跡です。
- 原因:研磨圧力の不均一、一方向のみの研磨、前工程の傷が残存
- 対策
研磨方向を交互に変える(クロス研磨)
段階的に番手を上げる
均一な圧力で研磨する
② 焼け
研磨熱による変色や材質変化です。特にステンレスで発生しやすい問題です。
- 原因:過度な研磨圧力、冷却不足、研磨速度が速すぎる
- 対策
適切な回転数と送り速度の設定
研磨中の冷却(水研磨・オイル研磨の採用)
研磨圧力を下げる
③ オレンジピール(肌荒れ)
表面がオレンジの皮のようにざらついた状態になる現象です。
- 原因:不適切な研磨材、研磨条件のミスマッチ
- 対策
材質に適した研磨材の選定
前処理の見直し
適切な研磨速度の設定
④ 寸法精度不良
研磨により設計寸法から外れてしまう問題です。
- 原因:過度な研磨、部分的な研磨集中
- 対策
精密測定による確認
工程間での寸法チェック
研磨代の適正化
研磨品質を安定させるポイント
高品質な研磨結果を安定して得るためのポイントを紹介します。
- 前処理の徹底:研磨前の洗浄・脱脂を確実に行う
- 適切な工具・材料選定:対象物に合った研磨材と工具を使用する
- 作業環境の整備:温度・湿度・照明などの環境条件を整える
- 定期的な点検:研磨工具の摩耗・劣化をチェックする
- 標準作業の確立:熟練作業者のノウハウを文書化する
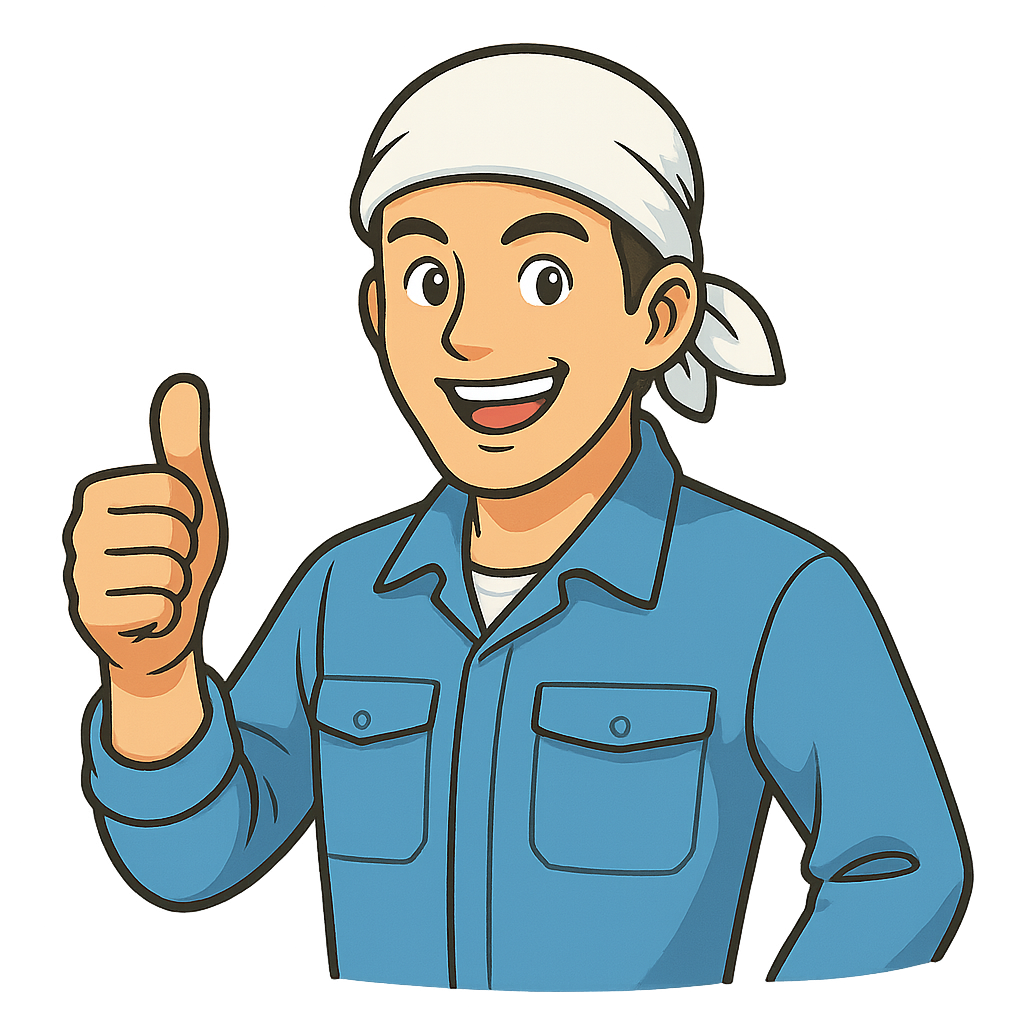
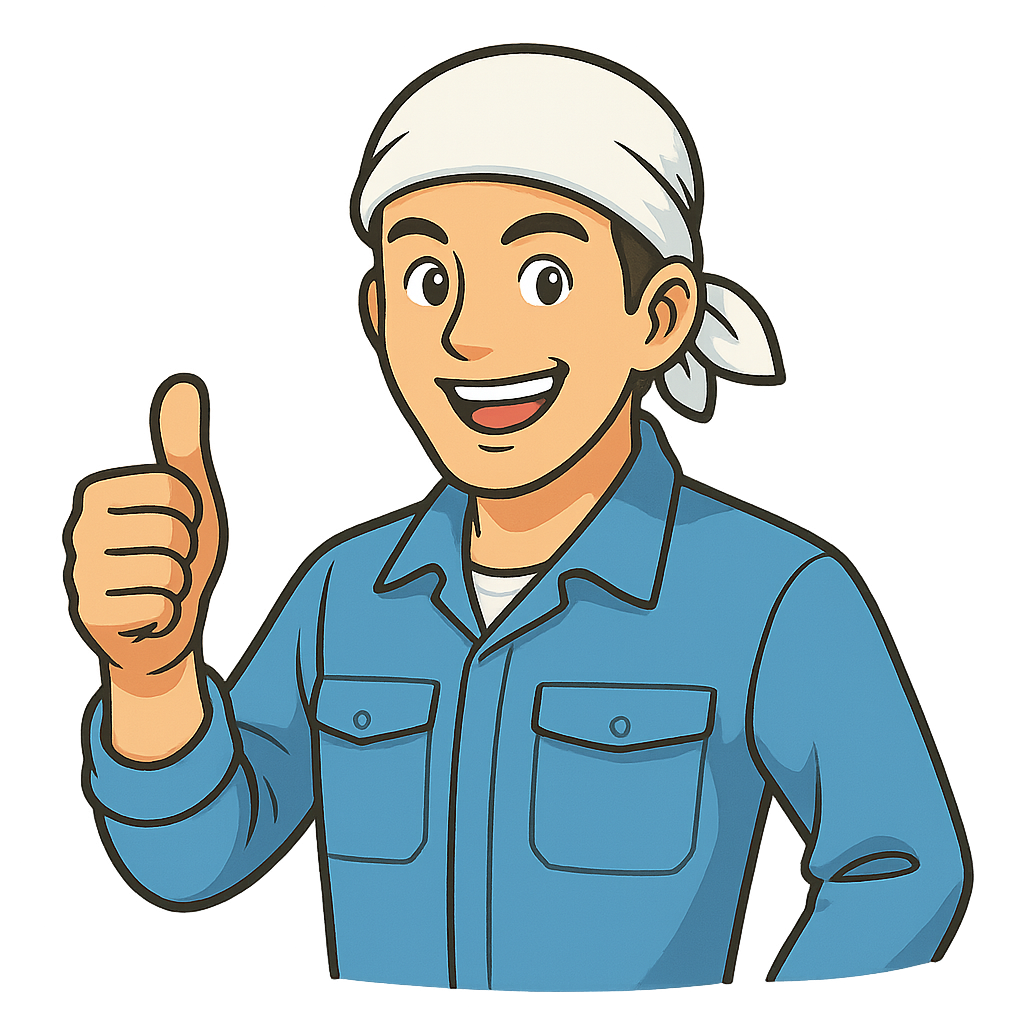
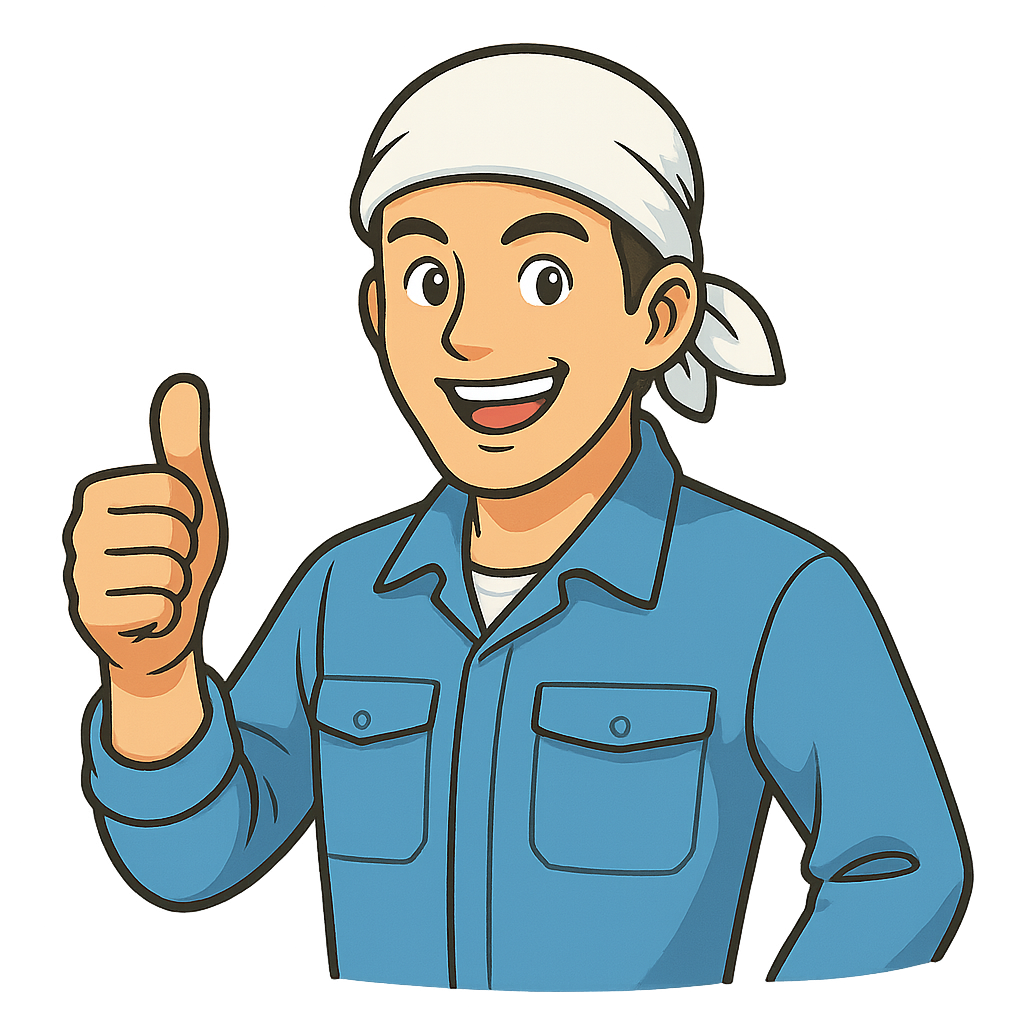
最終仕上げではコンパウンド量を ごく少量 にするとムラが減りますよ!特にバフ研磨では、「少ない量でじっくり」が美しい仕上がりのコツです。
5. 研磨外注先を選ぶ際のチェックリスト
自社で研磨を行わず外注を検討する場合、適切な外注先選定が重要です。以下のポイントをチェックすることで、信頼できる研磨外注先を見つけることができます。
技術力の評価ポイント
対応可能な材質と形状
- 取扱い材質の範囲(鉄系、非鉄金属、特殊材料など)
- 複雑形状への対応力(内面、曲面、細部など)
設備・技術の保有状況
- 研磨機械のラインナップ(バフ研磨機、研削盤など)
- 測定機器の有無(表面粗さ計、顕微鏡など)
- 熟練技術者の在籍状況
品質管理体制
- 検査方法と基準の明確さ
- 不良発生時の対応力
- 品質記録の管理状況
コスト・納期の評価ポイント
価格設定の透明性
- 見積もり内容の明確さ
- 追加費用発生条件の明示
納期の信頼性
- 過去の納期遵守率
- 急ぎ対応の可否
- 生産能力と安定性
ロット対応力
- 小ロット対応の可否
- 大量生産時の安定性
- 納品形態の柔軟性
コミュニケーション力の評価
技術的な相談対応
- 技術提案の積極性
- 問題発生時の報告速度
- 改善提案の有無
サンプル対応
- サンプル研磨の対応力
- 条件出しの丁寧さ
- フィードバックの取り込み姿勢
外注先選定においては、価格だけでなく総合的な視点で評価することが重要です。特に継続的な取引を前提とする場合は、コミュニケーション力や技術提案力も重視すべきポイントとなります。
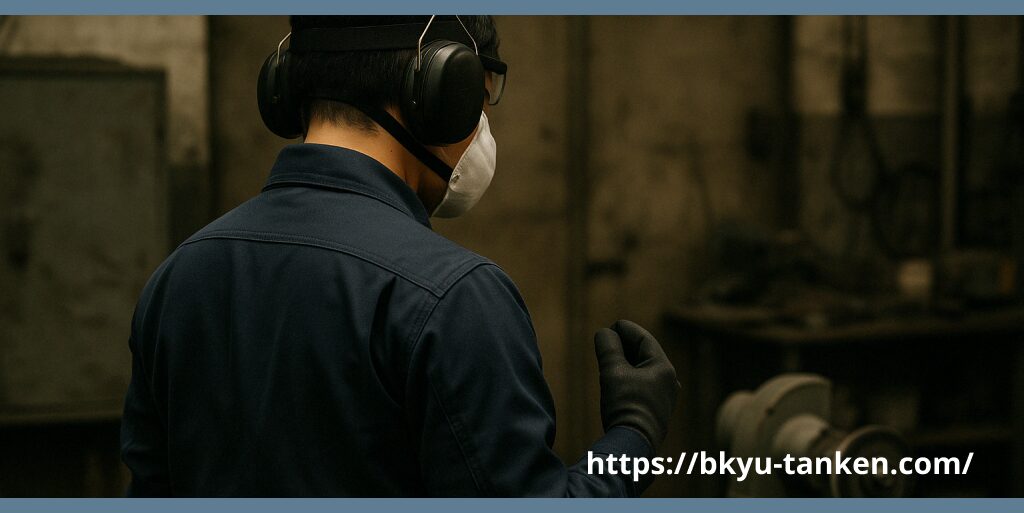
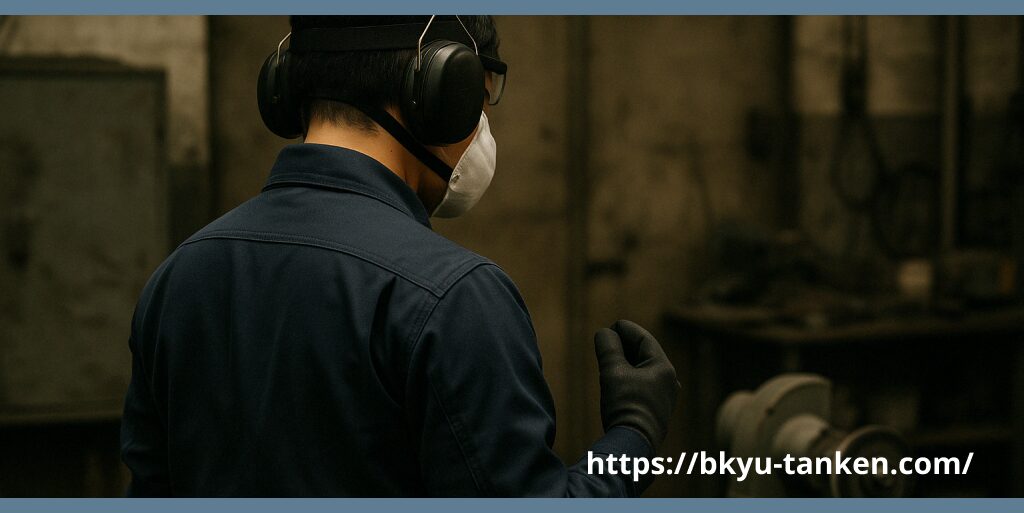
6. 製造現場で今日から使える改善Tips
研磨作業の品質向上とコスト削減を実現するための実践的なTipsを紹介します。すぐに現場で活用できる内容ですので、ぜひ試してみてください。
作業環境の改善ポイント
照明の工夫
- 斜光照明の活用:光を斜めから当てることで表面の凹凸が見やすくなる
- 照度の確保:研磨面の状態を正確に判断するために十分な明るさを確保
作業姿勢の改善
- 作業台の高さ調整:作業者の身長に合わせた適切な高さに設定
- 疲労軽減のための足置きマットの設置
粉塵対策
- 局所排気装置の適切な配置
- エアカーテンの設置による粉塵拡散防止
- 定期的な清掃による粉塵蓄積防止
工具・消耗品の管理改善
研磨材の適切な保管
- 湿気を避けた保管場所の確保
- 使用期限の管理と定期的なチェック
工具の定期メンテナンス
- バフモーターの振動チェック
- ベルト類の張り具合確認
- 消耗部品の定期交換
消耗品の在庫管理
- 使用頻度に基づく適切な在庫レベルの設定
- QRコードなどを活用した簡易在庫管理システムの導入
作業効率化のためのアイデア
作業の標準化
- 研磨手順の可視化(作業手順書の作成)
- チェックリストの活用による品質安定化
治具の工夫
- 形状に合わせた保持治具の自作
- 複数個同時研磨のための治具開発
工程間の連携強化
- 前工程との情報共有(素材状態、要求精度など)
- 後工程からのフィードバック収集と反映
これらの改善策は、大規模な設備投資をせずに実施できるものが多いため、中小製造業でも取り組みやすい内容となっています。小さな改善の積み重ねが、研磨品質の向上とコスト競争力の強化につながります。
まとめ:金属研磨の基本を踏まえた品質向上へのステップ
本記事では、金属研磨の基本概念から実践的なノウハウまでを解説しました。金属研磨は「なんとなく」ではなく、科学的な理解と経験に基づいた技術であることがお分かりいただけたでしょうか。
重要なポイントを改めてまとめると、
- 研磨の目的を明確にし、求められる表面性状に応じた適切な研磨方法を選択する
- 番手と表面粗さの関係を理解し、段階的な研磨プロセスを確立する
- 品質トラブルの原因を理解し、予防対策を講じることで安定した品質を確保する
研磨技術は一朝一夕で身につくものではありませんが、基本原理を理解することで効率的な技術習得が可能になります。現場での実践と改善を繰り返しながら、研磨技術の向上を目指しましょう。
コメント