研磨コンパウンド跡が残る原因と洗浄手順
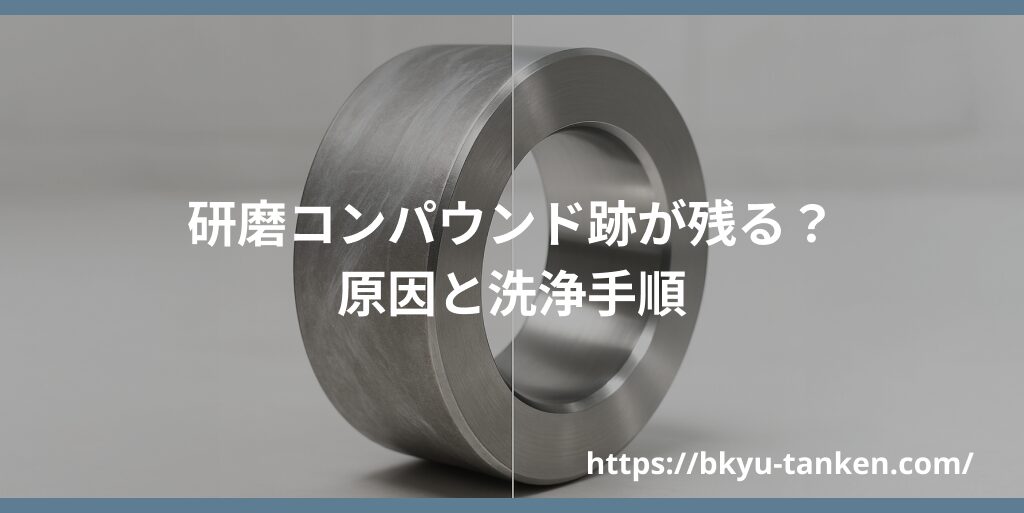
「しっかり磨いたはずなのに、なんだか白っぽく曇ってる…」
「洗浄しても、コンパウンドの油分がなかなか落ちない!」
「コンパウンド残りが原因で、塗装やメッキがのらない…歩留まりが悪くて困る…」
中小企業の金属加工現場で、こんな「研磨コンパウンド跡」の悩みを抱えていませんか? こんにちは!金属研磨ドットコムの研磨職人タカです。業界歴 20 年以上の経験で、このしつこいコンパウンド汚れには何度も泣かされてきました(笑)。
しかし、ご安心ください!コンパウンド跡が残るのには必ず原因があり、正しい手順で洗浄すれば、驚くほど綺麗に落とすことができます。これは、製品の最終的な表面品質を保証し、後工程の不良を防ぎ、結果的に歩留まりを改善するために、絶対に欠かせない工程です。
この記事では、研磨職人タカが、なぜコンパウンド跡が残るのか、その原因を解明し、効果的な洗浄手順と洗浄剤の選び方、さらには残留を防ぐための予防策まで、実践的に徹底解説します。
もうコンパウンドの残留汚れで悩むのは終わりにしましょう!正しい知識と手順で、ピカピカの製品を安定して作り出せるようになりますよ。
なぜ研磨コンパウンド跡は頑固に残るのか?主な原因
あの白っぽい油膜のような汚れ、なぜあんなに落ちにくいのでしょうか? まずは、コンパウンド跡が頑固に残ってしまう主な原因を理解しましょう。
コンパウンドの成分(油脂分・ワックス)の性質
研磨コンパウンドには、砥粒(研磨材の粒子)のほかに、それらを保持し、潤滑性や冷却性を与えるためのバインダー(結合剤)として、油脂(グリスや脂肪酸など)やワックス(ロウ)が多く含まれています。
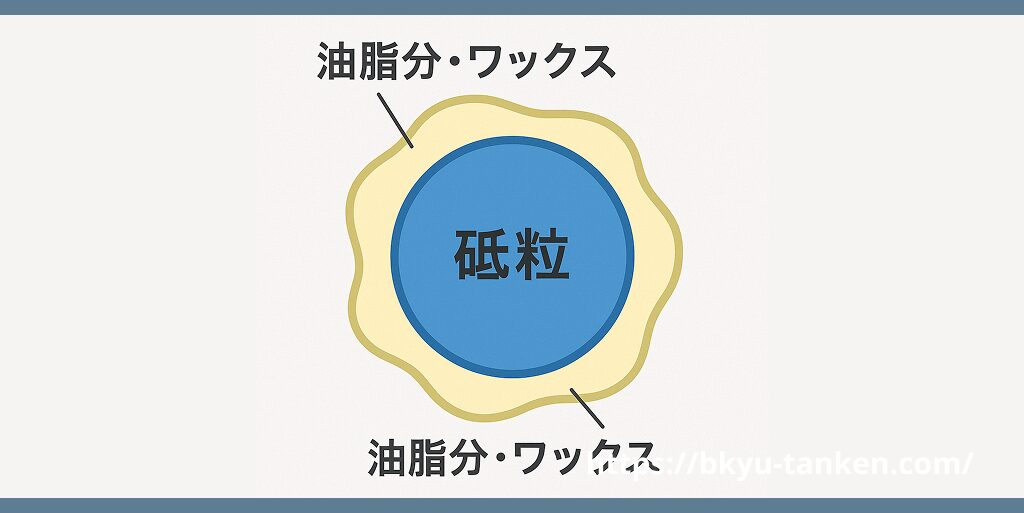
これらの油脂分やワックスは、基本的に水とは混ざりにくい(疎水性)性質を持っています。そのため、水洗いだけでは簡単に流れ落ちず、ワーク表面に油膜のように残ってしまうのです。これが、コンパウンド跡の正体の一つです。
研磨熱による焼き付き・固着
研磨作業中は、バフとワークの摩擦によって、局所的にかなりの高温が発生します。この熱によって、コンパウンド中の油脂分やワックスが変質したり、ワーク表面に焼き付いたり、固着したりしてしまうことがあります。
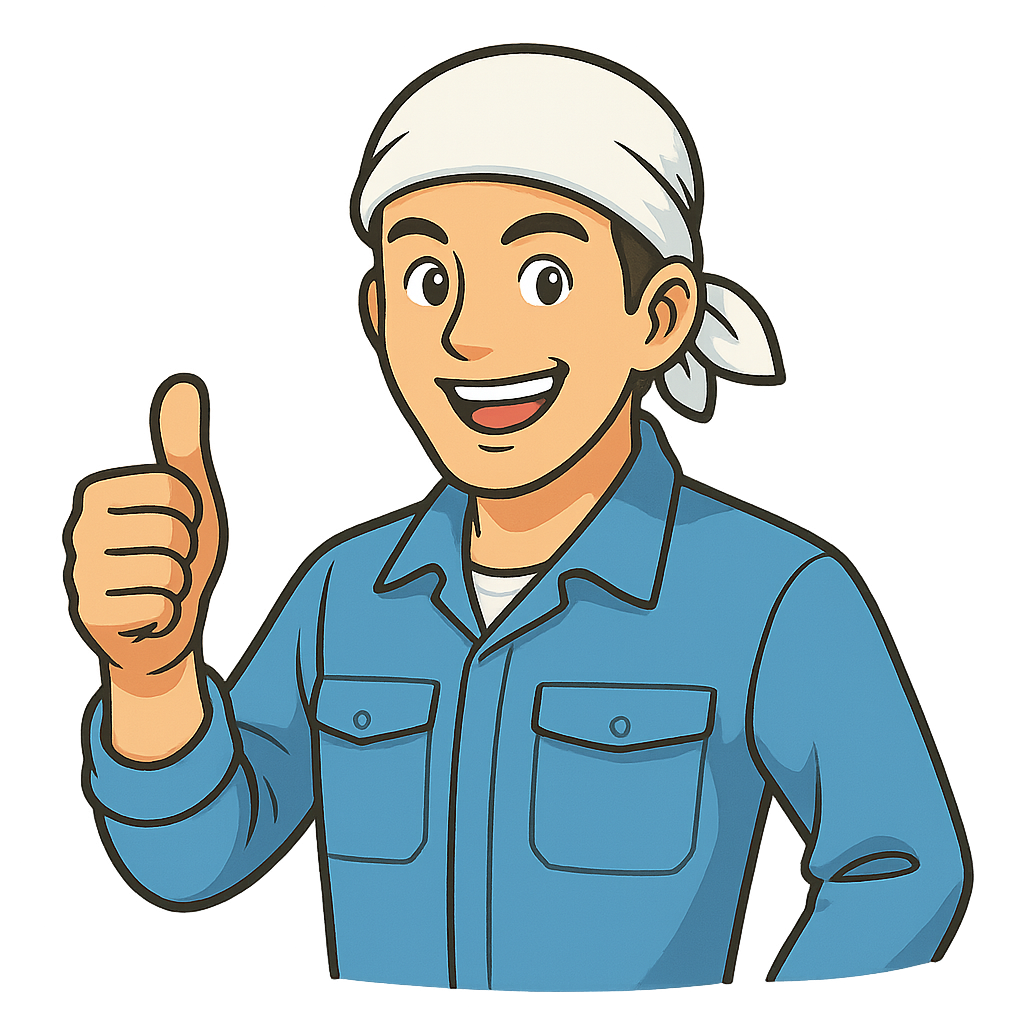
特に、押し付け圧力が強すぎたり、回転数が高すぎたりすると、研磨熱は想像以上に上昇します。焼き付いてしまうと、単なる油汚れよりもさらに落としにくくなるので注意が必要です。
焼き付いたコンパウンドは、化学的に変化している場合もあり、通常の洗浄剤では分解・除去が困難になるケースもあります。
ワーク表面の微細な凹凸への入り込み
どれだけ綺麗に磨き上げたように見える金属表面でも、ミクロのレベルで見ると、微細な凹凸や研磨痕(スクラッチ)が存在します。
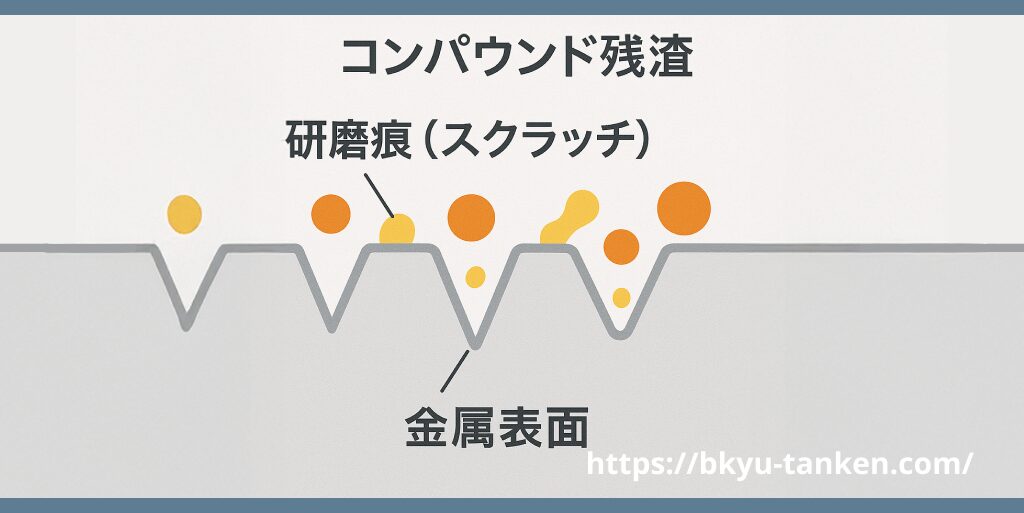
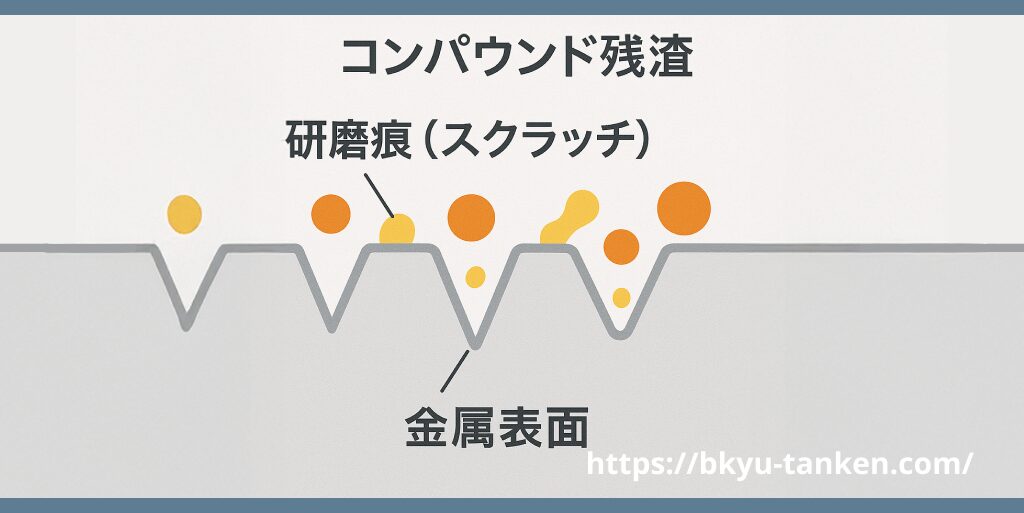
コンパウンドの砥粒や油脂分が、これらの微細な隙間に入り込んでしまうと、表面を拭いただけでは除去しきれず、洗浄後も残渣として残ってしまうことがあります。特に、柔らかい金属(アルミなど)や、複雑な形状の部品では、この傾向が強くなります。
不適切な洗浄方法・洗浄剤の使用
「とりあえず水で洗っている」「どんな汚れにも効きそうな強い洗剤を使っている」…もし、このような洗浄を行っている場合、それが原因でコンパウンド跡が落ちていない可能性があります。
- 水洗いだけ:前述の通り、油性の汚れは水だけでは落ちにくい。
- 洗浄剤のミスマッチ:コンパウンドの種類(油性/水性)や汚れの性質に合わない洗浄剤では、効果が薄い。
- 洗浄条件の不備:洗浄液の濃度が低い、温度が低い、洗浄時間が短いなどの理由で、十分に汚れを落としきれていない。
- すすぎ不足:汚れが分解されても、すすぎが不十分だと、洗浄剤成分とともに再付着してしまう。
正しい洗浄プロセスと、汚れの種類・材質に合った洗浄剤を選ぶことが、コンパウンド跡除去の基本となります。
【基本編】コンパウンド跡を落とす洗浄手順の全体像
では、具体的にどのように洗浄を進めればよいのでしょうか? ここでは、コンパウンド跡を効果的に除去するための基本的な洗浄手順(4 ステップ)の全体像を解説します。
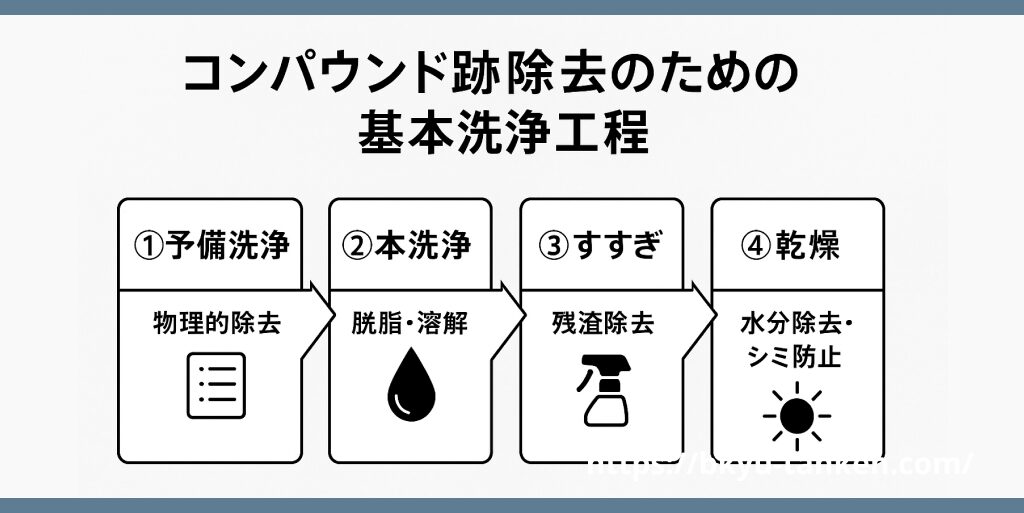
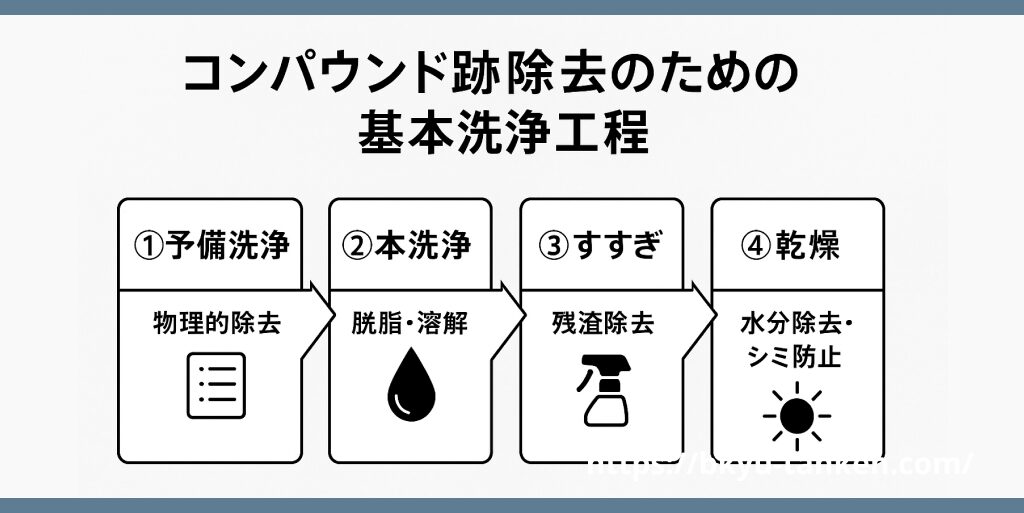
① 予備洗浄(物理的な除去)
本洗浄の効果を高めるために、まずはワーク表面に付着している、比較的大きなコンパウンドの塊や、ゆるく付着した汚れを物理的に除去します。
- 方法例:エアーブロー、ブラシでの払い落とし、柔らかい布での拭き取り、水による簡単な洗い流しなど。
- 目的:本洗浄で使用する洗浄液の汚れ負荷を軽減し、洗浄効果を高め、洗浄液の寿命を延ばす。
いきなり洗浄液にドボンと漬けるのではなく、この一手間を加えることが、意外と重要です。
② 本洗浄(脱脂・溶解)
ここが洗浄工程のメインです。ワークの材質やコンパウンドの種類に合わせて選定した洗浄剤を使用し、油脂分やワックスを溶解・乳化(水に混ざる状態にすること)・分解させ、ワーク表面から剥離させます。
- 方法例:洗浄液への浸漬、スプレー洗浄、超音波洗浄、手作業でのブラッシング洗浄など。
- ポイント:洗浄剤の種類、濃度、温度、洗浄時間などの条件を適切に管理することが重要。
この後のセクションで、具体的な洗浄方法や洗浄剤の選び方を詳しく解説します。
③ すすぎ(リンス)
本洗浄でワーク表面から剥がれた汚れや、残存している洗浄剤成分を、きれいな水(または適切なリンス液)で完全に洗い流します。
- 重要性:すすぎが不十分だと、洗浄剤成分や一度剥がれた汚れが乾燥後に再付着し、シミやムラの原因となります。
- 方法例:流水洗浄、シャワー洗浄、浸漬槽での多段すすぎなど。
- ポイント:できるだけ清浄な水(純水など)を使用し、十分な水量と時間をかける。最終すすぎ水の清浄度管理も重要。
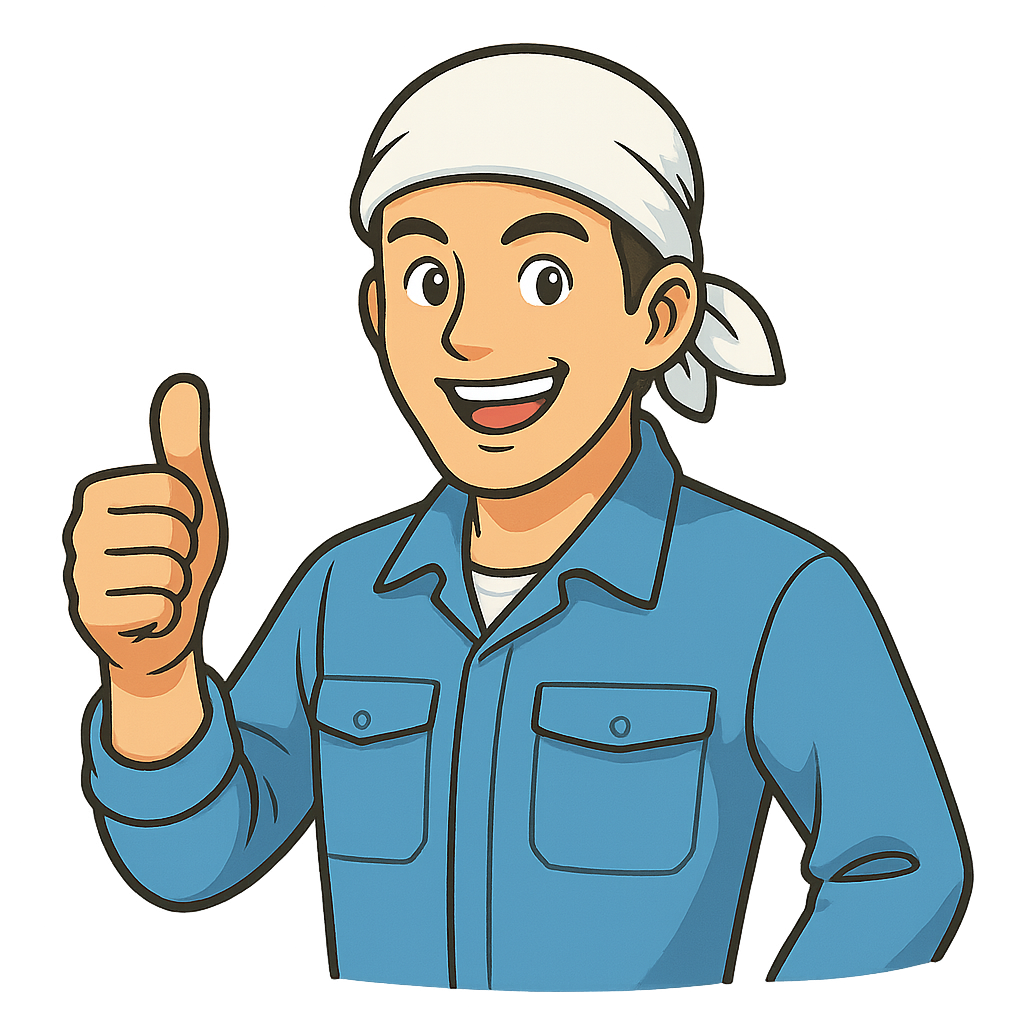
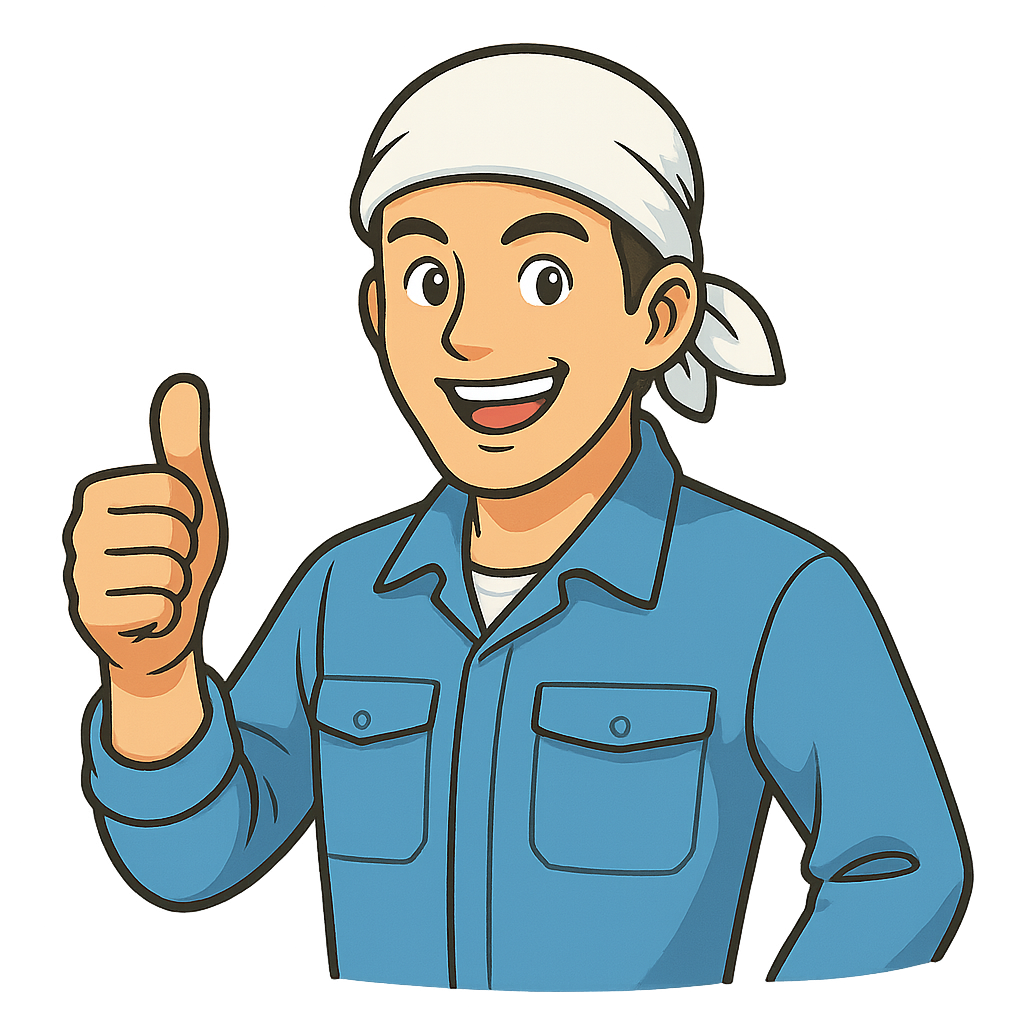
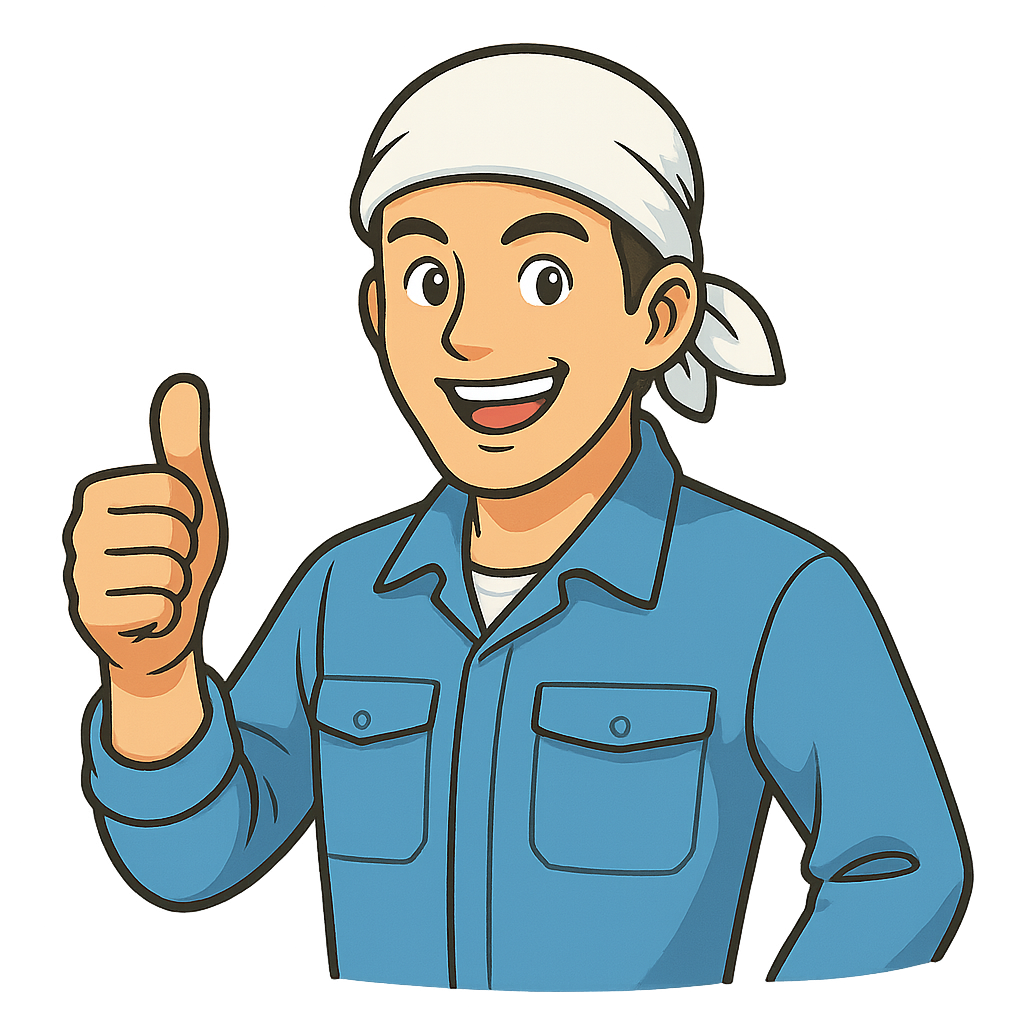
意外と軽視されがちなのが、この「すすぎ」工程です。「しっかり洗ったのにシミが残る…」という場合、すすぎ不足が原因であることも多いんですよ。洗浄剤メーカーが推奨するすすぎ方法を確認しましょう。
④ 乾燥
すすぎが終わったら、速やかにワーク表面の水分を除去します。水分が残っていると、水滴の跡(ウォータースポット)がシミになったり、サビの原因になったりします。
- 方法例:エアーブロー(清浄な圧縮空気を使用)、温風乾燥、オーブン乾燥、減圧乾燥、水切り剤(速乾性の溶剤)の使用など。
- 注意点:乾燥温度が高すぎると、材質によっては変質や変色を起こす場合がある。エアーブローのエアが汚れていると、油分などが再付着してしまう。
清浄な状態を保ったまま、完全に乾燥させることが最終目標です。
【実践編】効果的な洗浄方法と洗浄剤の選び方
基本の 4 ステップを踏まえ、ここではより具体的な洗浄方法と、その際に重要となる洗浄剤の選び方について解説します。
① 手拭き洗浄:手軽だが限界も
ウエス(布)などに洗浄剤を含ませて、手作業で拭き取る方法です。
- メリット:設備が不要で手軽に始められる。少量多品種の生産に向いている。
- デメリット:労力がかかる。微細な凹凸に入り込んだ汚れは除去しにくい。拭きムラが出やすい。大量生産には不向き。使用するウエスが汚れると、汚れを広げてしまう可能性も。
- 適した洗浄剤:溶剤系クリーナー、脱脂スプレーなど。
比較的軽度な油汚れや、最終仕上げの際の指紋除去などには有効ですが、頑固なコンパウンド跡の完全除去には限界があることが多いです。
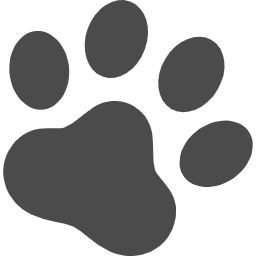
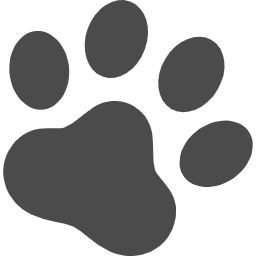
② 溶剤洗浄:油分に強いが注意点も
有機溶剤(炭化水素系、アルコール系、塩素系など)を使って油脂分を溶解させる方法です。浸漬、蒸気洗浄、拭き取りなどの方法があります。
- メリット:油脂分の溶解力が高く、油性コンパウンドに対して高い洗浄効果を発揮する。乾燥性が良いものが多い。
- デメリット:引火性、毒性、環境への影響(VOC規制など)に注意が必要な溶剤が多い。材質(特に樹脂)によっては侵してしまう可能性がある。適切な排気設備や保護具が必要。
- 適した洗浄剤:各種有機溶剤(用途、法規制、安全性に応じて選定)。
安全性や環境規制に配慮した、代替フロンや臭素系、非塩素系の溶剤なども開発されていますが、使用する際は SDS(安全データシート)をよく確認し、リスクを理解した上で適切に管理する必要があります。
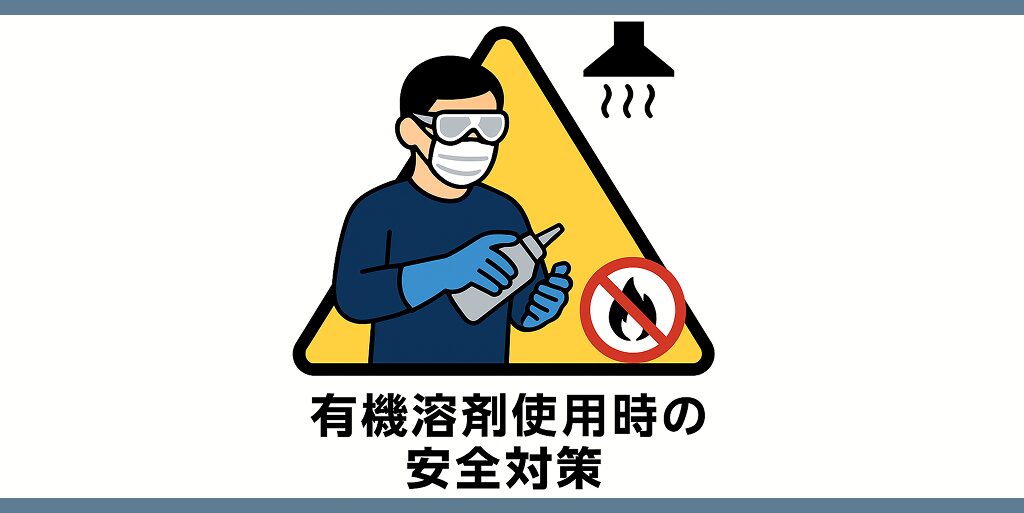
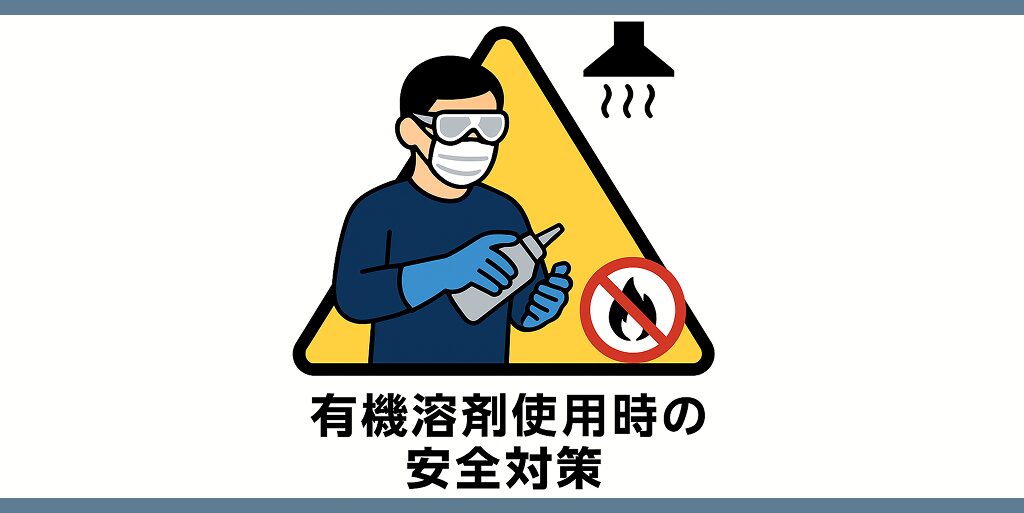
③ アルカリ洗浄:万能性が高いが材質を選ぶ
アルカリ性の水溶液(水酸化ナトリウム、ケイ酸ナトリウム、界面活性剤などを含む)を使って、油脂を鹸化(石鹸のような状態に変える)したり、乳化・分散させたりして除去する方法です。
- メリット:油脂だけでなく、固形の汚れや研磨粉に対しても効果がある場合が多い。不燃性で、比較的安全性が高い。洗浄剤の種類が豊富。
- デメリット:アルミニウム、亜鉛、真鍮などの非鉄金属は、アルカリ性が強すぎると腐食させてしまう。洗浄後のすすぎが重要。加温が必要な場合が多い。
- 適した洗浄剤:アルカリ性洗浄剤(pH、主成分、界面活性剤の種類、添加剤などを考慮して選定)。
pH 値(アルカリ性の強さ)や、界面活性剤の種類、腐食防止剤(インヒビター)の有無などを確認し、ワークの材質に合ったものを選ぶことが非常に重要です。
④ 超音波洗浄:細部まで強力洗浄
洗浄液中で超音波を発生させ、その衝撃波(キャビテーション効果)によって、微細な隙間に入り込んだ汚れまで物理的に剥離・除去する方法です。
- メリット:複雑な形状や、微細な穴、ネジ部などの洗浄が困難な箇所の汚れも効果的に除去できる。洗浄時間を短縮できる場合がある。
- デメリット:専用の超音波洗浄装置が必要。ワークの材質や形状によっては、超音波によるダメージ(エロージョン)が発生する可能性がある。洗浄液の選定が重要。
- 適した洗浄剤:超音波洗浄用に設計された洗浄剤(アルカリ性、中性、溶剤系など様々)。
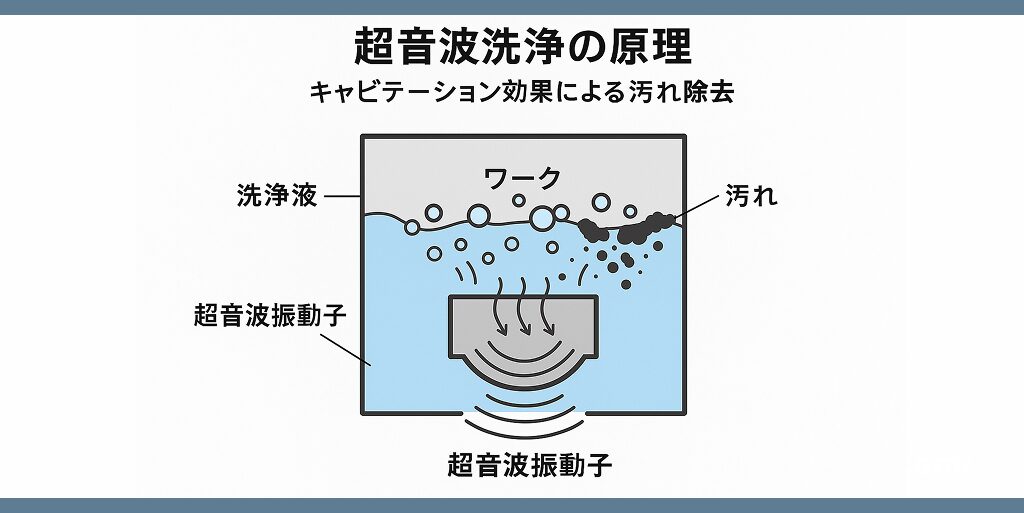
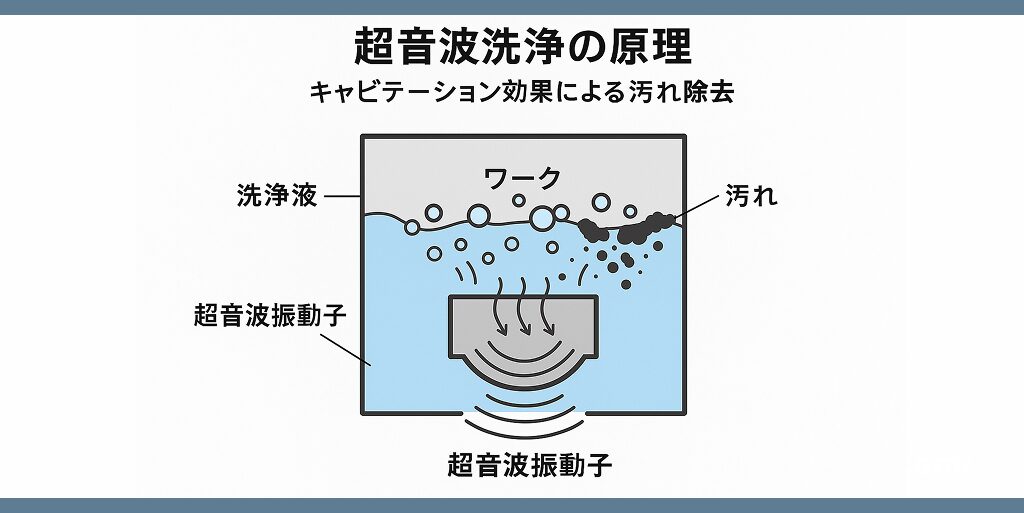
アルカリ洗浄や溶剤洗浄と組み合わせることで、より高い洗浄効果が期待できます。
洗浄剤選びのポイント(成分、pH、材質適合性)
どの洗浄方法を選ぶにしても、洗浄剤の選定が成功の鍵を握ります。
- 汚れの種類:コンパウンドが油性か水性か、主なバインダーは何か。
- ワークの材質:金属(鉄、ステンレス、アルミ、銅、真鍮など)、樹脂、ガラスなど。材質によっては使えない洗浄剤がある(特にアルカリ性、溶剤系)。
- 洗浄方法:浸漬、スプレー、超音波など、使用する装置や方法に適した洗浄剤か。
- pH:洗浄剤の酸性・中性・アルカリ性の度合い。アルカリ性が高いほど油汚れに強いが、材質への影響も大きくなる。
- 環境・安全規制:法規制(PRTR 法、有機則など)に該当しないか、作業環境や廃水処理に問題はないか。
- メーカー情報:洗浄剤メーカーのカタログや技術資料、SDS を確認し、推奨用途や使用条件、注意事項を守る。
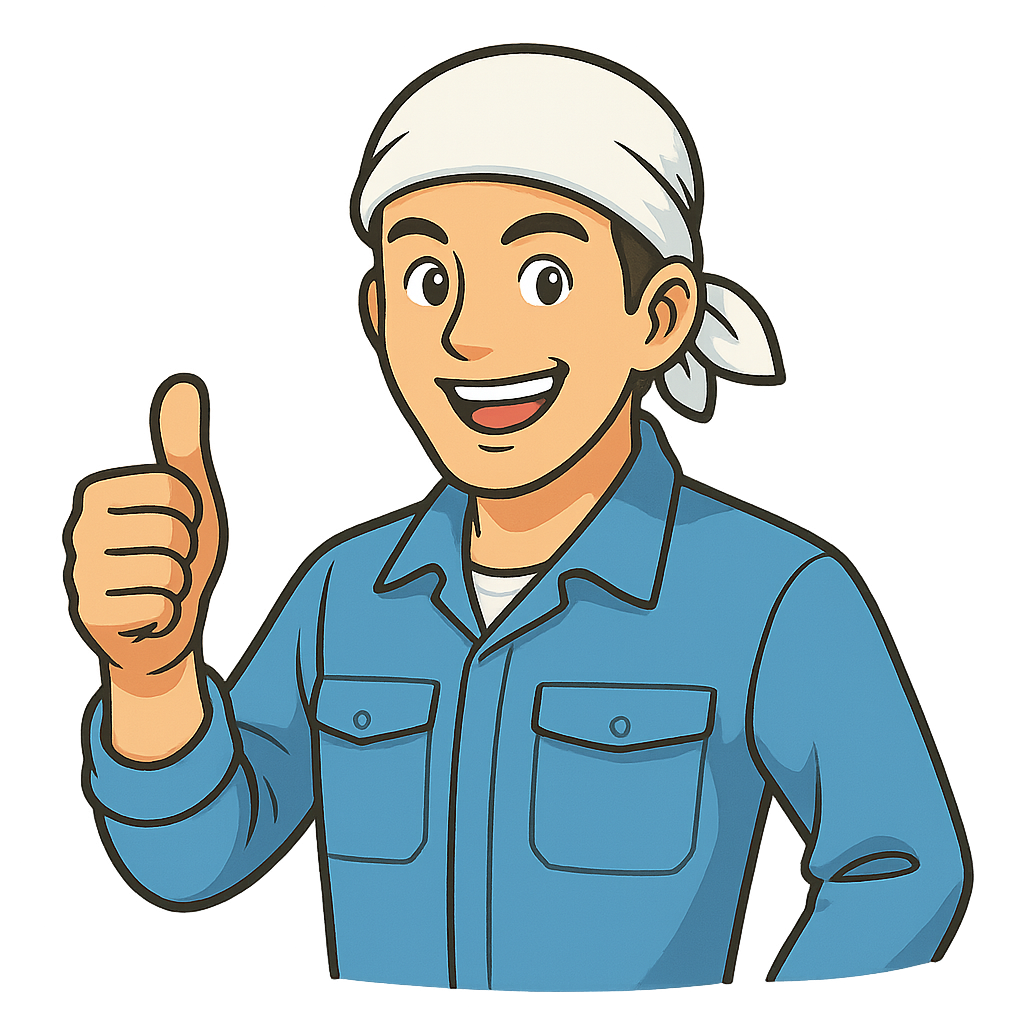
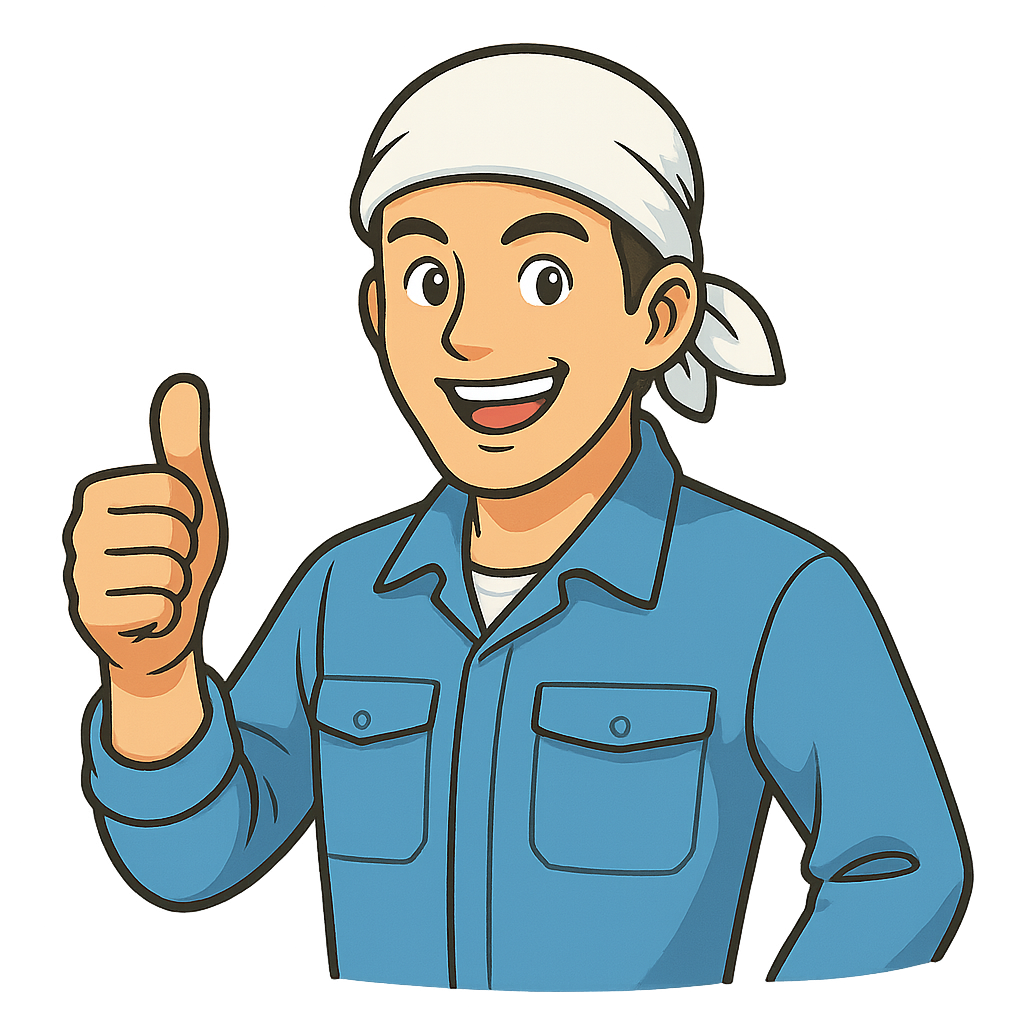
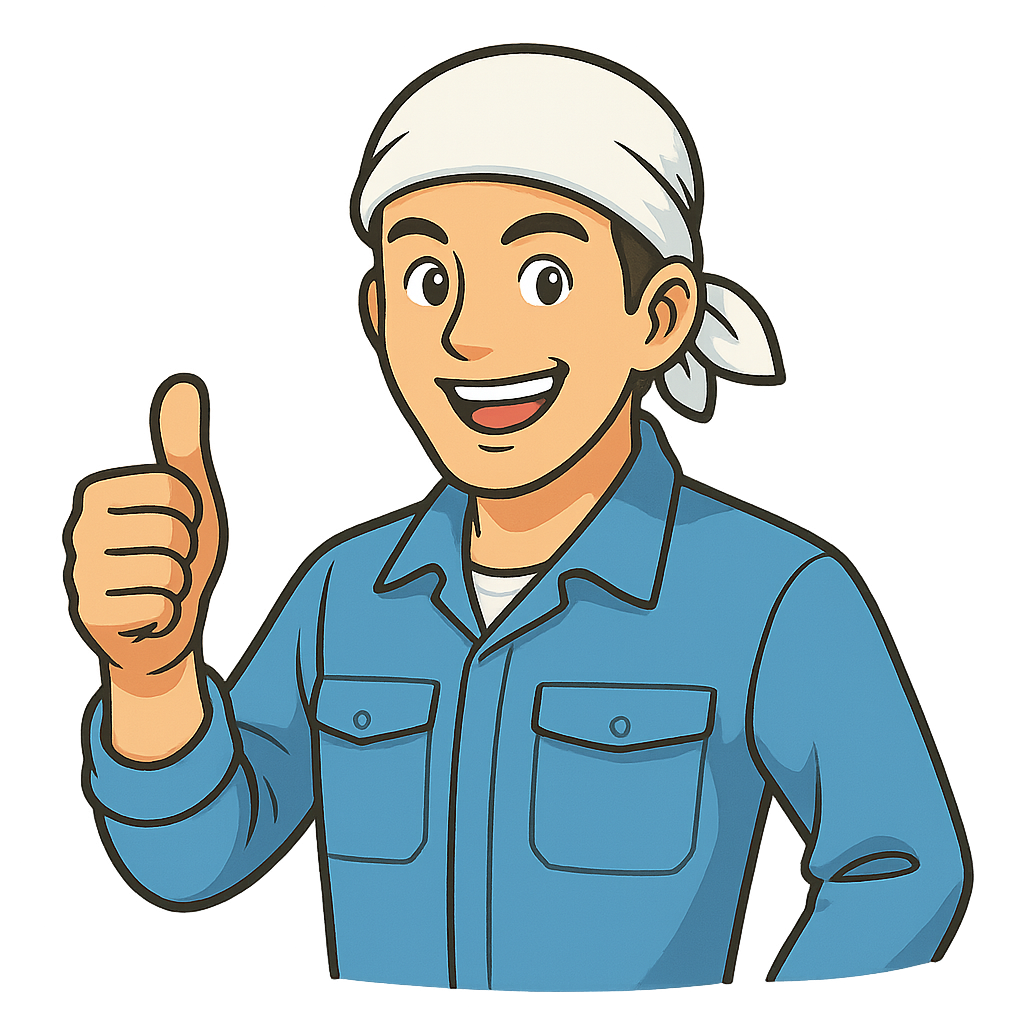
洗浄剤選びで迷ったら、まずはメーカーに相談してみるのが一番です。ワークの材質、コンパウンドの種類、現在の洗浄方法などを伝えれば、最適な洗浄剤や使用条件を提案してくれるはずですよ。サンプルでテストしてみるのも重要です。
コンパウンド跡の残留を防ぐための「予防策」
洗浄でしっかり落とすことも重要ですが、そもそもコンパウンド跡が残りにくいように、研磨工程自体を見直すことも有効な対策です。
研磨工程でのコンパウンド使用量の適正化
「たくさん付けた方がよく磨ける気がする」と、コンパウンドを過剰に使用していませんか?必要以上のコンパウンドは、研磨品質の向上に必ずしもつながらず、むしろ残留汚れの原因となり、洗浄の手間を増やすだけです。
- 適量塗布:最小限の量で最大の効果が得られるように、コンパウンドの塗布量を見直す。
- 塗布方法の改善:均一に、必要な箇所だけに塗布できるような方法(スプレー塗布など)を検討する。
バフの種類や回転数、研磨圧なども含めて、最適な研磨条件を見つけることが、結果的にコンパウンド使用量の削減につながります。
洗浄しやすいコンパウンドの選定
最近では、洗浄性を考慮して開発されたコンパウンドも増えています。
- 水溶性コンパウンド:水で容易に洗い流せるタイプ。ただし、研磨性能や防錆性などが油性と異なる場合がある。
- 易洗浄性コンパウンド:特殊な界面活性剤などが配合されており、アルカリ洗浄や水系洗浄剤で落としやすいように設計されたもの。
現在の研磨品質を維持できるか、コスト面なども考慮しつつ、より洗浄しやすいコンパウンドへの切り替えを検討する価値はあります。
研磨後、時間を置かずに洗浄する
研磨作業が終わったワークを、長時間放置していませんか?
時間が経つと、
- コンパウンドの油脂分が酸化したり、硬化したりする。
- 空気中のホコリやゴミが付着する。
- 研磨熱で表面に焼き付いた汚れが、冷えることでさらに固着する。
といった理由で、汚れが格段に落ちにくくなります。可能な限り、研磨工程の直後に洗浄工程を配置し、汚れが固着する前に洗い流すことが理想的です。
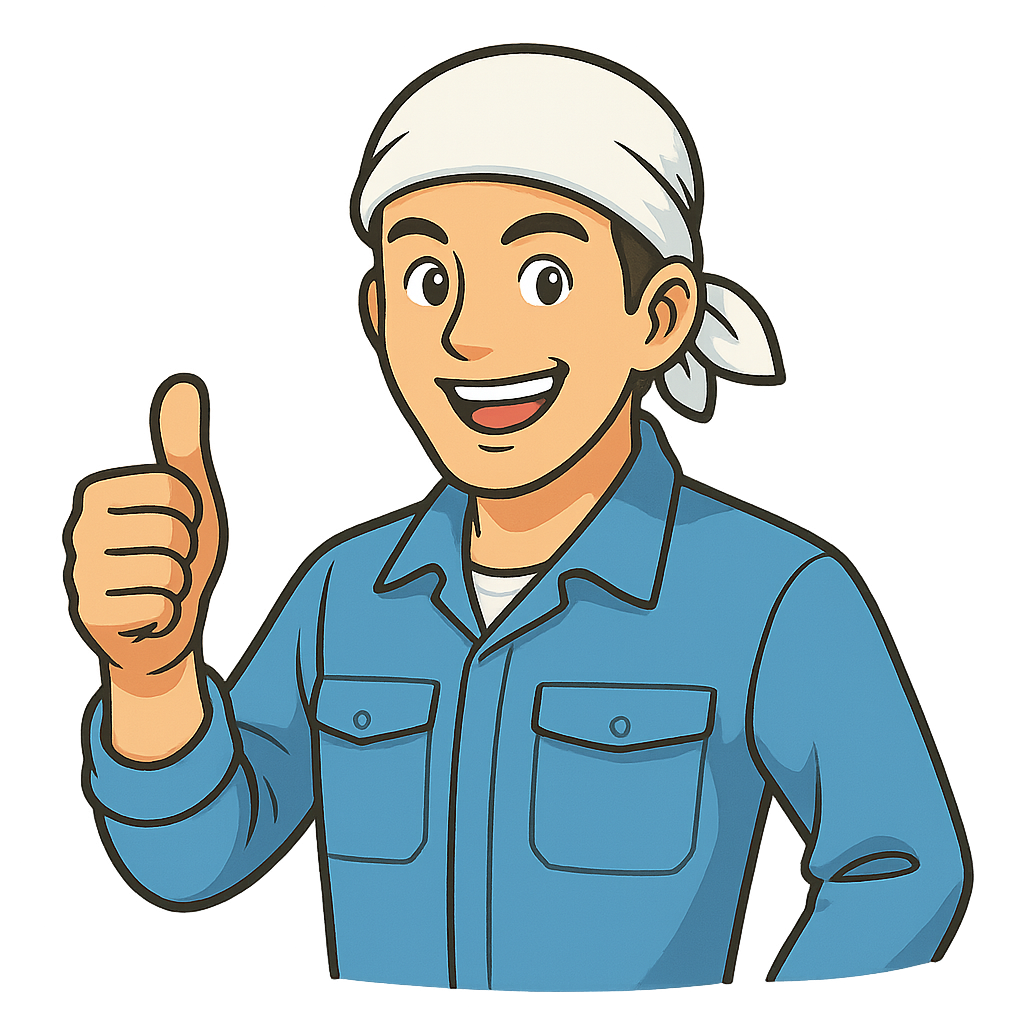
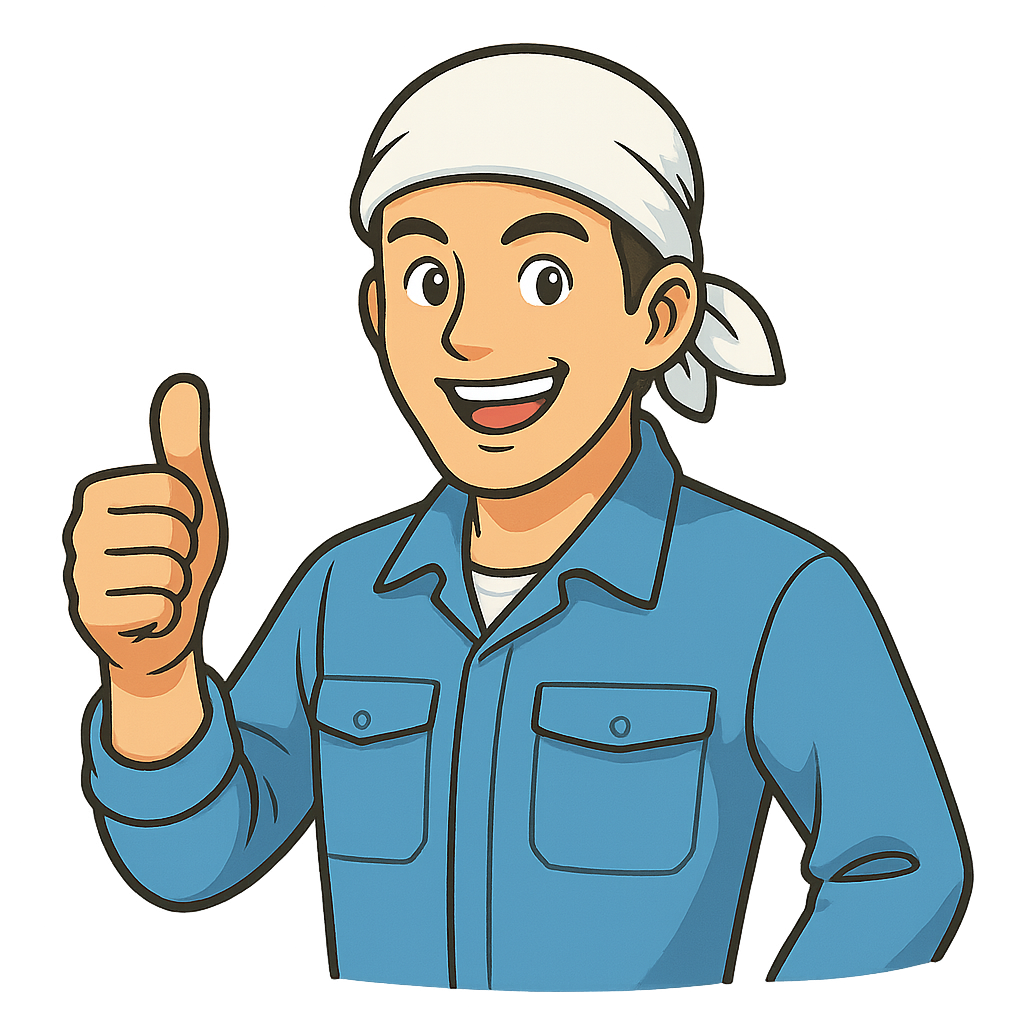
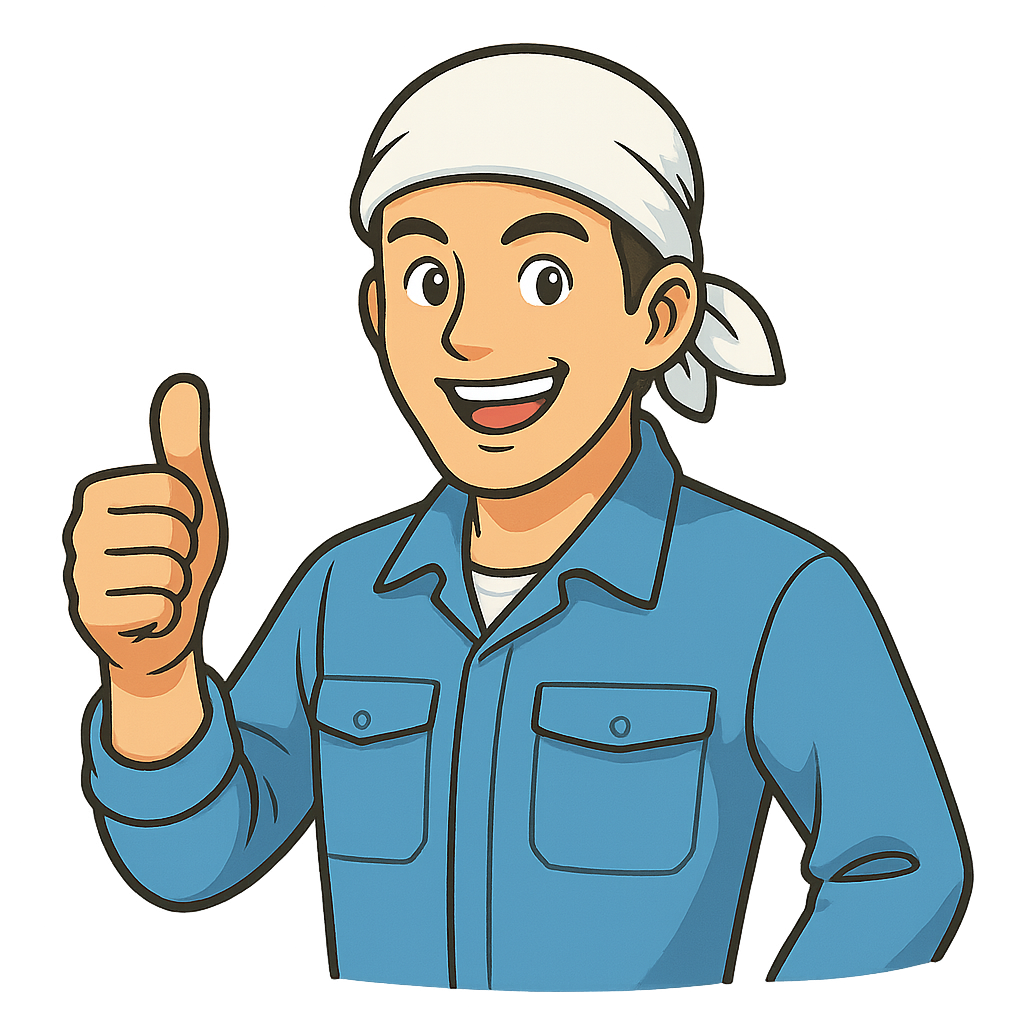
「予防は治療に勝る」と言いますが、コンパウンド汚れも同じですね。後工程の洗浄で苦労する前に、研磨工程で少し工夫するだけで、全体の効率が大きく改善されることもありますよ。
まとめ
今回は、多くの現場を悩ませる研磨コンパウンド跡について、その原因から、基本的な洗浄手順、具体的な洗浄方法と洗浄剤の選び方、そして予防策までを詳しく解説しました。
コンパウンド跡の主な原因
- 油脂・ワックスの性質
- 研磨熱による焼き付き・固着
- 表面の微細な凹凸への入り込み
- 不適切な洗浄方法・洗浄剤
基本洗浄 4 ステップ
- 予備洗浄(物理的除去)
- 本洗浄(脱脂・溶解)
- すすぎ(残渣除去)
- 乾燥(水分除去)
効果的な洗浄方法と選び方
- 手拭き、溶剤、アルカリ、超音波など、方法の特性を理解する。
- 汚れの種類、ワーク材質、安全性などを考慮し、最適な洗浄剤を選定する。
残留を防ぐ予防策
- コンパウンド使用量の適正化
- 洗浄しやすいコンパウンドの選定
- 研磨後、速やかに洗浄する
コンパウンド跡の除去は、単に見た目を良くするだけでなく、後工程の品質を保証し、製品全体の信頼性を高めるために不可欠な工程です。正しい知識に基づき、適切な洗浄プロセスを構築・維持することが、歩留まり改善、コスト削減につながります。
ぜひ、この記事を参考に、自社の洗浄方法を見直してみてください。「うちの汚れが落ちないんだけど…」「この材質に合う洗浄剤は?」など、具体的なお悩みがあれば、いつでも金属研磨ドットコムにご相談ください。一緒に解決策を見つけましょう!
コメント