【脱・属人化】研磨作業の標準化を進める手順とメリット
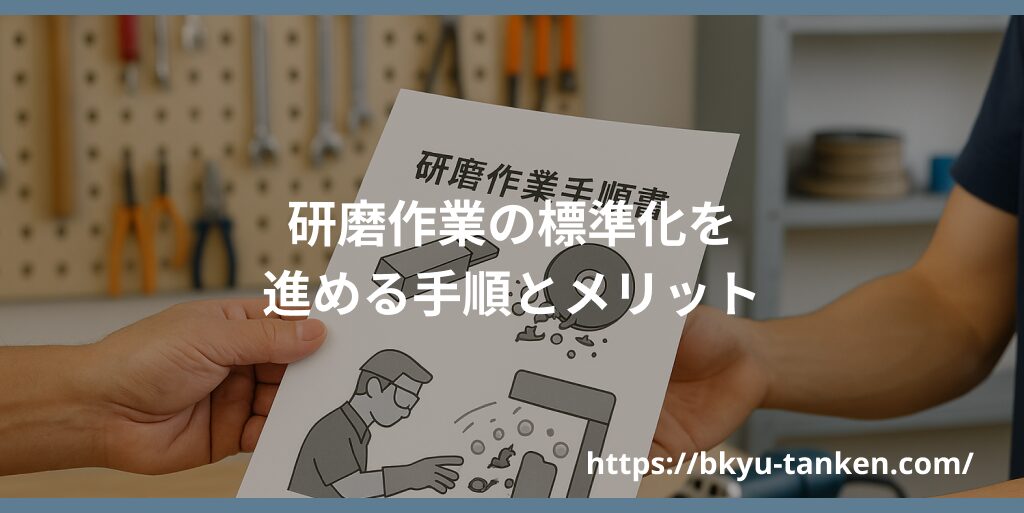
「この複雑な曲面の鏡面仕上げは、ベテランの〇〇さんしかできない…」
「作業者によって、仕上がりの光沢や寸法にバラつきが出てしまう…」
「新人に研磨を教えても、なかなか一人前にならない。教え方も人それぞれだし…」
中小企業の金属加工現場で、こんな悩みを抱えていませんか? こんにちは!金属研磨ドットコムの研磨職人タカです。業界歴 20 年、多くの現場を見てきましたが、「特定の人」にしかできない作業が多いというのは、中小企業共通の課題かもしれません。いわゆる「属人化」というやつですね。
しかし、この属人化を放置しておくと、品質の不安定さや、技術継承の難しさ、さらにはその人が辞めてしまった時のリスクなど、様々な問題を引き起こします。ではどうすれば良いのか? 答えは「研磨作業の標準化」にあります。
この記事では、研磨職人タカが、なぜ研磨作業の標準化が必要なのか、その具体的なメリット、そして中小企業でも実践できる標準化の進め方(5 つのステップ)について、分かりやすく解説します。
標準化は、決してベテランの技術を軽視するものではありません。むしろ、その貴重な技術やノウハウを会社の財産として共有し、誰もが高品質な研磨を安定して行えるようにするための重要な取り組みなのです。品質向上、効率アップ、そして未来への技術継承のために、一緒に「脱・属人化」への一歩を踏み出しましょう!
なぜ研磨作業の「属人化」が問題なのか?
「あの人がいれば大丈夫」というのは、一見頼もしく聞こえますが、長い目で見ると多くの問題をはらんでいます。具体的にどのような問題があるのか、見ていきましょう。
品質の不安定化と再現性の低さ
作業が特定の人に依存しているということは、その人の経験や勘、その日の体調によって仕上がりが左右される可能性があるということです。これでは、常に同じ品質の製品を安定して供給することが難しくなります。
顧客から「前回の納品物と仕上がりが違う」といったクレームにつながる可能性もありますし、再現性が低いということは、品質管理の観点からも大きな問題と言えます。
技術継承の困難と新人教育の非効率
ベテラン作業員の持つ高度な技術やノウハウは、「見て盗め」「やって覚えろ」といった昔ながらの方法だけでは、なかなか若手に伝わりません。教える側も、自分の感覚を言葉で説明するのが難しかったり、教え方にばらつきが出たりしがちです。
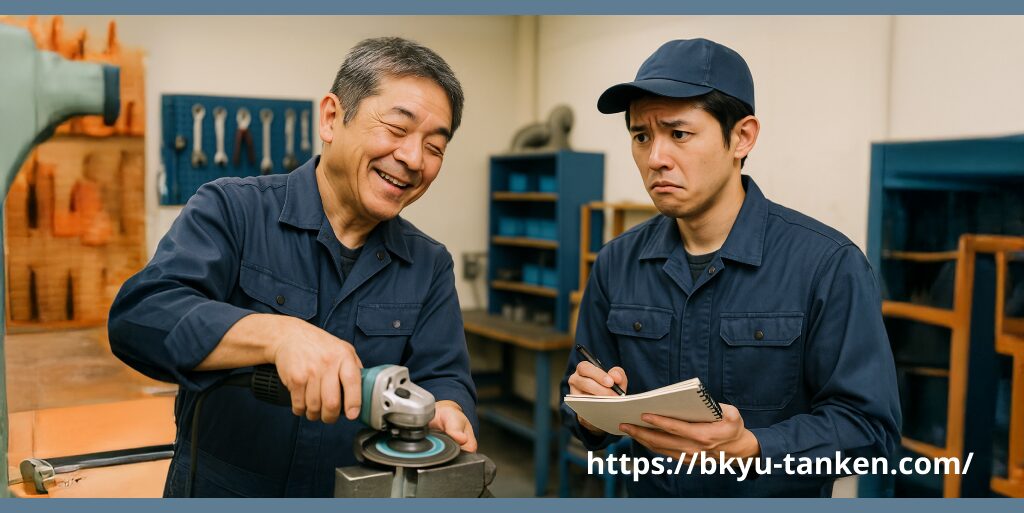
結果として、新人教育に非常に時間がかかり、いつまでたっても一人前になれない、あるいは途中で挫折してしまうといった非効率が生じます。
特定作業者への過負荷と退職リスク
「この仕事は〇〇さんしかできない」となると、その作業者に仕事が集中し、過度な負担がかかることになります。残業が増えたり、休みが取りにくくなったりすれば、モチベーションの低下や、最悪の場合、燃え尽きや退職につながるリスクも高まります。
また、そのキーパーソンが急に病気になったり、退職してしまったりした場合、その仕事が完全にストップしてしまうという経営上の大きなリスクも抱えることになります。
改善活動の妨げ
作業手順が個人の頭の中にしかない状態では、「どこに問題があるのか」「どうすればもっと効率が上がるのか」といった客観的な分析や改善が非常に困難です。
せっかく改善提案が出ても、「〇〇さんのやり方を変えるのは難しい」といった理由で進まなかったり、改善効果が測定しにくかったりします。「改善」を進めて生産性を向上させるためには、まず作業が「見える化」され、共有されていることが前提となるのです。
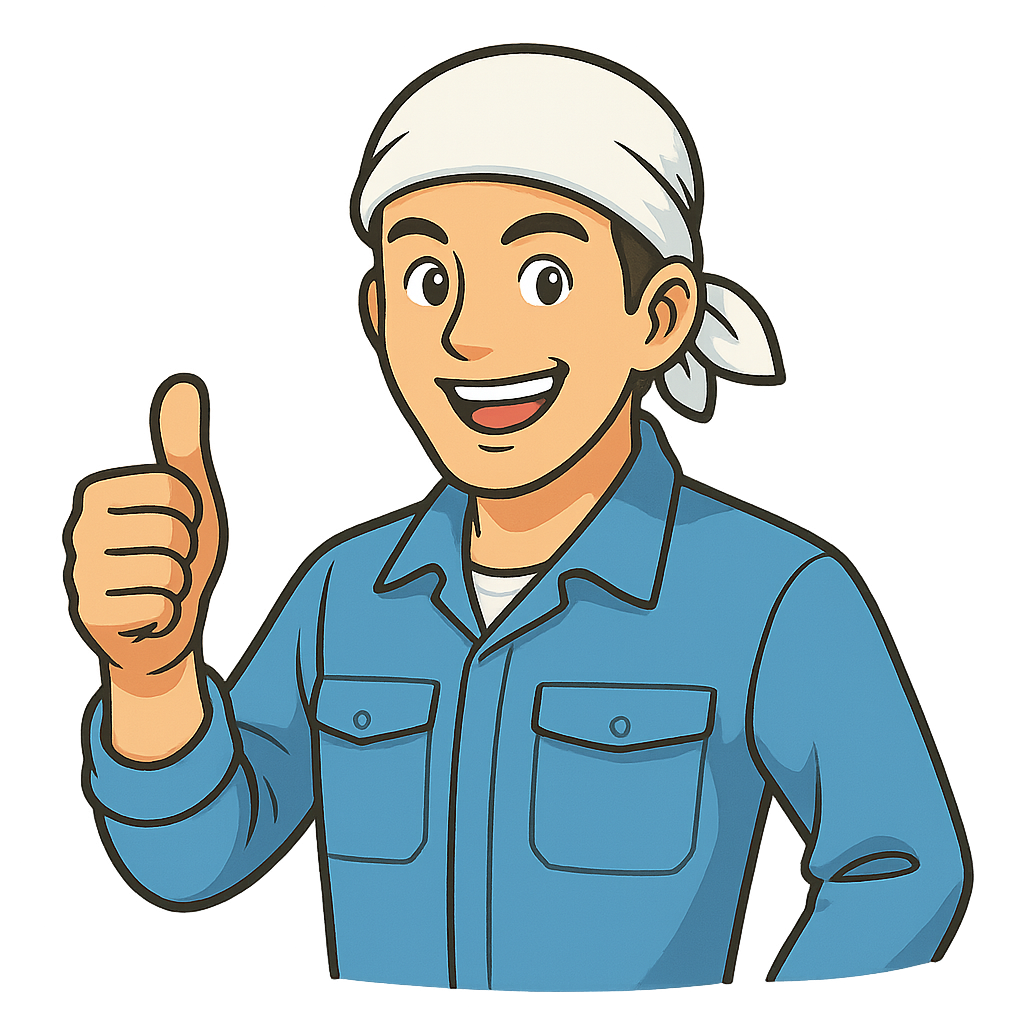
「ウチは少数精鋭だから大丈夫」と思っている社長さん、担当者さんもいるかもしれませんが、属人化のリスクは、会社の規模に関わらず存在します。むしろ、人が少ない中小企業だからこそ、一人に依存するリスクはより大きいと言えるかもしれませんよ。
研磨作業標準化のメリット:安定と成長の基盤
では、研磨作業を標準化することで、具体的にどのようなメリットが得られるのでしょうか? 安定した経営と、会社の成長につながる多くの利点があります。
① 常に安定した品質の実現
標準化された手順に従って作業を行えば、作業者が誰であっても、経験の浅い新人であっても、一定レベルの品質を安定して達成できるようになります。これは、顧客満足度の向上と、会社の信頼性向上に直結します。「いつでも同じ品質」は、ものづくり企業の基本であり、最大の強みです。
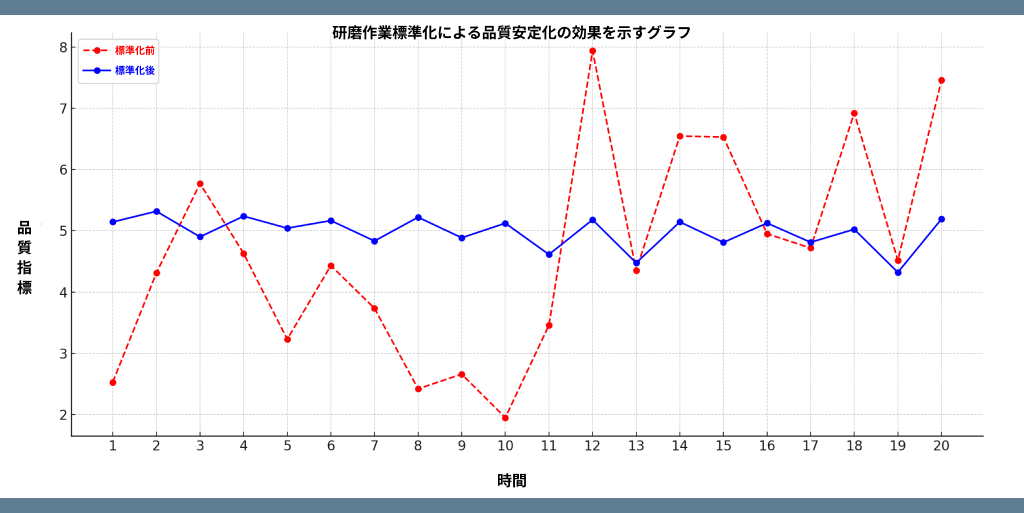
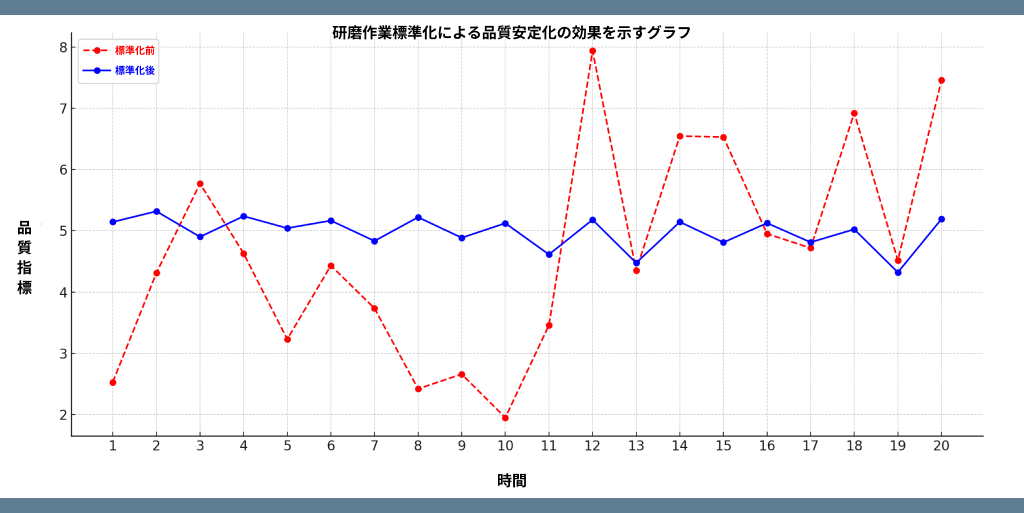
② 作業効率の向上とコスト削減
標準化された手順は、多くの場合、最も効率的で無駄のない方法として確立されます。これにより、作業時間の短縮や、手戻り・不良品の削減が期待でき、結果的に生産性の向上とコスト削減につながります。また、使用する工具や消耗品も標準化されるため、在庫管理なども効率化されます。
③ 新人教育の迅速化とレベルアップ
明確な作業手順書(SOP)があれば、新人教育の効率は劇的に向上します。教える側もポイントを絞って指導でき、教わる側も具体的な手順を理解しやすいため、短期間で基本的な作業を習得できます。
これにより、〔==教育担当者の負担が軽減されるだけでなく、新人自身も早く戦力として活躍できる==〕ようになり、組織全体のレベルアップにつながります。
>>> 作業手順書の作成方法
④ 技術・ノウハウの形式知化と共有
ベテラン作業員の頭の中にしかなかった「暗黙知」である技術やノウハウを、作業手順書という「形式知」に落とし込むことで、会社の貴重な財産として蓄積・共有できます。これにより、特定の人がいなくなっても技術が失われることがなくなり、継続的な技術力の維持・向上が可能になります。
⑤ 安全性の向上とミスの削減
作業手順を標準化する過程で、危険な作業や、間違いやすいポイントを洗い出し、安全な手順を確立することができます。明確な手順に従うことで、ヒューマンエラーによる事故やミスを減らす効果も期待できます。
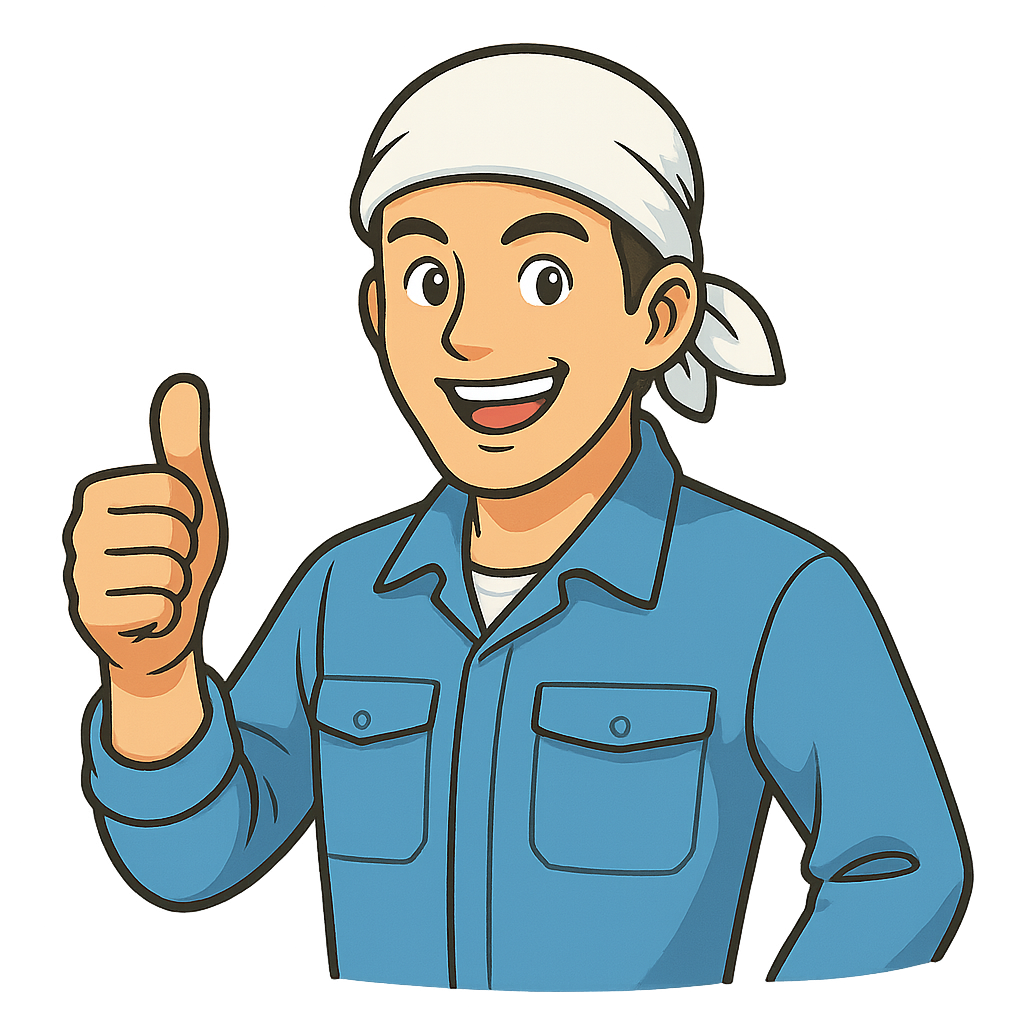
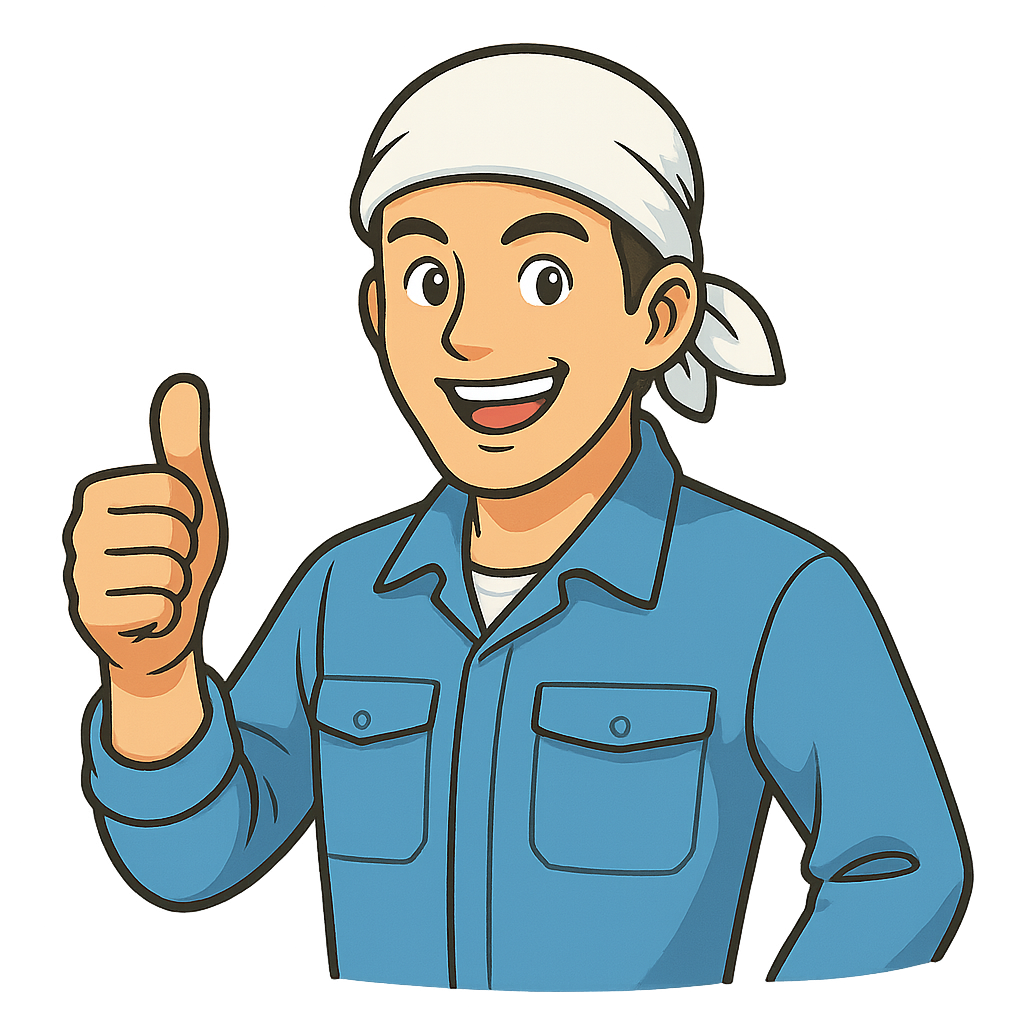
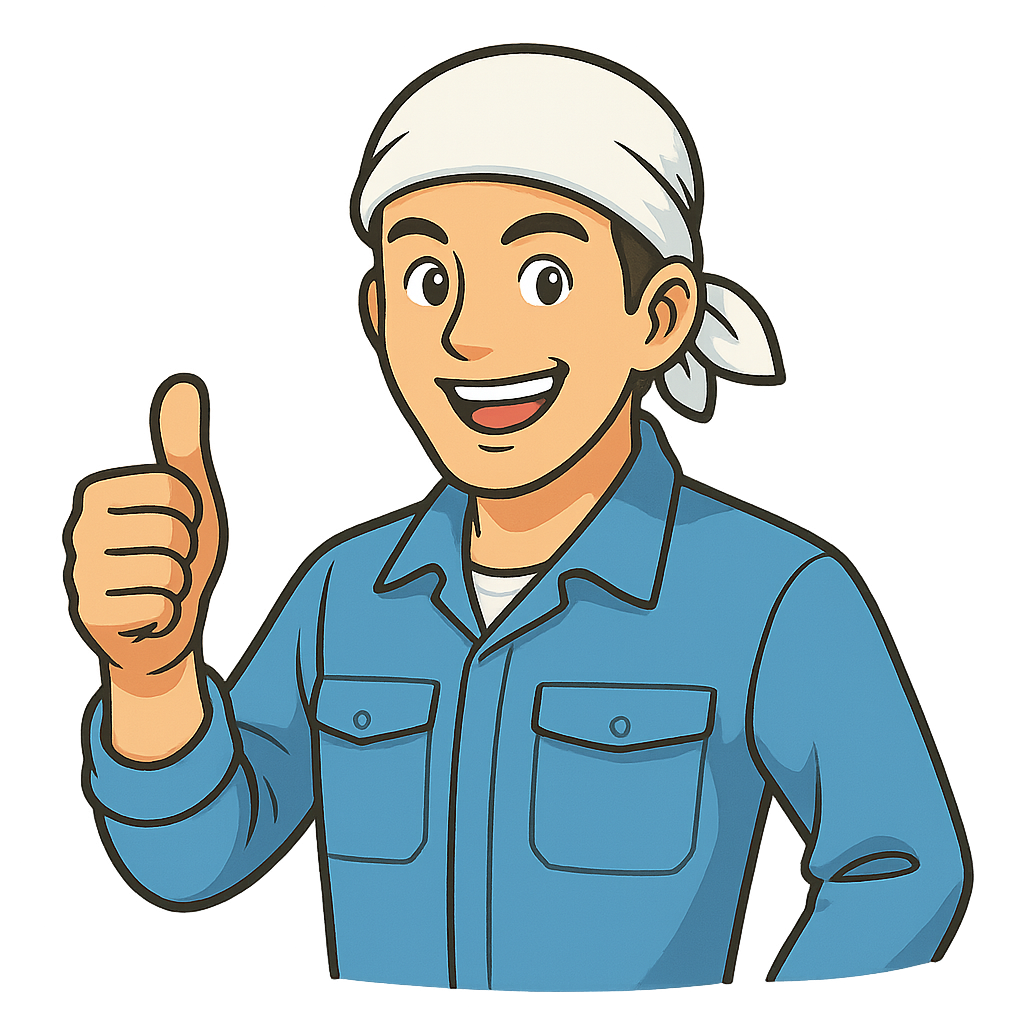
標準化は、単に「誰でもできるようにする」だけではありません。「より安全に、より効率的に、より高品質に」作業を行うための土台作りでもあるんです。会社全体のレベルを底上げする、非常に重要な取り組みだと考えてください。
【実践】研磨作業標準化を進める5つのステップ
「標準化が重要なのは分かったけど、具体的に何から始めればいいの?」という声が聞こえてきそうですね。ここでは、中小企業でも取り組みやすい、標準化を進めるための具体的な 5 つのステップをご紹介します。
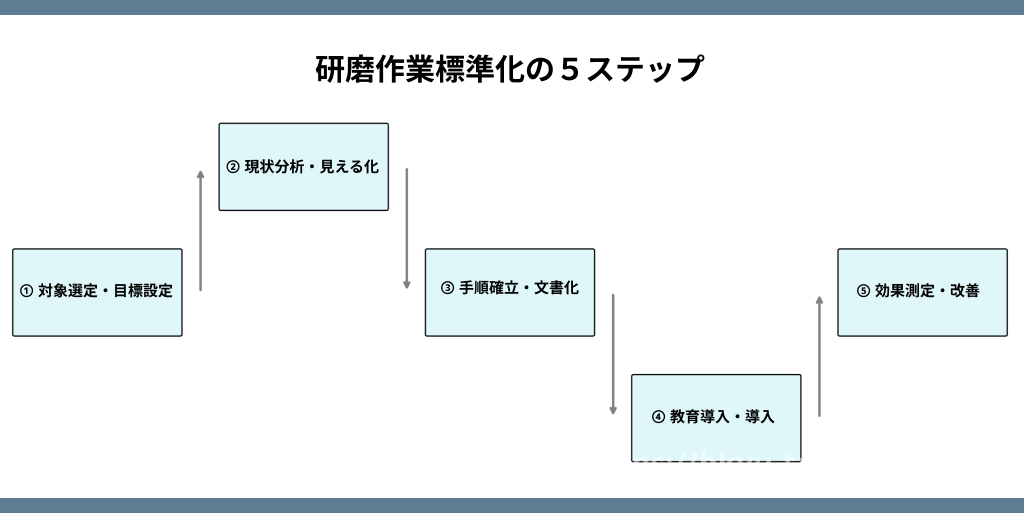
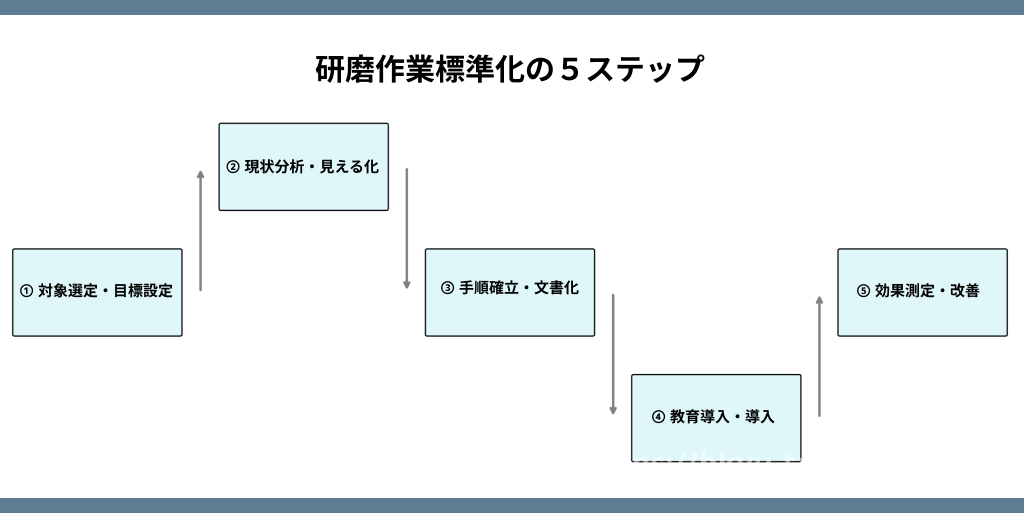
ステップ①:対象作業の選定と目標設定
いきなり全ての研磨作業を標準化しようとすると、負担が大きすぎて挫折してしまいます。まずは、標準化の効果が高いと思われる作業や、属人化の度合いが高い作業など、対象を絞り込みましょう。
そして、「品質のバラつきを〇%低減する」「新人教育期間を〇日短縮する」など、具体的で測定可能な目標を設定します。目標を明確にすることで、関係者の意識が統一され、取り組みやすくなります。
ステップ②:現状作業の分析と「見える化」
対象作業が決まったら、実際にその作業を行っている様子を観察し、ヒアリングを行いながら、現状の手順やノウハウを洗い出します。この時、必ずその作業に最も習熟しているベテラン作業員に協力してもらうことが重要です。
- どのような工具や消耗品を使っているか?
- どのような手順で進めているか?
- 各工程での判断基準は何か?(力加減、音、見た目など)
- 時間はどれくらいかかっているか?
- 注意している点や「コツ」は何か?
これらの情報を、メモや写真、動画などを活用して記録し、「見える化」していきます。
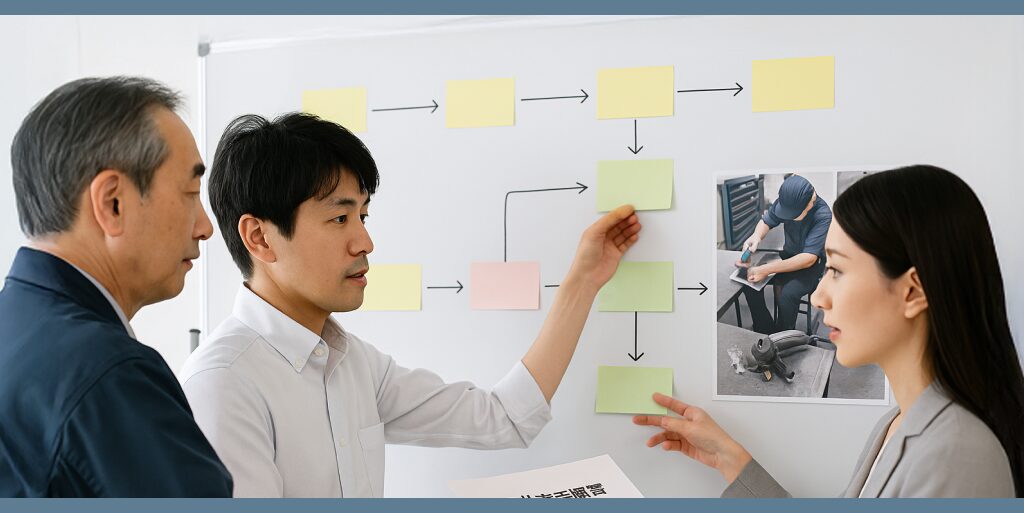
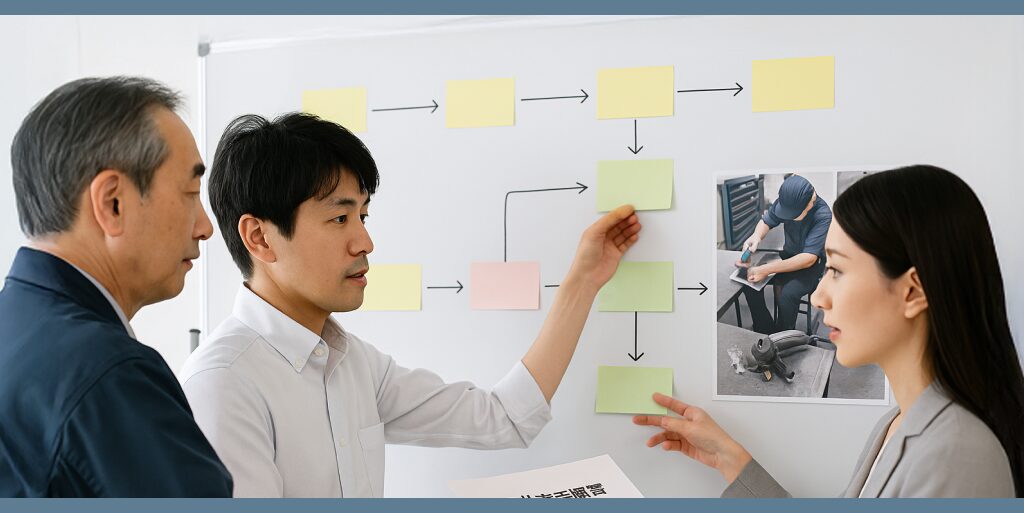
ステップ③:最適な手順の確立と文書化(SOP作成)
現状作業の分析結果をもとに、関係者で議論しながら、最も効率的で、安全かつ品質が安定する「ベストな手順」を確立します。ベテランのノウハウを尊重しつつも、なぜその手順なのかを掘り下げ、客観的な根拠に基づいた手順を目指します。
そして、確立した手順を「作業手順書(SOP: Standard Operating Procedure)」として文書化します。誰が見ても理解できるように、分かりやすい言葉遣いを心がけ、写真や図を多く取り入れるのがポイントです。(SOP作成の詳細は後述)
ステップ④:作業者への教育・訓練と導入
作成した作業手順書(SOP)を使って、対象となる作業者全員に教育・訓練を行います。単に手順書を配布するだけでなく、実際にやって見せたり(OJT)、練習する機会を設けたりしながら、確実に手順を習得してもらいます。
導入初期は、作業者が手順書通りに作業できているかを確認し、疑問点や不明点があれば丁寧にフォローすることが重要です。
ステップ⑤:効果測定と継続的な見直し・改善
標準化を導入したら、最初に設定した目標(品質、効率など)が達成されているかを定期的に測定・評価します。
- 品質データ(不良率、寸法精度など)の変化
- 作業時間の変化
- 新人の習熟度
測定結果をもとに、手順書の内容が分かりにくい、もっと良い方法が見つかったなど、改善点があれば、作業手順書を更新し、再度教育を行うというサイクル(PDCAサイクル)を回し続けます。標準化は一度作ったら終わりではなく、常に改善していくことが大切です。
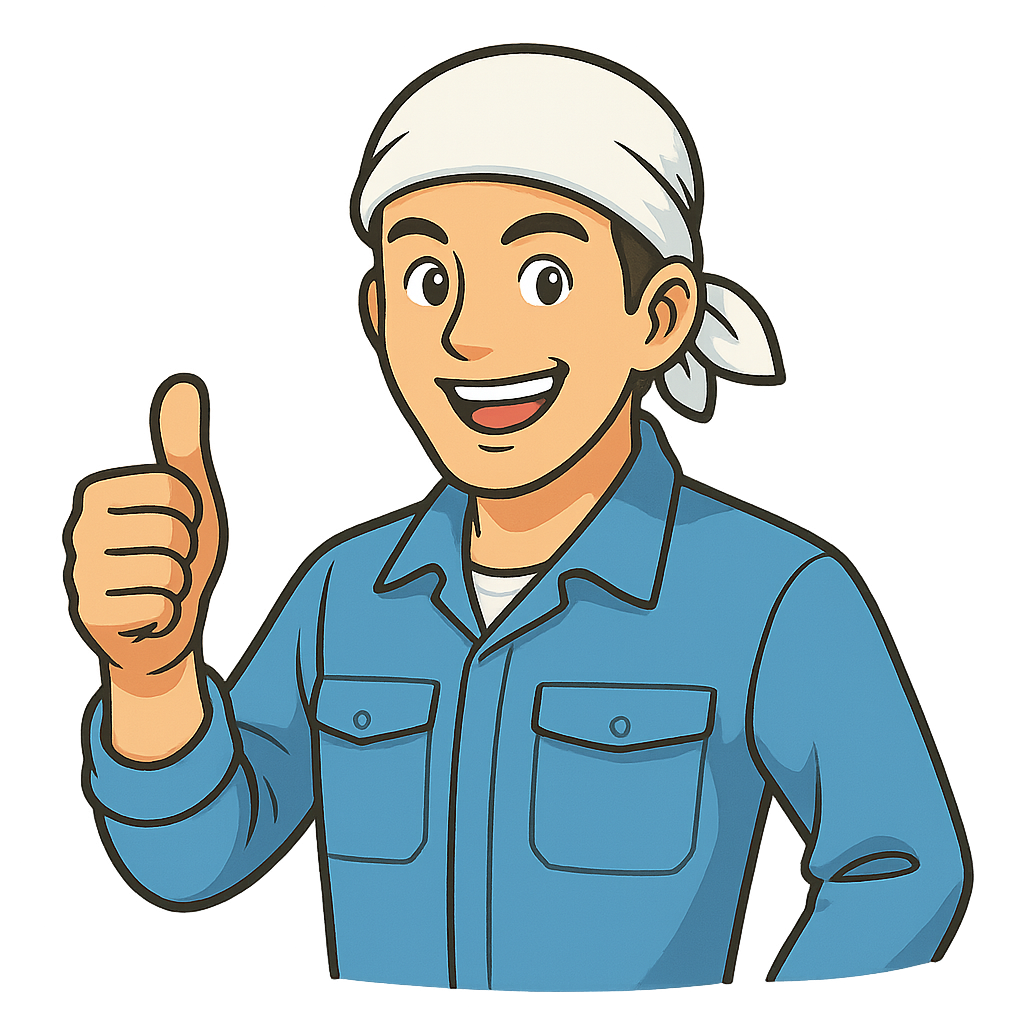
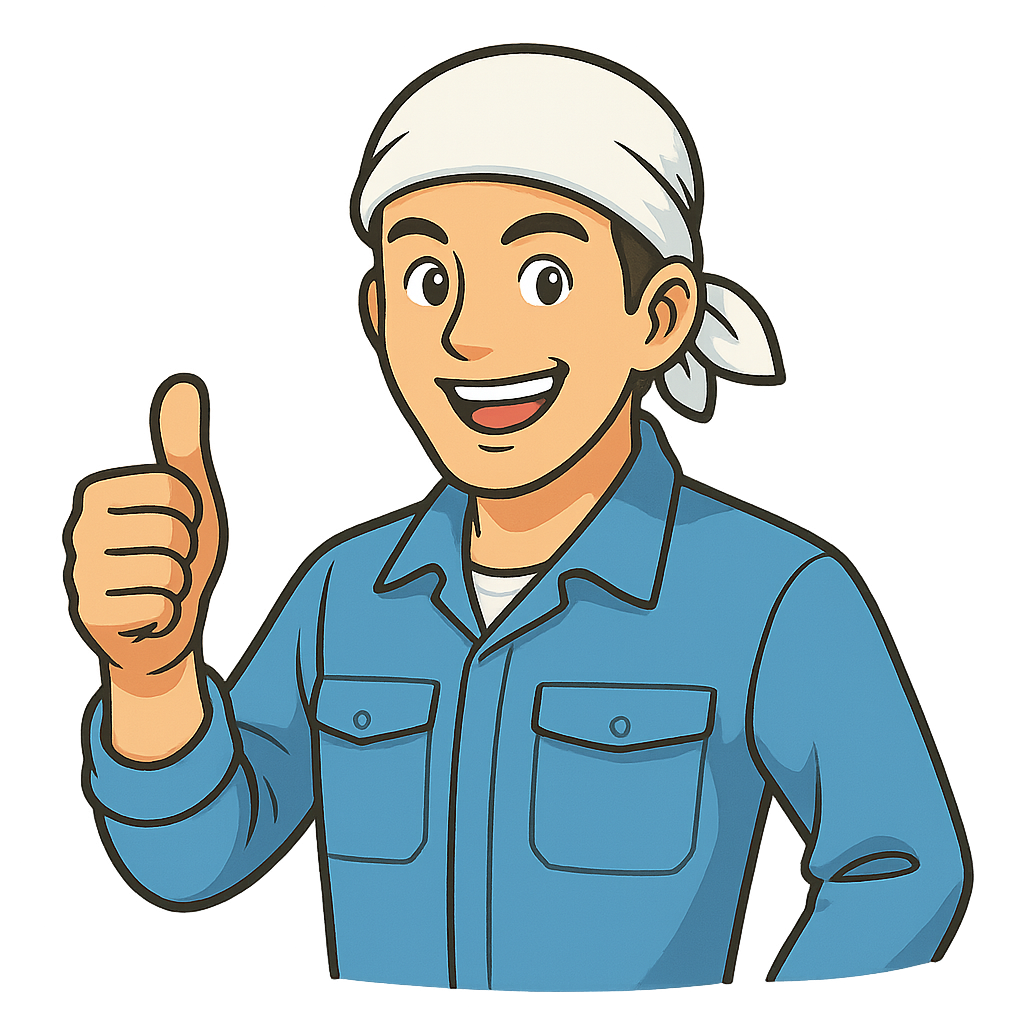
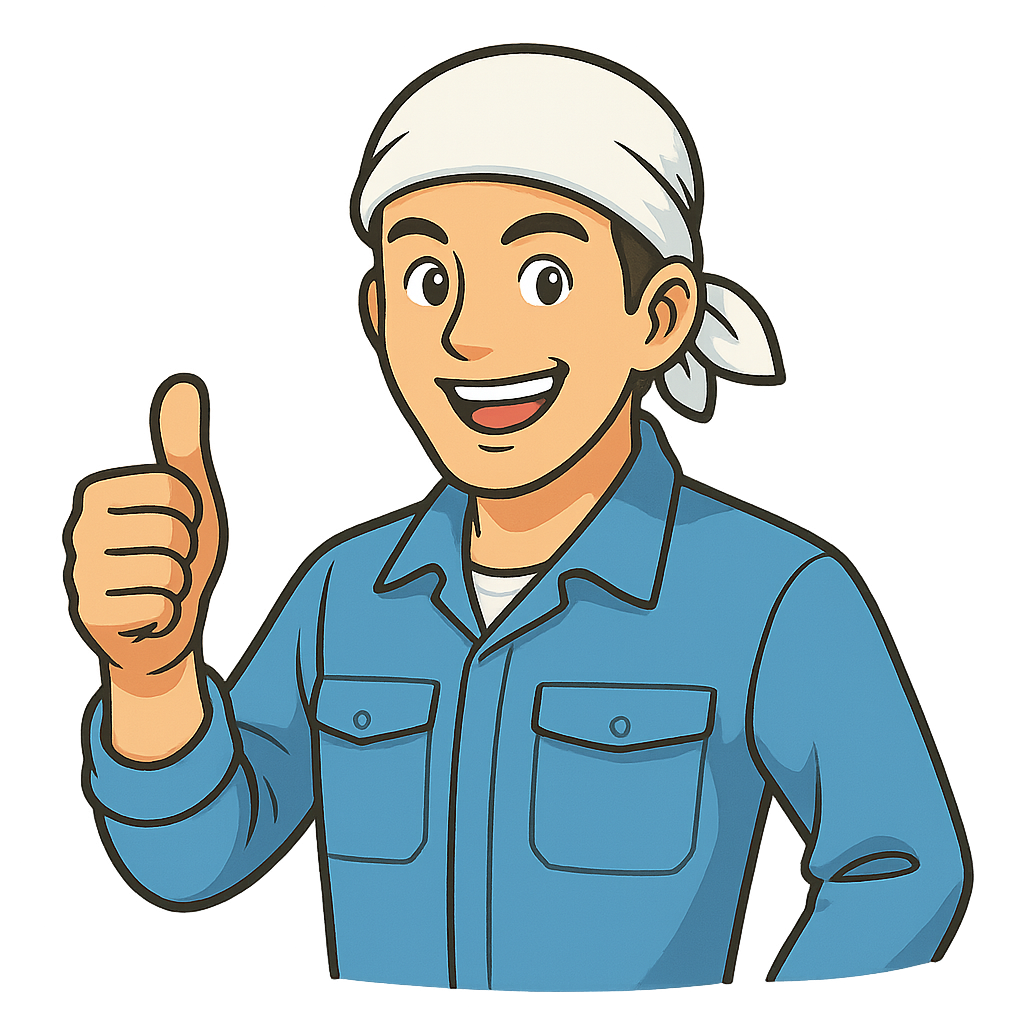
標準化を進める上で一番大切なのは、現場の作業者を巻き込むこと。特にベテランの方には、これまでの経験やプライドもあるでしょうから、敬意を払い、協力をお願いする姿勢が不可欠です。「やらされ感」ではなく、「みんなで良くしていく」という雰囲気を作ることが成功の秘訣ですよ。
効果的な作業手順書(SOP)作成のポイント
標準化の核となるのが「作業手順書(SOP)」です。「作ってみたけど、結局使われない…」とならないために、効果的な SOP を作成するためのポイントを押さえておきましょう。
① 5W1Hを明確にする
基本的なことですが、「誰が (Who)」「いつ (When)」「どこで (Where)」「何を (What)」「なぜ (Why)」「どのように (How)」作業するのかを明確に記述します。特に「なぜ、この手順が必要なのか(Why)」を説明することで、作業者の理解が深まり、納得感を持って取り組めるようになります。
② 写真やイラスト、動画を活用する
文字だけの説明では、実際の作業イメージを掴みにくいものです。各ステップの作業内容や、注意すべきポイントなどを、写真やイラスト、可能であれば短い動画などで示すと、格段に分かりやすくなります。
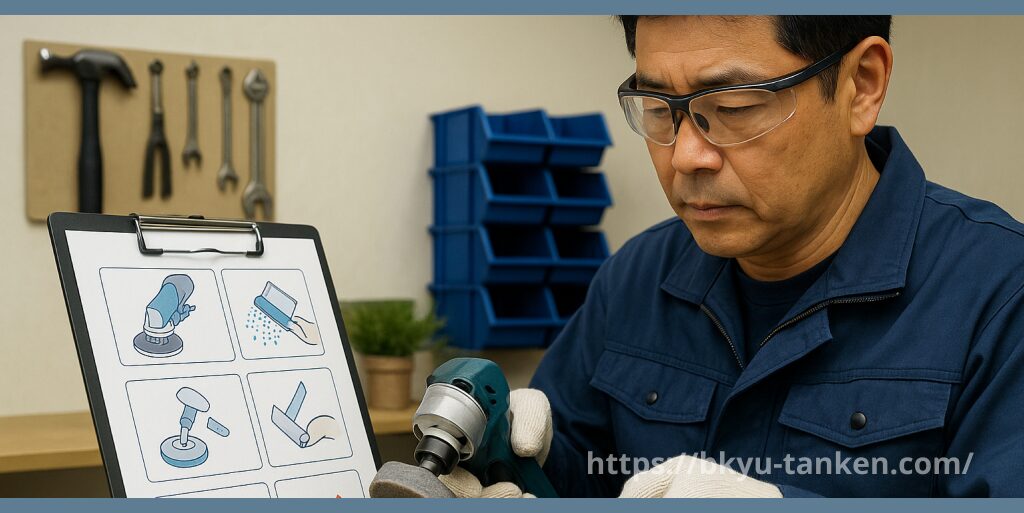
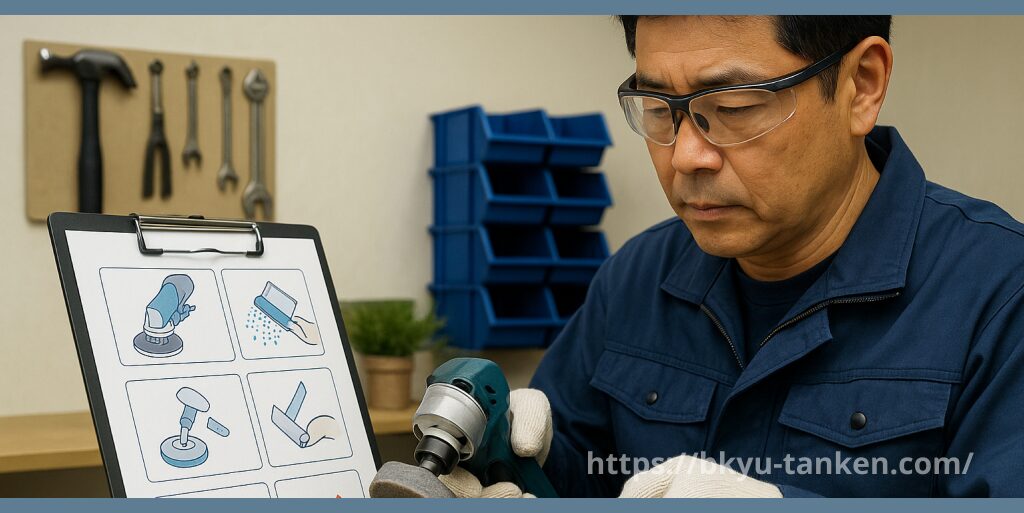
「百聞は一見に如かず」ですね。視覚的な情報は、言語や経験の差を超えて伝わりやすいというメリットもあります。
③ 数値化できるものは具体的に記述する
「適量」「十分」「しっかり」といった曖昧な表現は避け、できる限り具体的な数値で示しましょう。
- 研磨機の回転数(〇〇 rpm)
- 使用するバフ・研磨材の品番、番手
- 研磨時間(〇〇 秒/分)
- 押し付け圧力(可能であればゲージ圧などで示す、または感覚的な目安を具体的に記述)
- 検査基準(寸法公差 ±〇〇 mm、表面粗さ Ra 〇.〇 以下など)
数値を明確にすることで、作業の再現性が高まります。
④ 「コツ」や「注意点」も盛り込む
ベテランが持っている「言葉にしにくいけど重要な感覚」や「失敗しやすいポイント」なども、可能な限り具体的に記述します。
- 「〇〇のような音がしたら、圧力が強すぎるサイン」
- 「この部分を磨く時は、バフの角が当たらないように注意」
- 「研磨剤が乾いてきたら、少量追加する」
こうした、実践的な情報が、品質の安定化やミスの防止に役立ちます。
⑤ 定期的な見直しと改訂の仕組みを作る
一度作成した SOP も、新しい工具や材料が登場したり、より良い方法が見つかったりすれば、陳腐化していきます。
- 定期的な見直し:半年に 1 回、年に 1 回など、定期的に内容を確認する機会を設ける。
- 改訂履歴の管理:いつ、誰が、どの部分を、なぜ改訂したのかを記録に残す。
- 現場からのフィードバック:実際に SOP を使っている作業者からの意見や改善提案を収集する仕組みを作る。
SOP を「生きた文書」として維持管理していくことが重要です。
デジタル作業手順書作成ツール “Teachme Biz”
写真や動画ベースで簡単に SOP を作成・共有・管理できるクラウドサービス。ペーパーレス化と教育効率化を実現。
>>> 詳細・問い合わせはこちらから
まとめ
今回は、「脱・属人化」を目指すための研磨作業標準化について、その必要性からメリット、具体的な進め方、そして核となる作業手順書(SOP)作成のポイントまでを解説しました。
属人化の問題点
- 品質の不安定化、再現性の低さ
- 技術継承の困難、新人教育の非効率
- 特定作業者への過負荷、退職リスク 改善活動の妨げ
標準化のメリット
- 品質の安定化
- 効率向上、コスト削減
- 教育の迅速化、レベルアップ
- 技術・ノウハウの形式知化と共有
- 安全性の向上、ミスの削減
標準化 5 つのステップ
- 対象選定・目標設定
- 現状分析・見える化
- 手順確立・文書化(SOP作成)
- 教育・訓練と導入
- 効果測定・継続的改善
効果的な SOP 作成のポイント
- 5W1H の明確化
- 写真・イラスト・動画の活用
- 具体的な数値での記述
- 「コツ」「注意点」の明記
- 定期的な見直し・改訂
研磨作業の標準化は、目先の品質や効率を改善するだけでなく、会社の持続的な成長と、未来を担う人材育成の基盤となります。簡単な取り組みではありませんが、まずは小さな一歩から始めてみませんか?
是非、この記事を参考に「SOP」を作成してみてはいかがでしょうか?
コメント