【研磨職人タカ直伝】研磨作業の効率化!今すぐ試せる3つの時間短縮テクニック
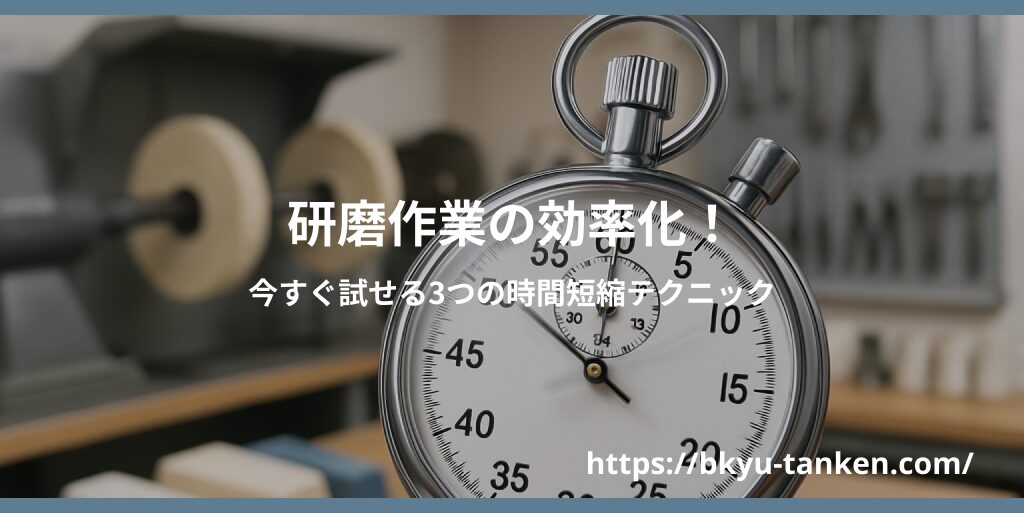
「納期が迫ってるのに、研磨作業が終わらない…」
「一人あたり、一日にもっと多くの部品を磨けるようにならないか?」
「研磨工程がボトルネックになって、全体の生産性が上がらない…」
中小企業の金属加工現場で、日々研磨作業に奮闘されている皆さん、こんにちは!金属研磨ドットコムの研磨職人タカです。業界歴 20 年以上の経験から言わせてもらうと、「研磨時間は、工夫次第でいくらでも短縮できる」というのが持論です。
「時間=コスト」である製造業において、研磨作業の効率化は、生産性向上、コスト削減、そして納期遵守に直結する、経営的にも非常に重要な課題です。しかし、「具体的に何をすれば時間が短縮できるのか分からない」と悩んでいる担当者の方も多いのではないでしょうか?
そこで今回は、研磨職人タカが、日々の現場で実践してきた経験に基づき、研磨作業の時間を短縮するための具体的な 3 つのテクニックを、分かりやすくご紹介します。「ウチでもすぐに試せそう!」と思っていただけるような、実践的な内容に絞りました。
この記事を読めば、あなたの会社の研磨作業が、もっと速く、もっと効率的になるヒントがきっと見つかります。無駄な時間をなくし、生産性を劇的に向上させましょう!
なぜ研磨作業に時間がかかるのか?主な原因を探る
時間短縮テクニックをお伝えする前に、まず「なぜ研磨作業に時間がかかってしまうのか?」その主な原因を簡単に整理しておきましょう。原因が分かれば、対策も立てやすくなります。
工程の多さと複雑さ
金属研磨は、多くの場合、単一の工程で終わることはありません。素地の状態から、粗研磨、中仕上げ、最終仕上げ(鏡面など)へと、段階的に表面を整えていく必要があります。使用する工具や研磨材の種類も多く、工程が複雑になればなるほど、当然時間はかかります。特に、求められる品質レベルが高いほど、工程数は増える傾向にあります。
工具・消耗品の選定ミス
研磨に使用するバフ、ベルト、ディスク、研磨剤などの選定が適切でないと、思うように削れなかったり、逆に削りすぎて手直しが必要になったりして、余計な時間がかかってしまいます。「とりあえずこれを使っている」という状態では、非効率が生じやすいのです。また、消耗品の寿命が短いと、交換頻度が高くなり、その時間もロスになります。
段取り・準備の手間
意外と見落とされがちなのが、「実際に研磨している時間」以外の時間です。ワークを治具にセットする時間、必要な工具や研磨剤を探す時間、バフやベルトを交換する時間、作業場所を片付ける時間など、「段取り」や「準備」にかかる時間が積み重なると、かなりのロスになります。
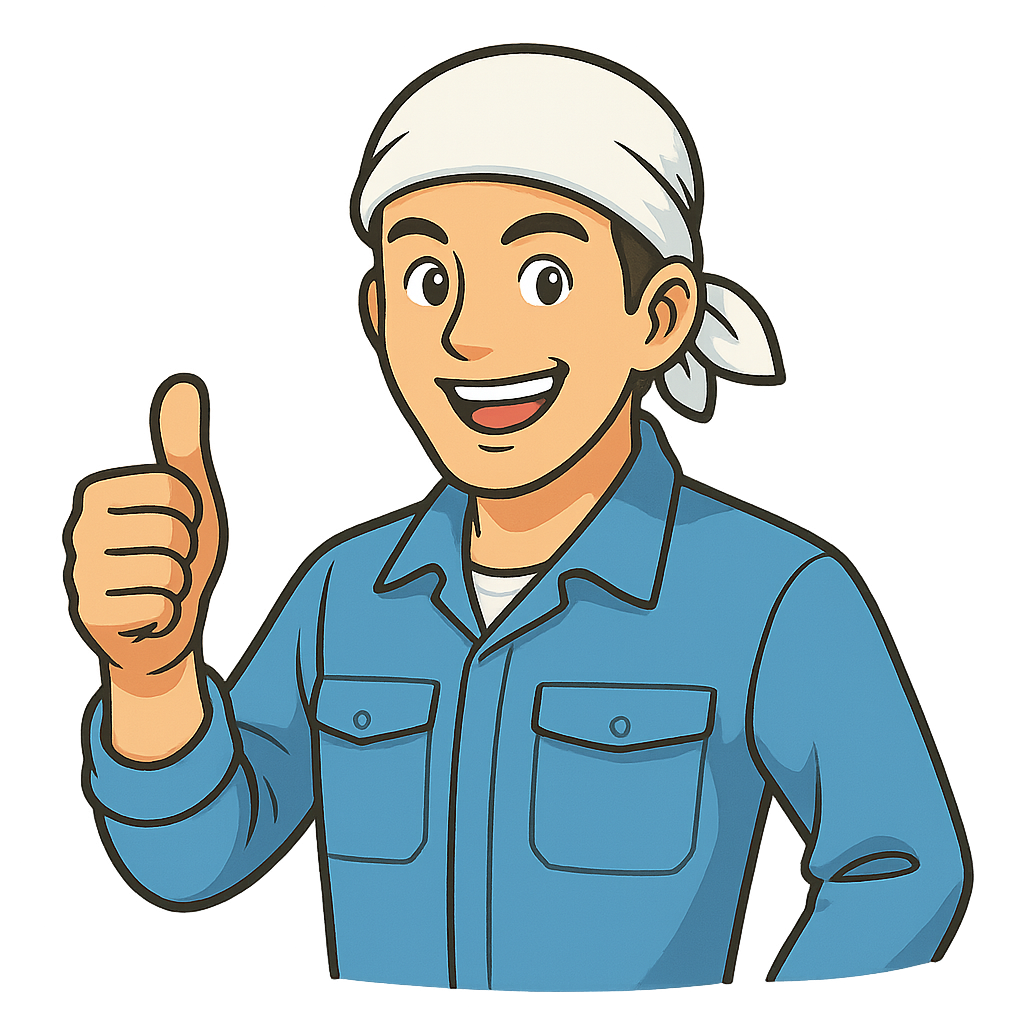
これらの原因は、複合的に絡み合っていることが多いです。だからこそ、一つの側面だけでなく、多角的にアプローチしていくことが、研磨作業の効率化には不可欠なんです。これから紹介する 3 つのテクニックは、これらの原因にそれぞれアプローチするものですよ。
【テクニック①】研磨工程の最適化:無駄をなくし流れを作る
まず取り組むべきは、研磨作業そのもののプロセスを見直し、無駄を徹底的に排除することです。
適切な研磨ステップの設計(粗→中→仕上げ)
「急がば回れ」という言葉があるように、研磨も手順が重要です。最終的な仕上げ品質から逆算し、「どの程度の粗さから始めて、どの番手(砥粒の粗さ)で、どの段階まで磨くか」という研磨ステップを適切に設計します。
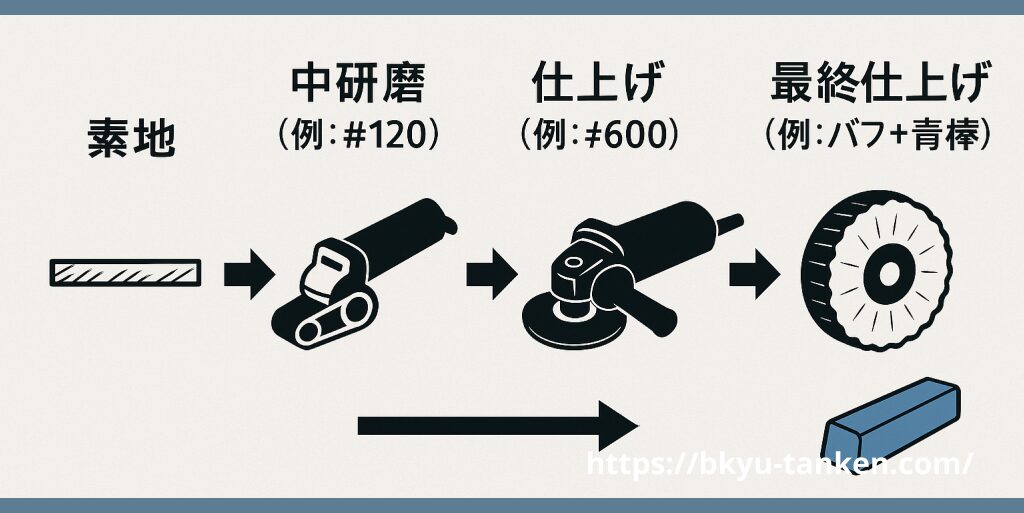
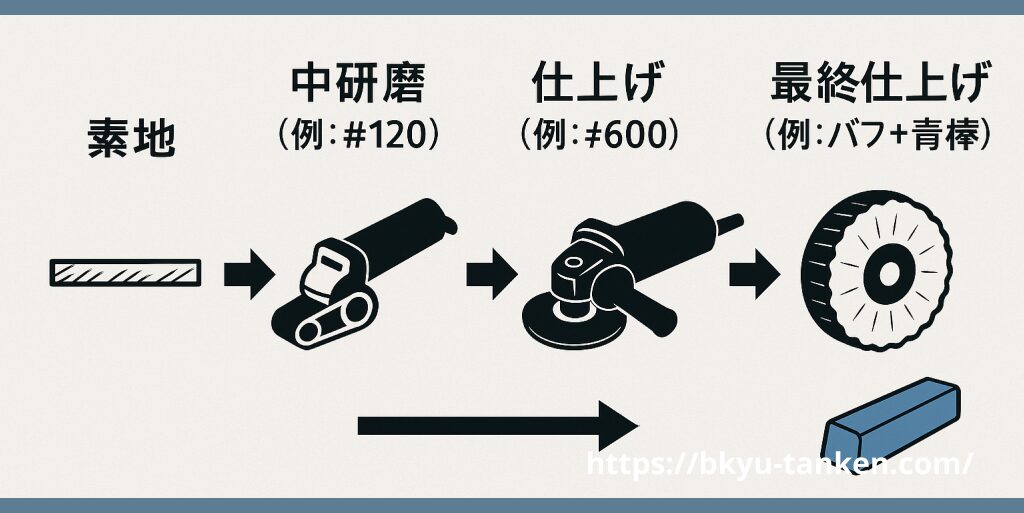
例えば、いきなり細かい番手で磨き始めても、深い傷はなかなか消えません。逆に、粗い番手で削りすぎると、その傷を消すために後工程で余計な時間がかかります。前工程の砥粒の目(研磨痕)を、次の工程で効率的に消せるような番手選びとステップ設定が、時間短縮の鍵です。
高性能な研磨材・バフの活用
「昔からこれを使っているから」という理由だけで、同じ研磨材やバフを使い続けていませんか?研磨材やバフの技術は日々進化しています。
- 高研削力の研磨材:より短い時間で目的の研削量に到達できる高性能な砥粒(セラミック砥粒など)を使った研磨材を選ぶ。
- 長寿命の消耗品:摩耗しにくく、交換頻度を減らせる耐久性の高いバフやベルトを選ぶ。
- 目詰まりしにくい製品: 目詰まりによる研磨力低下や交換の手間を減らせる製品(オープンコート構造の研磨紙布、特殊加工のバフなど)を選ぶ。
初期コストは多少高くても、トータルの作業時間短縮や消耗品コスト削減効果を考えれば、高性能な製品への切り替えは十分に検討する価値があります。
「手戻り」をなくす工夫
研磨作業で最も無駄な時間の一つが、「やり直し(手戻り)」です。磨き残しがあったり、逆に磨きすぎて寸法不良になったりすると、修正のために膨大な時間がかかってしまいます。
- 工程ごとのチェック:各研磨ステップが終わるごとに、狙い通りの状態になっているかを確認する習慣をつける。目視だけでなく、必要に応じて粗さ測定器などを使う。
- 標準化と教育:作業者によってやり方が違うと、品質がばらつき、手戻りの原因になります。最適な研磨手順を標準化し、作業者への教育を徹底する。
- 不良原因の分析:手戻りが発生したら、「なぜそうなったのか?」を分析し、再発防止策を講じる。
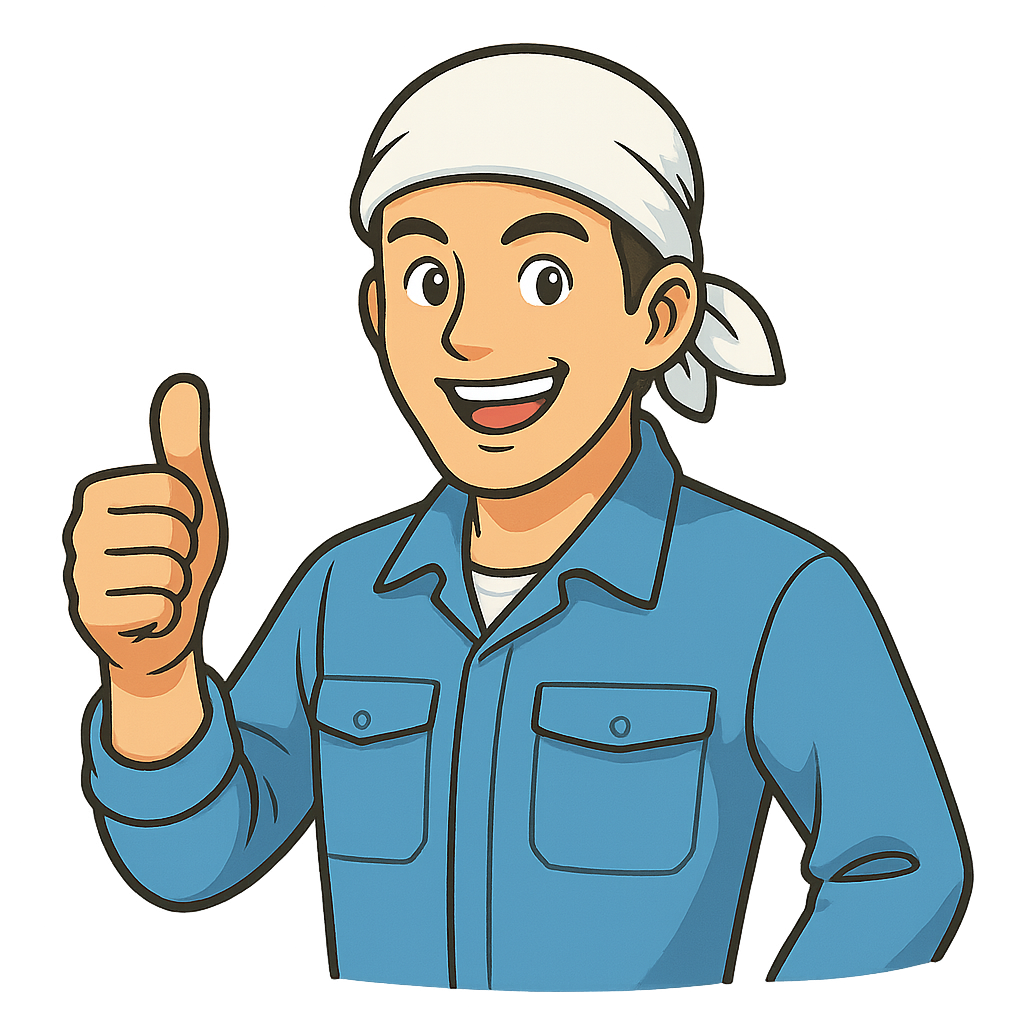
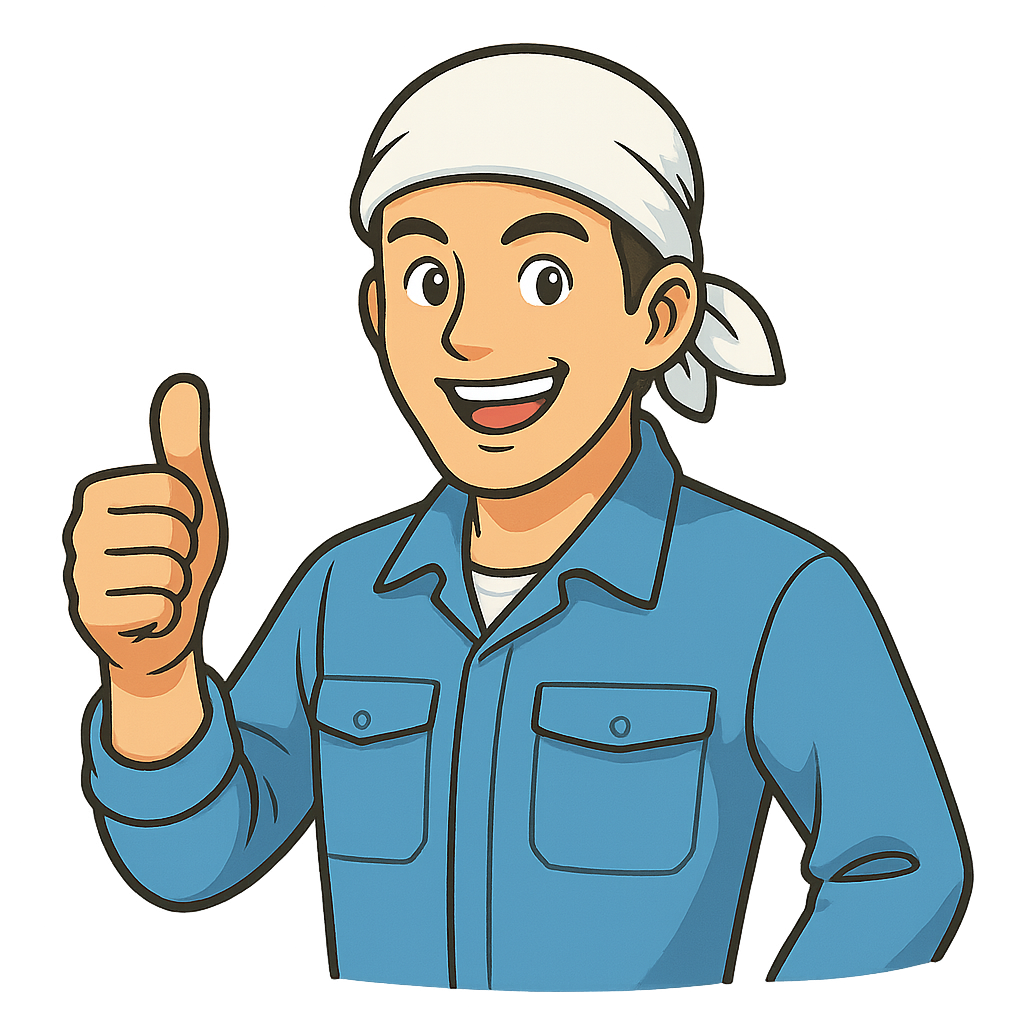
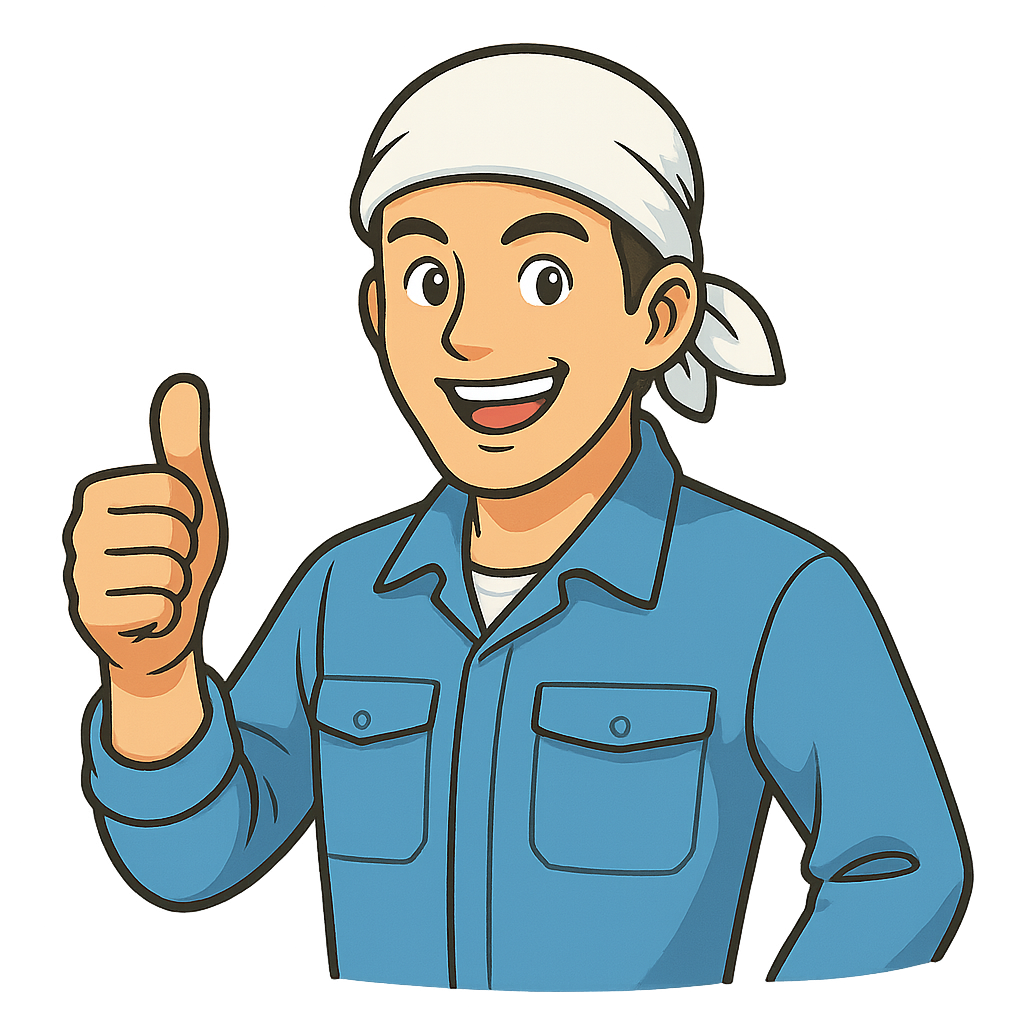
特に新人さんに多いのが、「早く終わらせよう」と焦って、確認を怠ってしまうケース。各工程でしっかり「止まって、見て、確認する」勇気を持つことが、結果的に一番の近道になることも多いんですよ。
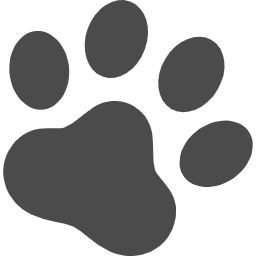
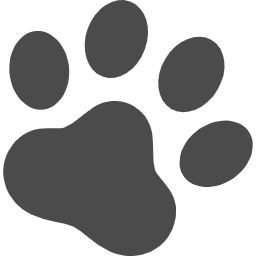
【テクニック②】段取り時間の徹底削減:準備を制する者は研磨を制す
研磨作業そのものの効率化と並行して、あるいはそれ以上に効果的なのが、「段取り時間の削減」です。研磨以外の時間にいかに無駄があるか、見直してみましょう。
治具・固定具の活用と標準化
ワークを手で押さえながら研磨していませんか?不安定な状態で研磨すると、時間がかかる上に危険です。また、製品ごとに押さえ方を工夫するのも時間の無駄です。
- 専用治具の製作:よく加工する製品については、ワンタッチで確実に固定できる専用の治具を製作・導入する。
- 汎用治具の活用: 様々な形状に対応できるモジュラー式の治具やバイスなどを活用し、段取り替えを容易にする。
- 治具の標準化・管理:治具を標準化し、誰でもすぐに使えるように置き場所などを決めて管理する。
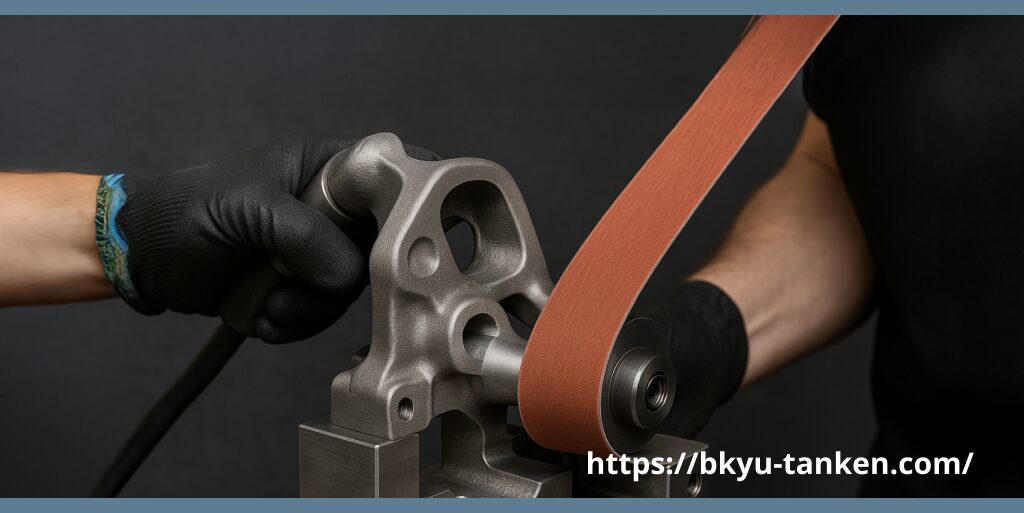
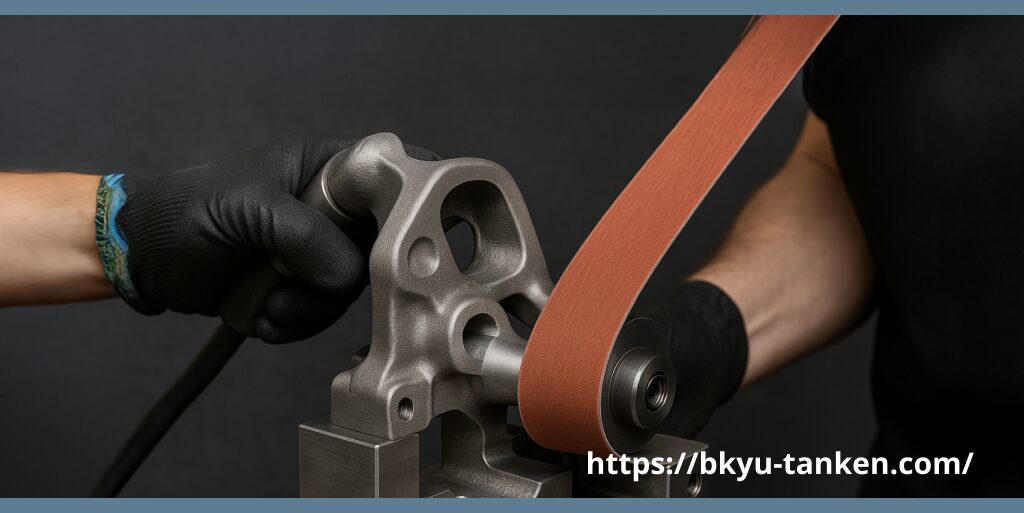
治具への初期投資は必要ですが、毎回の固定時間短縮、安定した研磨による品質向上、安全性向上といったメリットは非常に大きいです。
工具交換の迅速化(クイックチェンジ等)
研磨工程では、番手や種類の異なるバフ、ベルト、ディスクなどを頻繁に交換する必要があります。この交換作業に手間取っていては、時間がもったいないです。
- クイックチェンジシステムの導入:工具の着脱がネジ締め不要で、ワンタッチまたは簡単な操作で行えるクイックチェンジ式のホルダーやアダプターを導入する。
- 工具の事前準備:次に使う工具をあらかじめ近くに準備しておく。
- 交換手順の標準化・訓練:工具交換の手順を最も効率的な方法に標準化し、作業者がスムーズに行えるように訓練する。
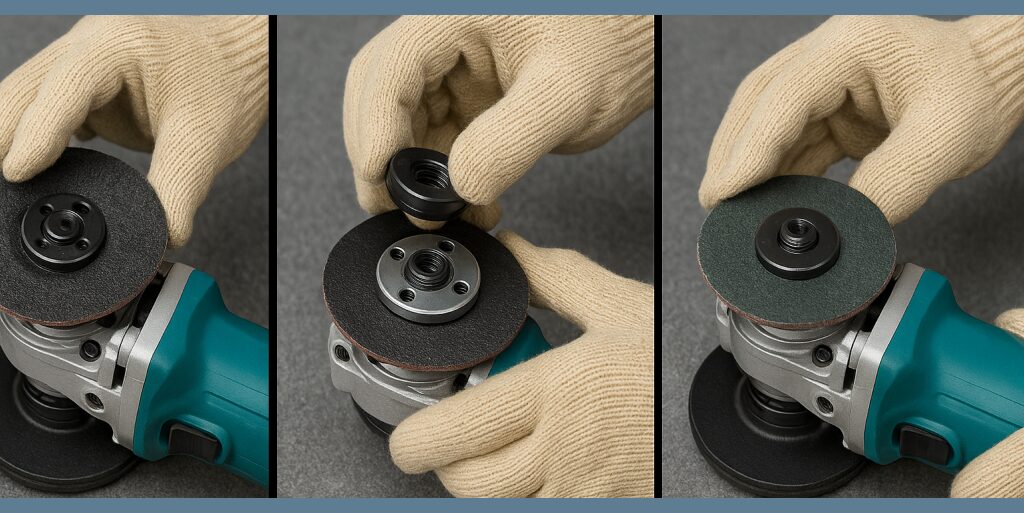
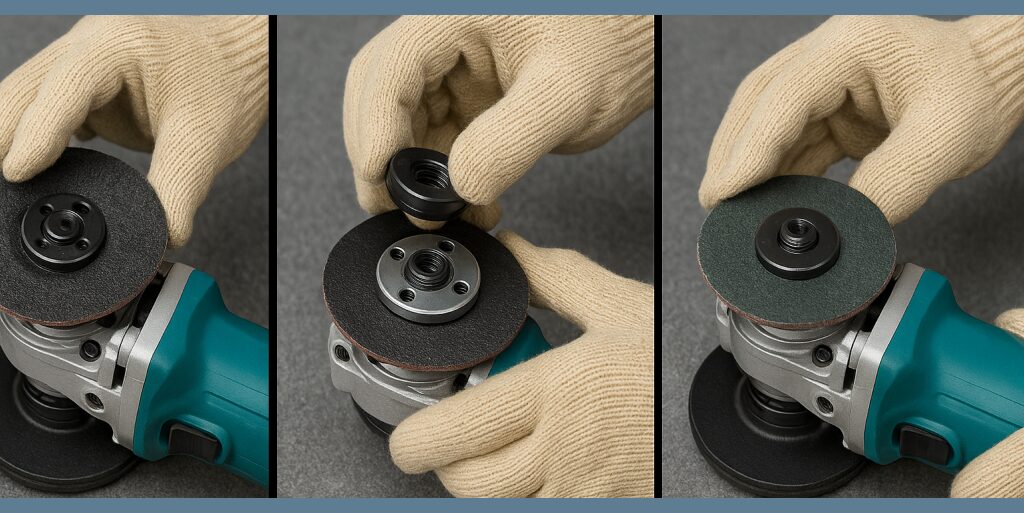
数秒、数十秒の短縮でも、一日、一週間、一ヶ月と積み重なれば、膨大な時間になります。
5S活動による作業環境整備
「あれ、あのバフどこに置いたっけ?」「工具を探すのに時間がかかる…」こんな経験はありませんか? 作業環境が乱雑だと、物を探す時間(探索ロス)や、移動の無駄が発生し、効率を大きく低下させます。
5S(整理・整頓・清掃・清潔・躾)を徹底し、常に働きやすい環境を維持することが重要です。
- 整理:要るものと要らないものを分け、不要なものは処分する。
- 整頓:必要なものを、決められた場所に、使いやすいように配置し、表示する(見える化)。
- 清掃:作業場や機械を常にきれいに保ち、点検も兼ねる。
- 清潔:整理・整頓・清掃の状態を維持する。
- 躾:決められたルールを守る習慣をつける。
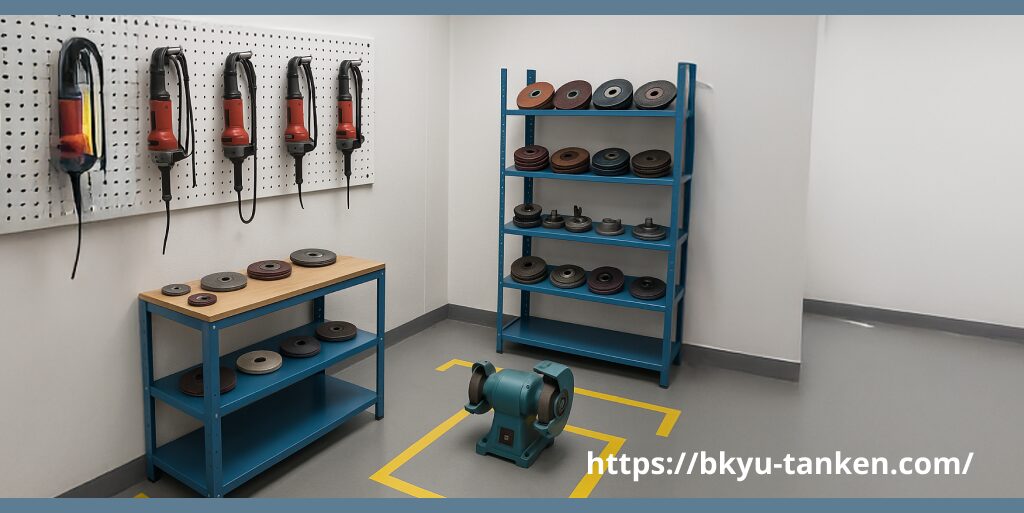
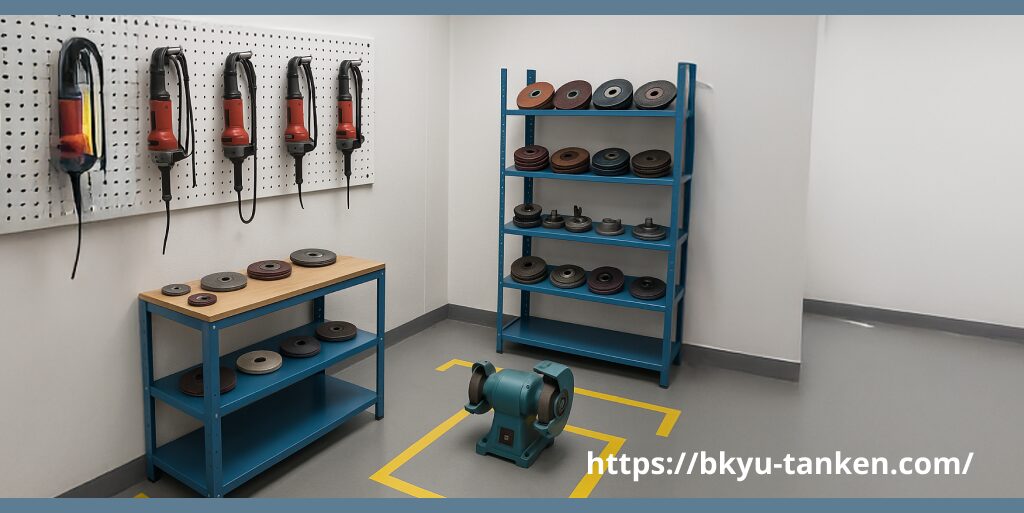
5Sは、効率化だけでなく、安全性の向上や、従業員のモチベーションアップにもつながる、非常に基本的かつ重要な活動です。
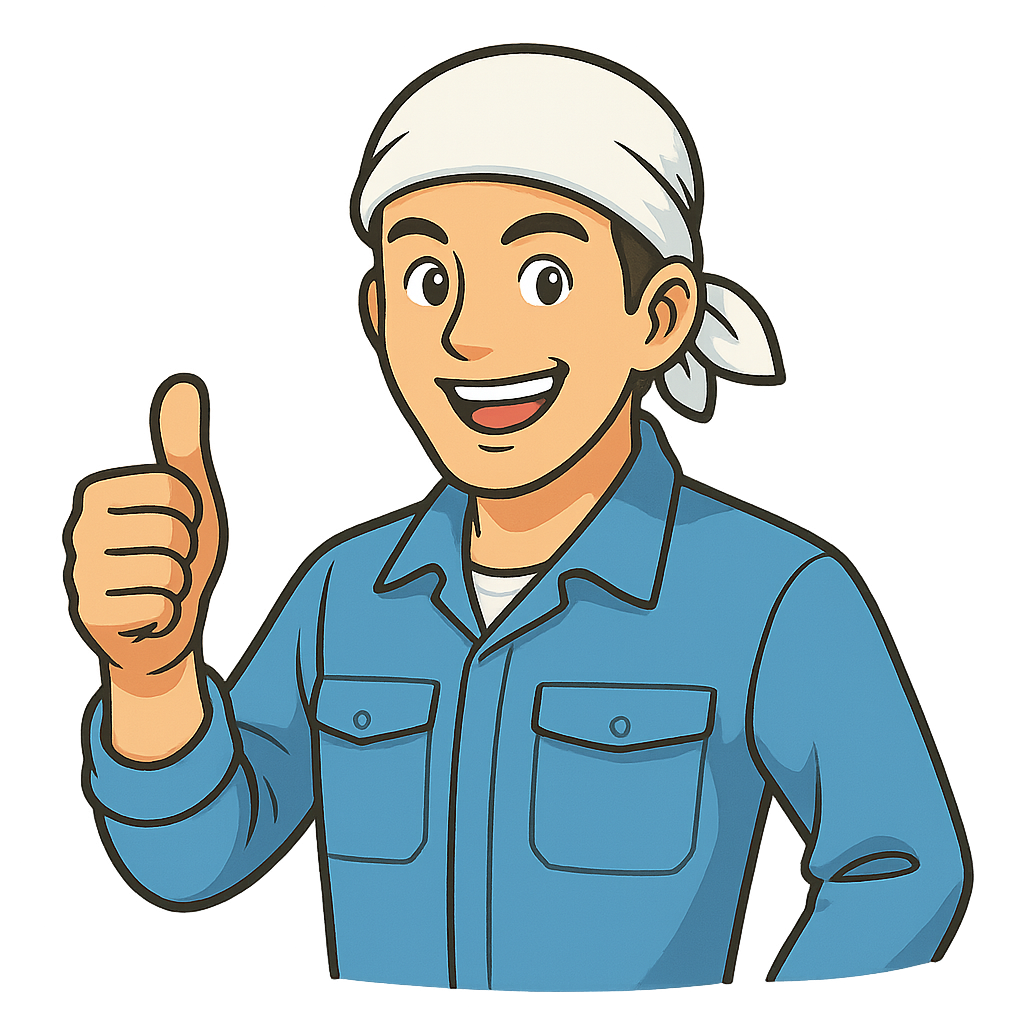
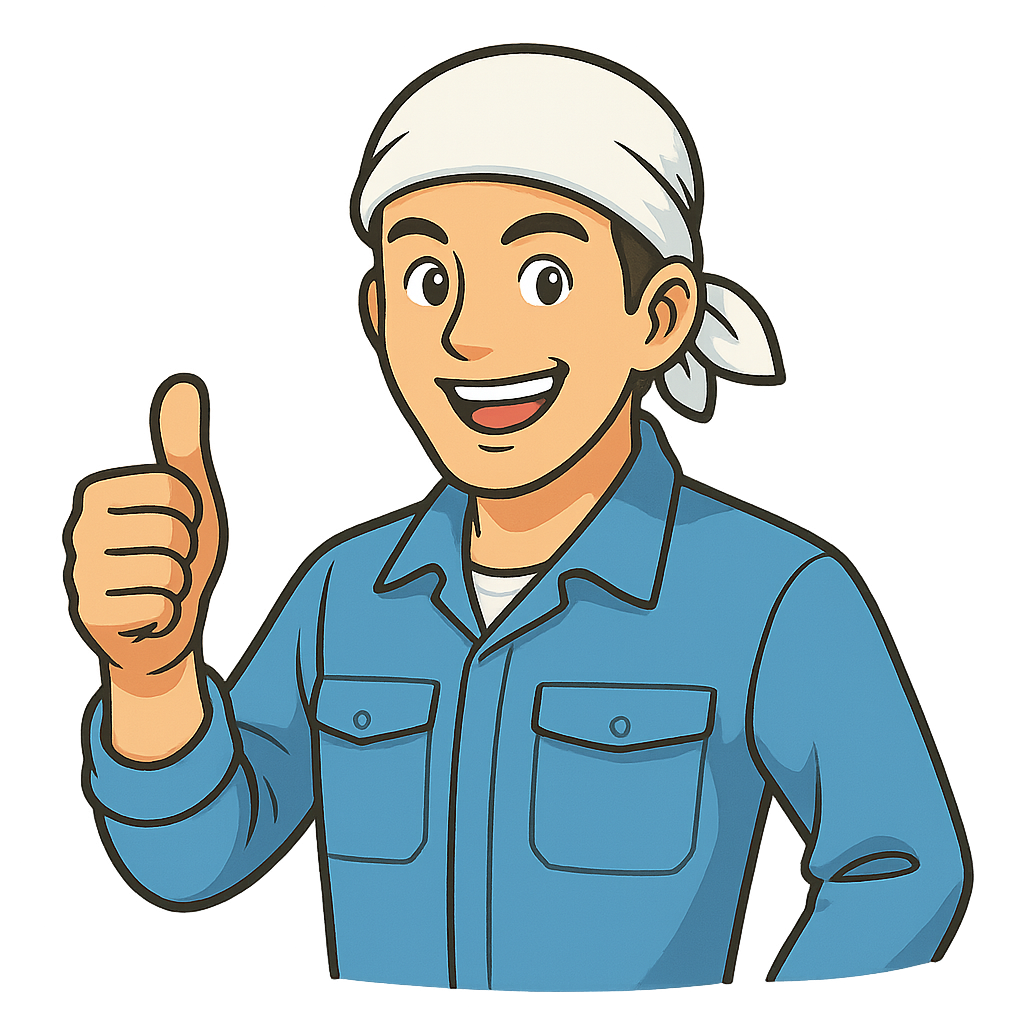
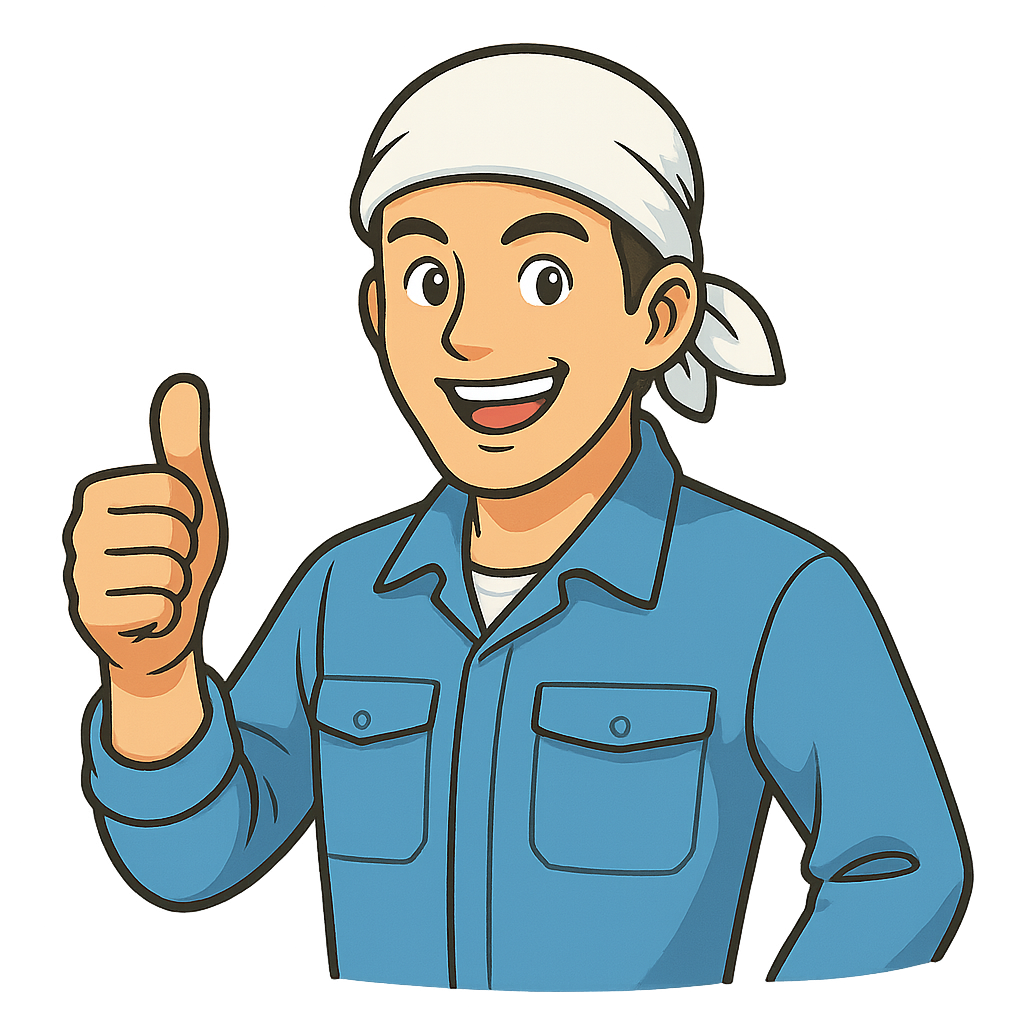
段取り改善は、地味に見えるかもしれませんが、効果は絶大です。「塵も積もれば山となる」の典型ですね。特に5Sは、お金をかけずにすぐに始められる効率化の第一歩ですよ!
【テクニック③】自動化・省力化の検討:人と機械のベストミックス
最後のテクニックは、人の力だけに頼るのではなく、機械や装置の力を借りて効率化を図るアプローチです。
単純・反復作業のロボット化
もし、毎日同じような形状の部品を、大量に、同じ手順で研磨しているのであれば、研磨ロボットの導入は非常に有効な時間短縮策となり得ます。
- 24時間稼働:ロボットは休憩なしで長時間稼働できるため、圧倒的な生産量を実現可能。
- 品質の安定化:プログラム通りに動作するため、人によるばらつきがなく、均一な品質を保てる。
- 労働環境の改善:過酷な研磨作業をロボットに任せることで、作業者の負担を軽減できる。
もちろん、導入には初期投資やティーチングなどの課題もありますが、人手不足が深刻化する中、単純・反復作業の自動化は、将来を見据えた重要な選択肢です。以前の記事(研磨ロボット導入のメリット・注意点)も参考にしてください。
簡易自動機・省力化装置の導入
「ロボット導入はハードルが高い…」と感じる場合でも、諦める必要はありません。特定の工程や作業を補助する、比較的安価な簡易自動機や省力化装置も多く存在します。
- 簡易研磨機:特定の形状(パイプ、平面など)の研磨を半自動で行う装置。
- 搬送装置:ワークの供給や排出を自動化するコンベアやローダー。
- パワーアシスト装置:重いワークの持ち運びや操作を補助する装置。
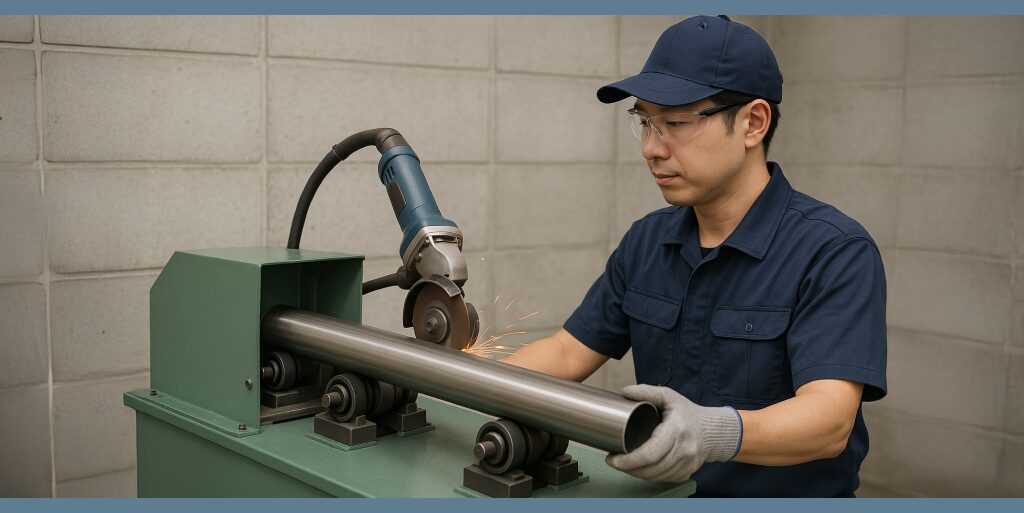
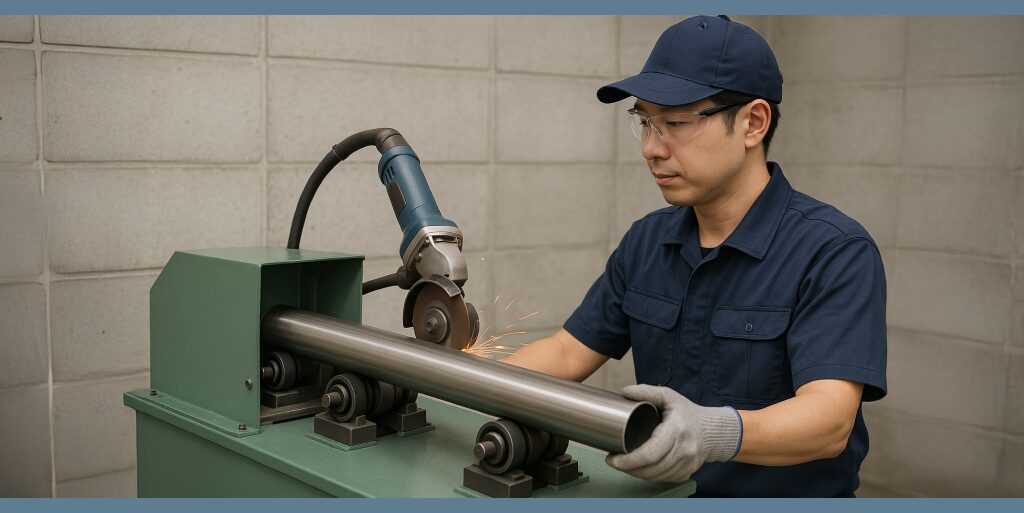
全ての工程を自動化するのではなく、最も時間がかかっている工程や、負担の大きい作業をピンポイントで補助するだけでも、大きな効率化につながる場合があります。
作業者の多能工化と役割分担
機械化だけでなく、「人の使い方」を見直すことも重要です。
- 多能工化:一人の作業者が複数の工程や作業(例えば、研磨だけでなく前後の工程や検査)を担当できるように訓練する。これにより、特定の作業者の不在時にも生産が滞るリスクを減らせます。
- 役割分担の見直し:熟練者は高度な判断が必要な作業や仕上げ工程に集中し、比較的単純な作業(材料準備、粗磨き、運搬など)は他の作業者やパートタイマーなどが担当するなど、スキルレベルに応じた最適な役割分担を検討する。
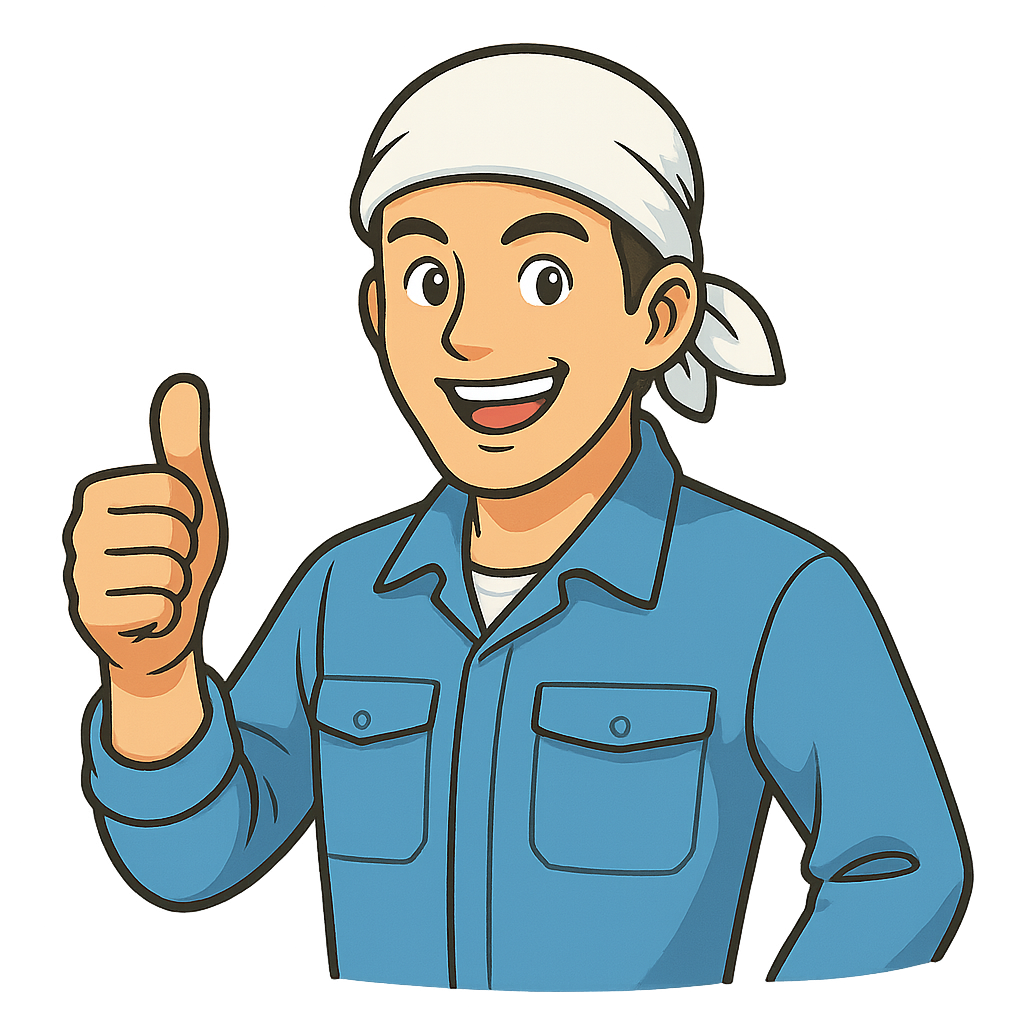
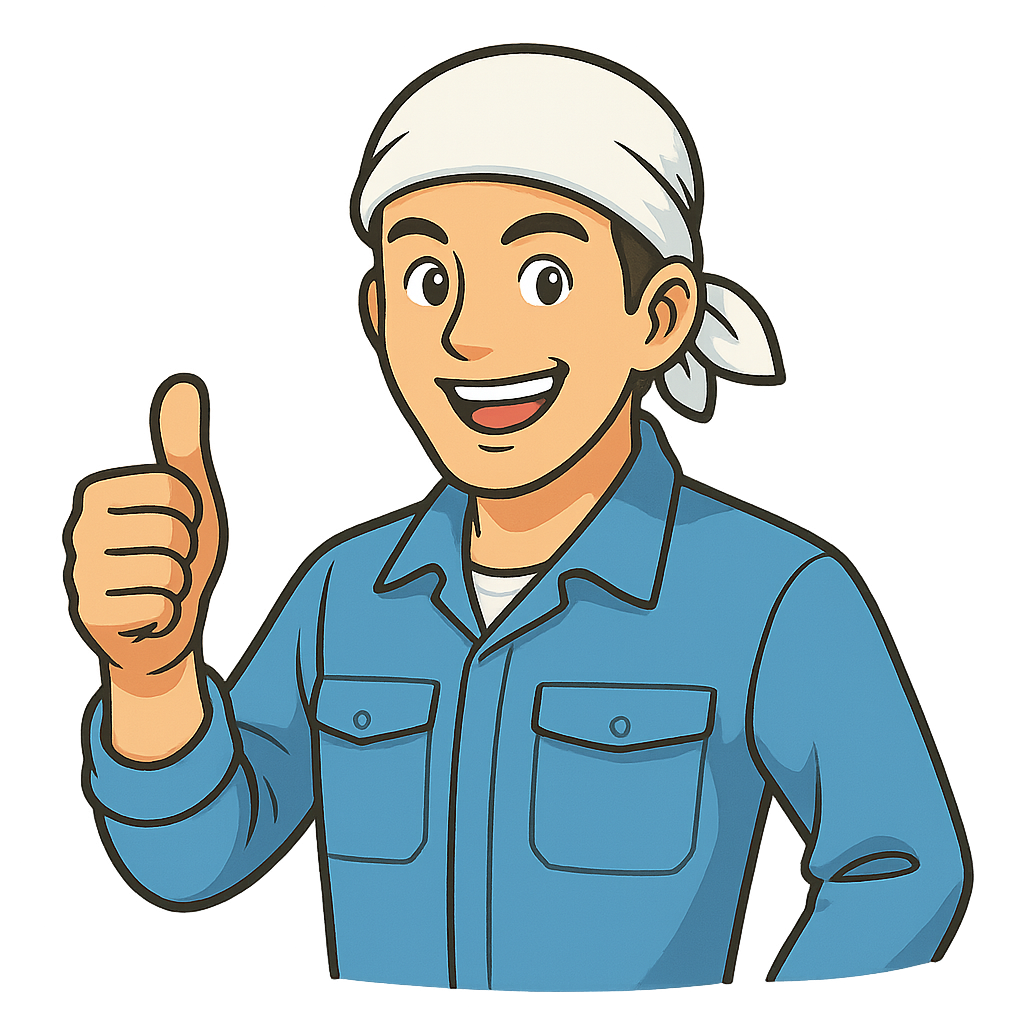
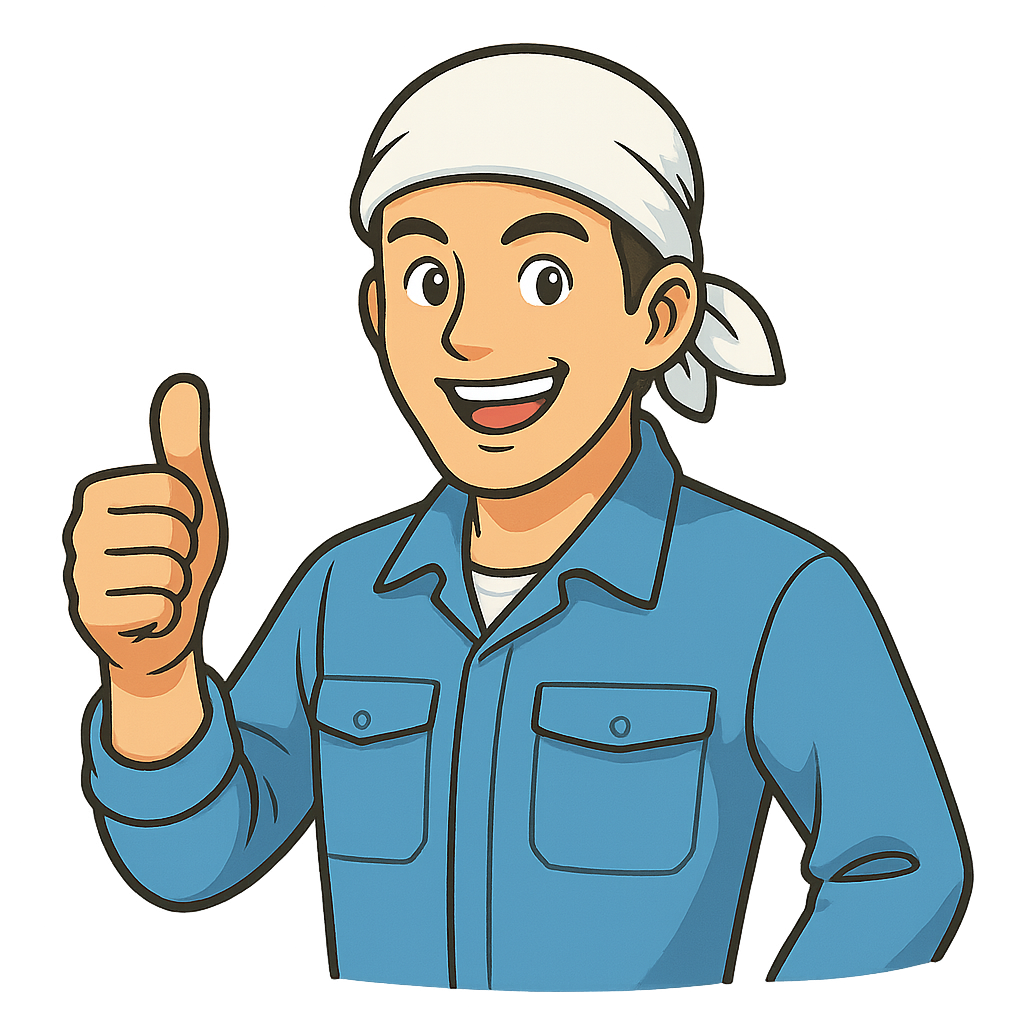
機械と人間の得意なことをうまく組み合わせる「ベストミックス」が重要です。単純作業は機械に任せ、人はより付加価値の高い作業や、機械では難しい複雑な作業に集中する。これが、これからの研磨現場の目指すべき姿かもしれませんね。
まとめ
今回は、研磨作業の時間短縮を実現するための具体的な 3 つのテクニックをご紹介しました。
時間短縮 3 つのテクニック
- 研磨工程の最適化:適切なステップ設計、高性能な消耗品の活用、手戻りの撲滅。
- 段取り時間の徹底削減:治具の活用・標準化、工具交換の迅速化、5S による環境整備。
- 自動化・省力化の検討:単純作業のロボット化、簡易自動機・省力化装置の導入、人の役割分担見直し。
研磨作業の効率化は、一朝一夕に達成できるものではありません。しかし、今回ご紹介したテクニックの中から、まずは一つでも、自社の状況に合わせて「これならできそうだ」と思うものから試してみてはいかがでしょうか。
小さな改善の積み重ねが、やがて大きな時間短縮、生産性向上につながります。「時間は有限、工夫は無限」です!
もし、「自社の場合はどうすれば?」「この製品を使えば効率は上がる?」といった具体的なご相談があれば、いつでも金属研磨ドットコムの研磨職人タカまで、お気軽にお声がけください。
コメント