手作業研磨 vs 機械研磨:コストと品質比較
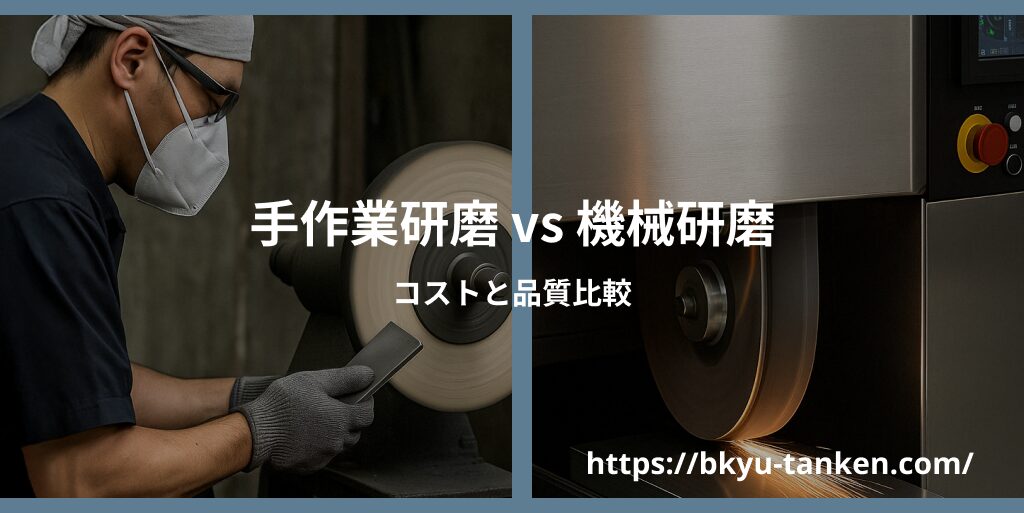
研磨工程の選択に迷っていませんか?「手作業研磨」と「機械研磨」、どちらが自社の製品に最適なのか、判断が難しいものです。本記事では、20年以上の実務経験を持つ研磨職人の視点から、両方式の正確なコストと品質の比較をご紹介します。
「納期を短縮したいけれど、品質は落としたくない」
「コスト削減と品質向上を同時に実現したい」
「少量多品種生産に最適な研磨方法は?」
こういった悩みを抱える中小製造業の現場責任者の方々に向けて、メリット・デメリットを徹底解説します。記事の最後には、御社の状況に合わせた研磨方法を選ぶための具体的な判断基準もご提案。導入事例と共に、最適な研磨ソリューションへの道筋を示します。
1. 手作業研磨と機械研磨の基本的な違い
研磨方法を選ぶ前に、まずは両者の基本的な特徴を理解しましょう。
手作業研磨の特徴
手作業研磨とは、熟練した職人が手持ちの工具や砥石を使って金属表面を磨き上げる方法です。人の手による繊細な感覚と判断が最大の武器となります。
主な特徴
- 職人の経験と技術に依存
- 複雑な形状や細部の研磨に対応可能
- 一点ものや特殊形状に最適
- 設備投資が比較的少ない
- 技術習得に時間がかかる
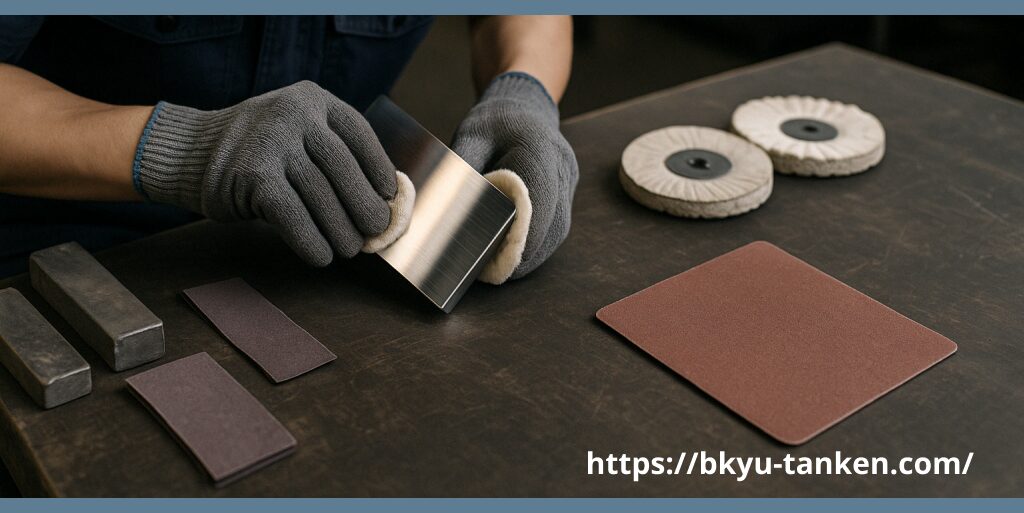
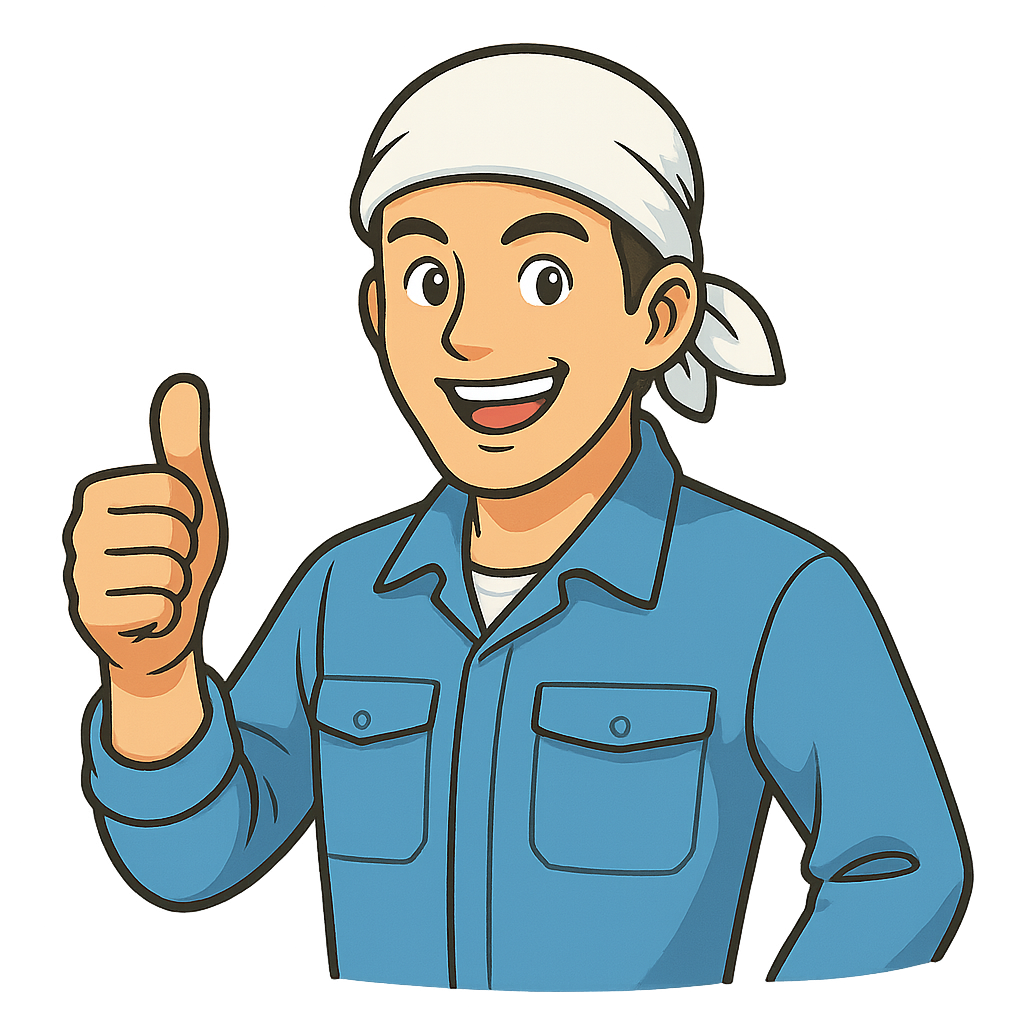
手作業研磨の最大の魅力は「対応力」です。機械では難しい複雑形状や、一品ものの特殊な仕上げも可能です。ただし、人によるバラつきをいかに抑えるかが永遠の課題でもあります。
手作業研磨では、サンドペーパーから始まり、徐々に目の細かい研磨材へと移行していきます。最終的には布バフなどを使用して鏡面仕上げを行うこともあります。職人の感覚で圧力や角度を微調整しながら進めるため、細やかな対応が可能です。
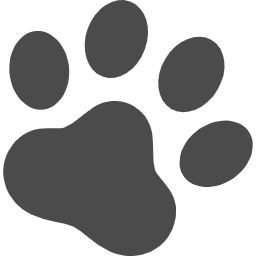
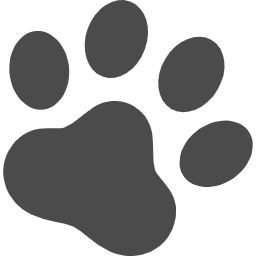
機械研磨の特徴
機械研磨は、専用の研磨機械を使用して金属表面を処理する方法です。自動化された一定の条件下で研磨を行うため、安定した品質を保つことができます。
主な特徴
- 均一で安定した仕上がり
- 大量生産に適している
- 作業効率が高い
- 初期投資コストが高い
- 形状によっては対応が難しい


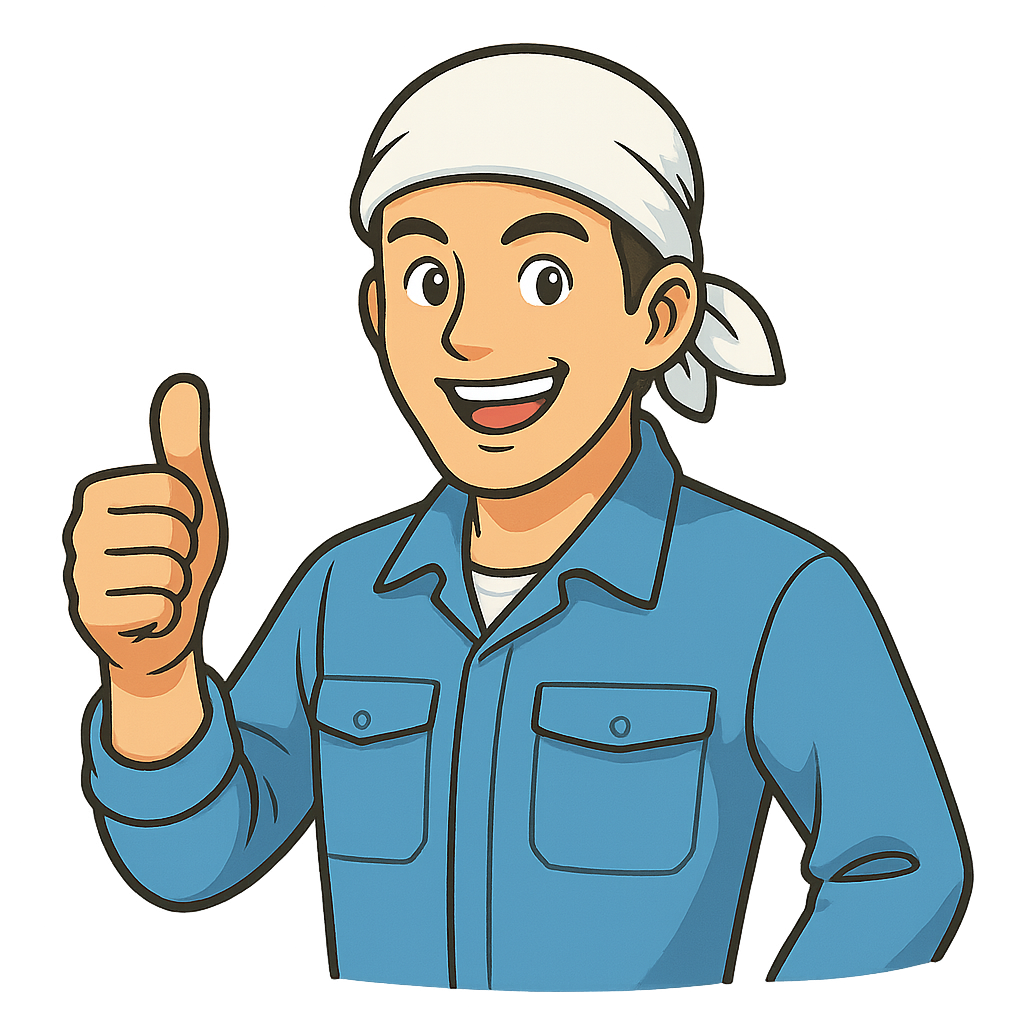
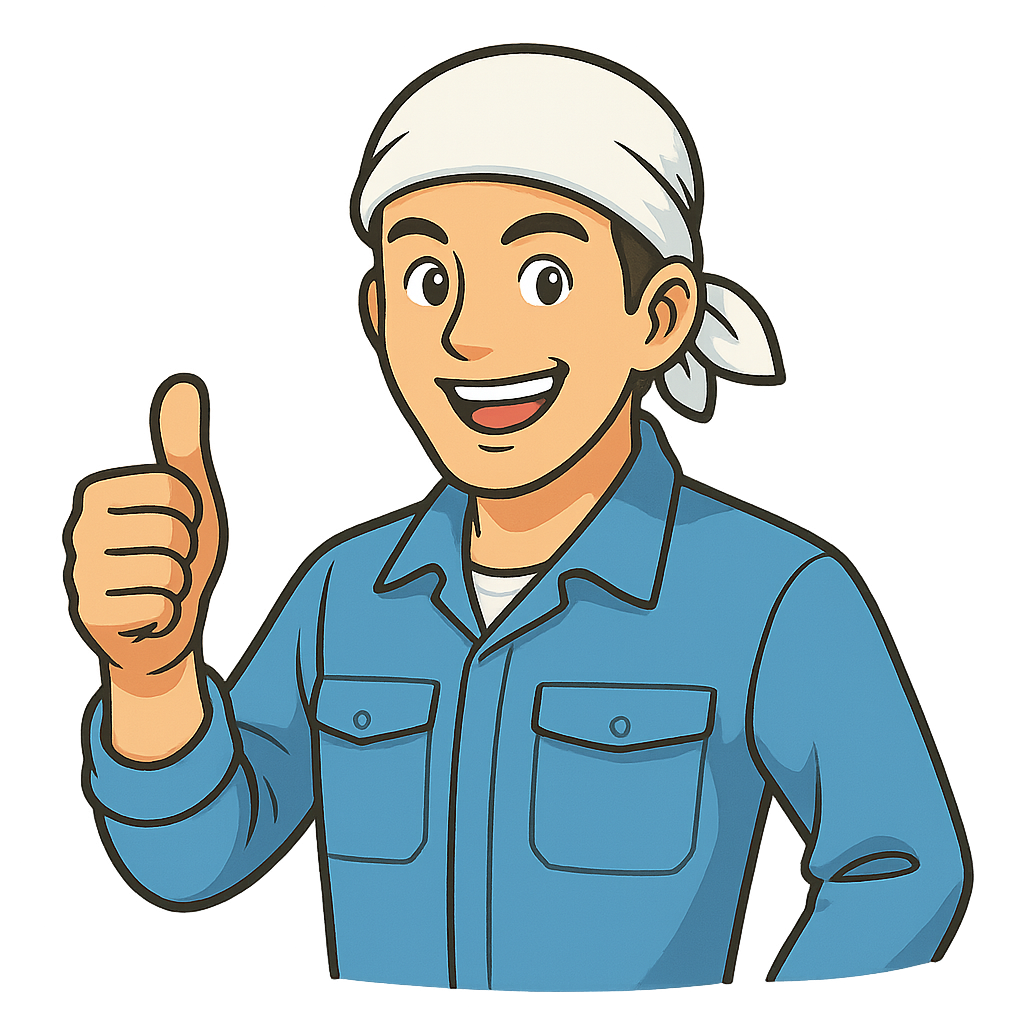
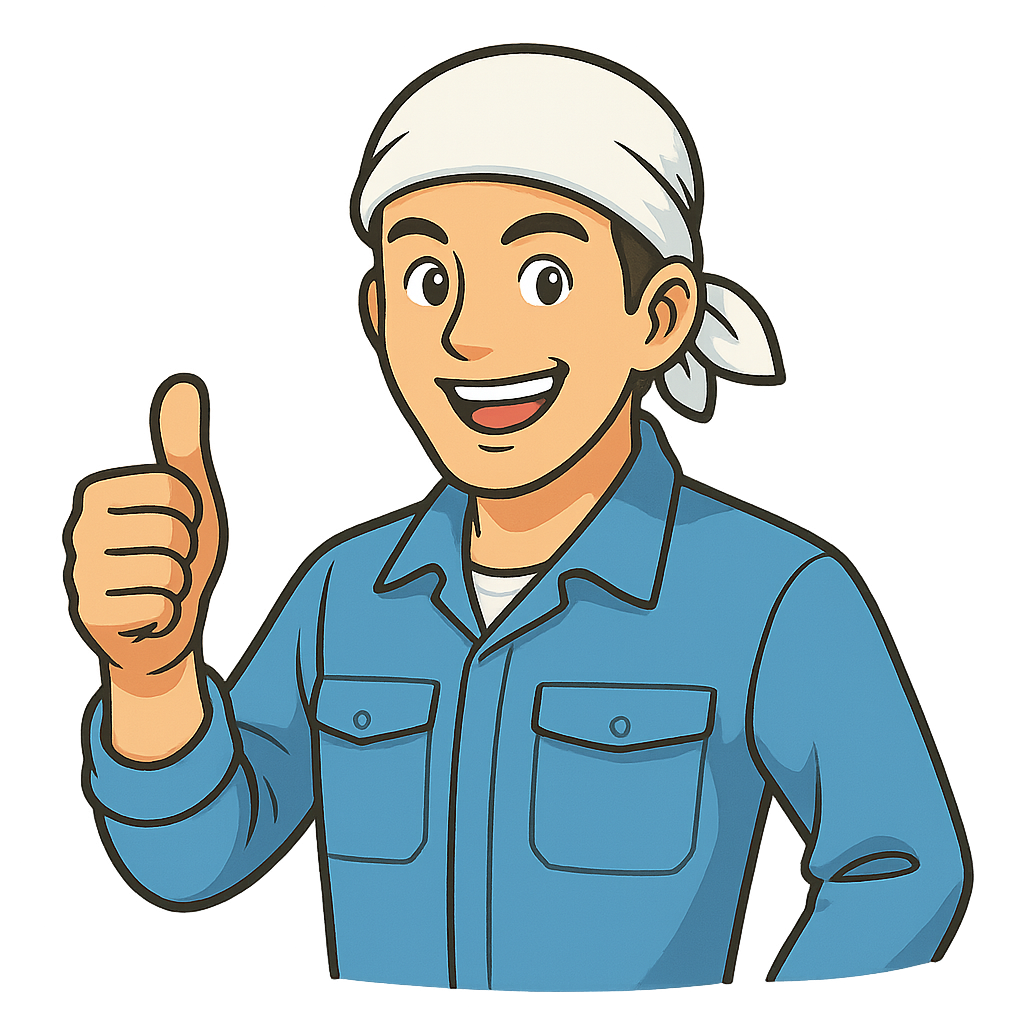
機械研磨は「再現性」が最大の強みです。一度条件を設定すれば、同じ品質の製品を何百個でも作れます。ただし、機械にも得意・不得意があるので、製品形状に合わせた機種選定が重要です。
機械研磨は、バレル研磨やバフ研磨、ベルト研磨など様々な種類があります。形状や素材、求められる仕上がりによって最適な方法が異なります。近年はCNC制御の研磨機も増えており、複雑な形状にも対応できるようになってきています。
2. コスト比較:初期投資から長期運用まで
研磨方法を選ぶ際、コストは最も重要な判断材料の一つです。ここでは初期投資から運用コストまで、総合的に比較していきます。
初期投資コスト
手作業研磨の初期投資
- 工具・研磨材:10万円〜30万円程度
- 作業スペース設備:10万円〜50万円程度
- 集塵設備:5万円〜20万円程度
- 合計:25万円〜100万円程度
機械研磨の初期投資
- 研磨機本体:50万円〜500万円程度
- 設置工事・周辺設備:20万円〜100万円程度
- 専用研磨材・消耗品:10万円〜30万円程度
- 合計:80万円〜630万円程度
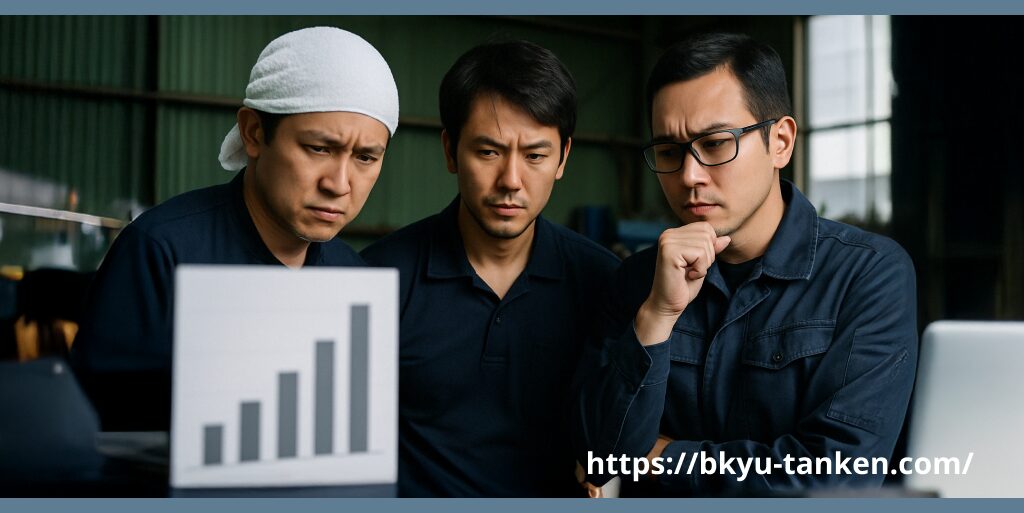
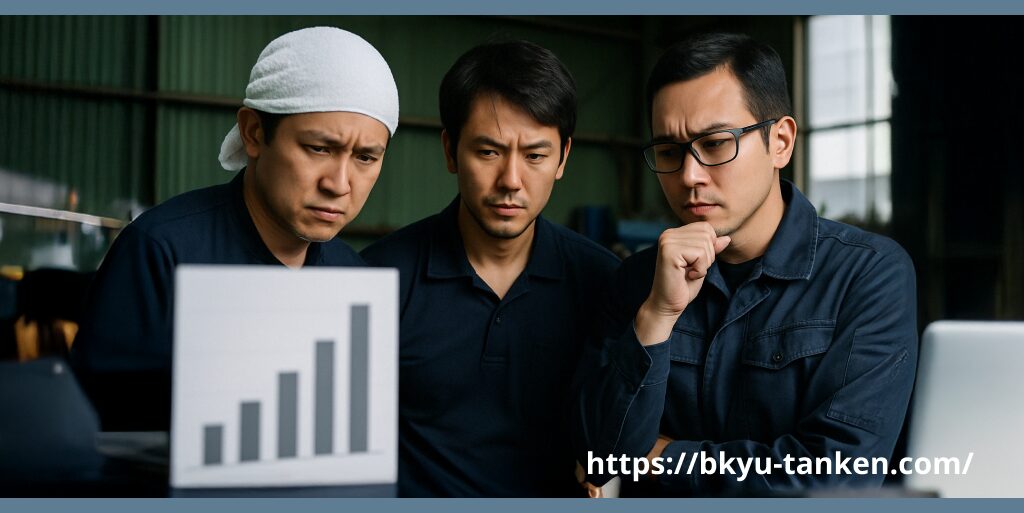
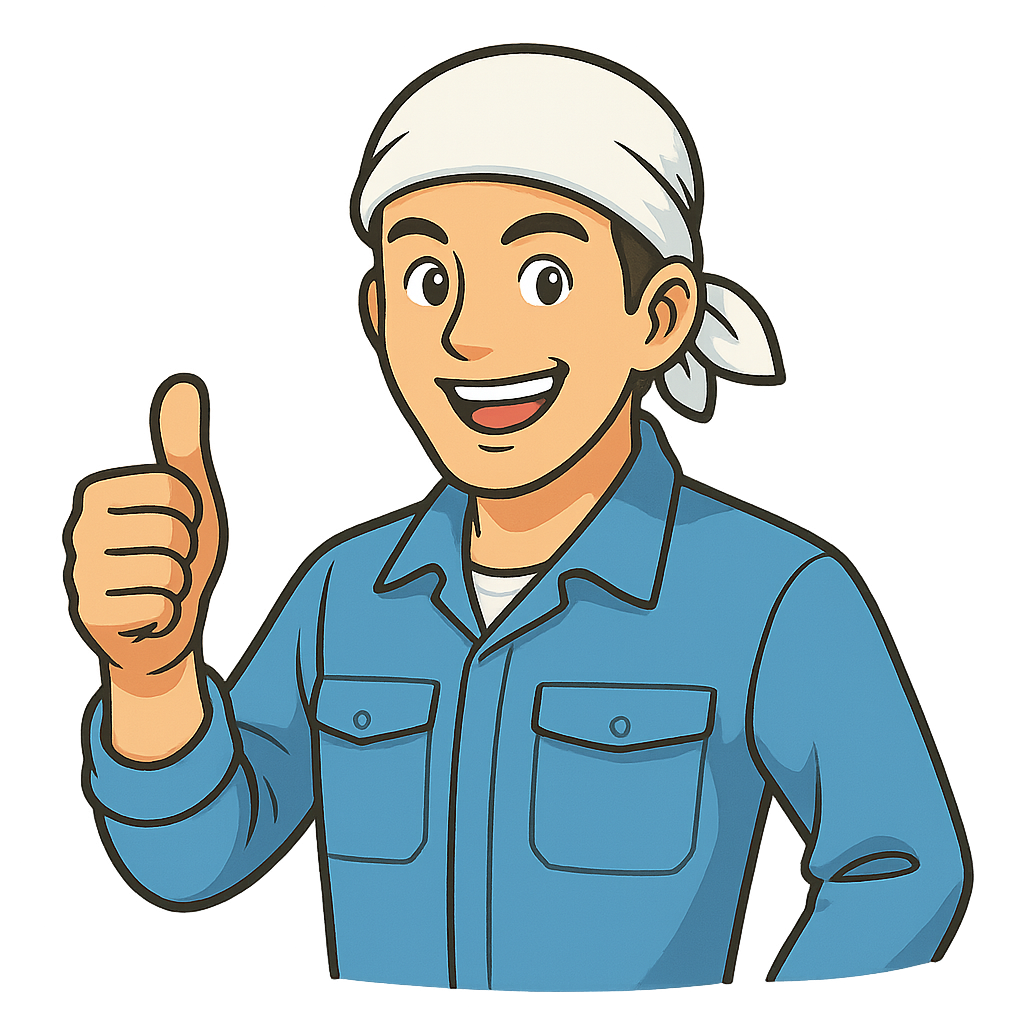
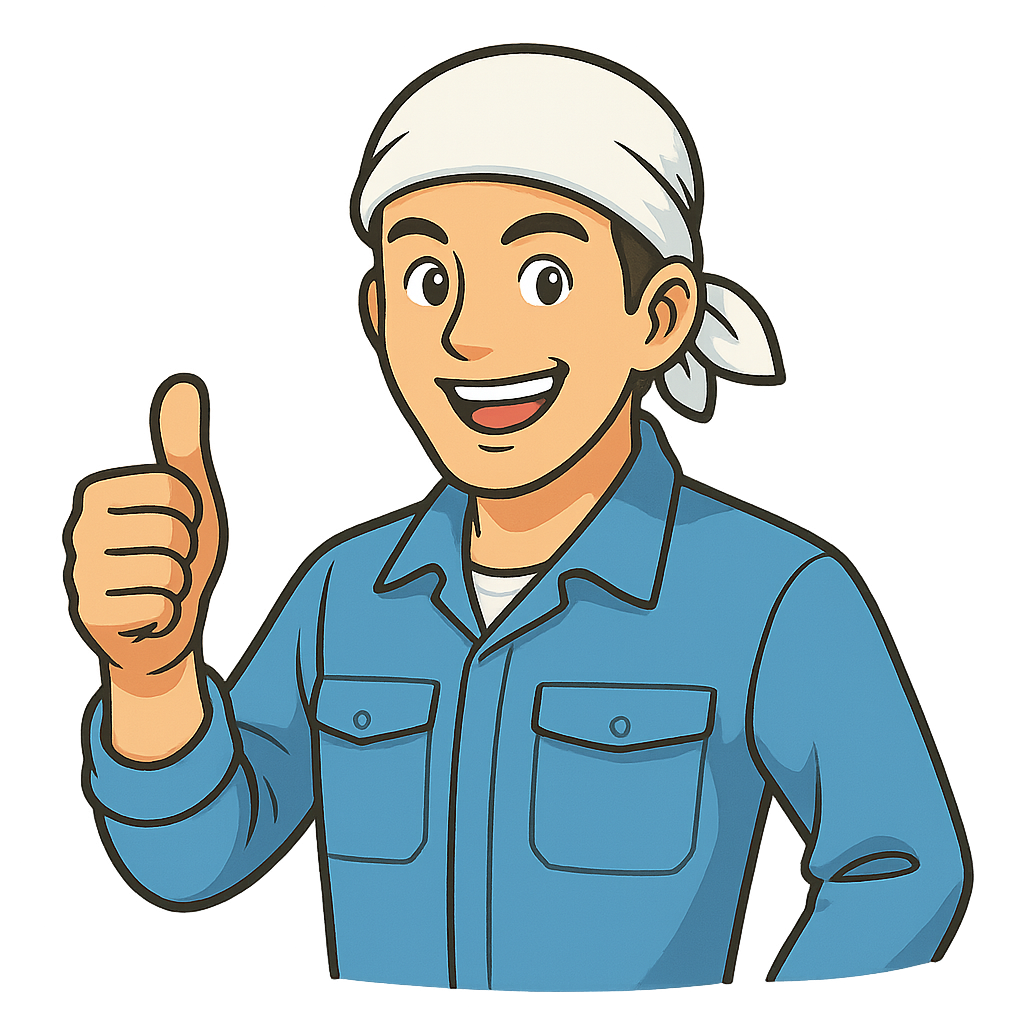
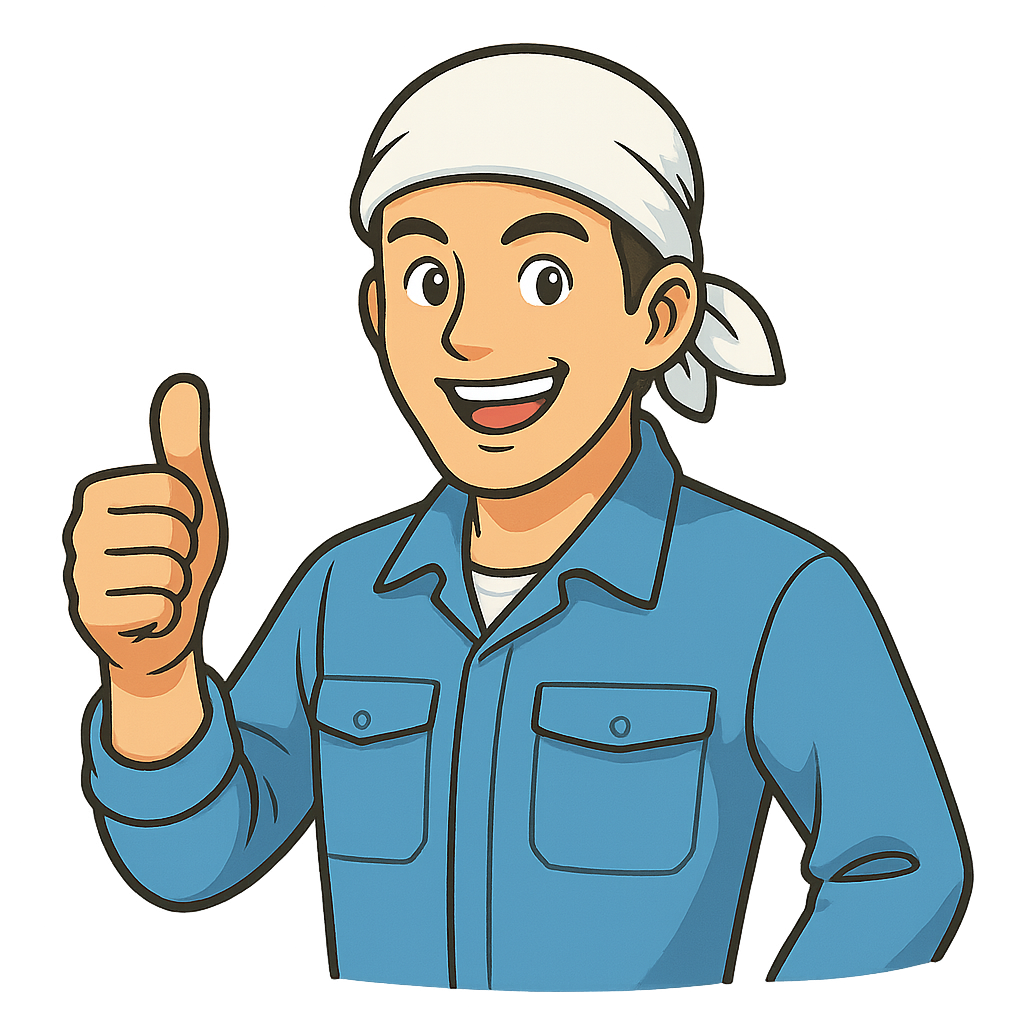
初期投資だけを見ると手作業研磨が圧倒的に安く見えますが、長期的な視点も必要です。月産数量や製品寿命を考慮して判断しましょう。特に年間1000個以上の同一製品を扱う場合は、機械化のメリットが大きくなります。
運用コスト
手作業研磨の運用コスト(月額)
- 人件費:30万円〜45万円/人
- 研磨材消耗品:3万円〜10万円
- 電気代・その他:1万円〜3万円
- 月間合計:34万円〜58万円/人
機械研磨の運用コスト(月額)
- 人件費(オペレーター):25万円〜40万円/人
- 研磨材・消耗品:5万円〜15万円
- 電気代・メンテナンス:3万円〜10万円
- 月間合計:33万円〜65万円
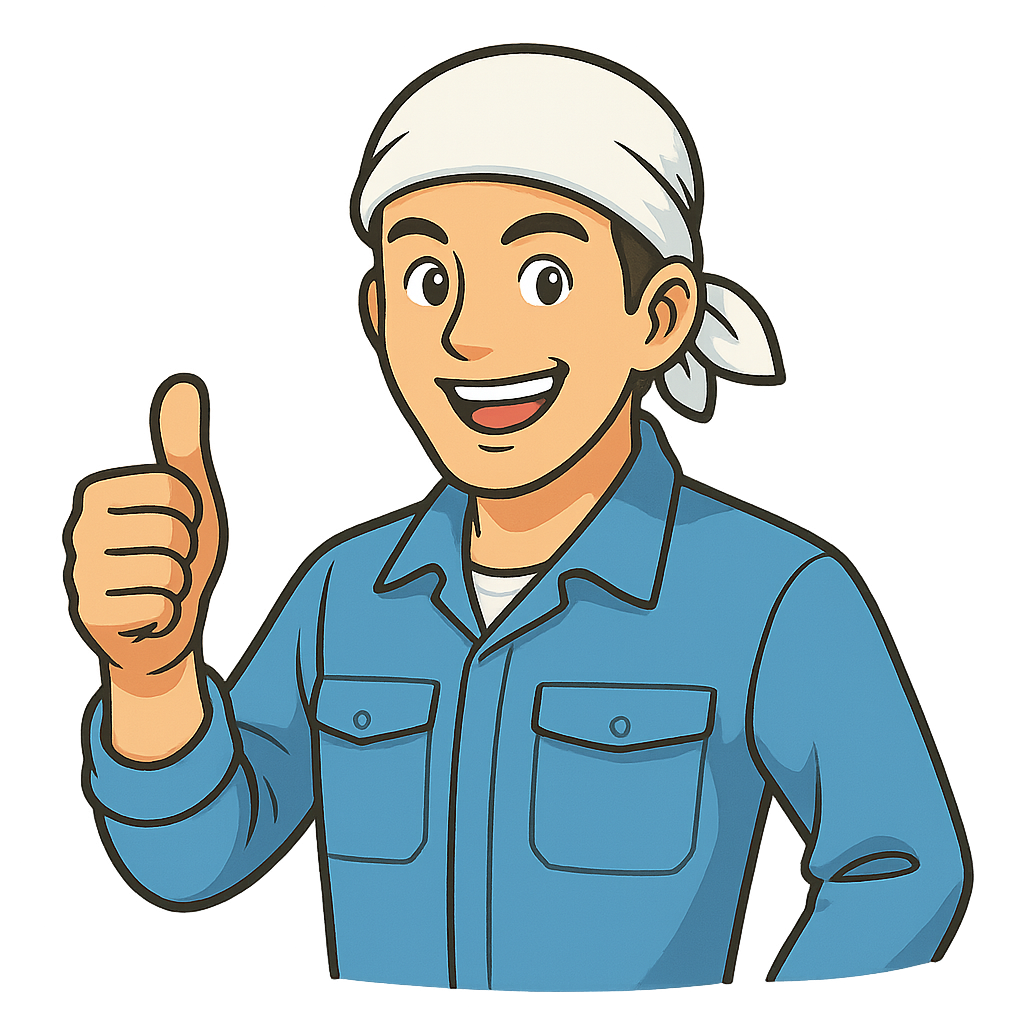
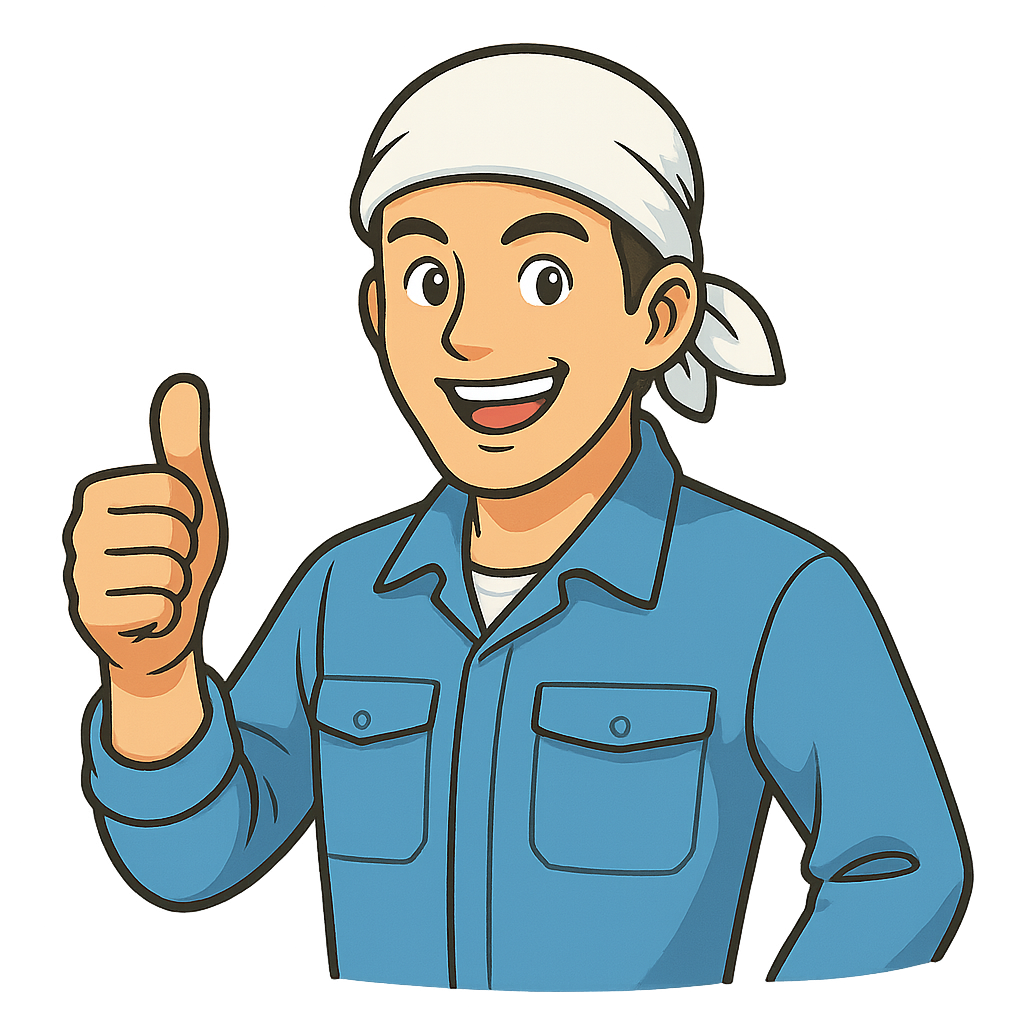
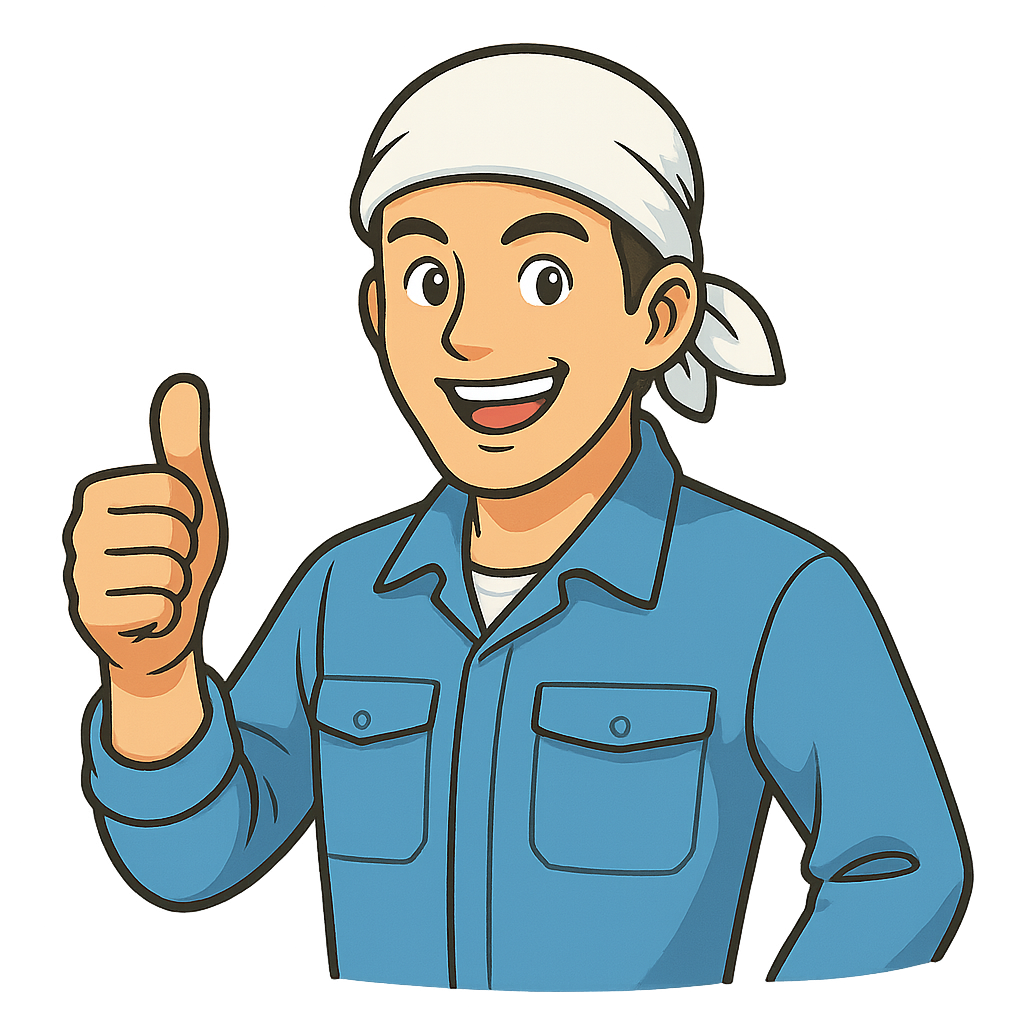
運用コストの最大の違いは「生産量に対するスケーラビリティ」です。手作業は生産量に比例して人員が必要になりますが、機械研磨は一定数量を超えると急激にコストパフォーマンスが向上します。
長期的な総コスト比較
製品数量別に5年間の総コスト(初期投資+運用コスト)を試算してみましょう。
少量生産(月産50個)の場合
- 手作業研磨:約2,100万円(初期100万円+運用2,000万円)
- 機械研磨:約2,500万円(初期500万円+運用2,000万円)
- 結果:手作業研磨が約400万円お得
中量生産(月産300個)の場合
- 手作業研磨:約3,900万円(初期100万円+運用3,800万円)
- 機械研磨:約3,500万円(初期500万円+運用3,000万円)
- 結果:機械研磨が約400万円お得
大量生産(月産1000個以上)の場合
- 手作業研磨:約6,100万円(初期100万円+運用6,000万円)
- 機械研磨:約4,500万円(初期500万円+運用4,000万円)
- 結果:機械研磨が約1,600万円お得
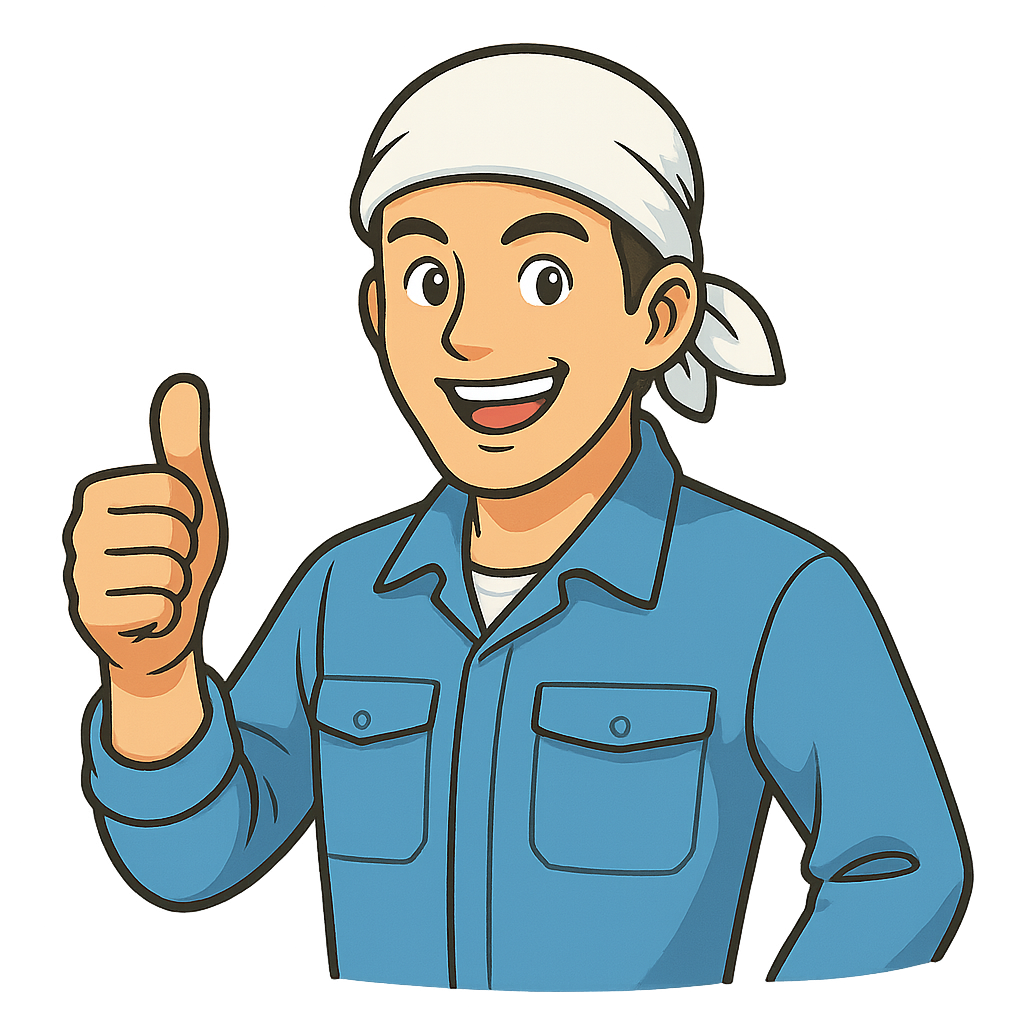
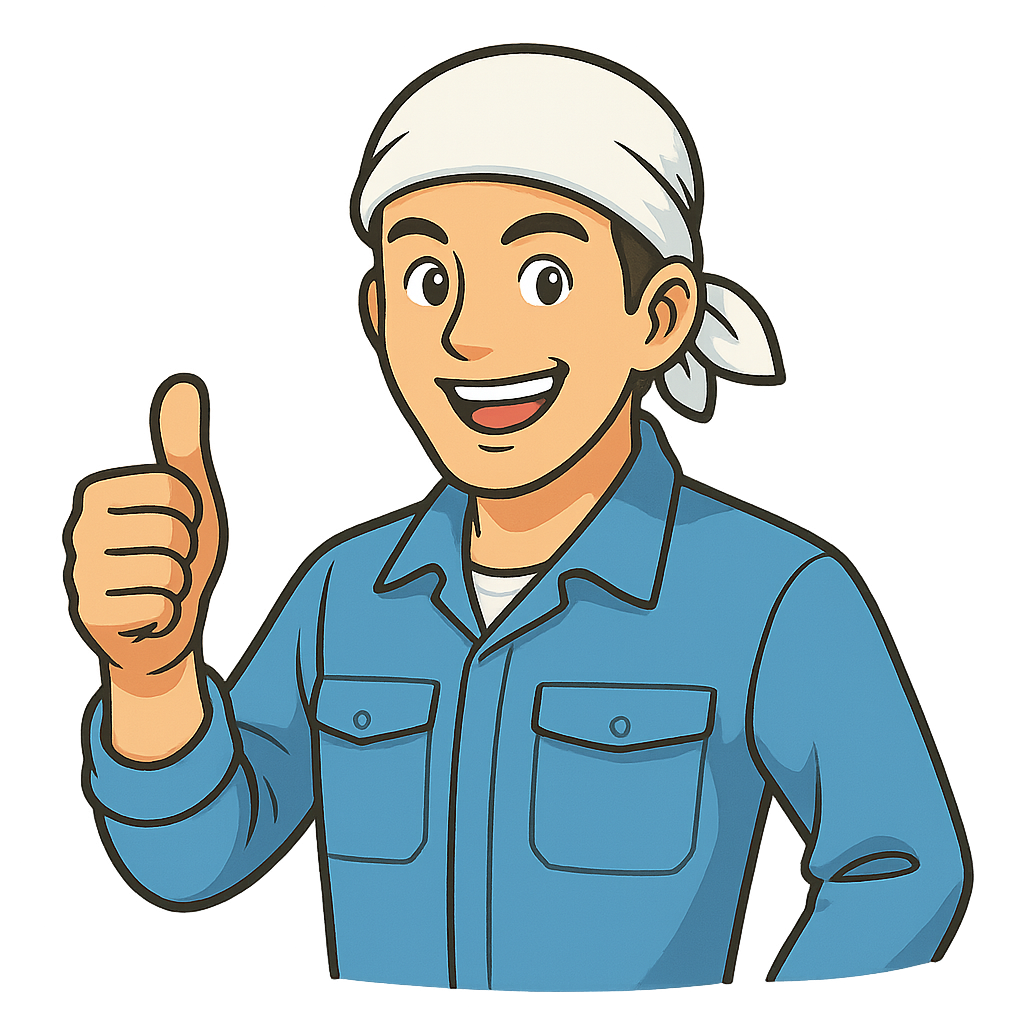
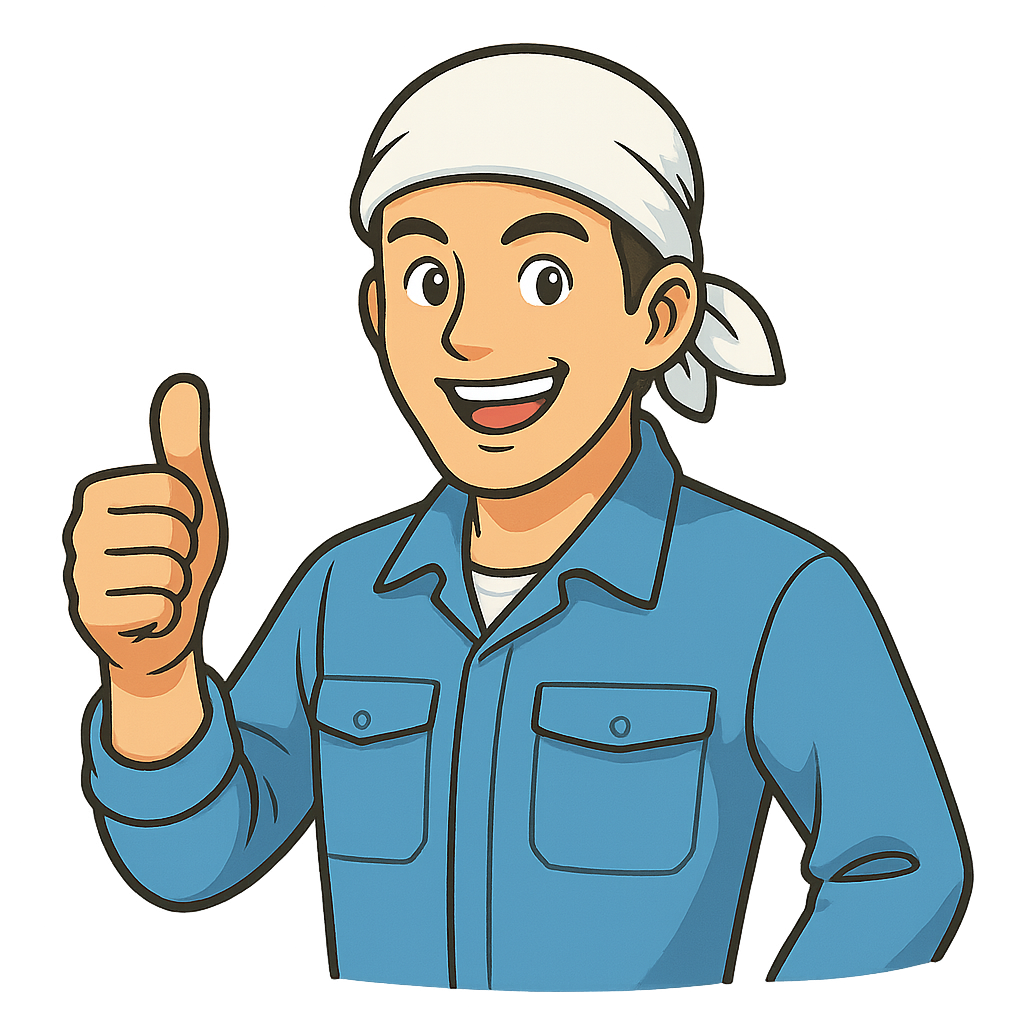
この試算は一般的な傾向を示したものです。実際には製品の複雑さや求められる仕上げレベルによって大きく変わります。特に複雑な形状や高度な仕上げが必要な場合は、手作業のほうが総コストで優位になるケースもあります。
3. 品質比較:仕上がりの差と適した用途
コストと同様に重要なのが「品質」です。同じ研磨でも、手法によって仕上がりの特性が異なります。
表面粗さと均一性
手作業研磨
- 熟練職人なら非常に細かい表面粗さ(Ra0.05μm以下)も可能
- 部位や角度によって微妙な差が生じることがある
- 職人の技量によって品質にばらつきがある可能性
機械研磨
- 安定した表面粗さ(一般的にRa0.1〜0.5μm程度)
- 均一な仕上がりが特徴
- 複雑形状の細部では限界がある場合も
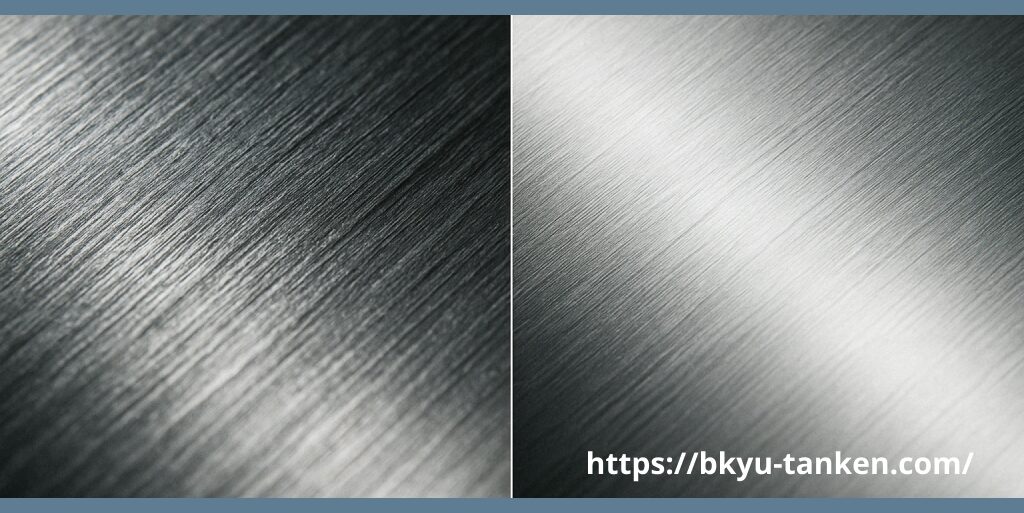
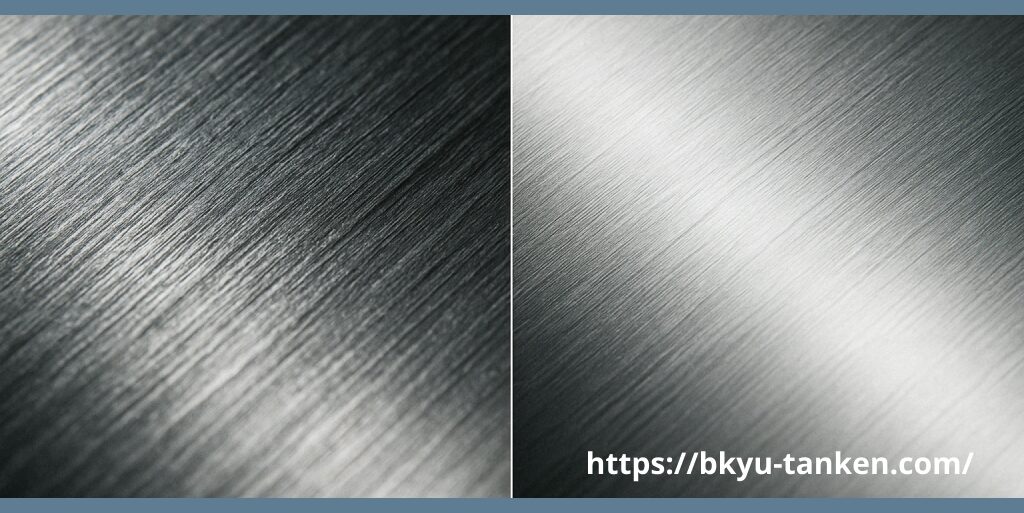
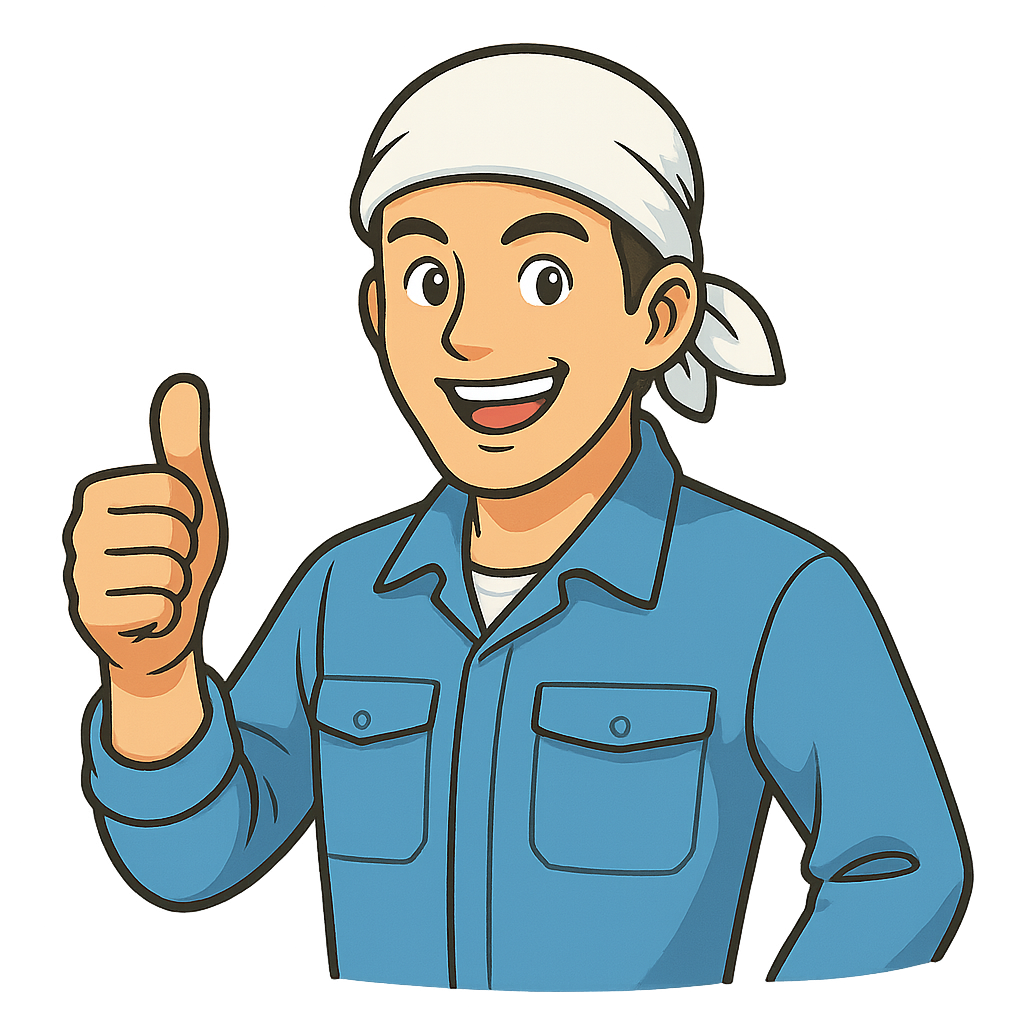
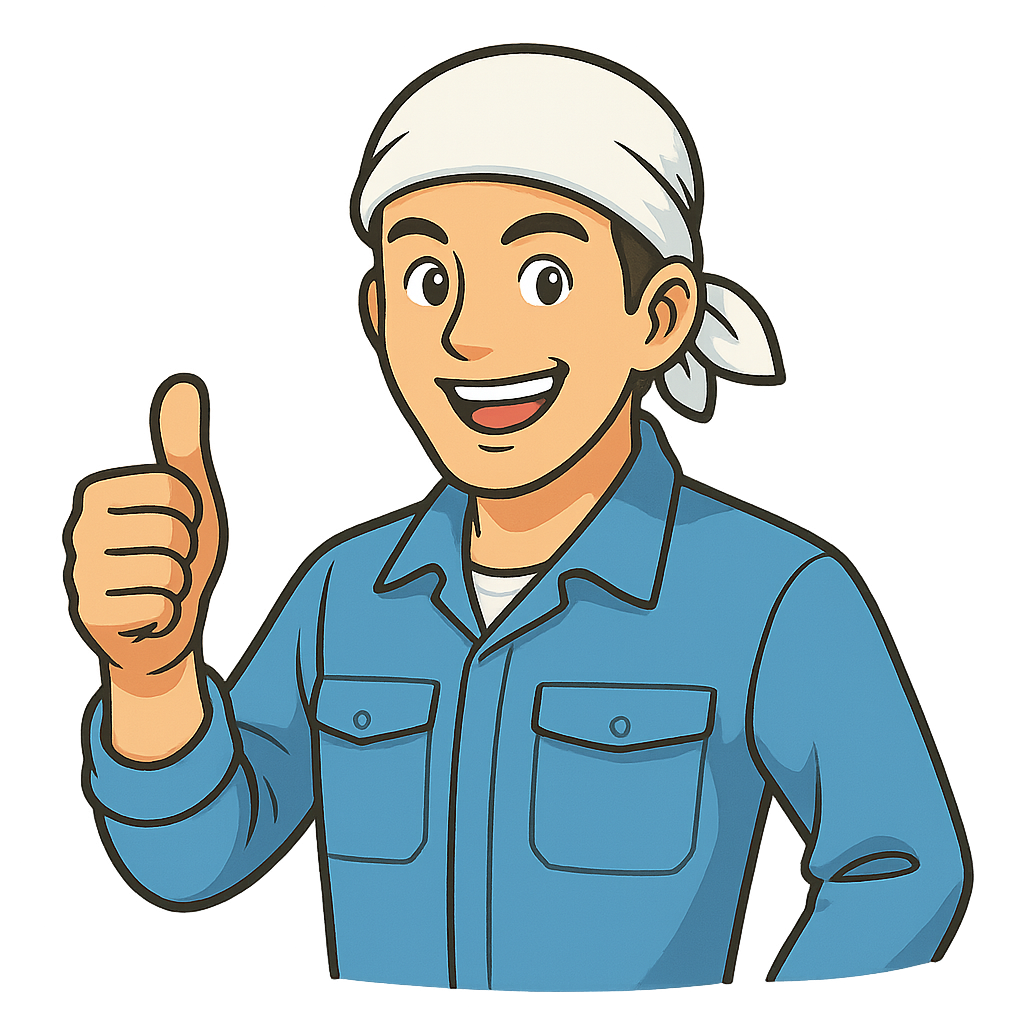
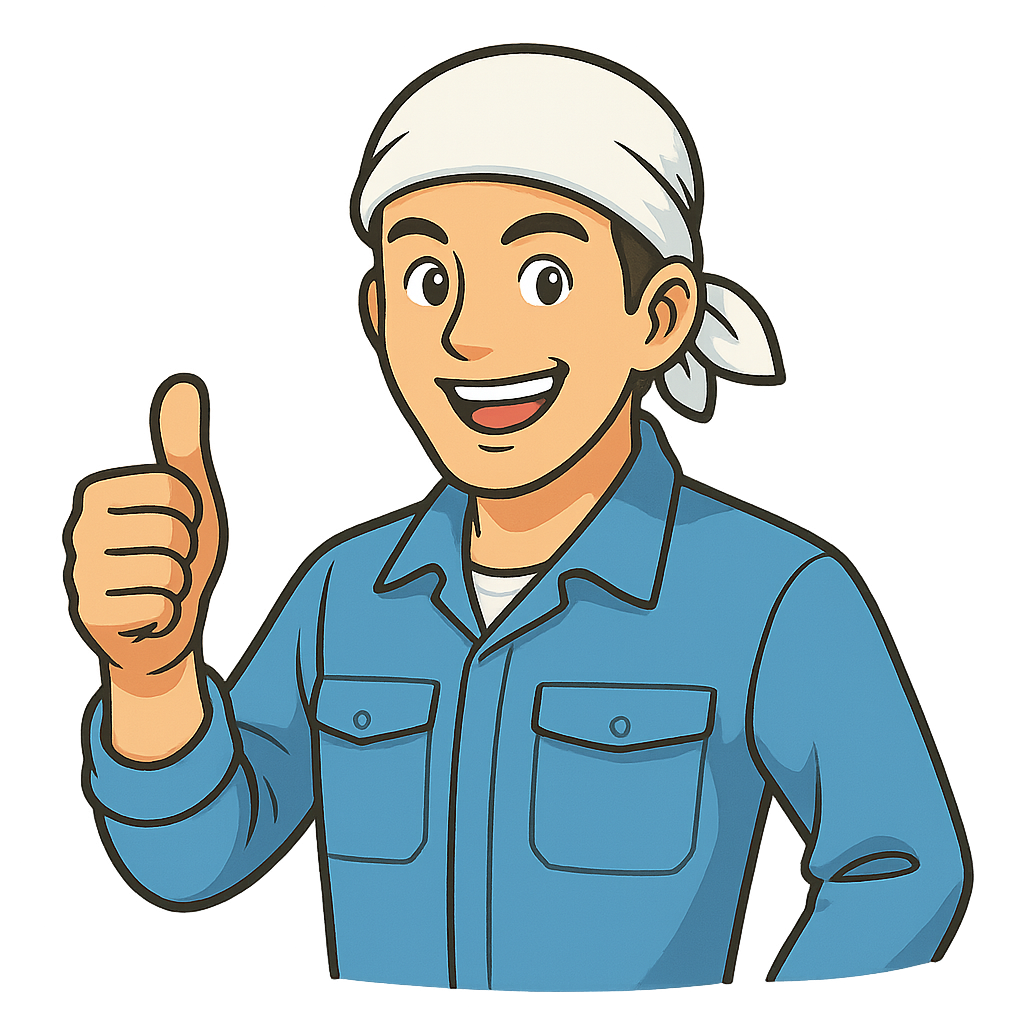
表面粗さの数値だけでなく、研磨の「方向性」も重要です。手作業では意図的に方向性を付けることもできますが、機械研磨では装置の特性に依存します。美観を重視する場合は特に注意が必要です。
複雑形状への対応
手作業研磨
- 複雑な形状や入り組んだ部分にも対応可能
- 部分的に異なる仕上げを施すことができる
- 形状に合わせて工具や力加減を調整できる
機械研磨
- 単純形状や平面が得意
- 入り組んだ部分は苦手な場合が多い
- 5軸制御などの高度な機械でも対応しきれない細部がある
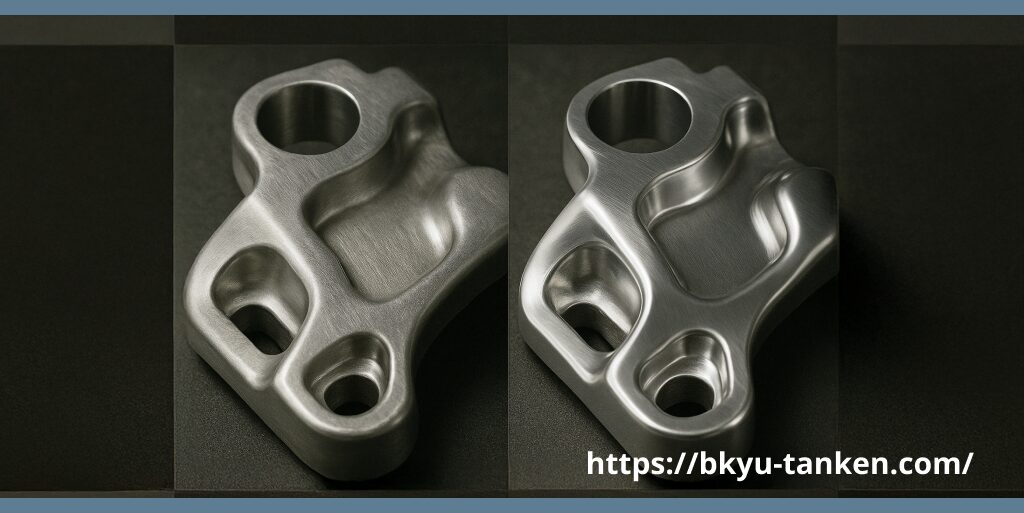
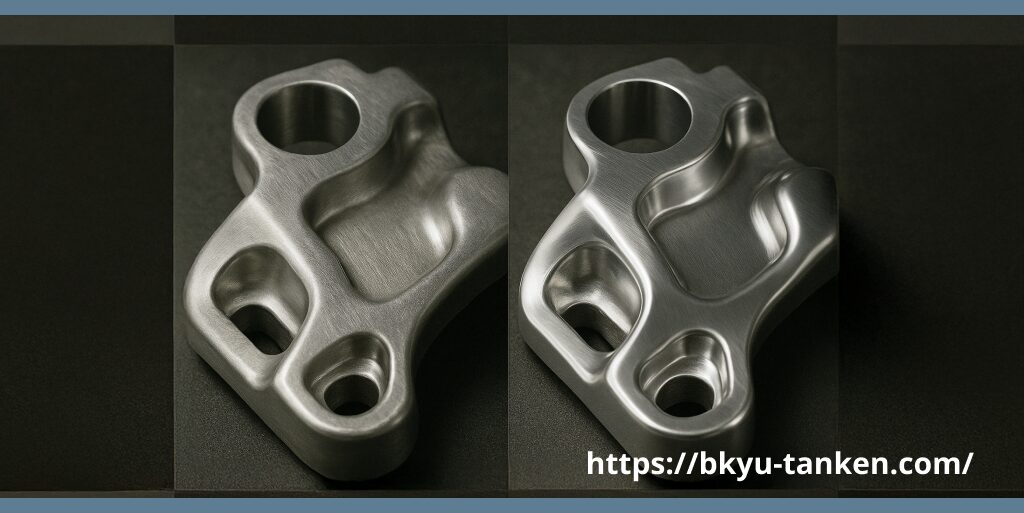
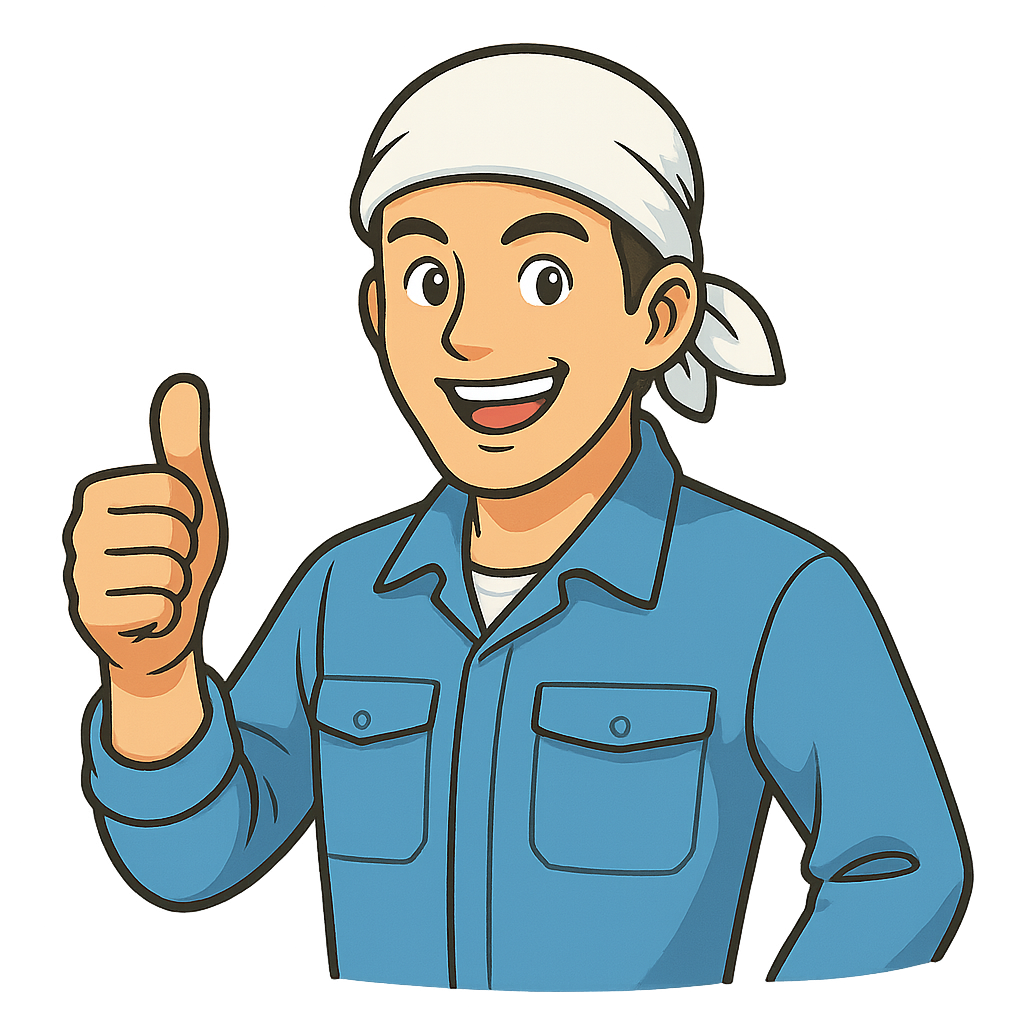
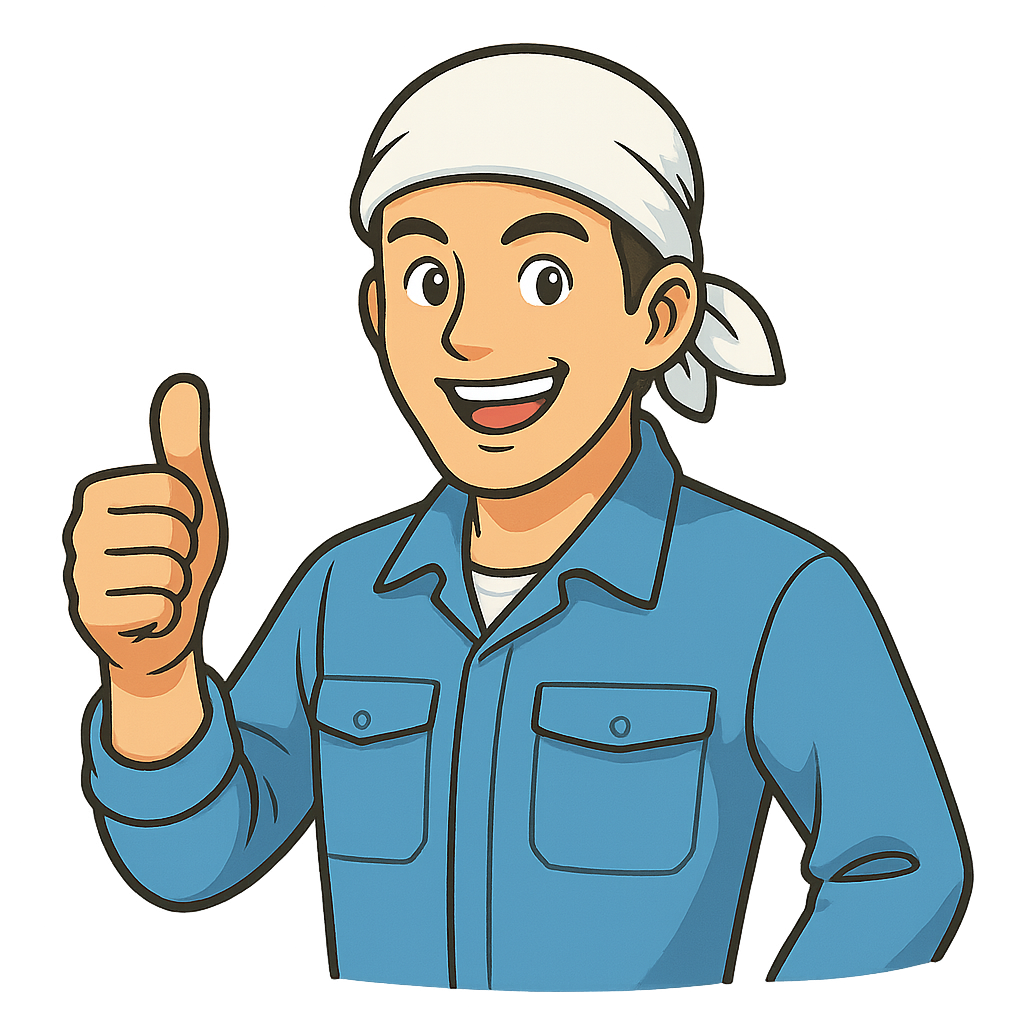
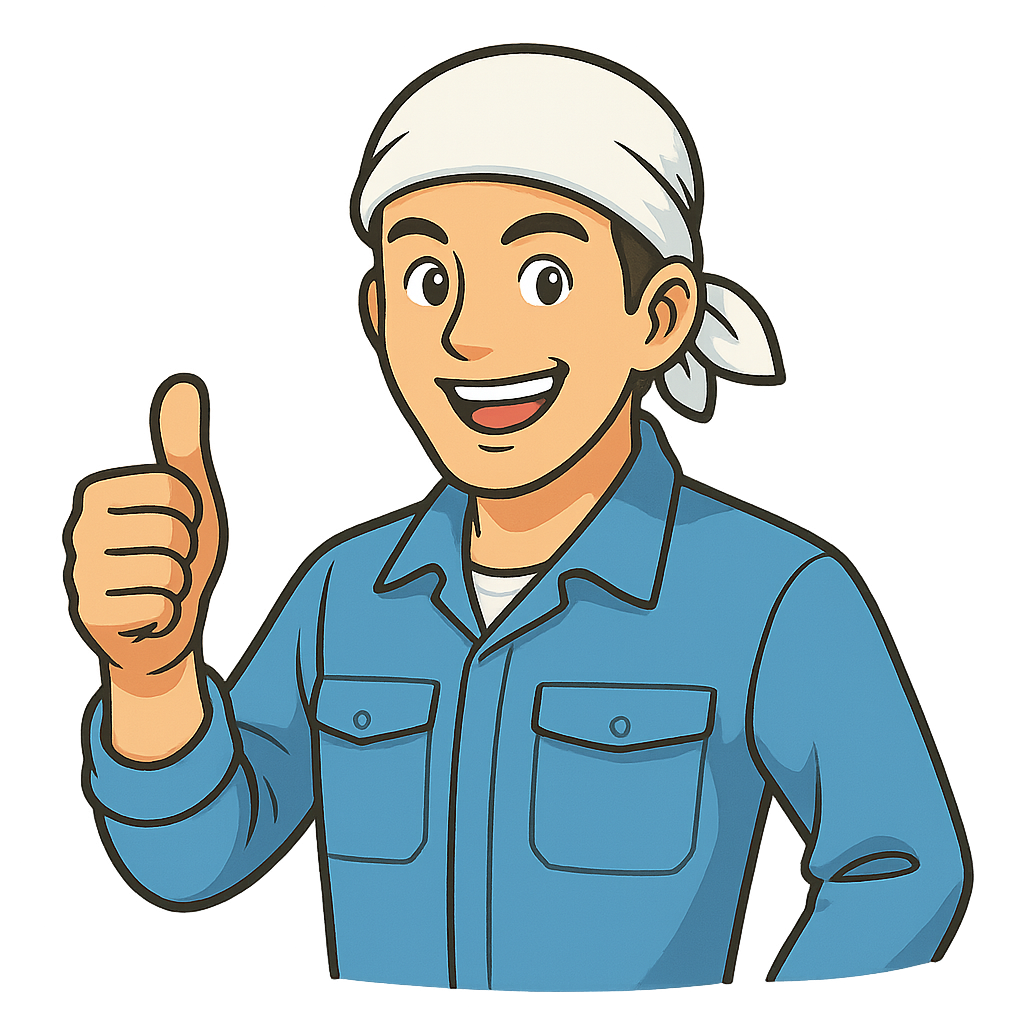
複雑形状の研磨では、「手作業+機械」の組み合わせが効果的なケースも多いです。機械で全体の粗研磨を行い、細部や仕上げは手作業で対応するハイブリッド方式を検討してみてください。
特殊仕上げへの対応
手作業研磨
- 鏡面仕上げから梨地仕上げまで幅広く対応
- 部分的に異なる仕上げの組み合わせも可能
- 芸術的な表現やグラデーションも実現可能
機械研磨
- 均一な仕上げが得意
- 同一条件での再現性が高い
- 特殊な仕上げには専用機械が必要になることも
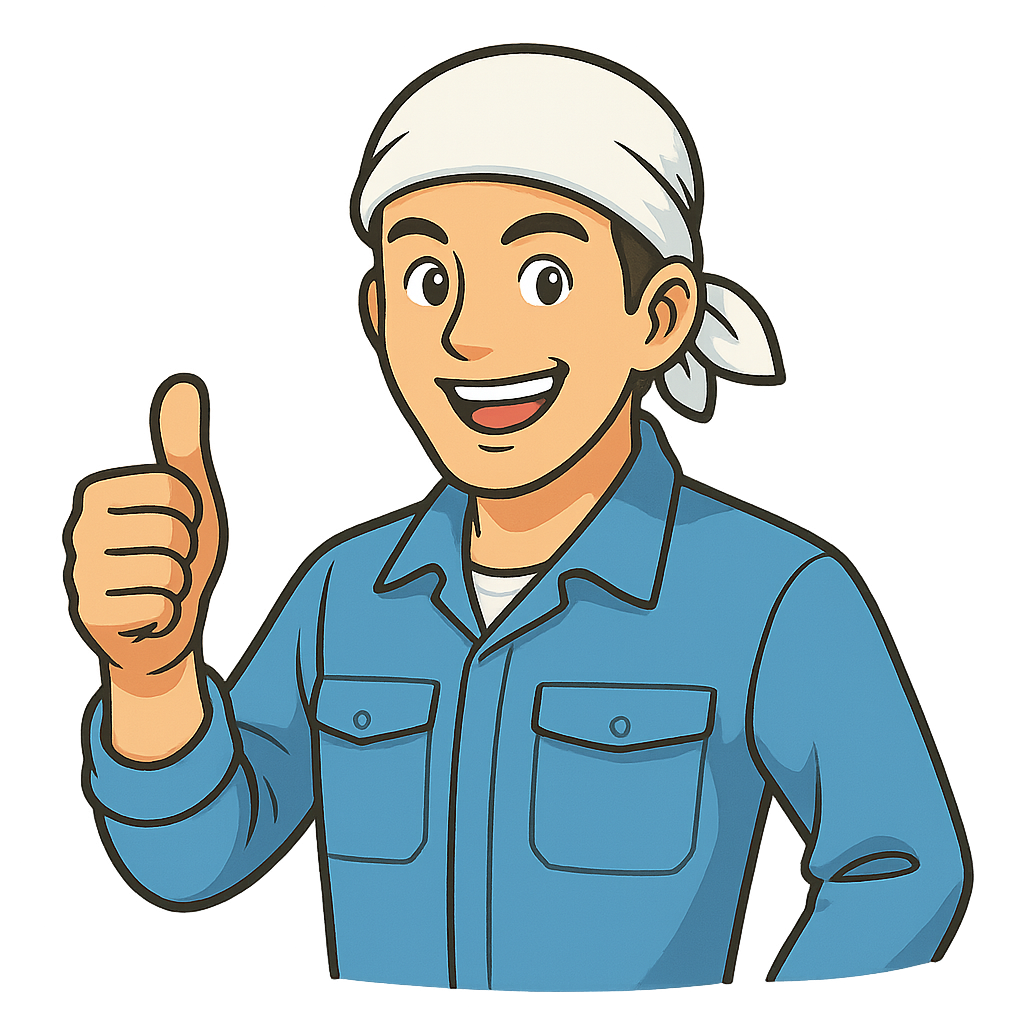
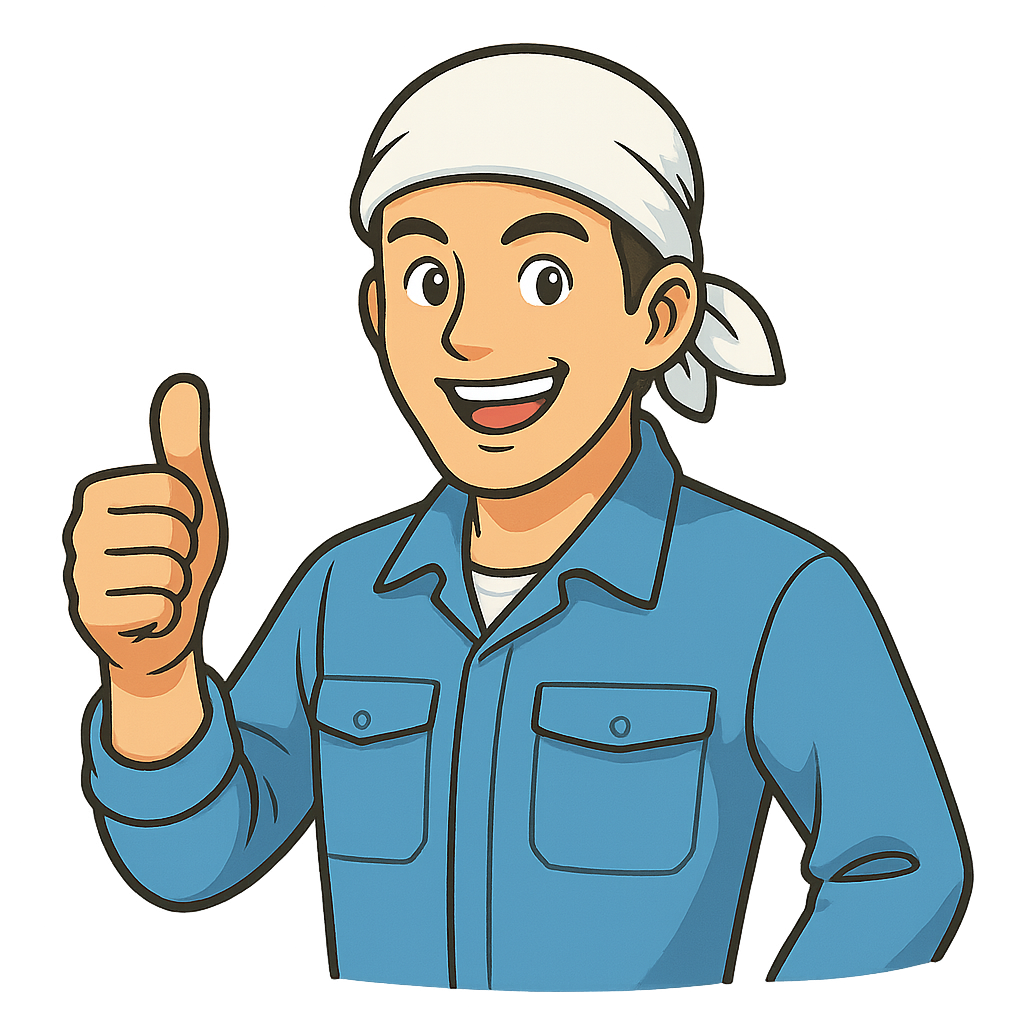
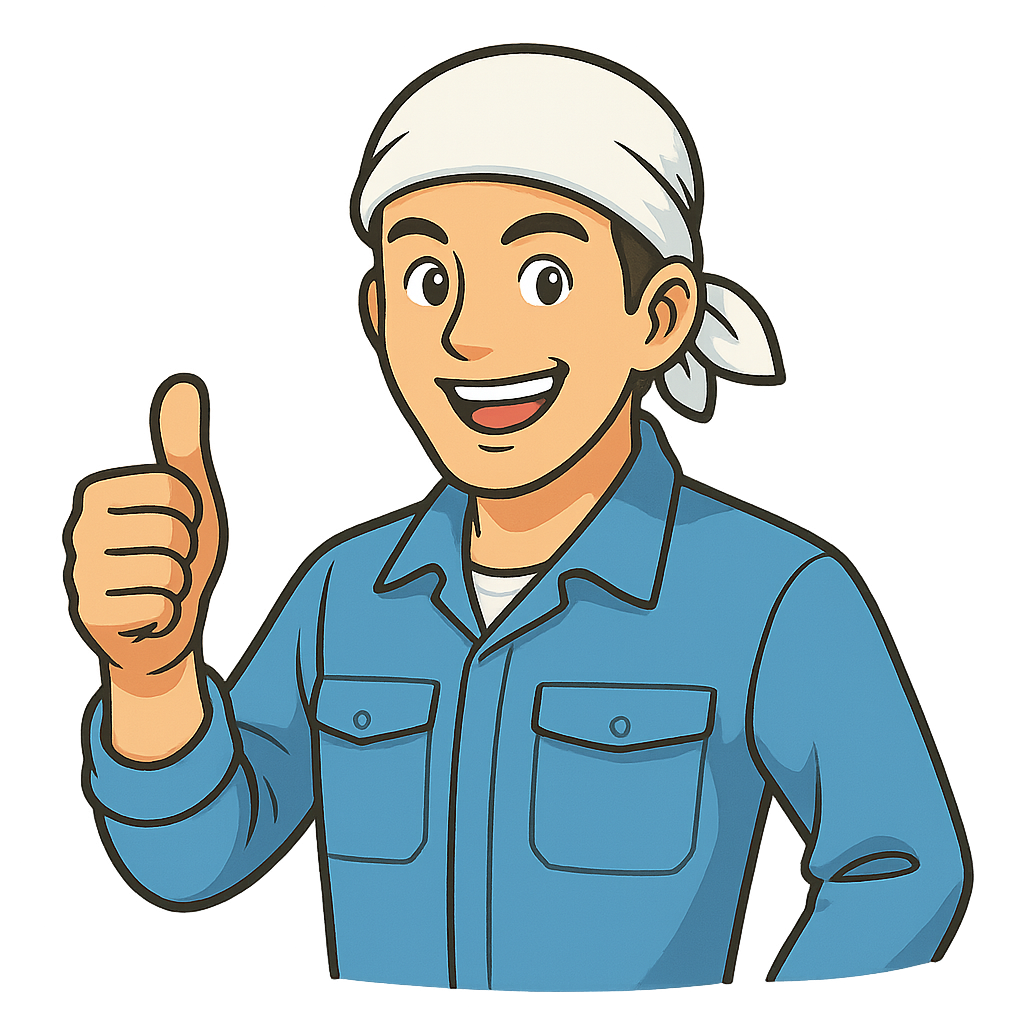
高級時計や装飾品などの特殊仕上げでは、いまだに手作業が主流です。一方で、工業製品の一般的な研磨なら機械研磨で十分な品質が得られます。何を「品質」と定義するかで選択が変わってきます。
4. 製品別・業界別の最適研磨法
業界や製品によって求められる研磨の質や条件は大きく異なります。ここでは代表的な業界別に最適な研磨方法を解説します。
精密機器・医療機器業界
精密機器や医療機器では、高い表面品質と寸法精度が要求されます。
手作業研磨に適した製品例
- 医療用インプラント
- 特殊形状の精密部品
- 少量生産の試作品
機械研磨に適した製品例
- 内視鏡部品
- 医療用ピンセット
- 精密ネジ・ボルト類
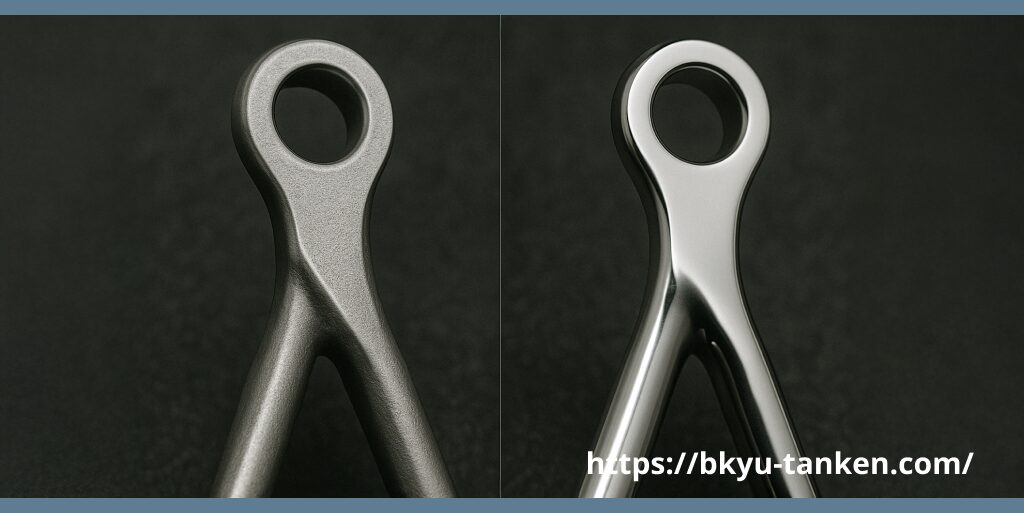
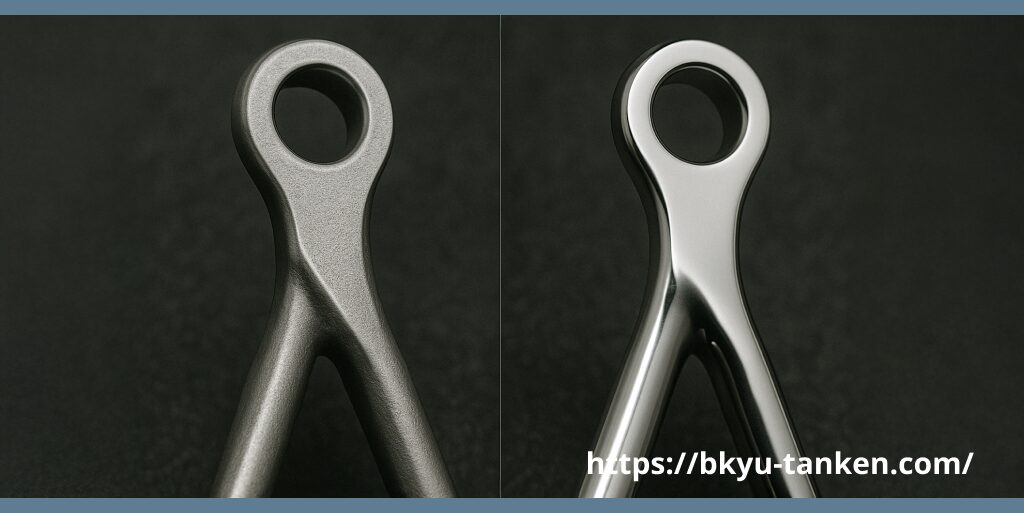
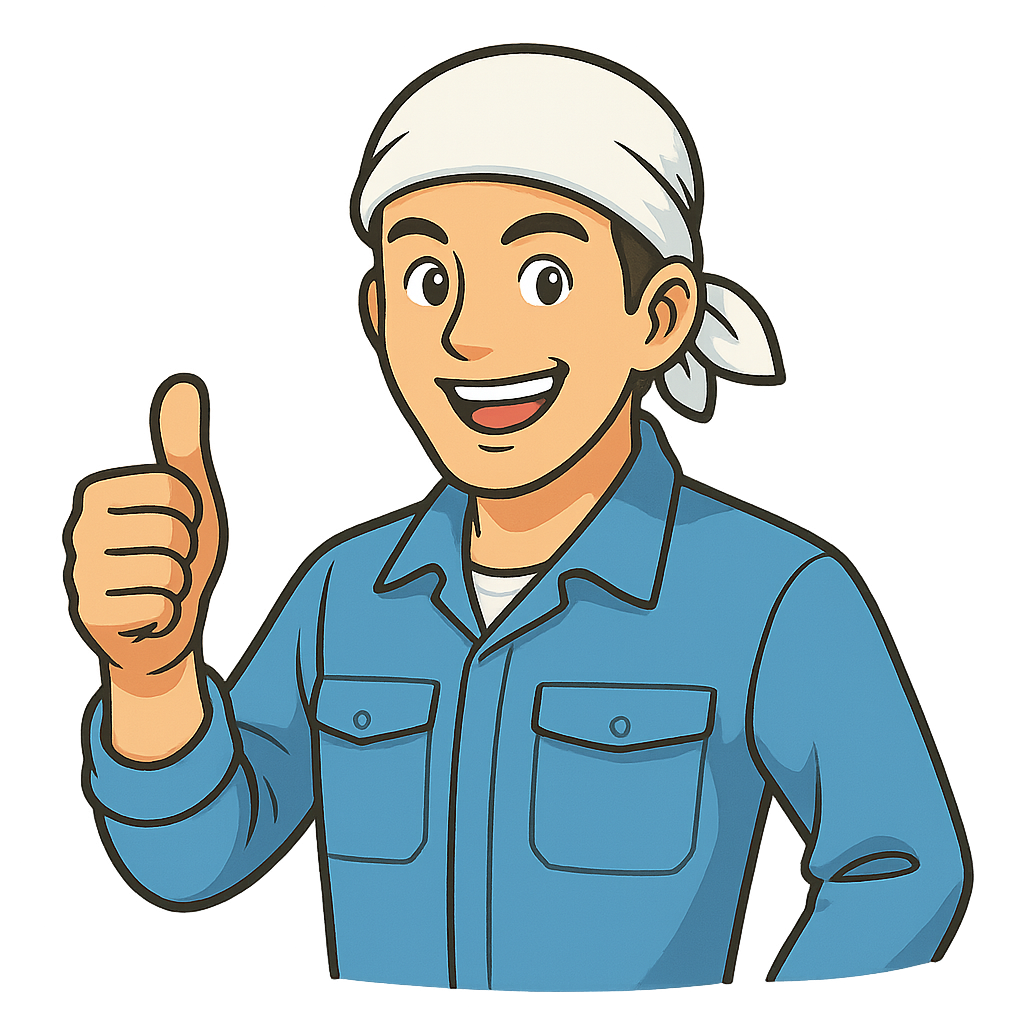
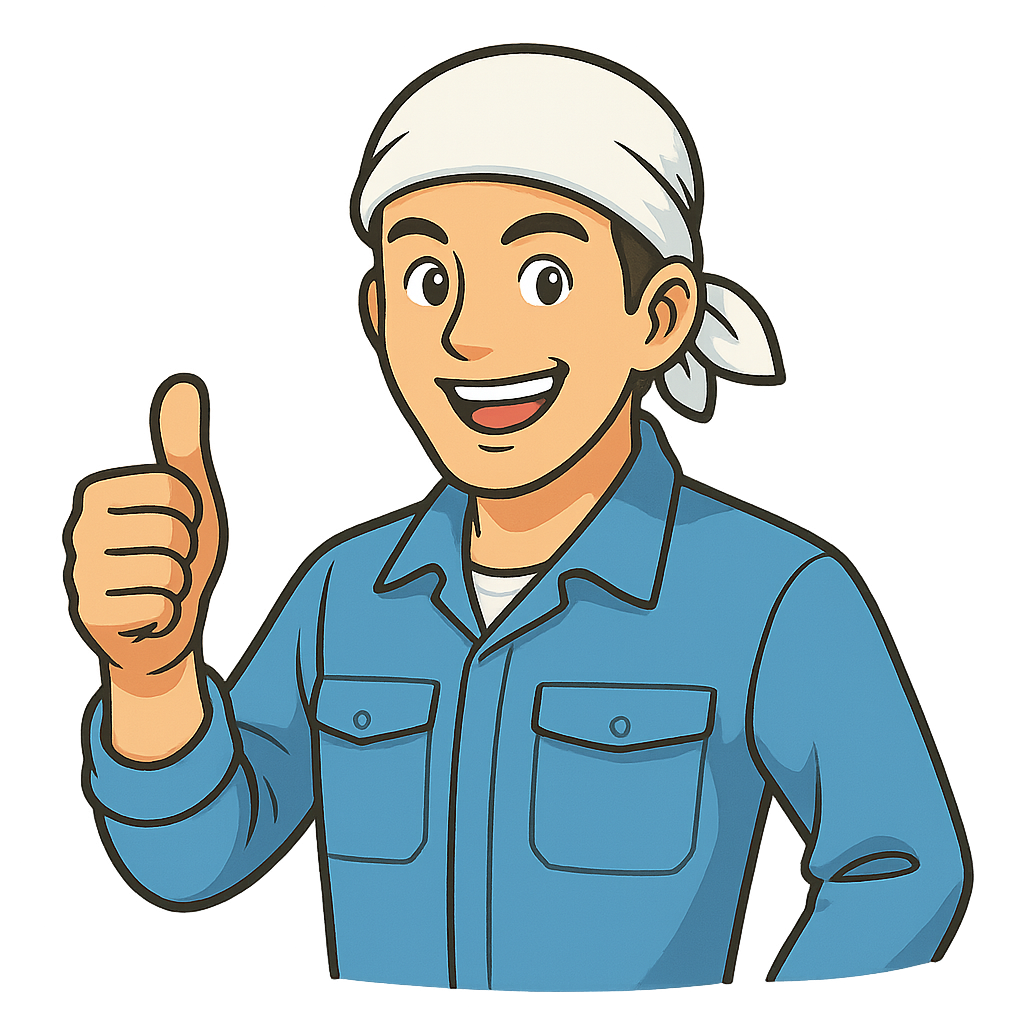
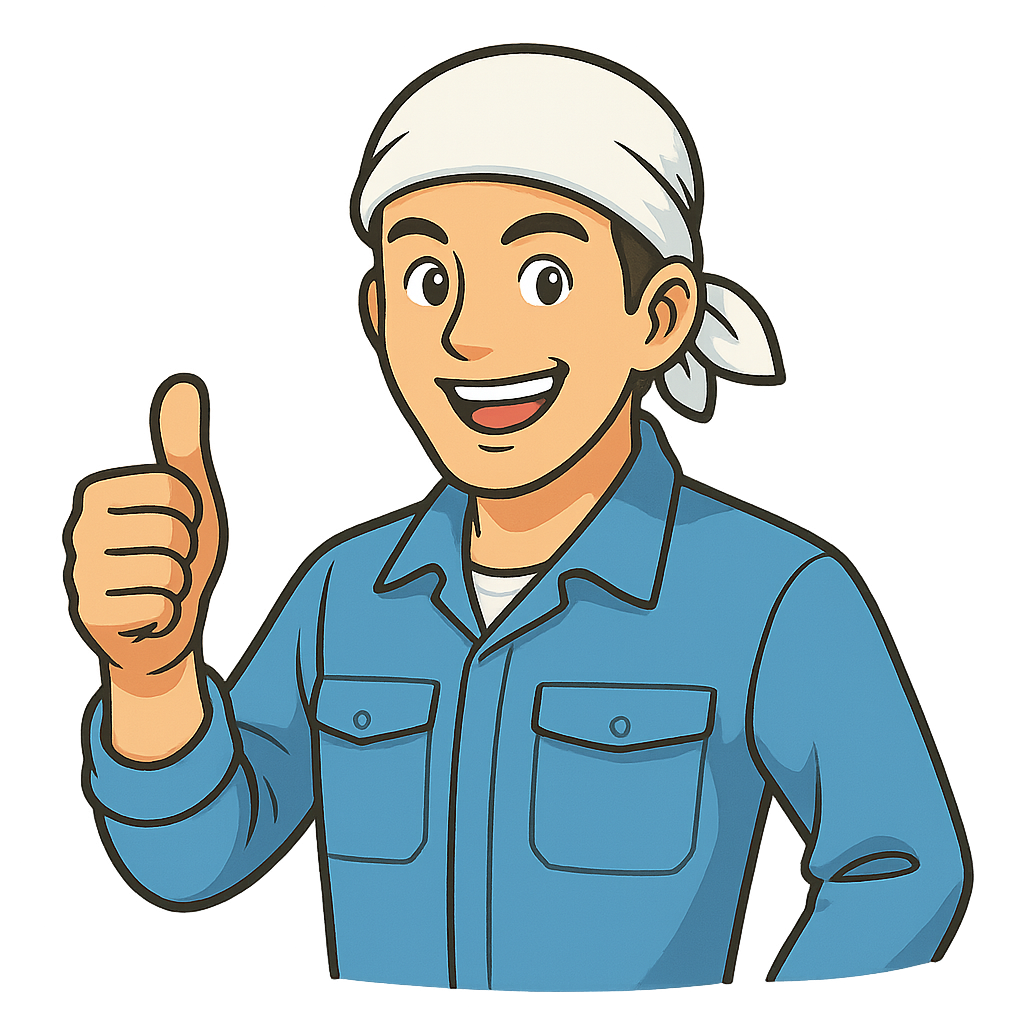
医療機器では「清浄度」も重要な要素です。手作業の場合は人由来の汚染リスクがあるため、クリーンルーム環境での作業が必要になることも。機械研磨のほうが衛生面では有利な場合が多いです。
自動車・航空機部品業界
自動車や航空機業界では、大量生産と高い信頼性が求められます。
手作業研磨に適した製品例
- 高級車の特注部品
- 試作エンジン部品
- モックアップモデル
機械研磨に適した製品例
- エンジンバルブ
- シリンダー内面
- ターボチャージャー部品
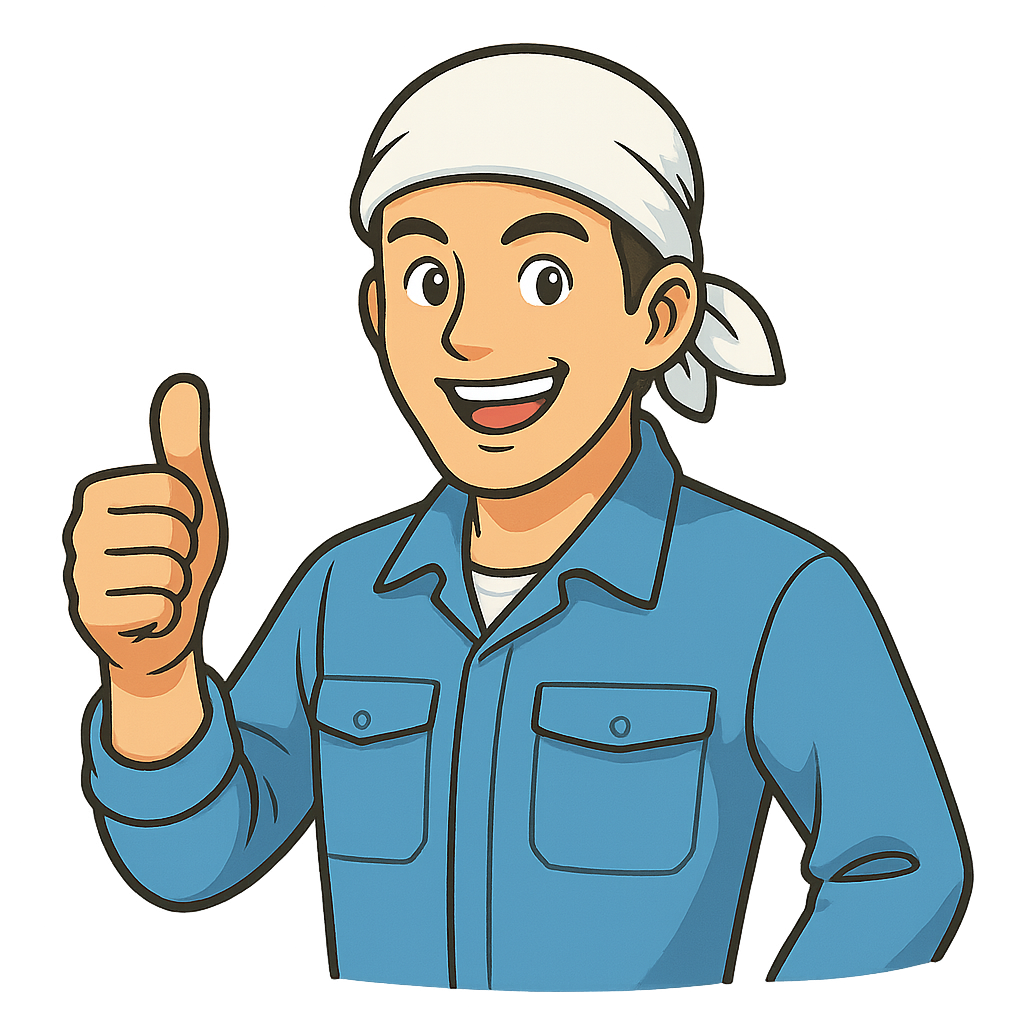
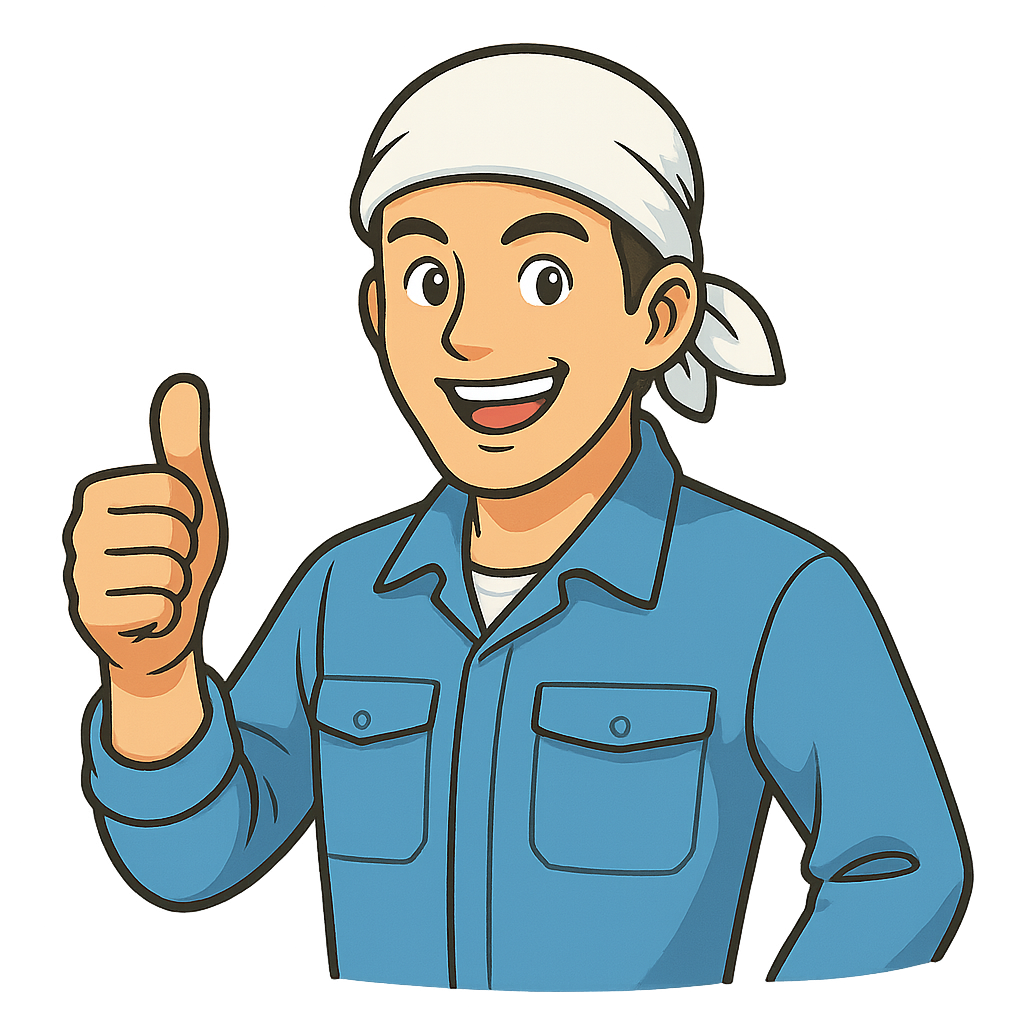
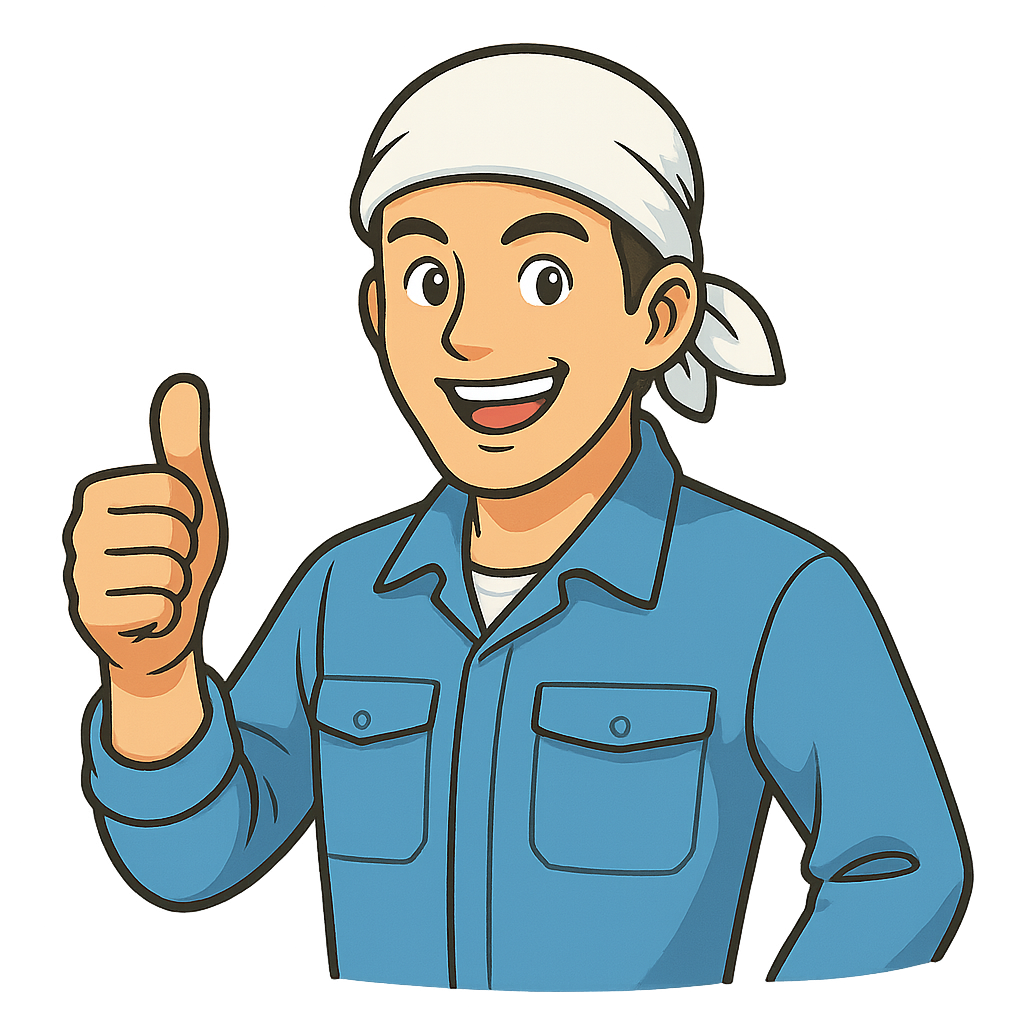
自動車部品では「量産性」と「コスト」が最重要視されるため、ほとんどが機械研磨です。ただし、F1やスーパーカーなどの特殊車両では今でも手作業研磨が用いられています。耐久性や性能に直結する部分だからこそ、職人の感覚が生きる領域があるのです。
装飾品・宝飾品業界
装飾品や宝飾品では、美観と芸術性が最も重視されます。
手作業研磨に適した製品例
- 高級時計ケース
- アクセサリー
- 特殊金属アート作品
機械研磨に適した製品例
- 量産アクセサリーパーツ
- チェーン・リング等の基本形状品
- 装飾用金具
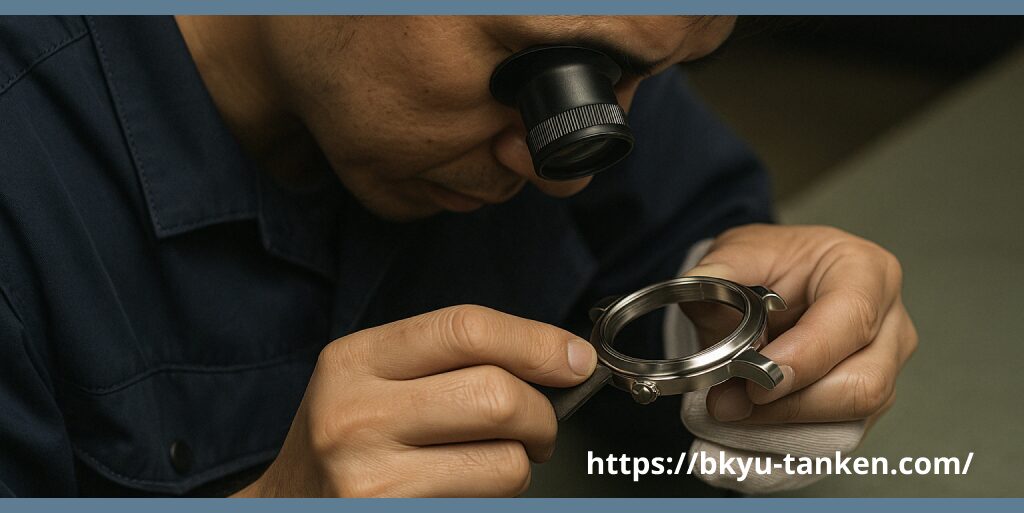
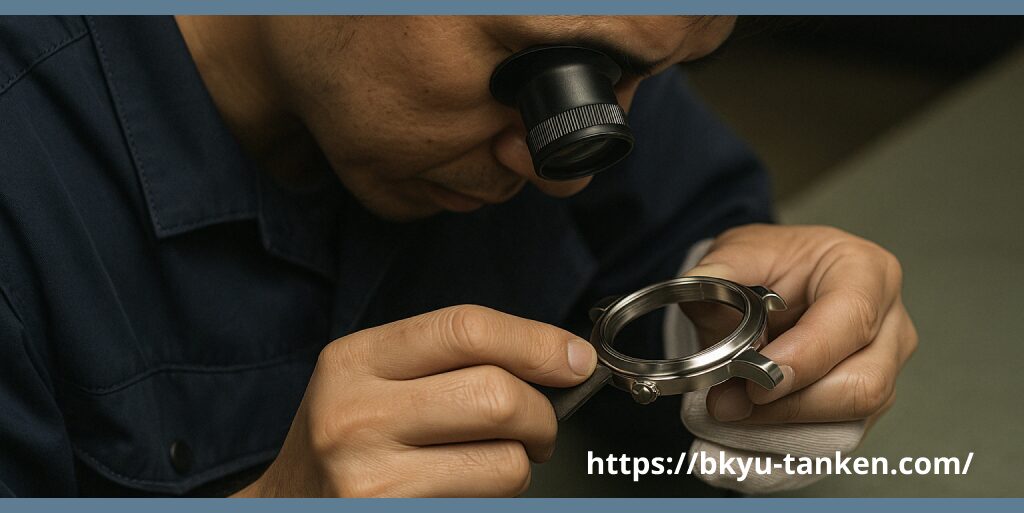
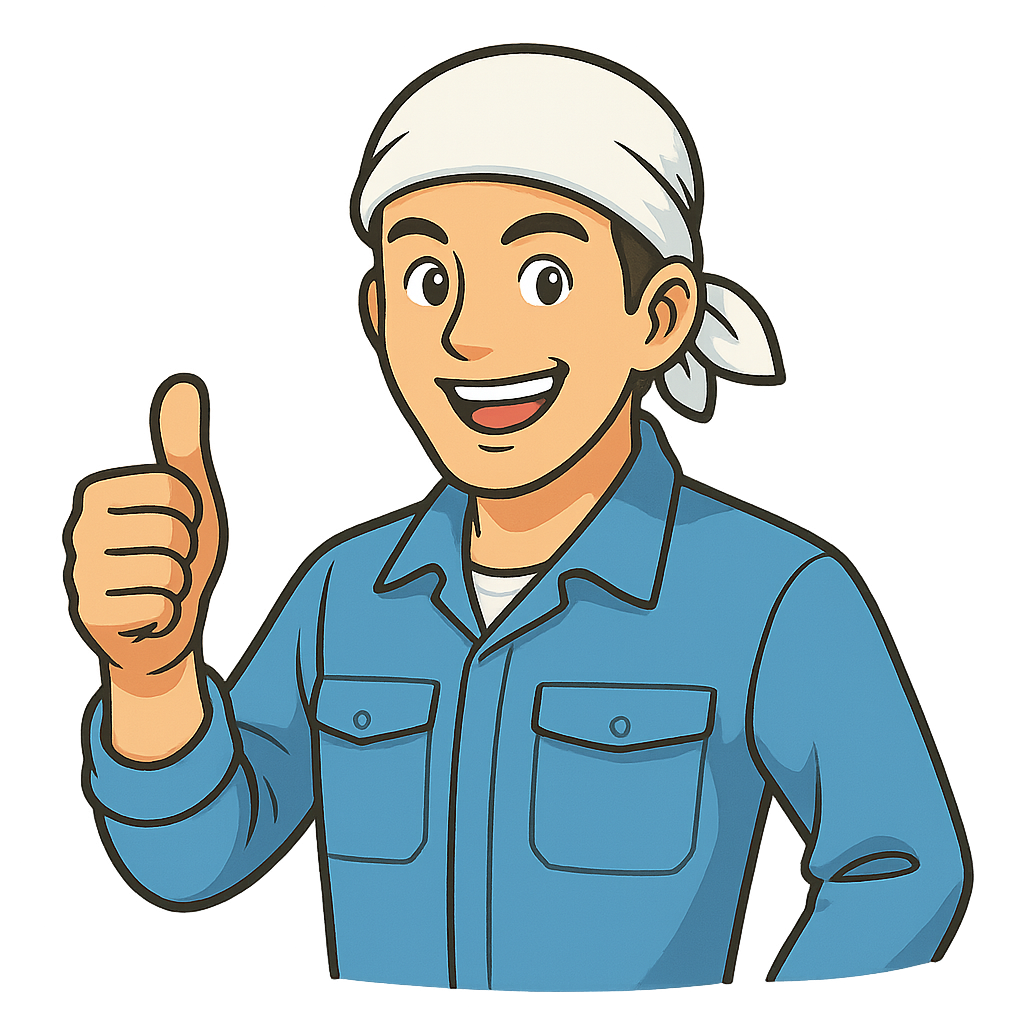
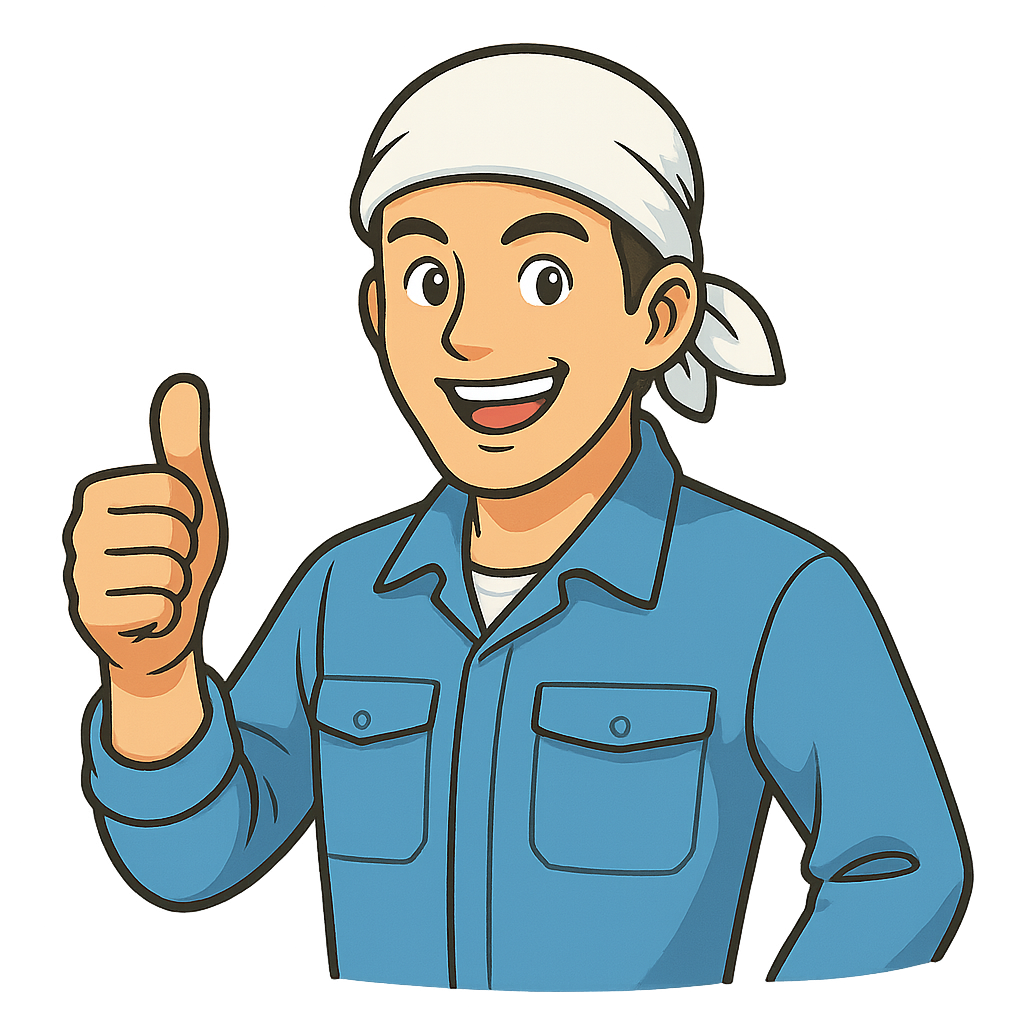
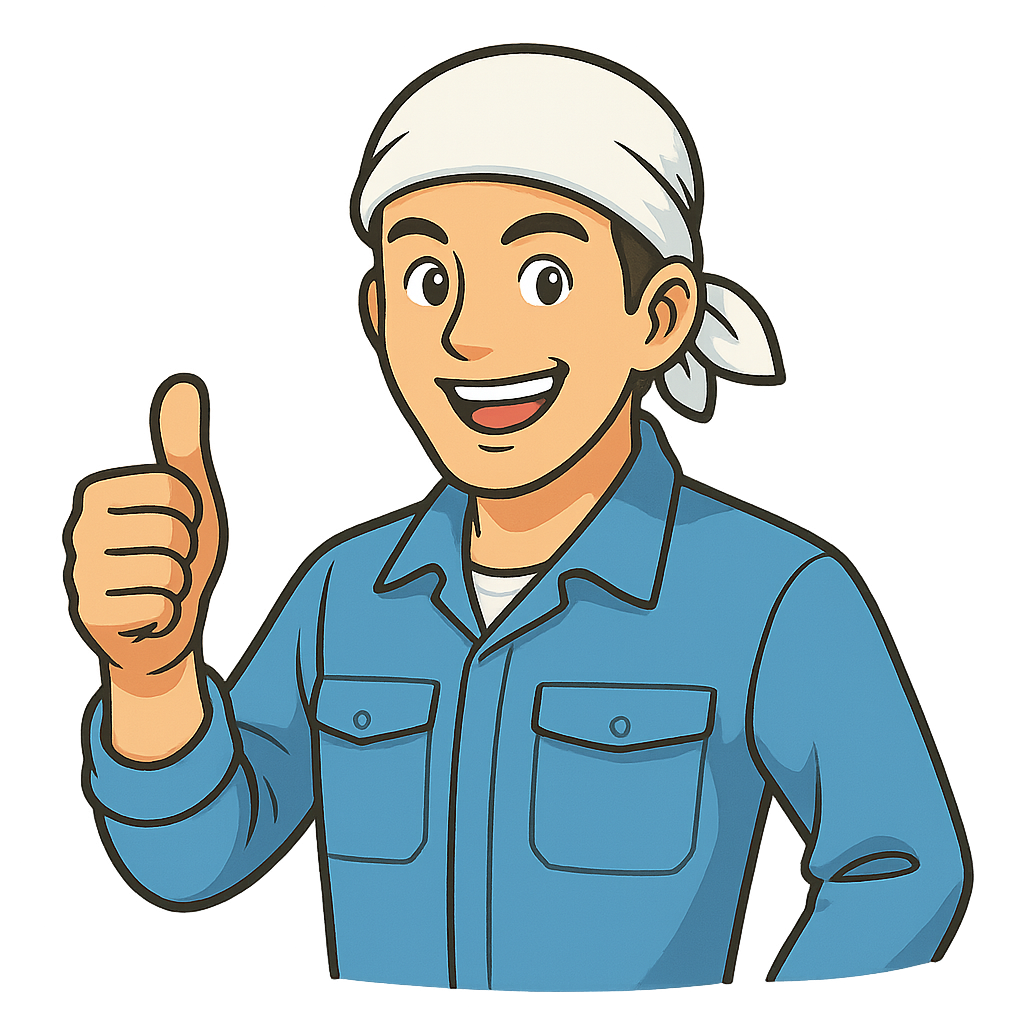
宝飾品や高級時計の世界では、手作業研磨が「価値」の一部となっています。機械では出せない独特の風合いや光の反射が、プレミアム感を生み出しているのです。量産品とは異なる評価軸があることを理解しましょう。
5. 導入事例:中小企業での成功例
実際の企業ではどのように研磨方法を選択しているのでしょうか。代表的な事例をご紹介します。
事例1:手作業研磨から部分的機械化へ(A社・精密部品メーカー)
背景
従業員15名の精密部品メーカーA社は、創業以来40年間、手作業による研磨を続けてきました。しかし、熟練職人の高齢化と受注量の増加により、生産性向上が課題となっていました。
取り組み
- 全工程を分析し、標準化できる作業を特定
- 単純形状の前処理工程のみ機械研磨を導入
- 仕上げ工程は引き続き手作業で対応
結果
- 生産性が約1.5倍に向上
- 職人の技術を最も価値のある工程に集中させることができた
- 初期投資約300万円を1年半で回収
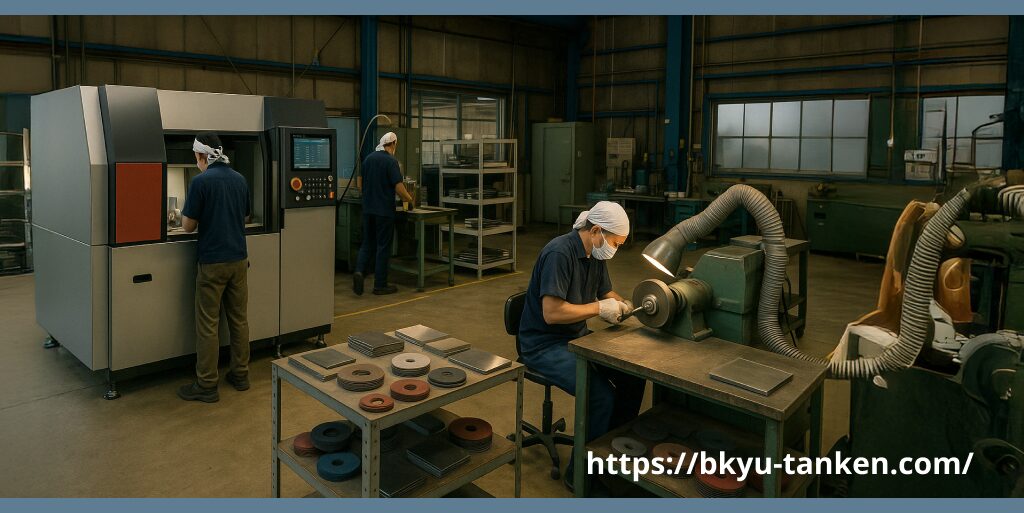
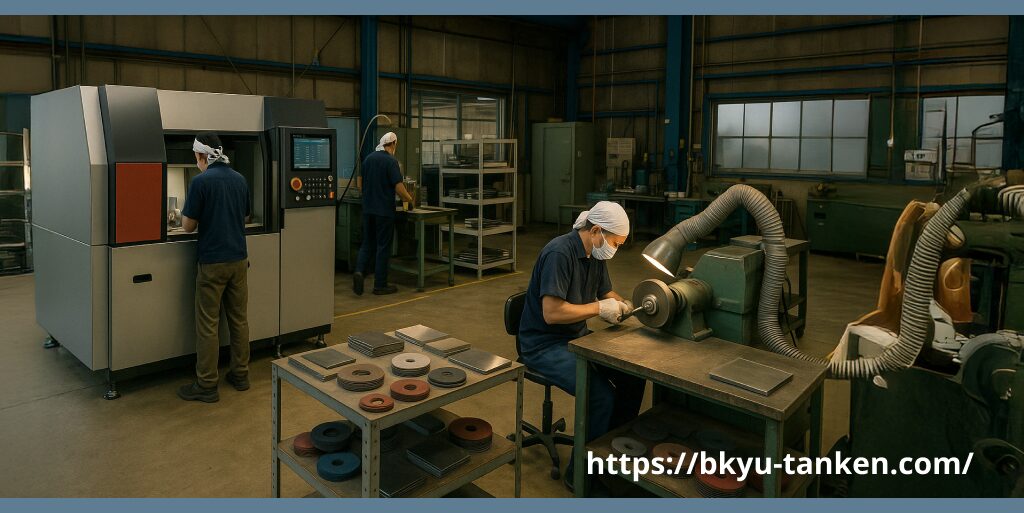
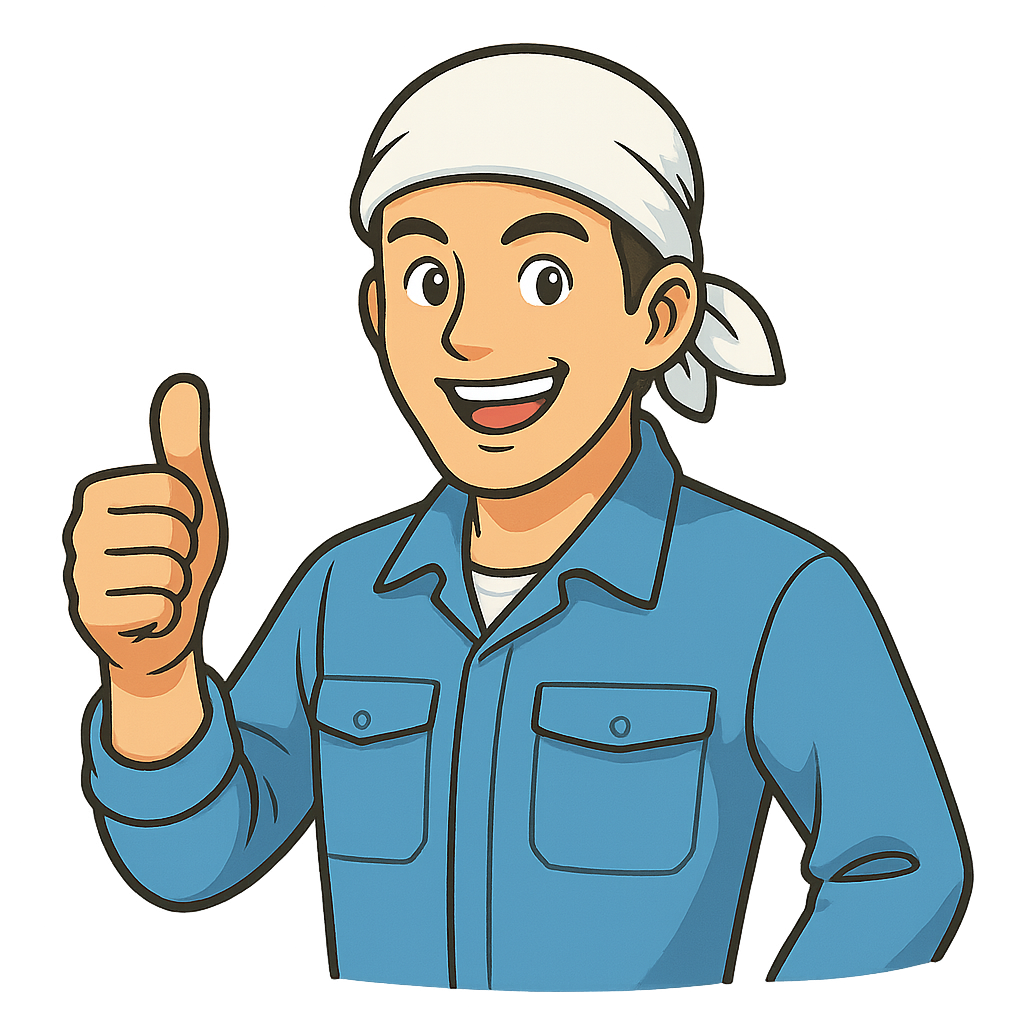
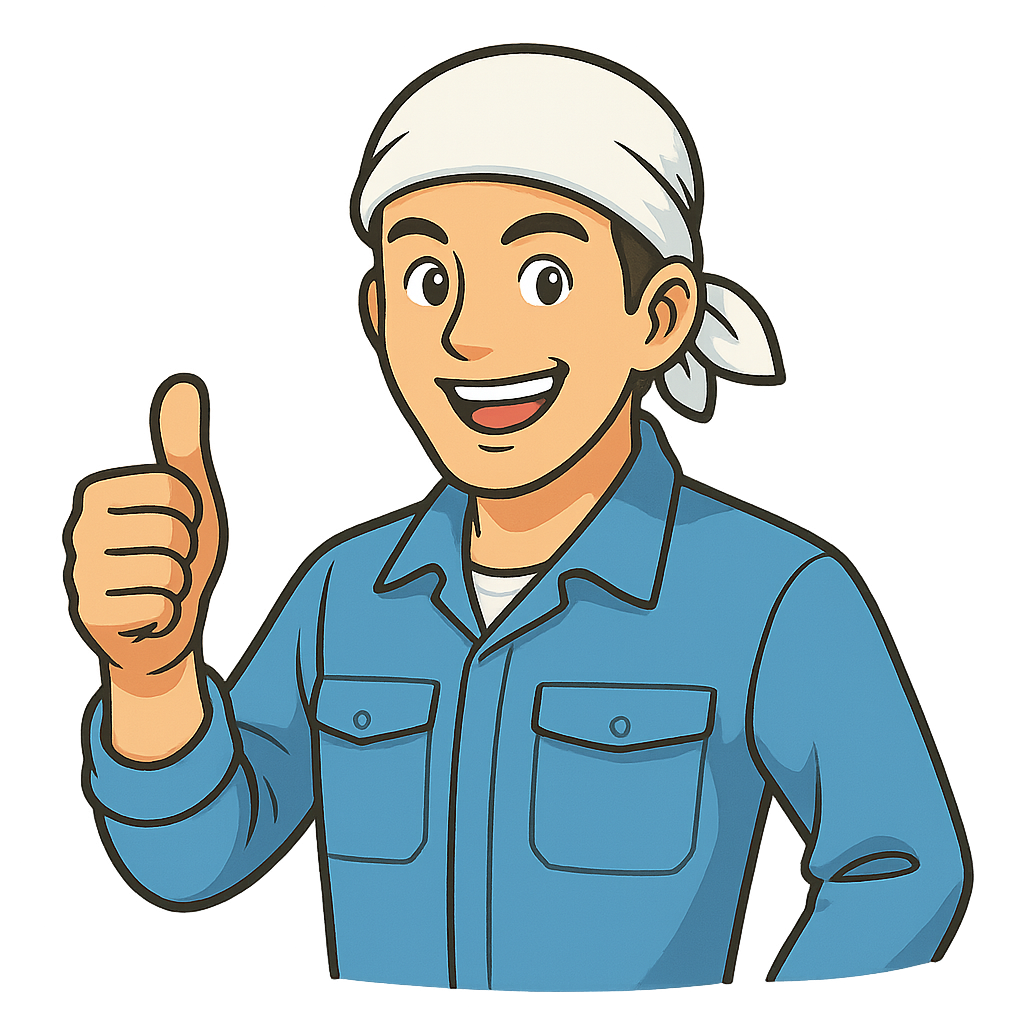
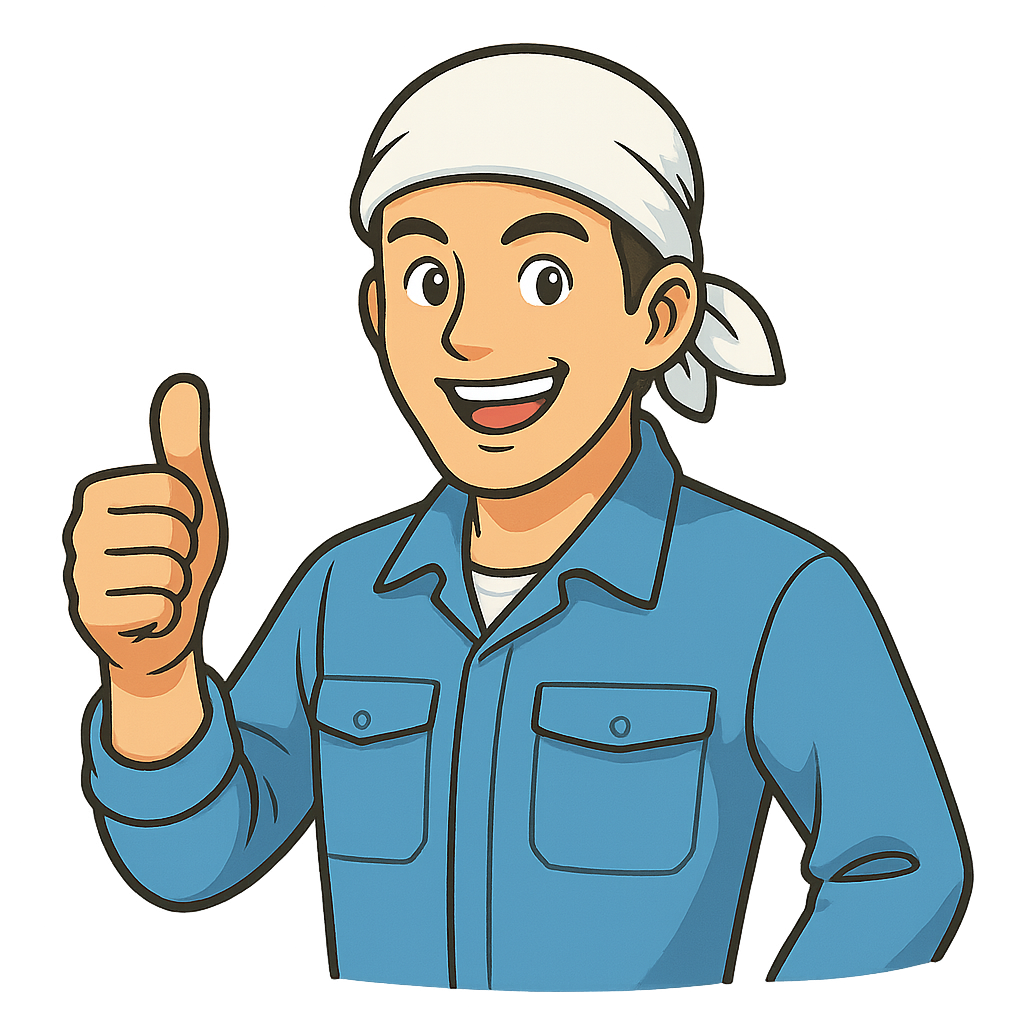
A社の成功の秘訣は「全面的な機械化」ではなく「最適な組み合わせ」を見つけたことです。コア技術は手作業で守りつつ、標準化できる部分は機械に任せるというバランス感覚が重要です。
事例2:機械研磨への全面移行(B社・自動車部品サプライヤー)
背景
従業員30名の自動車部品サプライヤーB社は、受注量の急増に伴い、従来の手作業研磨では対応しきれなくなっていました。
取り組み
- 全面的な機械研磨への移行を決断
- 複数の研磨機メーカーでテスト研磨を実施
- 社内研修制度を設け、オペレーター教育を徹底
結果
- 生産量が約3倍に増加
- 品質のバラつきが大幅に減少(不良率1/5に)
- 初期投資約800万円を2年で回収
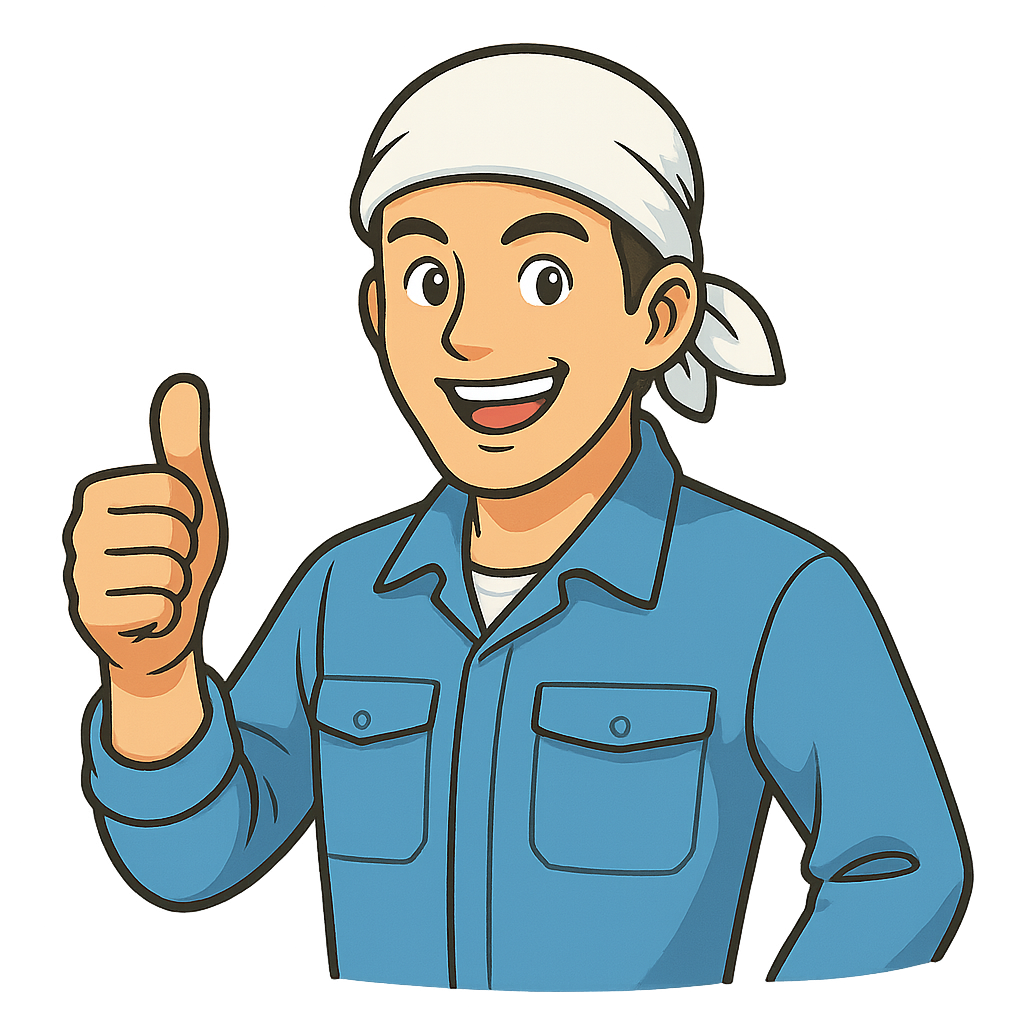
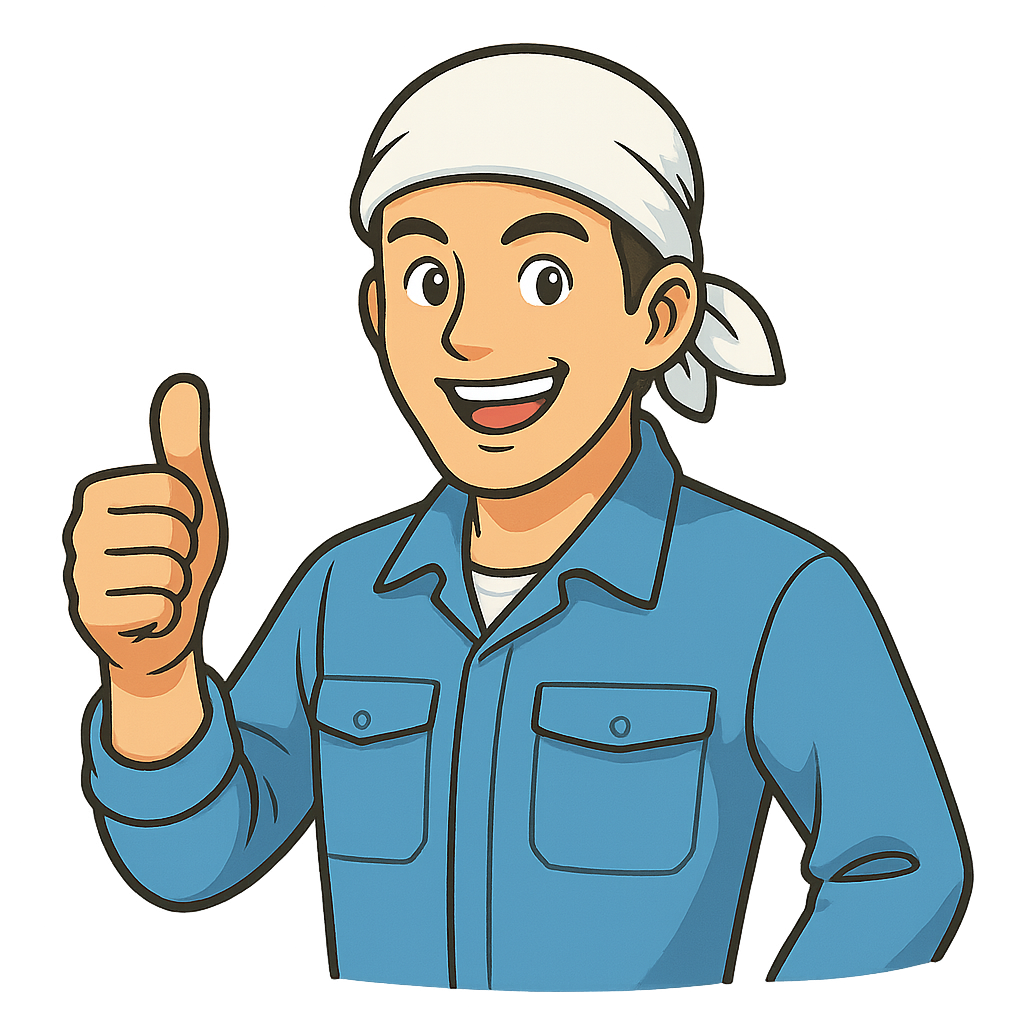
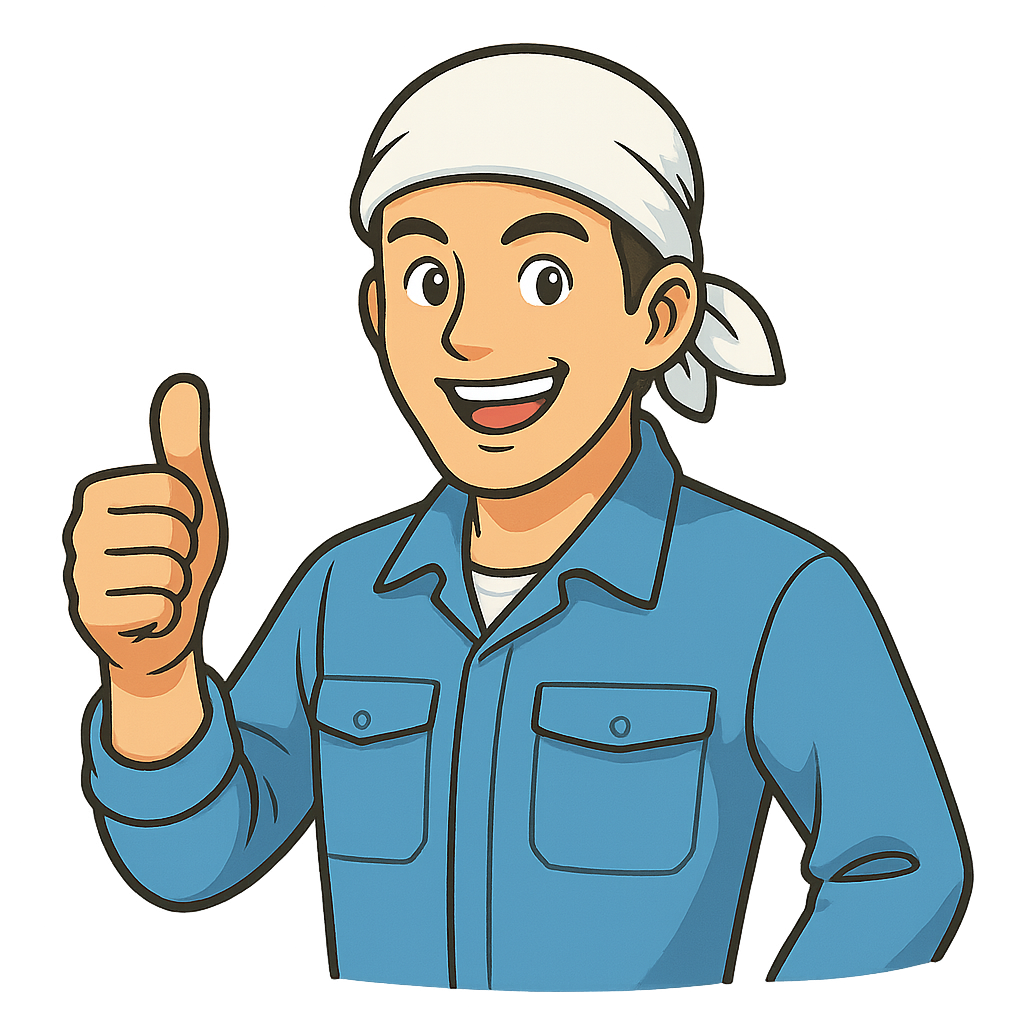
B社の事例は「決断の速さ」と「全社的な取り組み」が成功のポイントでした。機械化に踏み切る際は、現場の反発を恐れず、全員で新しい技術を学ぶ姿勢が重要です。
事例3:ハイブリッド方式の採用(C社・医療機器メーカー)
背景
従業員20名の医療機器メーカーC社は、高品質と量産性の両立に悩んでいました。
取り組み
- 工程を「粗研磨」と「仕上げ研磨」に明確に分離
- 粗研磨は全て機械化、仕上げは手作業を維持
- デジタル測定器を導入し、品質管理を強化
結果
- 品質を維持したまま生産性が2倍に向上
- 職人の負担が軽減され、技術伝承が進展
- 新規受注が20%増加
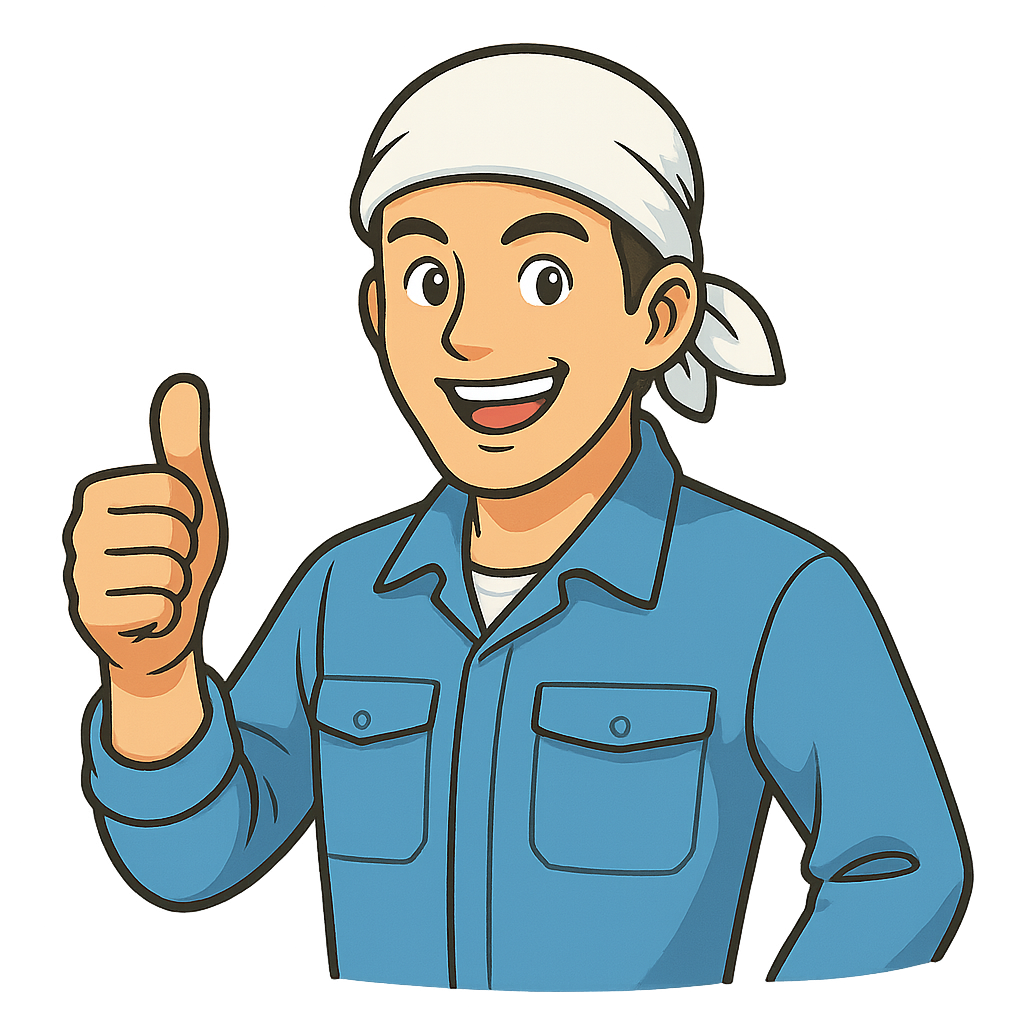
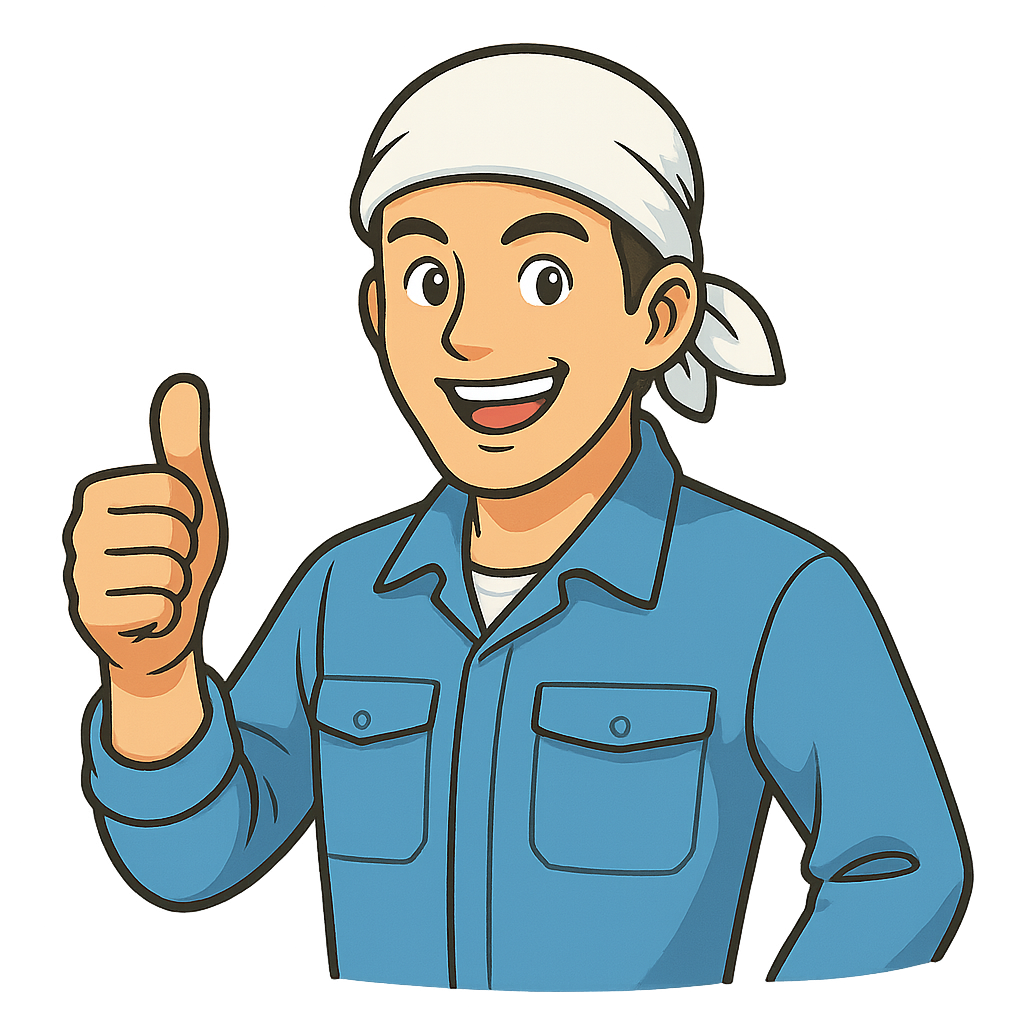
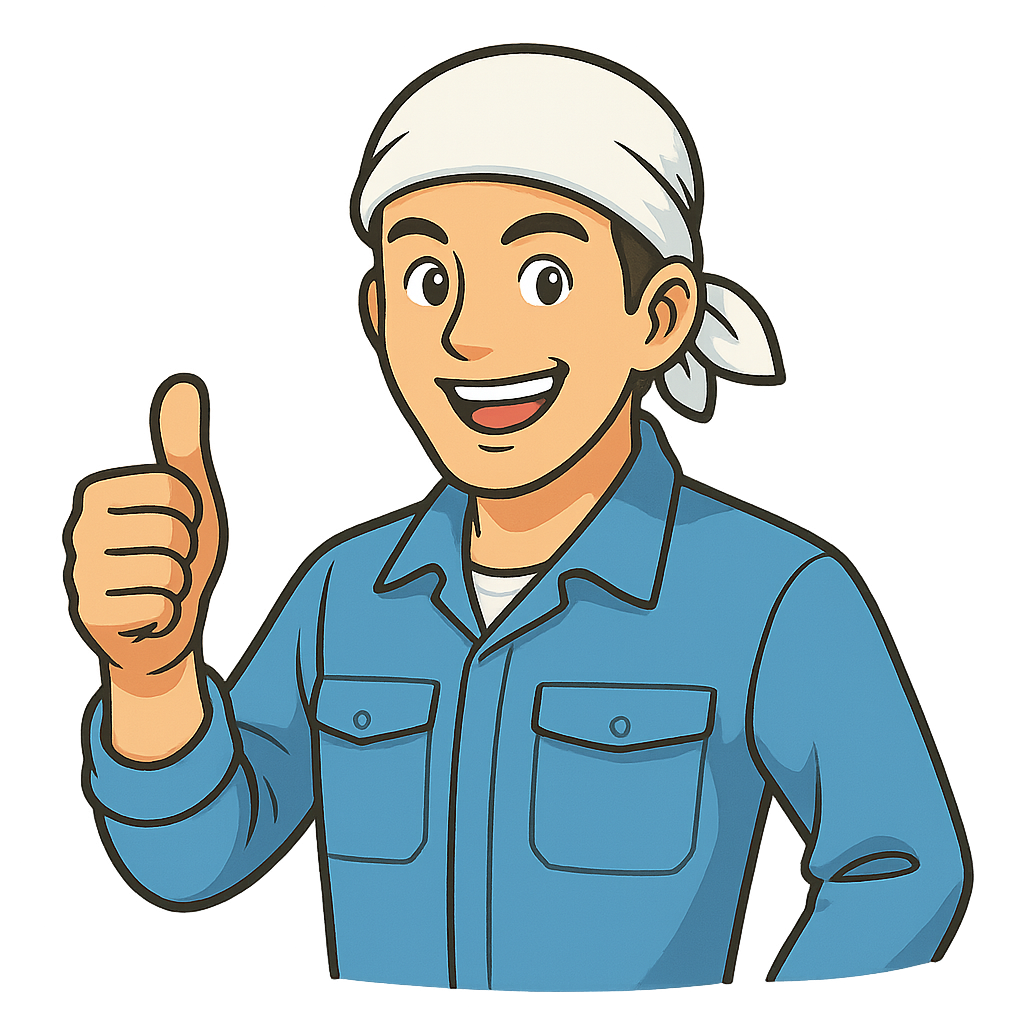
C社の事例は「工程の再設計」が鍵でした。単に「手作業か機械か」の二択ではなく、各工程で最適な方法を選び、組み合わせることで最大効果を得られます。
6. 選択の判断基準と移行のステップ
ここまでの情報を踏まえ、御社に最適な研磨方法を選択するための判断基準と、移行ステップをご紹介します。
最適研磨方法の判断基準
以下のフローチャートを参考に、御社の状況に最適な研磨方法を判断してみましょう。
生産量はどのくらいか?
- 月産50個未満 → 手作業研磨が有利
- 月産50〜300個 → ハイブリッド方式を検討
- 月産300個以上 → 機械研磨が有利
製品形状はどうか?
- 複雑・入り組んだ形状 → 手作業中心
- 比較的単純な形状 → 機械研磨可能
求められる品質レベルは?
- 特殊な仕上げ・美観重視 → 手作業中心
- 一般的な品質・均一性重視 → 機械研磨可能
予算はどのくらいか?
- 初期投資を抑えたい → 手作業から始める
- 長期的なコスト削減重視 → 機械研磨を検討
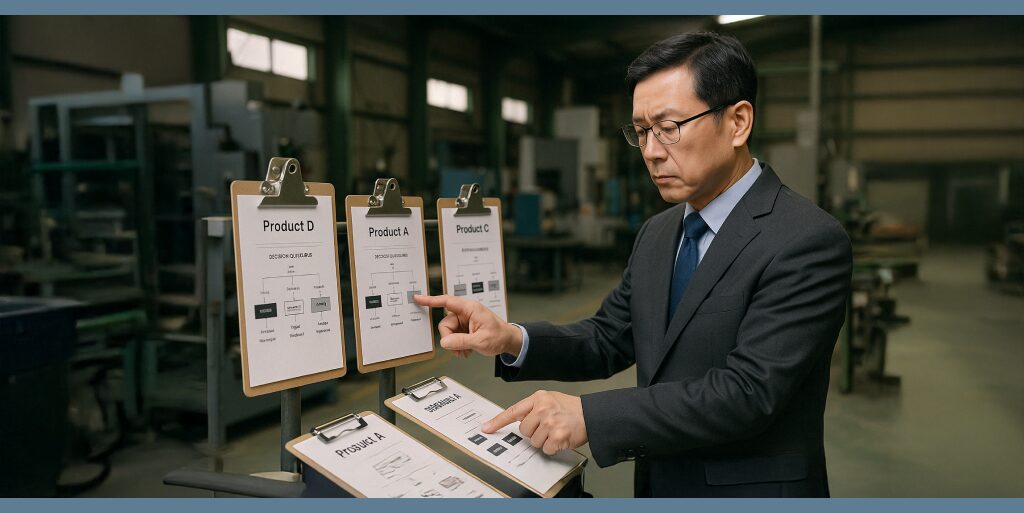
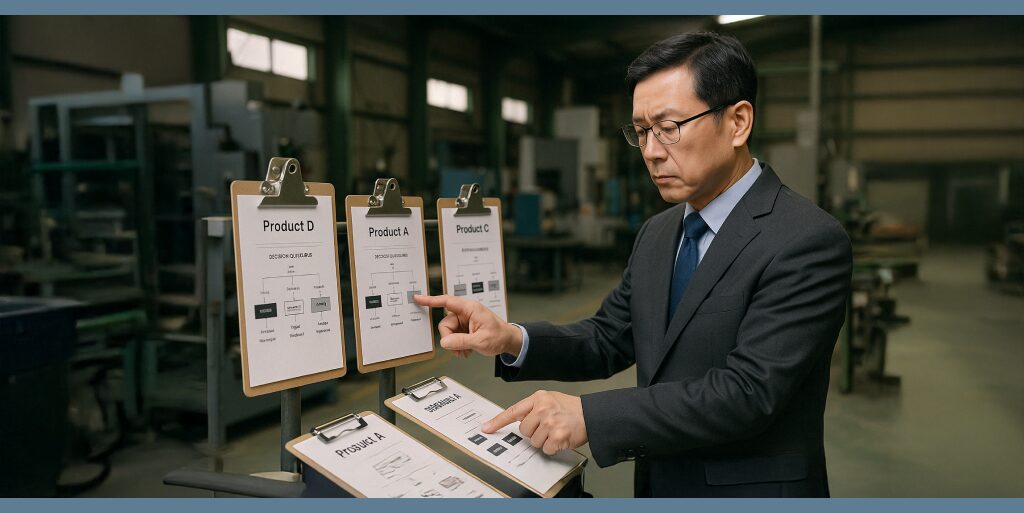
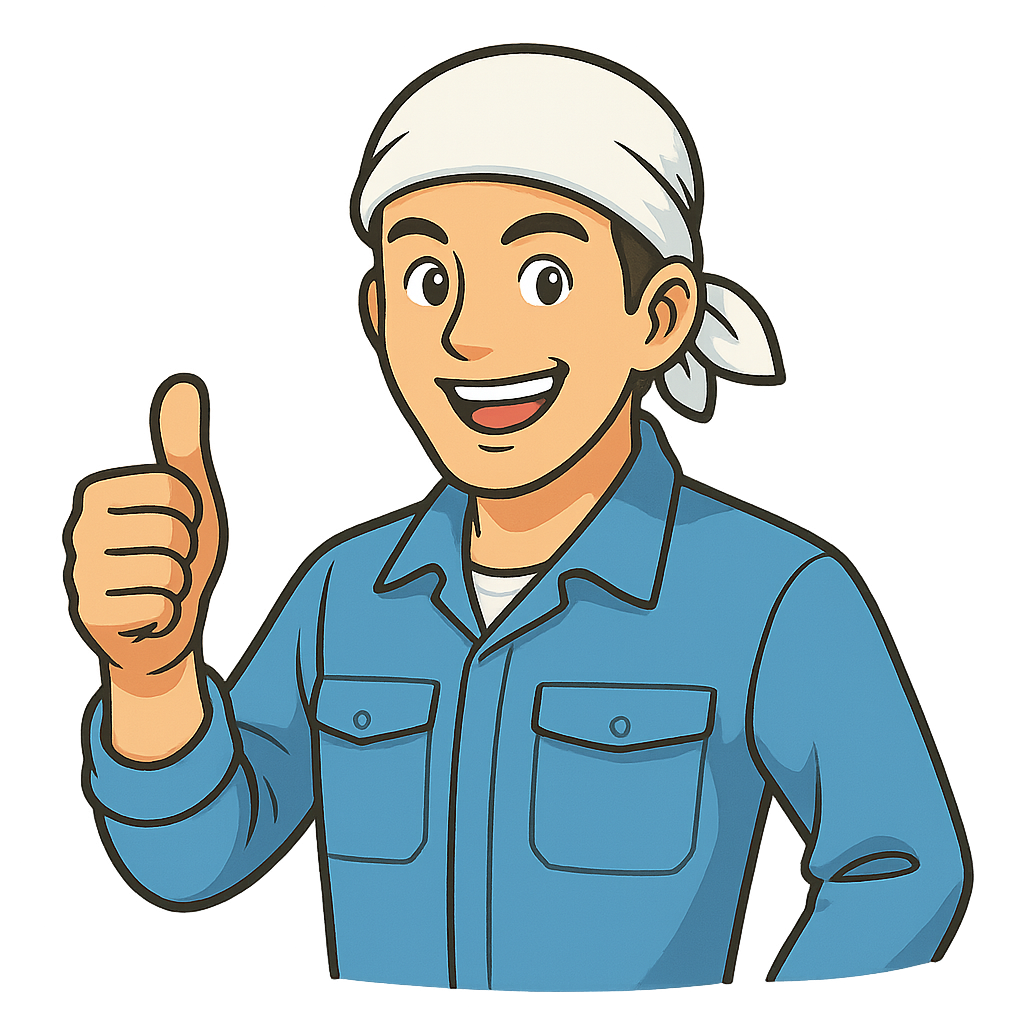
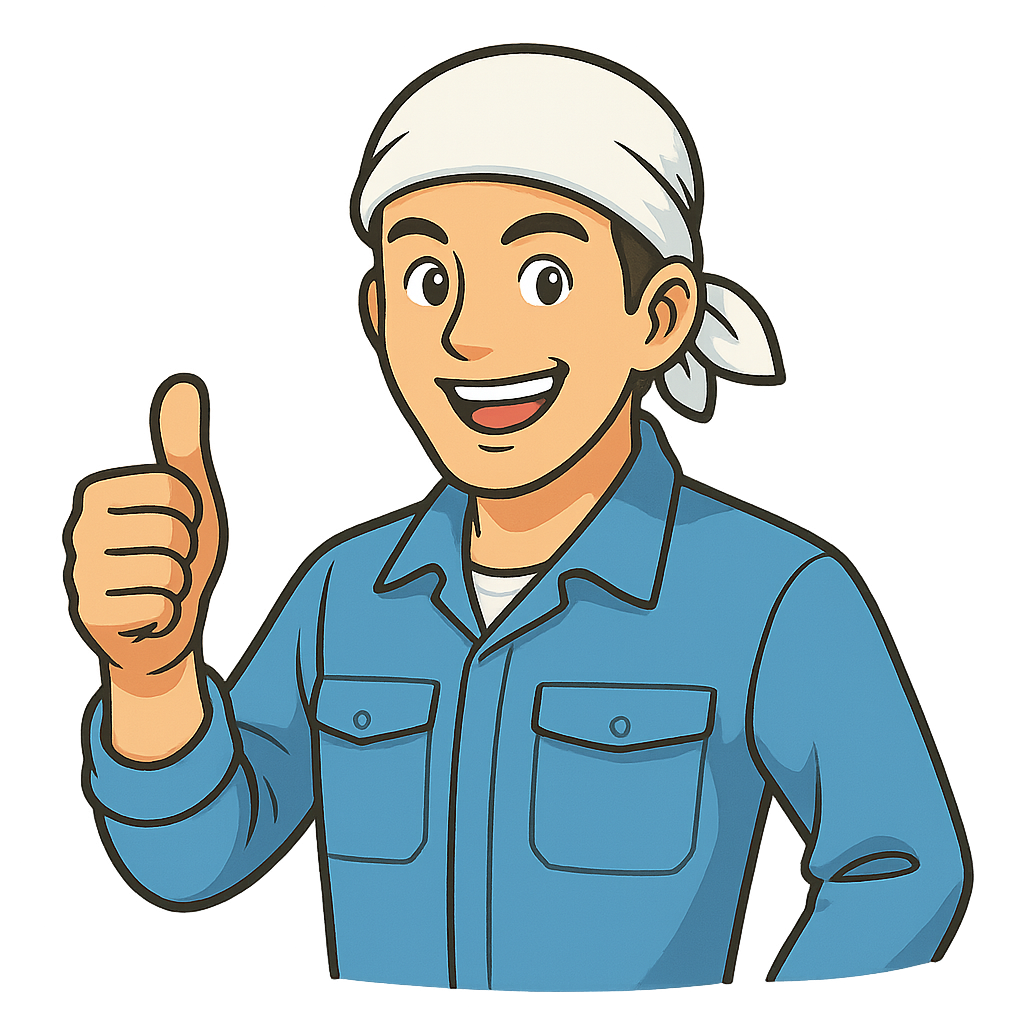
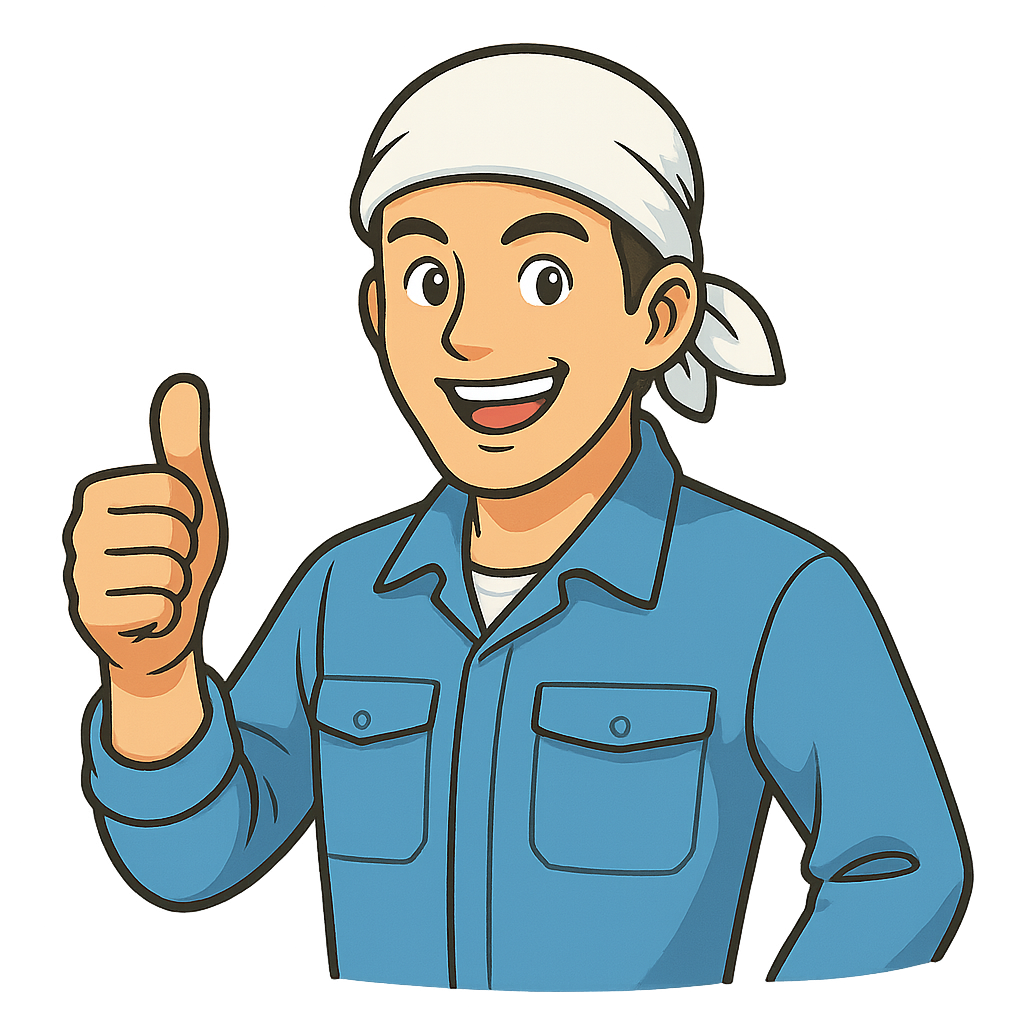
どちらか一方に完全に移行する必要はありません。多くの場合、「80:20の法則」が当てはまります。つまり、80%は機械化し、残り20%の重要な部分に職人の技術を集中させるという方法が理想的です
移行のステップ
実際に研磨方法を変更する際は、以下のステップを踏むことをおすすめします。
現状分析と目標設定
- 現在の生産性、品質、コストを詳細に把握
- 具体的な改善目標を数値で設定
テスト実施
- 少量の試作品で比較テスト
- 複数の機械メーカーやツールでの比較
段階的導入
- 一部の製品や工程から試験的に導入
- データに基づいた評価
人材育成
- 機械オペレーターの育成計画
- 手作業技術の継承方法の確立
効果測定と継続改善
- 定期的な効果測定と目標との比較
- 課題の洗い出しと改善サイクルの確立
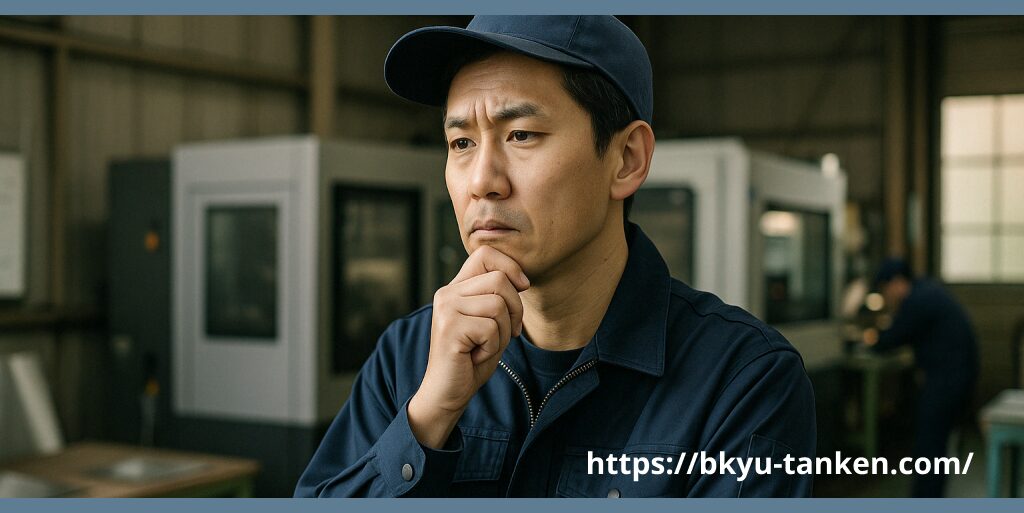
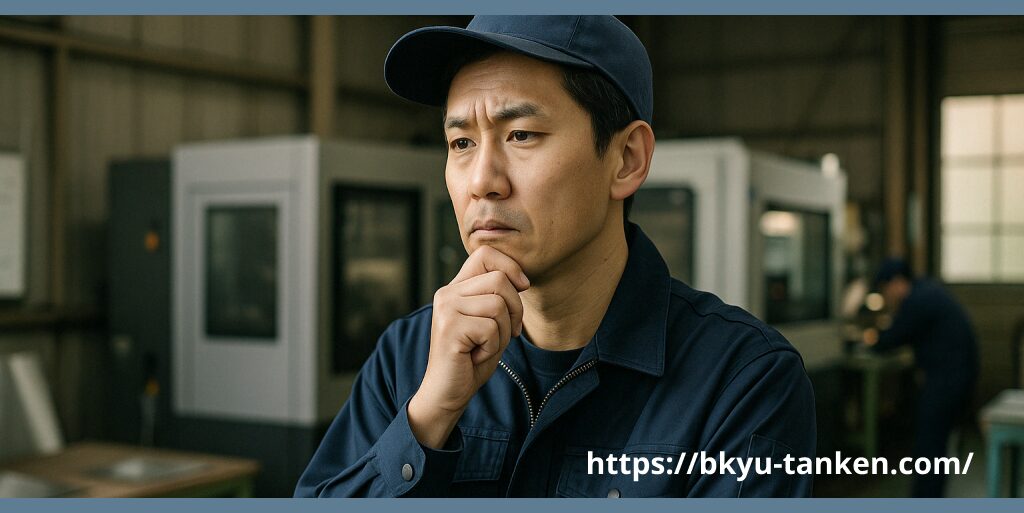
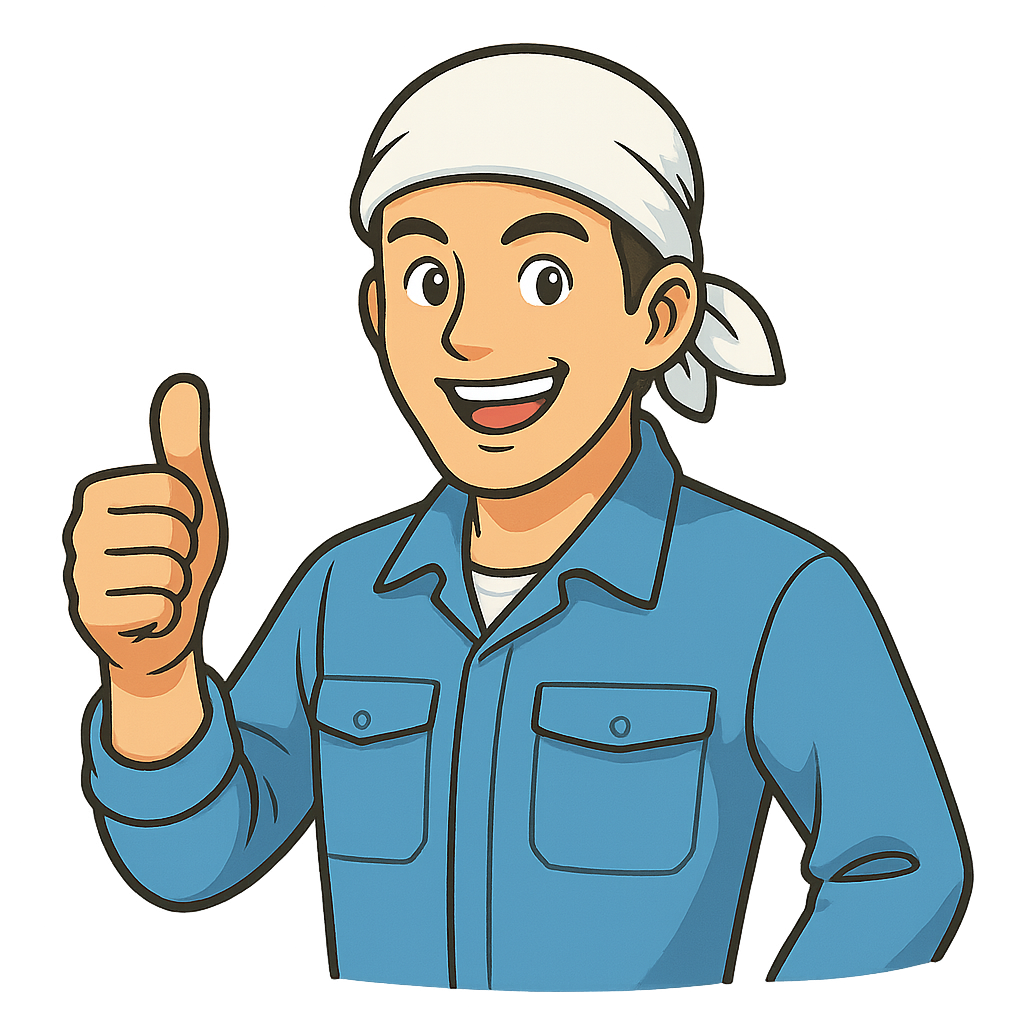
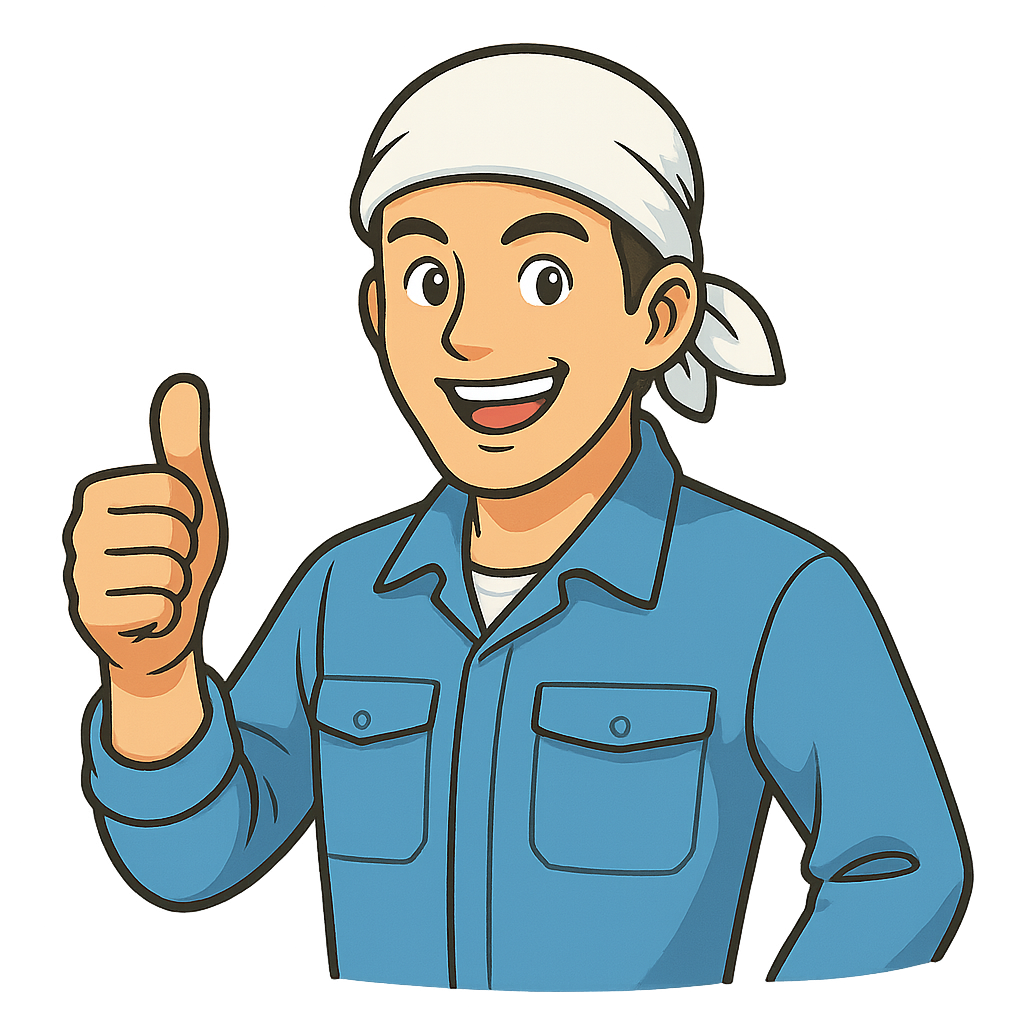
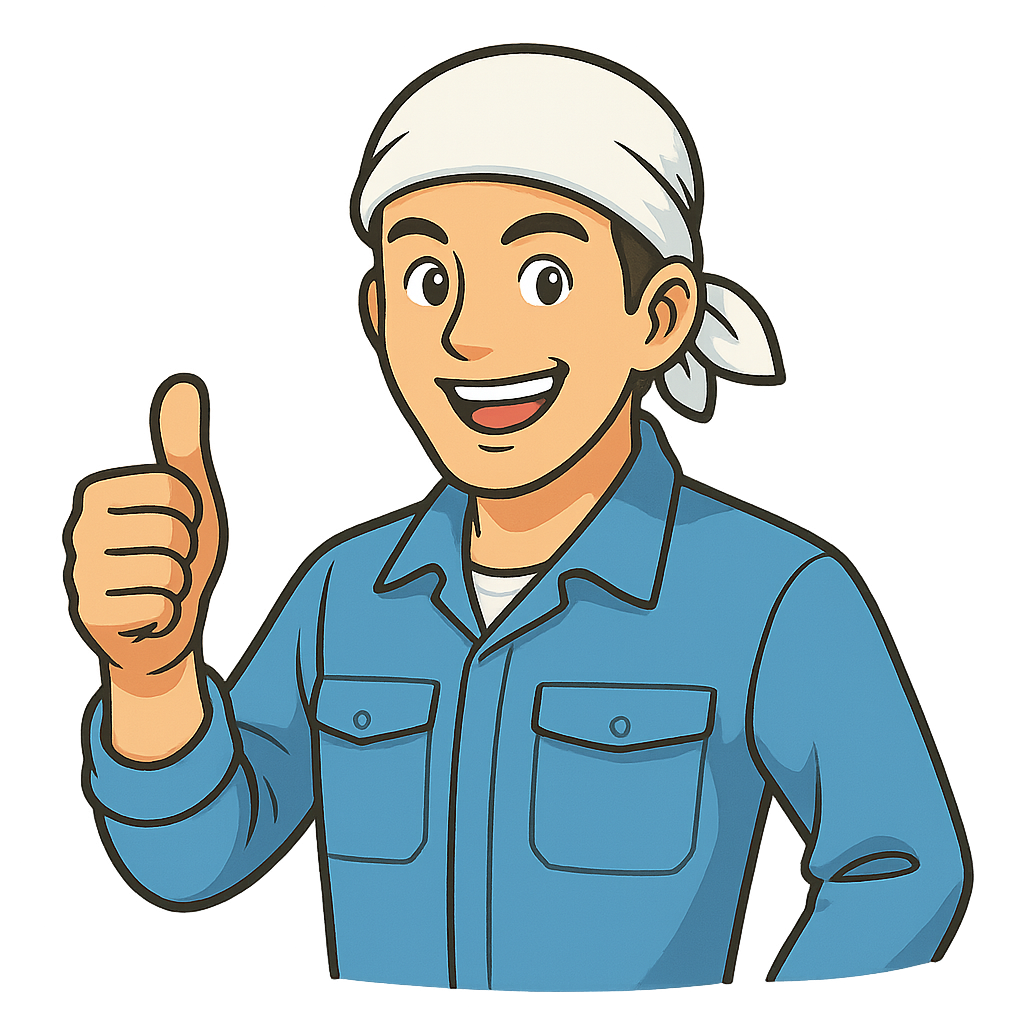
どちらか一方に完全に移行する必要はありません。多くの場合、「80:20の法則」が当てはまります。つまり、80%は機械化し、残り20%の重要な部分に職人の技術を集中させるという方法が理想的です
研磨方法の移行は「技術革新」であると同時に「文化の変化」でもあります。特に熟練職人の心理的抵抗を理解し、彼らの経験を新しいシステムに活かす方法を見つけることが成功の鍵です。全員が参加できるプロジェクトとして進めましょう。
まとめ:あなたの工場に最適な研磨方法は?
ここまで手作業研磨と機械研磨について詳しく比較してきましたが、「どちらが絶対に優れている」という答えはありません。大切なのは、自社の状況や製品特性に合った最適解を見つけることです。
今回の内容を整理すると、
- 手作業研磨の強み:複雑形状への対応力、特殊仕上げの実現、初期投資の少なさ
- 機械研磨の強み:均一性と再現性、大量生産での効率性、長期的なコスト効果
これからの製造業は、両方の良さを理解し、最適に組み合わせることが競争力につながります。「職人技術 vs 機械化」という二項対立ではなく、両者の強みを活かしたハイブリッド方式が次世代の研磨技術の主流になっていくでしょう。
御社の課題や状況について、具体的なアドバイスが必要でしたら、いつでもご相談ください。20年以上の研磨経験を活かし、最適な研磨ソリューションをご提案いたします。
コメント