アルミ研磨におけるバリ取り不良の原因と解決策:現場で即実践できる7つの改善テクニック
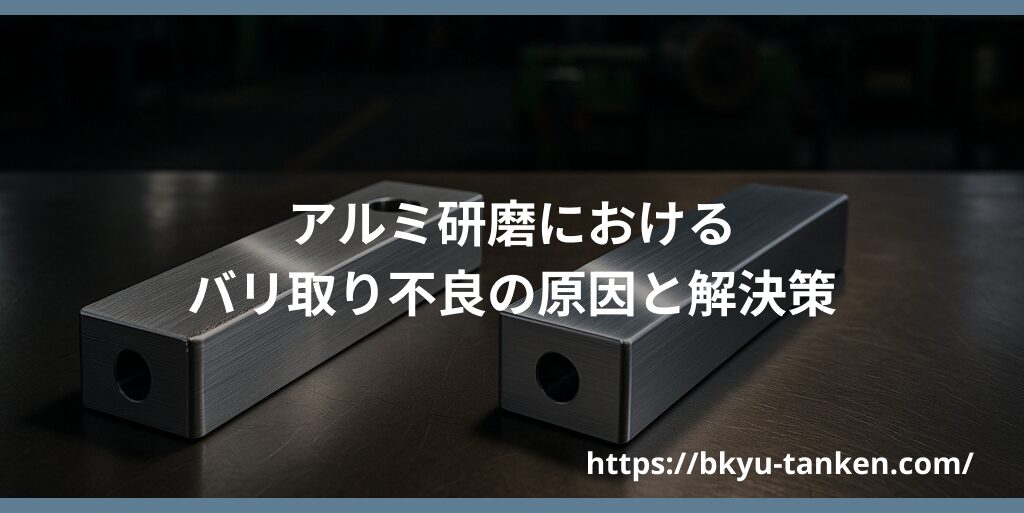
アルミニウム部品の製造工程において、バリ取り作業は品質を左右する重要なプロセスです。しかし、多くの製造現場では「バリは除去できたのに表面に傷が残る」「作業効率が上がらない」「品質にばらつきがある」といった課題に直面しています。特に中小企業では、限られた設備や人員の中で高品質な製品を安定して供給するプレッシャーがあります。
この記事では、アルミ研磨工程におけるバリ取り不良の主要な原因と具体的な解決策を、現場ですぐに実践できる形でご紹介します。適切な工具選定から作業手順の最適化、効果的な検査方法まで、品質向上とコスト削減を同時に実現するアプローチをわかりやすく解説します。
1. バリ取り不良が発生する3大原因
アルミ部品のバリ取り不良は、多くの場合以下の3つの原因に集約されます。それぞれの原因を正確に把握することが、効果的な対策の第一歩となります。
切削条件と工具選定の不適合
アルミニウムは軟質金属であるため、切削時に刃物の送り速度や回転数が不適切だと、バリ(切削時に発生する不要な突起物)が過剰に発生します。特に高速切削時には注意が必要です。
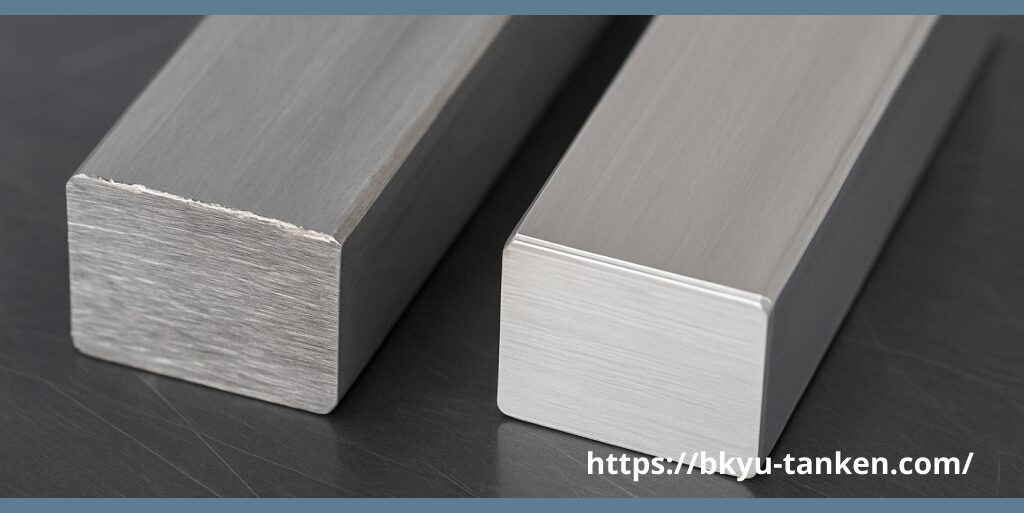
適切な切削条件を設定せずに加工を行うと、バリの大きさや形状にばらつきが生じ、後工程のバリ取り作業が困難になります。例えば、切削速度が速すぎると「むしれ」が発生し、遅すぎると「押しつぶし」によるバリが増加します。
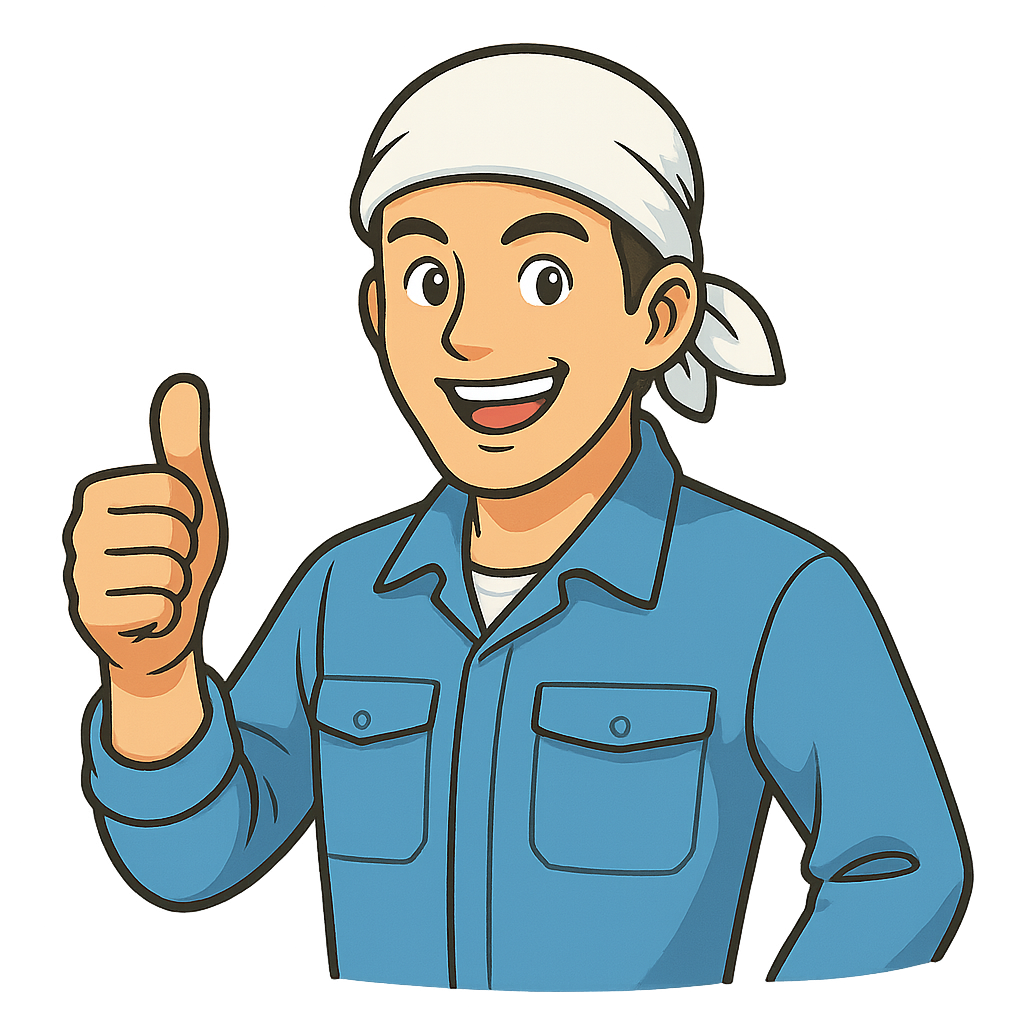
切削油の種類や量も重要です。アルミ専用の切削油を使うと、バリの発生を30%程度抑えられることがあります。コスト面でも結果的に有利になりますよ。
不適切な研磨材・研磨工具の使用
バリ取りに使用する研磨材や工具がアルミニウムの特性に合っていないケースも多く見られます。アルミは軟らかく、目詰まりを起こしやすい特徴があります。
一般的な研磨材では以下の問題が発生しやすくなります。
- 粒度が粗すぎる場合:表面に深い傷がつく
- 粒度が細かすぎる場合:バリ除去効率が低下
- 研磨圧が強すぎる場合:アルミ表面が変形する
- 研磨速度が速すぎる場合:熱によるアルミの溶着
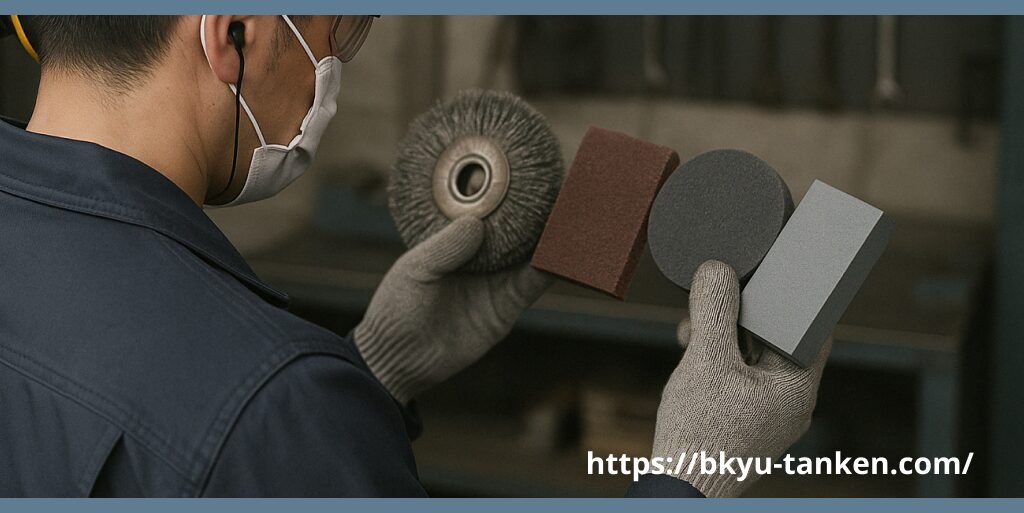
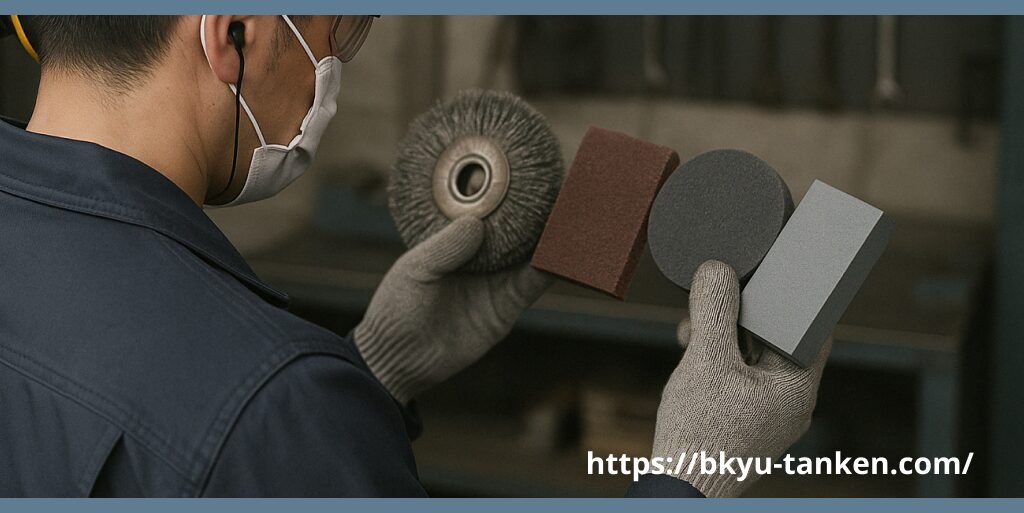
作業手順と検査基準の不明確さ
多くの現場では、バリ取り作業の標準手順書が不十分であったり、作業者によって手法がばらついたりすることがあります。特に経験の浅い作業者は、必要以上に力を入れたり、同じ箇所を何度も研磨したりする傾向があります。
また、バリ取り後の検査基準が曖昧なため、「どこまで研磨すればよいのか」という判断が難しく、結果として過剰研磨や研磨不足といった問題が発生します。
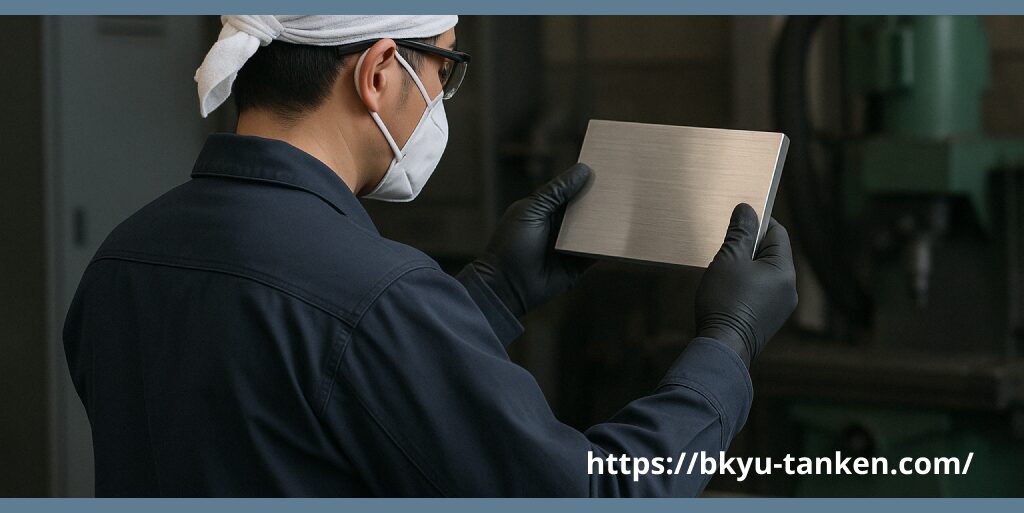
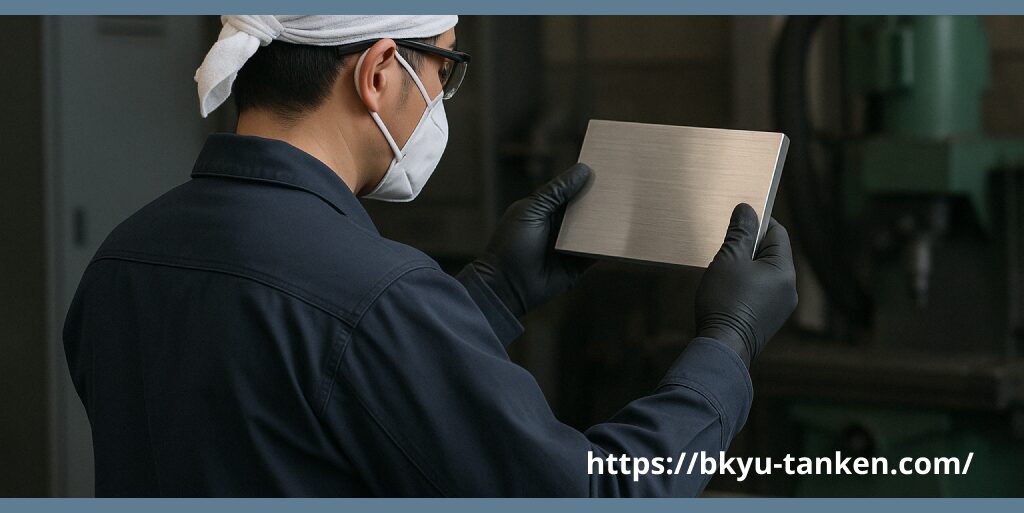
バリ取り不良を解決する効果的なアプローチ
バリ取り不良を解決するには、原因に応じた適切な対策が必要です。ここでは、現場ですぐに実践できる効果的なアプローチを紹介します。
材料特性に合わせた切削条件の最適化
アルミニウムの切削加工では、材料特性(合金の種類、硬度など)に応じた最適な切削条件を設定することが重要です。
アルミニウム切削の基本条件
- 切削速度:一般的に高速(300〜500m/分)
- 送り量:中程度(0.1〜0.3mm/回転)
- 切込み量:合金の硬さによる調整が必要
- 工具材質:超硬工具が推奨
これらの条件は、使用する工作機械や冷却方法によっても調整が必要です。最適条件を見つけるには、少量のテスト加工を行い、バリの発生状況を確認することをおすすめします。
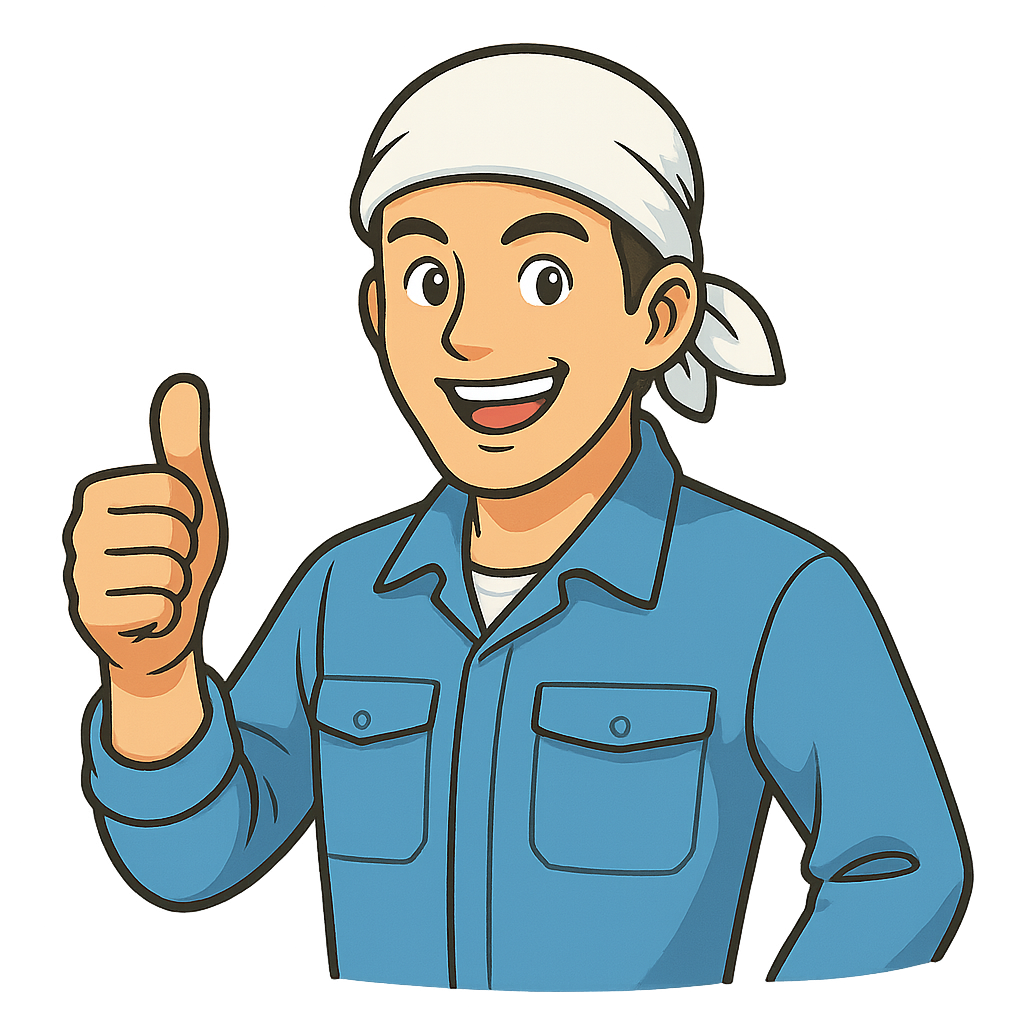
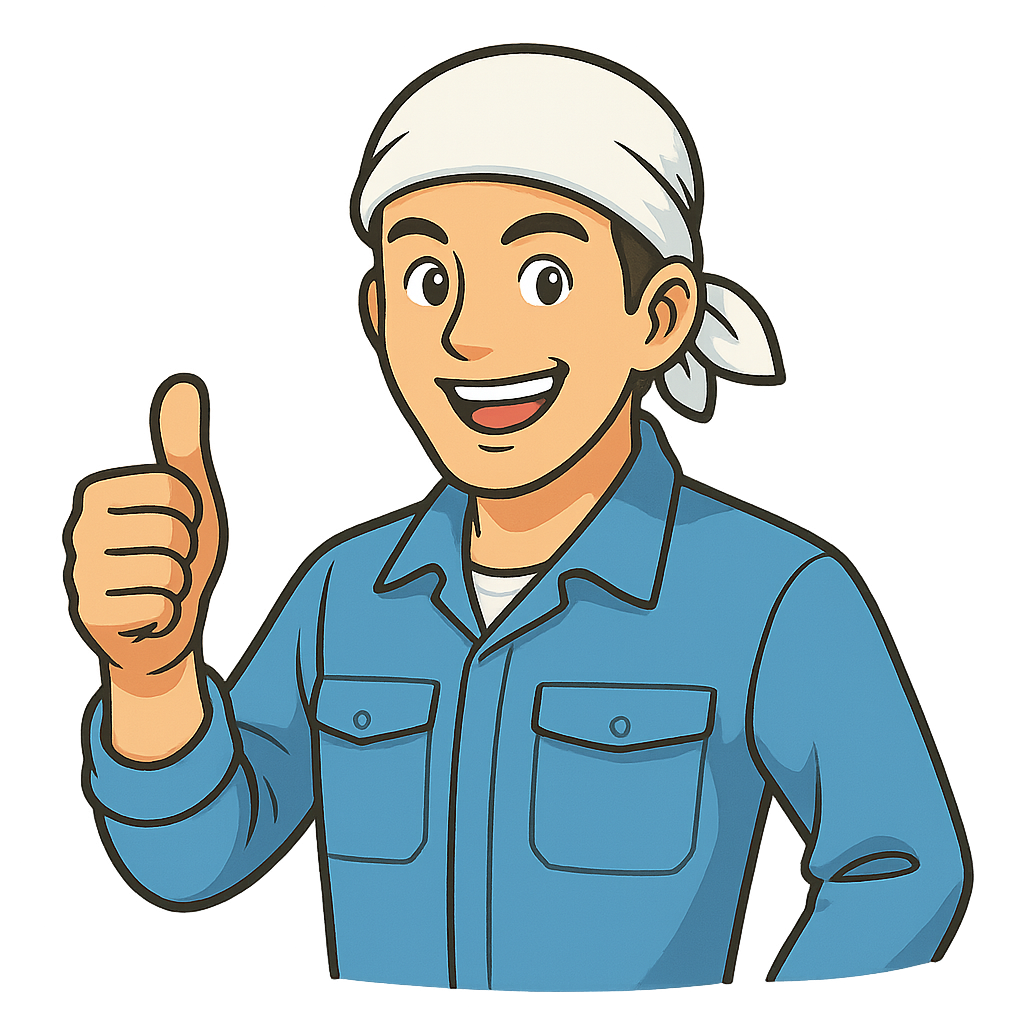
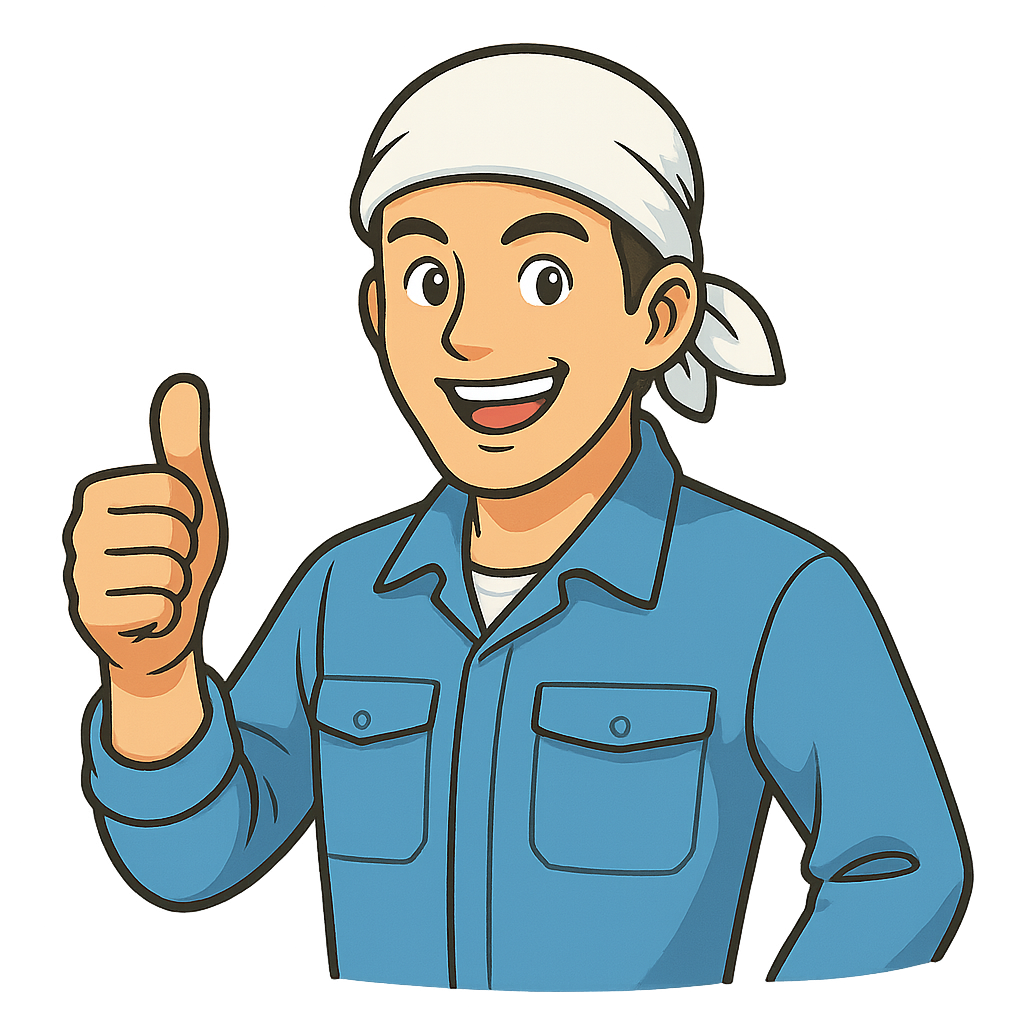
切削工具のエッジ形状も重要です。アルミ専用の『ポジティブレーキ』と呼ばれる刃先形状を持つ工具を使うと、バリの発生を大幅に抑えられます。初期投資は増えますが、後工程のコスト削減につながりますよ。
アルミニウム専用研磨材の選定と使用法
アルミニウムのバリ取りには、専用に設計された研磨材を使用することで効率と品質が大きく向上します。特に3M スコッチブライト(Scotch-Brite)などの不織布系研磨材は、アルミの研磨に適しています。
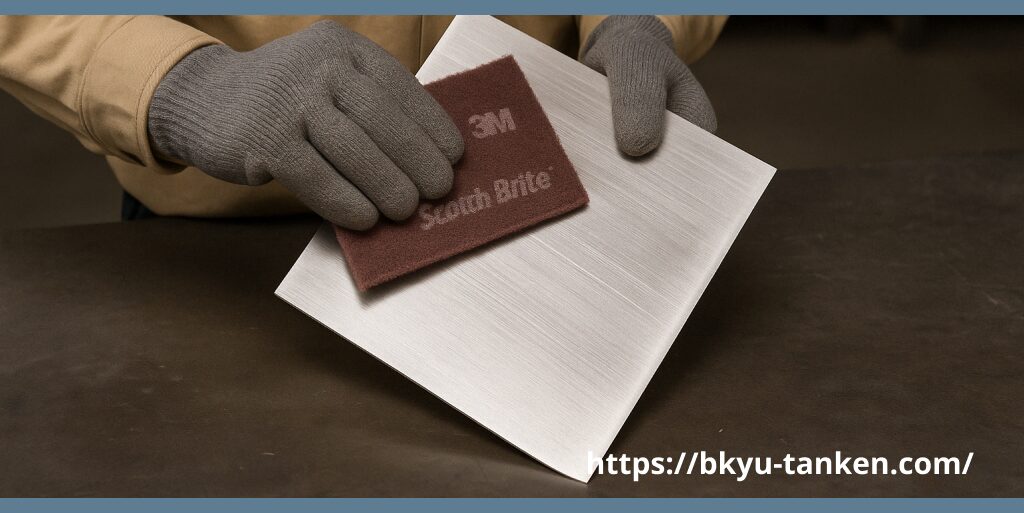
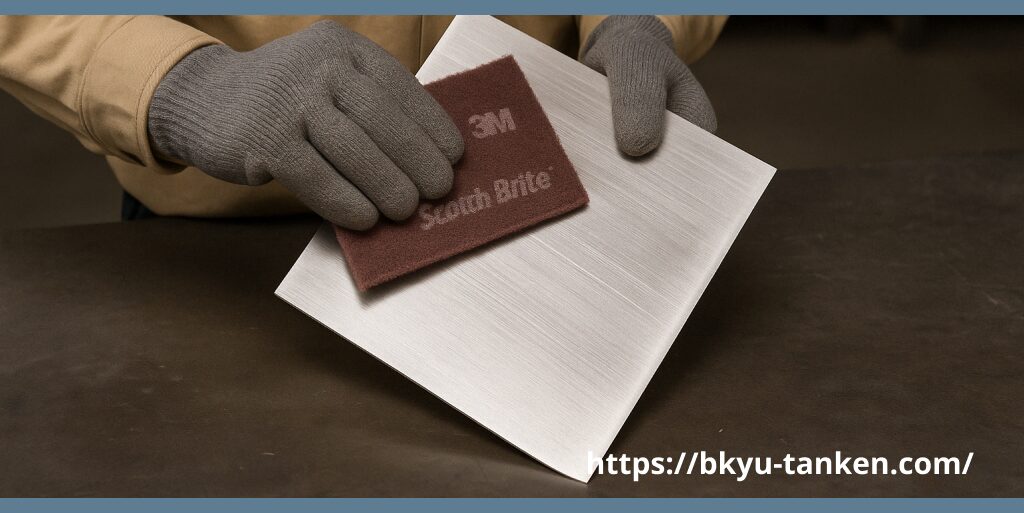
アルミ研磨に適した研磨材の選び方
粗研磨(バリ除去初期):#80〜#120の粒度
- フラップホイールやサンディングディスク
- バリの大きさに応じて選定
中研磨(表面平滑化):#180〜#320の粒度
- 不織布系研磨材
- 目詰まりしにくい構造のものを選定
仕上げ研磨(表面美観向上):#400以上の粒度
- バフ研磨や化学研磨
- 製品要求に応じて選定
使用時のポイントは、研磨圧を一定に保ち、同じ箇所を長時間研磨しないことです。特に角部や細い部分は熱がこもりやすいため注意が必要です。
標準作業手順と検査基準の確立
バリ取り作業の品質を安定させるには、明確な標準作業手順書と客観的な検査基準が不可欠です。
標準作業手順書に含めるべき内容
- 使用する研磨材の種類と順序
- 各工程での研磨時間と圧力の目安
- 研磨方向と動作パターン
- 注意すべき部位とその対応方法
- 工具の交換タイミング
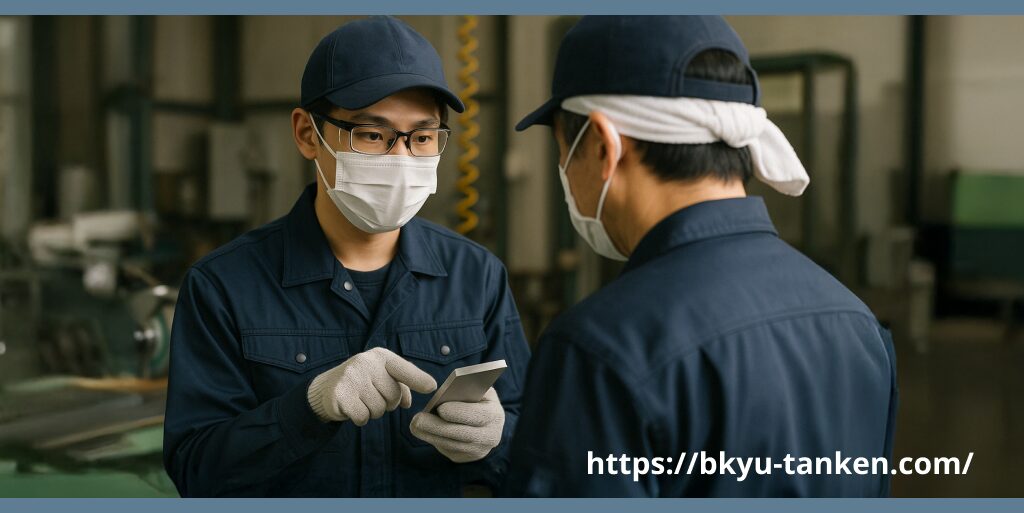
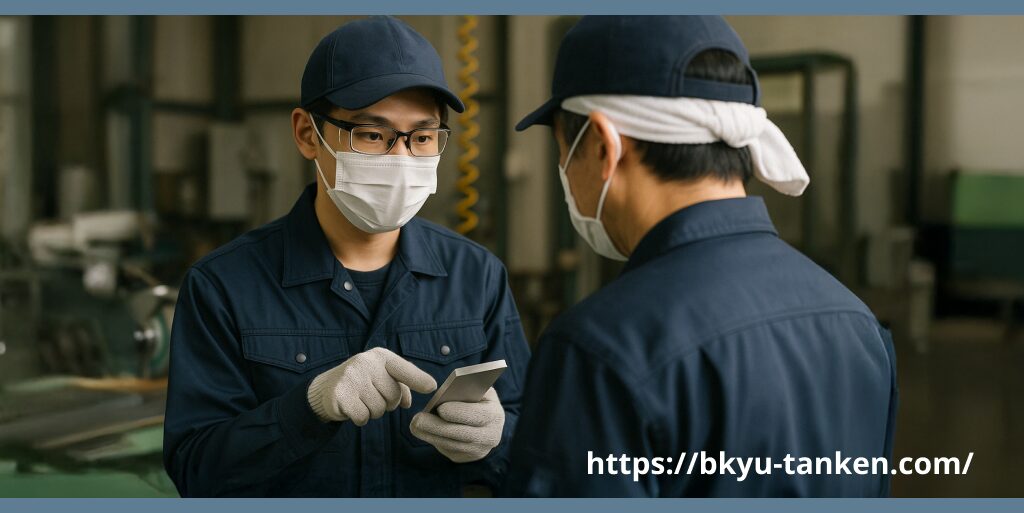
検査基準には、面粗度の数値目標や、目視検査のポイントを明記します。可能であれば、良品・不良品のサンプルを用意し、比較できるようにすると効果的です。
3. 現場で効果を発揮するバリ取り技術
ここでは、実際の現場で即効性のある具体的なバリ取り技術を紹介します。
フラップホイールを使用した効率的バリ取り
フラップホイールは、柔軟性と研磨力を兼ね備えた効率的なバリ取り工具です。特にアルミニウム専用に設計されたものを使用することで、品質と効率が向上します。
フラップホイールの効果的な使用法
- 回転数:製品推奨値の80%程度で開始
- 接触角度:15〜30度で軽く当てる
- 移動速度:一定のスピードで連続的に動かす
- 研磨方向:できるだけ一方向に統一
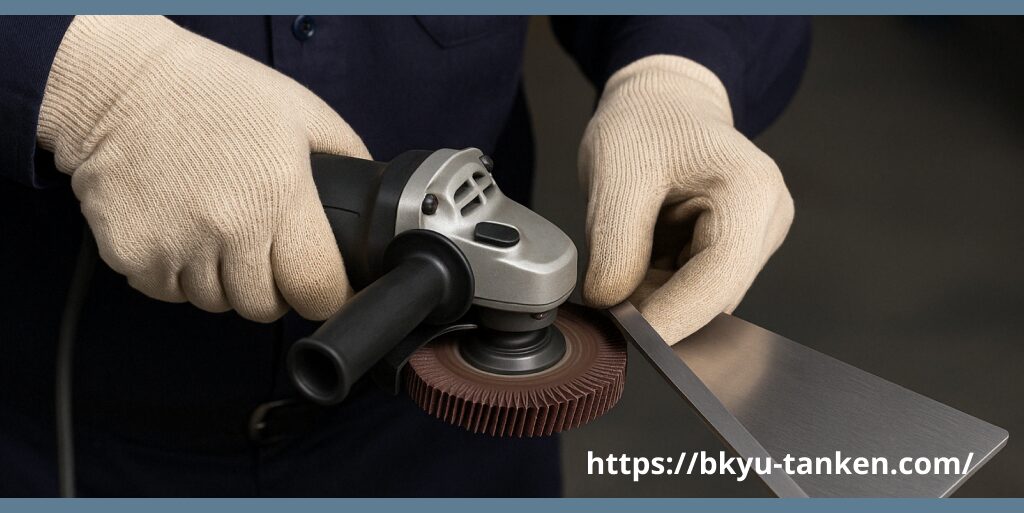
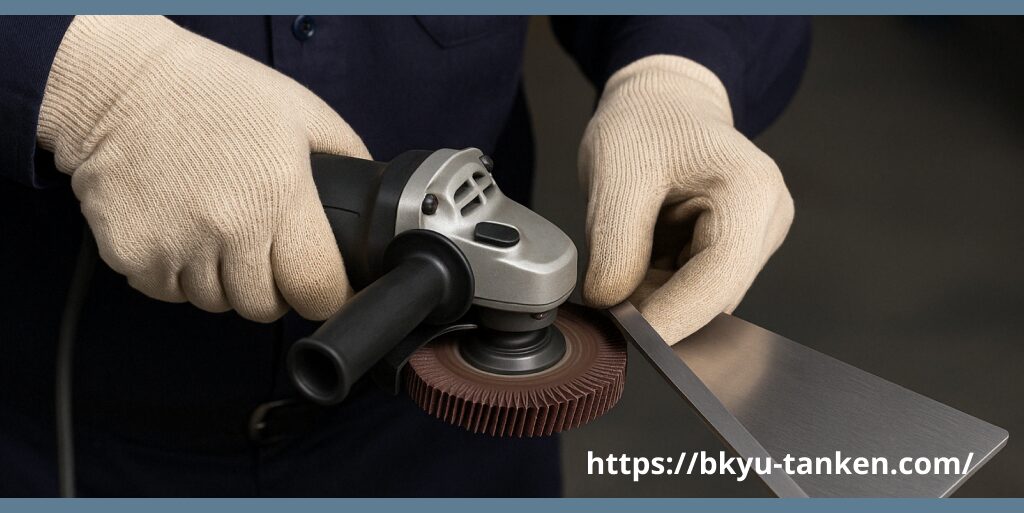
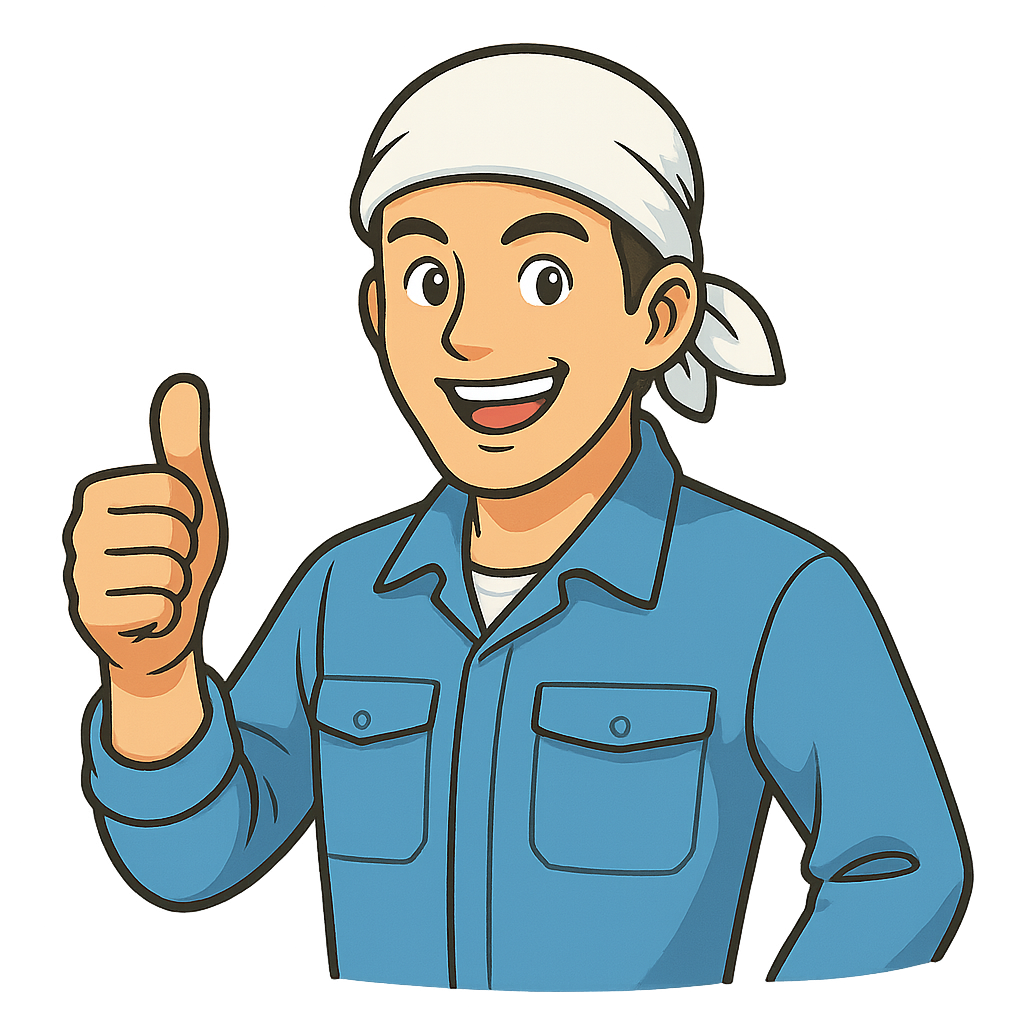
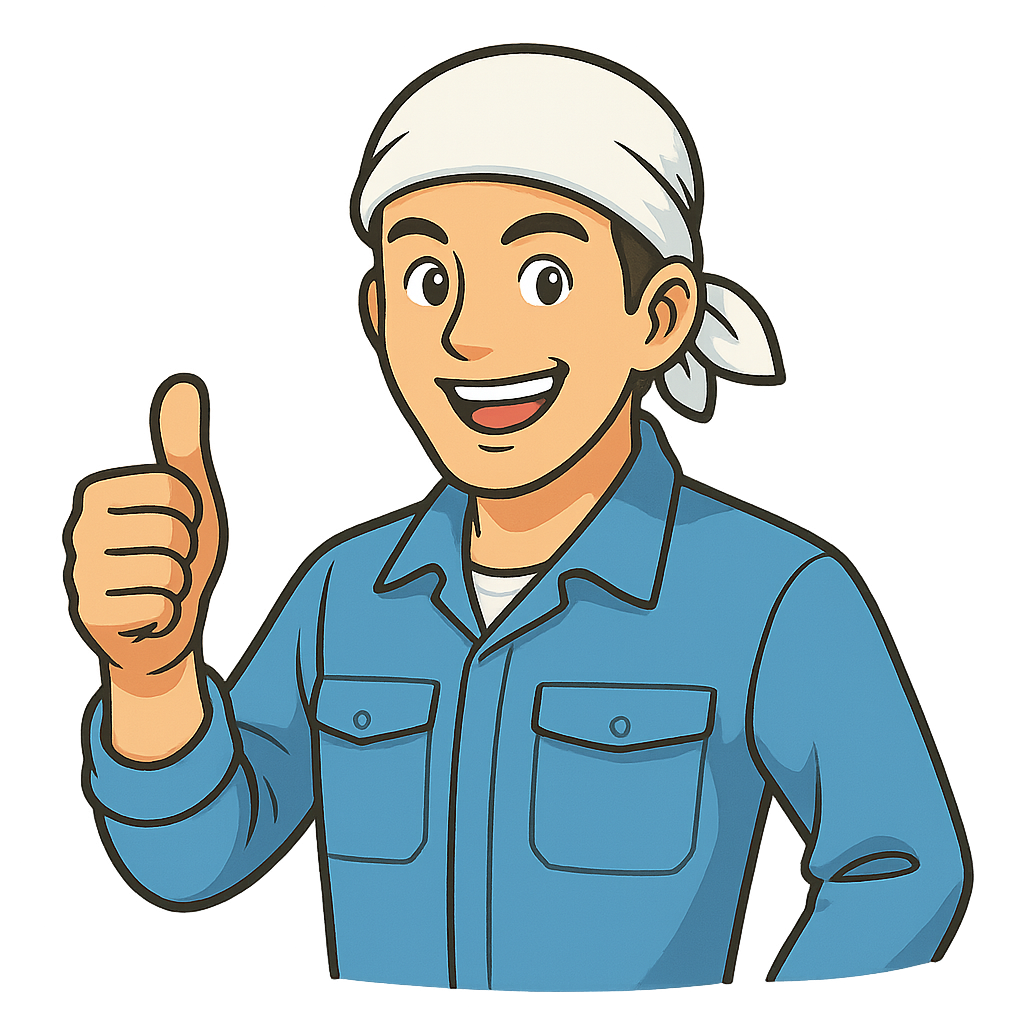
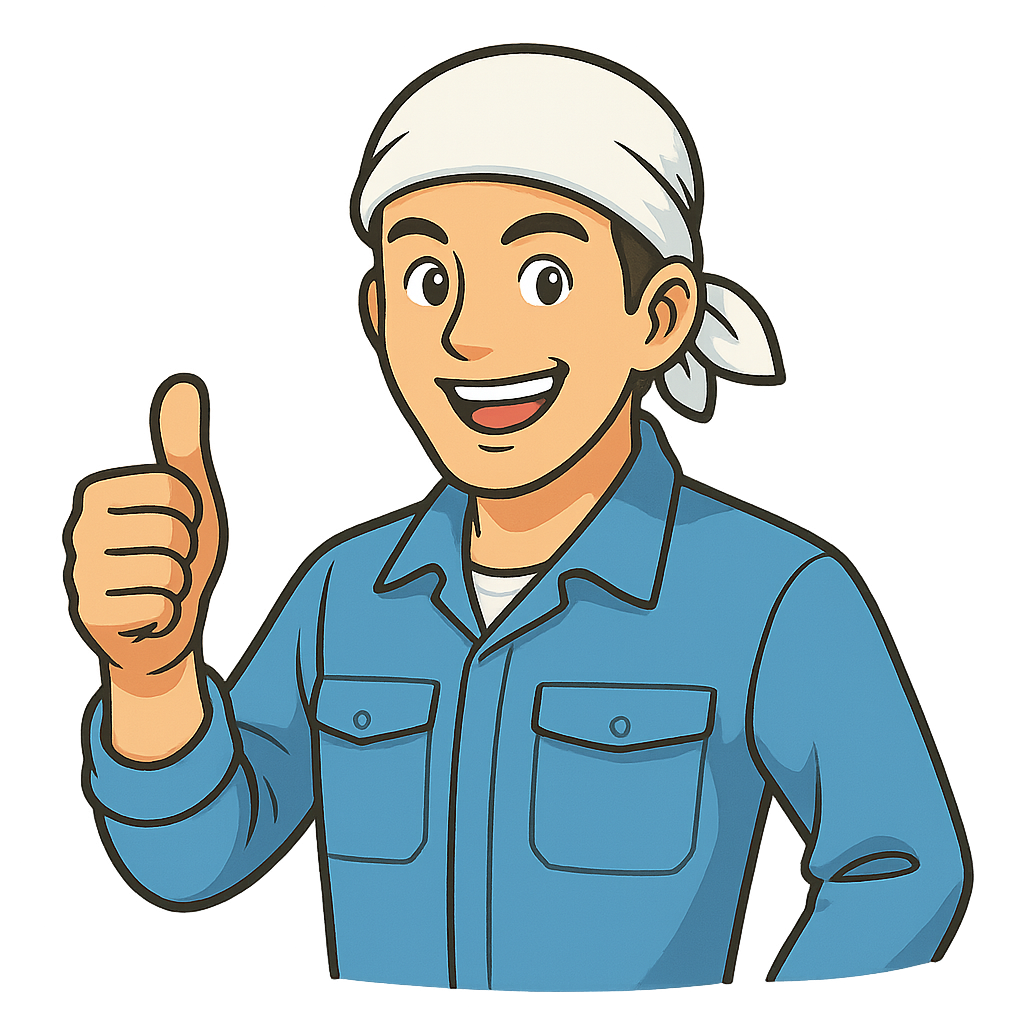
フラップホイールは使い始めに『ならし運転』をすると性能が安定します。実際の製品を研磨する前に、同じ材質の端材などで30秒程度試し研磨をすることをおすすめします。
研磨ブラシによる微細バリの除去
微細なバリや入り組んだ形状部のバリ取りには、研磨ブラシが効果的です。繊維に研磨材が含まれているタイプや、ワイヤータイプなど様々な種類があります。
研磨ブラシ選定のポイント
- 繊維の硬さ:アルミには中〜軟めの硬さ
- 研磨材粒度:#120〜#320が一般的
- ブラシ形状:加工部位の形状に合わせて選択
使用時は、過度な押し付けを避け、ブラシの弾力を活かした軽い接触を心がけることが重要です。
化学研磨と機械研磨の組み合わせ
複雑な形状や高い表面品質が求められる場合は、機械研磨と化学研磨を組み合わせる方法が効果的です。
機械研磨で大きなバリを除去した後、化学研磨液に浸漬することで、微細なバリや表面の凹凸を均一に除去できます。ただし、化学研磨には適切な設備と安全管理が必要なため、外部委託も検討すべき選択肢です。
化学研磨の基本プロセス
- 脱脂・洗浄
- 化学研磨液への浸漬(温度・時間管理が重要)
- 中和・洗浄
- 乾燥・検査
4. バリ取り品質の検査と評価方法
バリ取り作業の品質を確保するには、適切な検査・評価方法が欠かせません。
目視検査のポイントと照明条件
目視検査は最も基本的ですが、効果的な検査方法です。ポイントは適切な照明条件にあります。
効果的な目視検査の条件
- 斜光照明:表面に対して15〜30度の角度から光を当てる
- 明るさ:500〜1000ルクス程度
- 背景:検査物と対比のつく色(黒または白)
- 拡大鏡:2〜5倍程度の拡大率
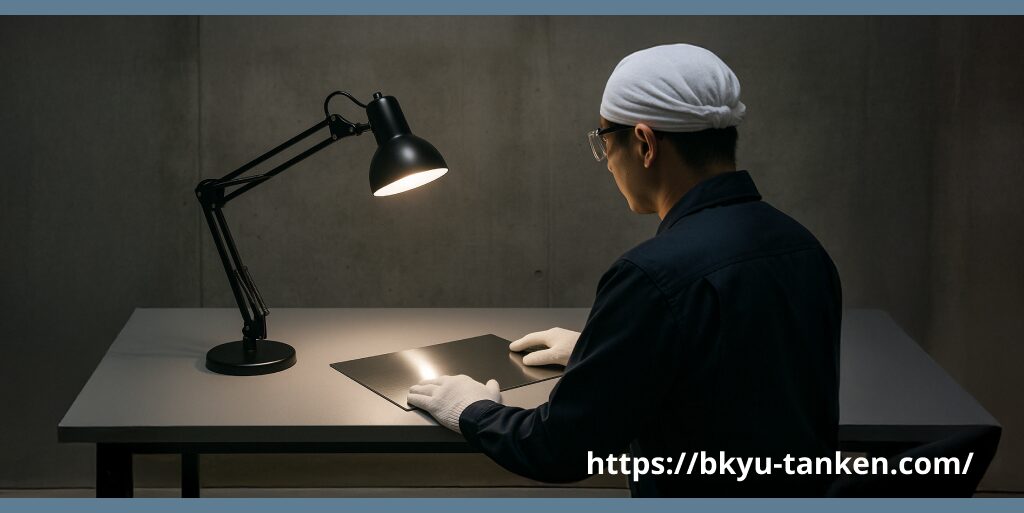
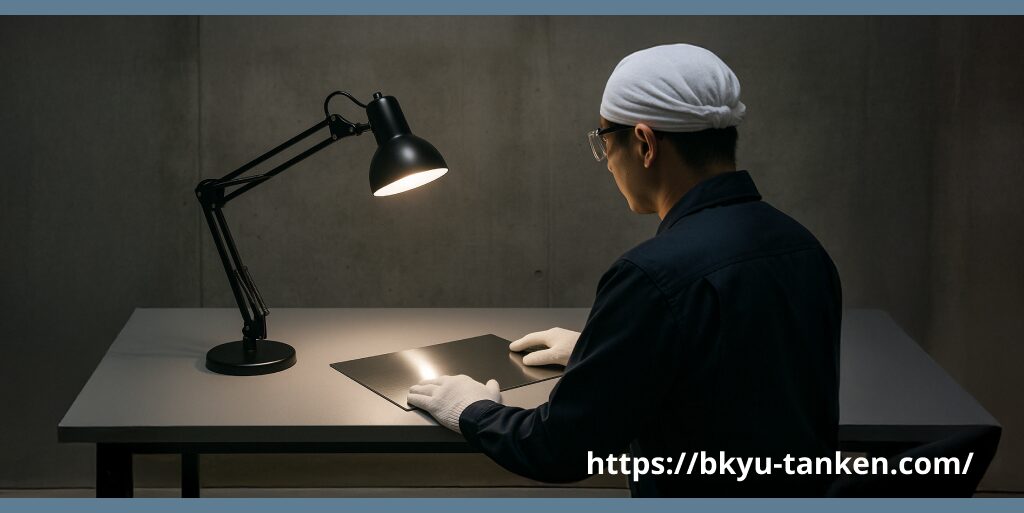
測定機器を使用した面粗度評価
より客観的な評価には、面粗度計などの測定機器を活用します。面粗度は、表面の凹凸の大きさを数値化したもので、一般的にRa(算術平均粗さ)などの指標で表されます。
アルミニウム製品の一般的な面粗度目標値
- 精密部品:Ra 0.1〜0.4μm
- 一般機械部品:Ra 0.8〜3.2μm
- 外観重視部品:Ra 0.2〜0.8μm
これらの値は製品の用途によって異なるため、要求仕様に応じた適切な目標値を設定することが重要です。
バリ取り工程の記録と追跡
品質の安定化と継続的改善のためには、バリ取り工程の記録と追跡が重要です。
記録すべき項目
- 使用した研磨材の種類とロット番号
- 作業者名 作業時間
- 機械設定(回転数、圧力など)
- 検査結果と不良の内容(発生時)
これらのデータを分析することで、不良の傾向や原因を特定し、効果的な改善策を立案できます。
5. コスト効率を高めるバリ取り工程の最適化
バリ取り作業は品質だけでなく、コスト効率も重要な要素です。以下に、コスト効率を高める方法を紹介します。
工具寿命の延長と効率的な使用法
研磨材や工具の寿命を延ばすことは、直接的なコスト削減につながります。
工具寿命を延ばすポイント
- 適切な保管(湿気・直射日光を避ける)
- 定期的なクリーニング(特に不織布系研磨材)
- 適切な回転数と圧力の管理
- 研磨材の定期的な回転・位置変更
フラップホイールなどは、使用後に圧縮エアで清掃することで、目詰まりを防止し寿命を延ばせます。
作業時間短縮のための効率化テクニック
バリ取り作業の時間短縮は、生産性向上に直結します。
効率化のポイント
- 作業台の配置最適化(動線を短く)
- 工具交換の迅速化(クイックチェンジシステムの導入)
- 複数工程の統合(可能な場合)
- 治具の活用(同じ形状の製品を効率的に処理)
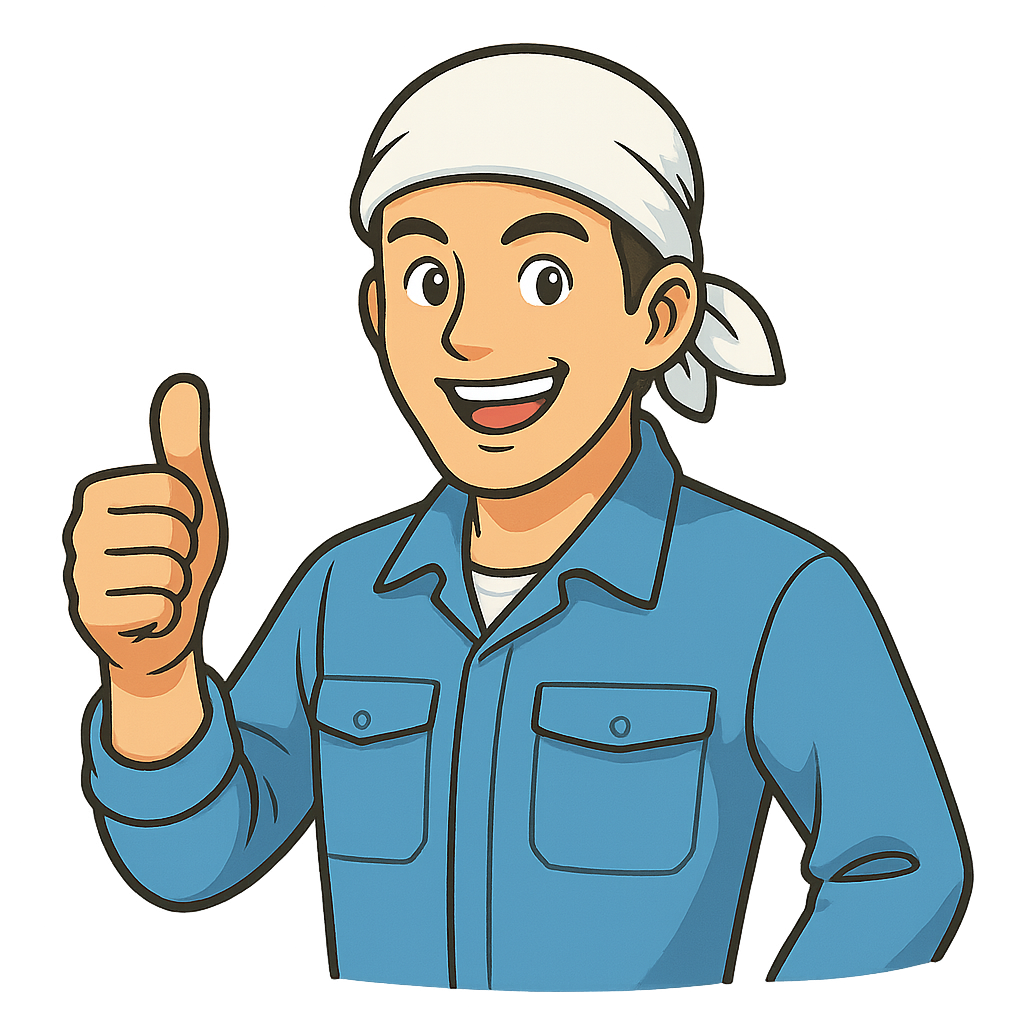
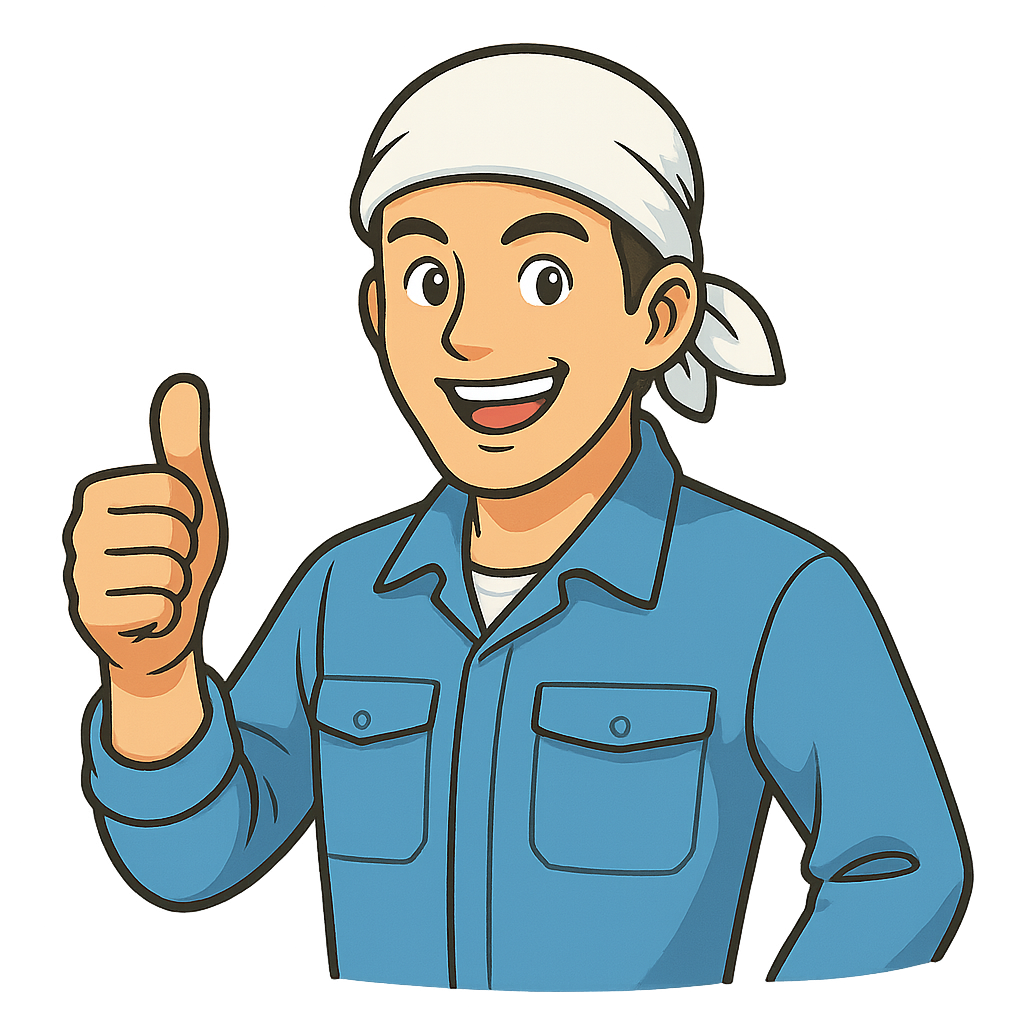
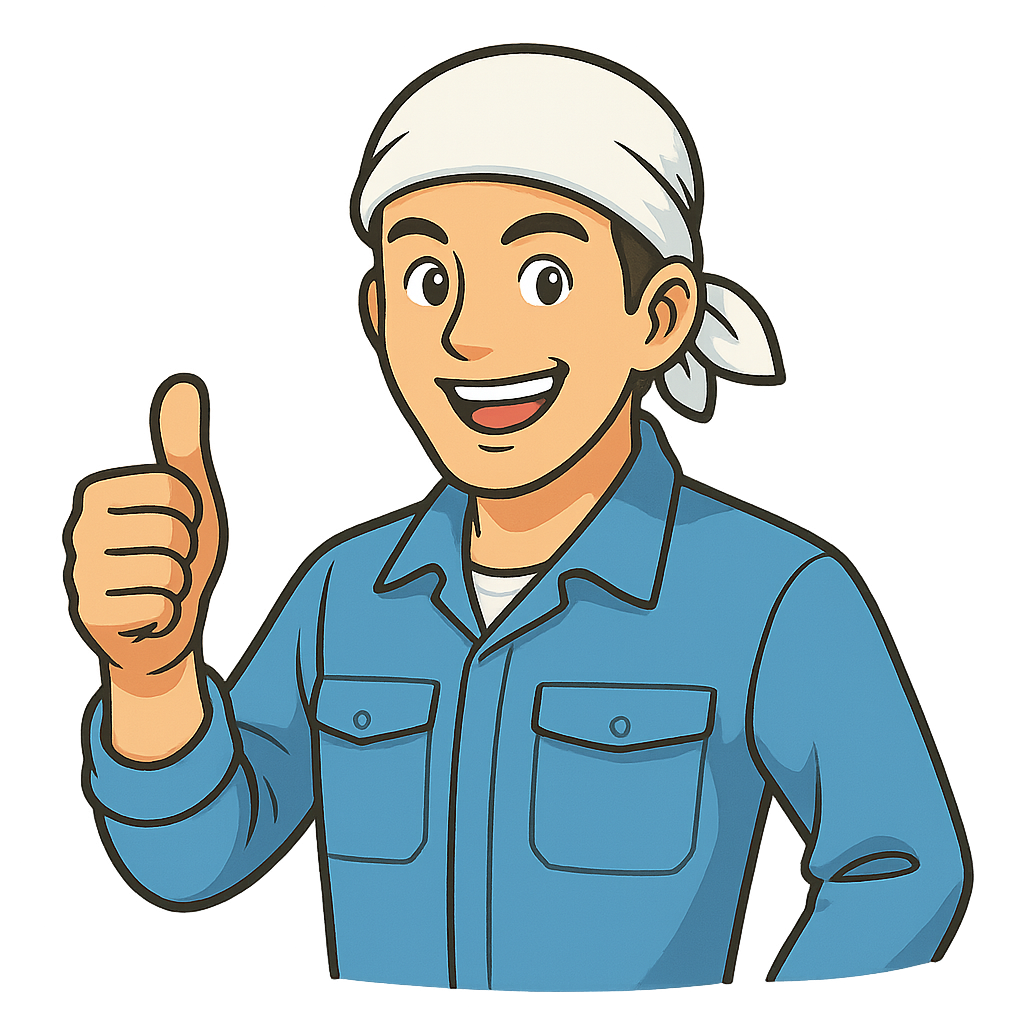
バリ取り作業の『見える化』も効果的です。作業時間や工程ごとの所要時間を計測・表示することで、作業者の意識が変わり、自然と効率化が進むことがよくあります。
自動化・半自動化の導入検討
生産量が多い場合は、バリ取りの自動化や半自動化も検討価値があります。
導入を検討すべき設備
- バレル研磨機(小〜中サイズの部品向け)
- ロボットによるバリ取りシステム(複雑形状向け)
- ブラシ研磨機(平面や単純形状向け)
初期投資は必要ですが、作業の安定化や人件費削減につながり、長期的にはコスト効率が向上します。
6. 現場で使える具体的バリ取り改善事例
ここでは、実際の製造現場で効果を上げた具体的な改善事例を紹介します。
治工具の工夫による効率化
ある自動車部品メーカーでは、アルミダイカスト部品のバリ取り作業に時間がかかっていました。そこで、専用治具を開発し、一度に複数箇所のバリを処理できるようにしました。
改善のポイント
- 製品の固定方法を工夫(作業者の両手を自由に)
- バリの発生しやすい箇所に集中できる治具形状
- 人間工学に基づいた作業姿勢の改善
結果として、作業時間が約40%短縮され、品質も向上しました。
研磨材選定による表面品質の向上
電子機器筐体を製造する企業では、アルミ部品の表面に微細な傷が残る問題がありました。原因を調査したところ、バリ取り用の研磨材が不適切であることが判明しました。
3M スコッチブライト(Scotch-Brite)の適切な粒度のものに変更し、さらに研磨方向を一定にすることで、表面品質が大幅に向上しました。クレーム率は80%低減し、顧客満足度も向上しました。
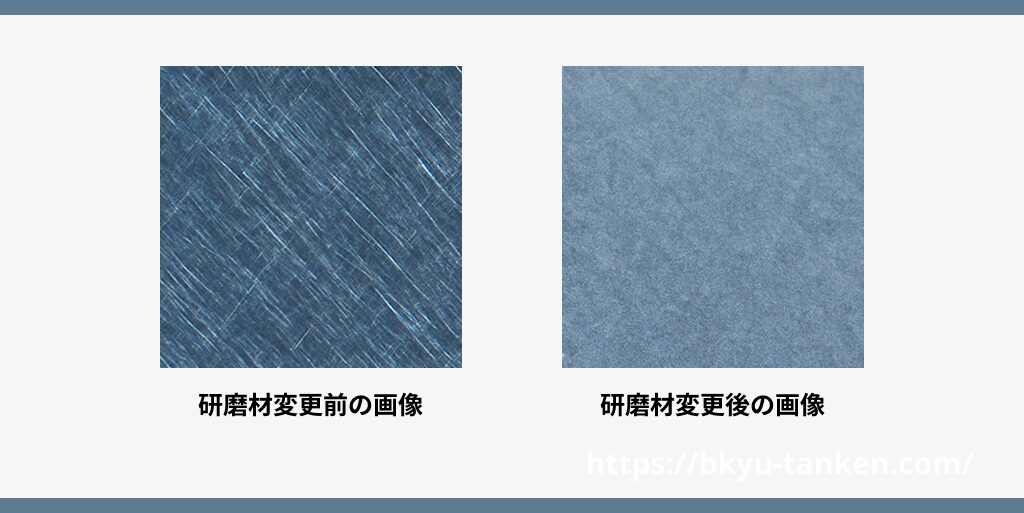
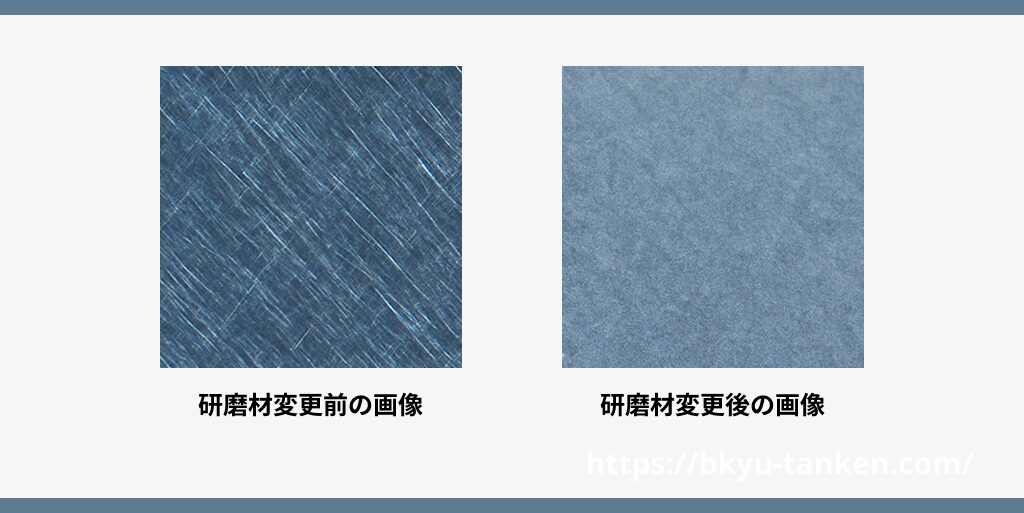
作業標準化による品質のばらつき低減
医療機器部品を製造する中小企業では、作業者によるバリ取り品質のばらつきが問題でした。そこで、以下の取り組みを実施しました。
- 詳細な作業手順書の作成
- 作業者へのトレーニング実施
- 定期的な技能評価と指導
- 良品・不良品の実物見本作成
これらの取り組みにより、品質の均一化が進み、納期遅延や再加工が大幅に減少しました。
7. よくある質問と回答
まとめ
アルミ研磨におけるバリ取り不良は、適切な知識と手法によって大幅に改善できます。
本記事で紹介した内容をまとめると、
- バリ取り不良の主な原因は、切削条件の不適合、不適切な研磨材選択、作業手順の不明確さにあります。
- 効果的な解決策としては、材料特性に合わせた切削条件の最適化、専用研磨材の選定、標準作業手順の確立が重要です。
- 品質とコスト効率を両立するには、適切な検査方法の導入と作業の効率化が鍵となります。
これらの改善策は、すぐに現場で実践できるものばかりです。まずは小規模なテストから始め、効果を確認しながら段階的に導入していくことをおすすめします。
製造業の競争が激化する中、バリ取り工程の品質向上は製品全体の価値を高める重要な要素です。
皆さんの製造現場で、この記事が役立てば幸いです。
コメント